Information injection-pump assembly
BOSCH
9 400 615 580
9400615580
ZEXEL
101606-9730
1016069730
NISSAN-DIESEL
1670095075
1670095075
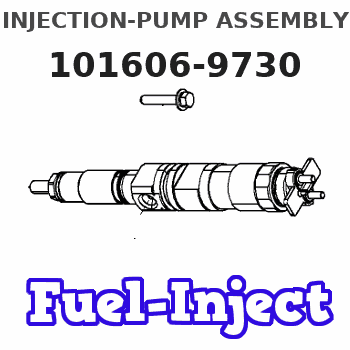
Rating:
Service parts 101606-9730 INJECTION-PUMP ASSEMBLY:
1.
_
7.
COUPLING PLATE
8.
_
9.
_
11.
Nozzle and Holder
16600-95013
12.
Open Pre:MPa(Kqf/cm2)
19.6{200}
15.
NOZZLE SET
Cross reference number
BOSCH
9 400 615 580
9400615580
ZEXEL
101606-9730
1016069730
NISSAN-DIESEL
1670095075
1670095075
Zexel num
Bosch num
Firm num
Name
Calibration Data:
Adjustment conditions
Test oil
1404 Test oil ISO4113 or {SAEJ967d}
1404 Test oil ISO4113 or {SAEJ967d}
Test oil temperature
degC
40
40
45
Nozzle and nozzle holder
105780-8140
Bosch type code
EF8511/9A
Nozzle
105780-0000
Bosch type code
DN12SD12T
Nozzle holder
105780-2080
Bosch type code
EF8511/9
Opening pressure
MPa
17.2
Opening pressure
kgf/cm2
175
Injection pipe
Outer diameter - inner diameter - length (mm) mm 6-2-600
Outer diameter - inner diameter - length (mm) mm 6-2-600
Overflow valve
131424-1520
Overflow valve opening pressure
kPa
157
123
191
Overflow valve opening pressure
kgf/cm2
1.6
1.25
1.95
Tester oil delivery pressure
kPa
157
157
157
Tester oil delivery pressure
kgf/cm2
1.6
1.6
1.6
Direction of rotation (viewed from drive side)
Right R
Right R
Injection timing adjustment
Direction of rotation (viewed from drive side)
Right R
Right R
Injection order
1-4-2-6-
3-5
Pre-stroke
mm
3
2.95
3.05
Beginning of injection position
Drive side NO.1
Drive side NO.1
Difference between angles 1
Cal 1-4 deg. 60 59.5 60.5
Cal 1-4 deg. 60 59.5 60.5
Difference between angles 2
Cyl.1-2 deg. 120 119.5 120.5
Cyl.1-2 deg. 120 119.5 120.5
Difference between angles 3
Cal 1-6 deg. 180 179.5 180.5
Cal 1-6 deg. 180 179.5 180.5
Difference between angles 4
Cal 1-3 deg. 240 239.5 240.5
Cal 1-3 deg. 240 239.5 240.5
Difference between angles 5
Cal 1-5 deg. 300 299.5 300.5
Cal 1-5 deg. 300 299.5 300.5
Injection quantity adjustment
Adjusting point
A
Rack position
8.8
Pump speed
r/min
1400
1400
1400
Average injection quantity
mm3/st.
79.4
78.4
80.4
Max. variation between cylinders
%
0
-3.5
3.5
Basic
*
Fixing the lever
*
Injection quantity adjustment_02
Adjusting point
B
Rack position
9.2
Pump speed
r/min
600
600
600
Average injection quantity
mm3/st.
68.3
66.3
70.3
Max. variation between cylinders
%
0
-5
5
Fixing the lever
*
Injection quantity adjustment_03
Adjusting point
C
Rack position
7.2+-0.5
Pump speed
r/min
285
285
285
Average injection quantity
mm3/st.
9
7.2
10.8
Max. variation between cylinders
%
0
-10
10
Fixing the rack
*
Injection quantity adjustment_04
Adjusting point
D
Rack position
13.2+-0.
5
Pump speed
r/min
150
150
150
Average injection quantity
mm3/st.
115
115
Fixing the lever
*
Remarks
After startup boost setting
After startup boost setting
Timer adjustment
Pump speed
r/min
500
Advance angle
deg.
0.5
Timer adjustment_02
Pump speed
r/min
800
Advance angle
deg.
1.5
1
2
Timer adjustment_03
Pump speed
r/min
1200
Advance angle
deg.
4
3.5
4.5
Remarks
Finish
Finish
Test data Ex:
Governor adjustment
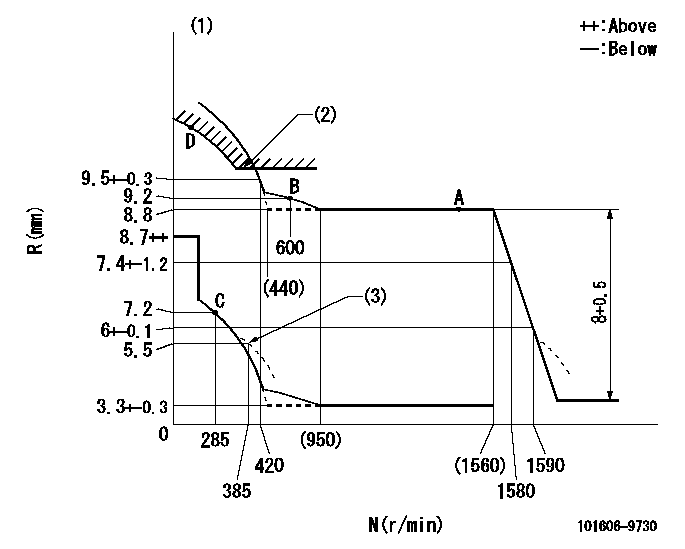
N:Pump speed
R:Rack position (mm)
(1)Tolerance for racks not indicated: +-0.05mm.
(2)Excess fuel setting for starting: SXL (N = N1)
(3)Damper spring setting
----------
SXL=10+0.2mm N1=380r/min
----------
----------
SXL=10+0.2mm N1=380r/min
----------
0000000901

F:Full load
I:Idle
(1)R = aa
(2)Stopper bolt setting
----------
aa=65mm
----------
a=16.5deg+-5deg b=20.5deg+-3deg
----------
aa=65mm
----------
a=16.5deg+-5deg b=20.5deg+-3deg
Stop lever angle
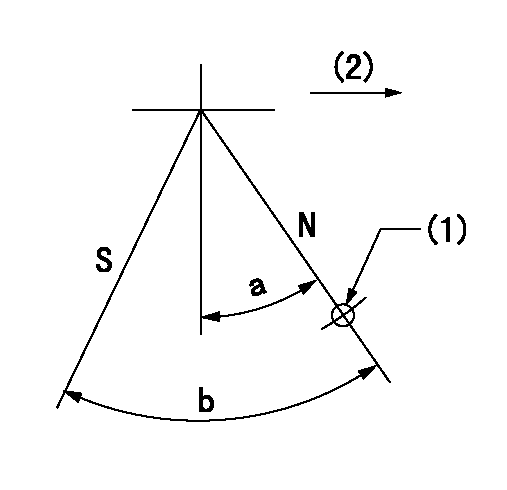
N:Pump normal
S:Stop the pump.
(1)Use the pin at R = aa
(2)Drive side
----------
aa=20mm
----------
a=40deg+-5deg b=71deg+-5deg
----------
aa=20mm
----------
a=40deg+-5deg b=71deg+-5deg
Timing setting

(1)Pump vertical direction
(2)Coupling's key groove position at No 1 cylinder's beginning of injection
(3)-
(4)-
----------
----------
a=(30deg)
----------
----------
a=(30deg)
Information:
Start By:a. remove cylinder head assemblyb. remove oil panc. remove piston cooling jets 1. Remove two rod cap bolts (1) from each rod. Remove rod caps (2).2. Using a soft jawed hammer, tap rod (3) away from the crankshaft. Remove bearing half (4).
When removing the cylinder pack, watch the rod, and prevent it from catching on the bore in the cylinder block as it comes out.
3. Install tooling (A), and remove cylinder pack (5). 4. Remove cylinder liner seal (6) at the base of the spacer block.5. Remove the remainder of tooling (A) from cylinder pack (5). 6. Remove the rod and piston from the cylinder liner. Remove seal (7) from the cylinder liner. The following steps are for the installation of the cylinder pack.7. Install a new cylinder liner seal (6) in the base of the spacer block. Lubricate the seal with clean engine oil. Some engines use pistons which have the word "FRONT" stamped on the crown of the piston. Be sure the word "FRONT" is toward the front of the engine when the piston is installed. The etched number on the connecting rod must be on the right side and must be installed in the corresponding cylinder. 9U-5839 Liquid Gasket Material is applied to the cylinder liners in the area shown in the illustration. The liquid gasket material helps prevent oil leaks from between the cylinder block and spacer block. DO NOT apply any 9U-5839 Liquid Gasket Material between the engine spacer block and the cylinder block surfaces. Using excessive amounts of liquid gasket material on the liner flange seat can cause oil leaks due to distortion of the O-ring seals between the spacer block and cylinder block.8. Install a new seal (7) on the cylinder liner.9. Lubricate the lower portion of the cylinder liner with clean engine oil. Be sure the corresponding crankshaft throw is at bottom center. Position cylinder pack (5), and guide rod (3) into place. Use tooling (B), and press cylinder pack (5) into place. Refer to the "Systems Operation Testing And Adjusting" module, Form No. SENR5561, for checking Cylinder Liner Projection.10. With rod (3) in this position, install the upper half of rod bearing (4). Be sure the bearing tab properly engages with the slot in the connecting rod. Lubricate the bearing surface with clean engine oil. Tap the piston down with a soft faced hammer until the rod and bearing contacts the crankshaft.11. With rod cap bearing in place and lubricated, install rod cap (2). Lubricate rod bolts (1) with 2P2506 Thread Lubricant. Install rod bolts (1), and tighten them to a torque of 130 7 N m (95 5 lb ft). Mark each bolt head, and tighten each bolt an additional 1/6 60 5 ( turn).End By:a. install piston cooling jetsb. install oil panc. install cylinder head assembly
When removing the cylinder pack, watch the rod, and prevent it from catching on the bore in the cylinder block as it comes out.
3. Install tooling (A), and remove cylinder pack (5). 4. Remove cylinder liner seal (6) at the base of the spacer block.5. Remove the remainder of tooling (A) from cylinder pack (5). 6. Remove the rod and piston from the cylinder liner. Remove seal (7) from the cylinder liner. The following steps are for the installation of the cylinder pack.7. Install a new cylinder liner seal (6) in the base of the spacer block. Lubricate the seal with clean engine oil. Some engines use pistons which have the word "FRONT" stamped on the crown of the piston. Be sure the word "FRONT" is toward the front of the engine when the piston is installed. The etched number on the connecting rod must be on the right side and must be installed in the corresponding cylinder. 9U-5839 Liquid Gasket Material is applied to the cylinder liners in the area shown in the illustration. The liquid gasket material helps prevent oil leaks from between the cylinder block and spacer block. DO NOT apply any 9U-5839 Liquid Gasket Material between the engine spacer block and the cylinder block surfaces. Using excessive amounts of liquid gasket material on the liner flange seat can cause oil leaks due to distortion of the O-ring seals between the spacer block and cylinder block.8. Install a new seal (7) on the cylinder liner.9. Lubricate the lower portion of the cylinder liner with clean engine oil. Be sure the corresponding crankshaft throw is at bottom center. Position cylinder pack (5), and guide rod (3) into place. Use tooling (B), and press cylinder pack (5) into place. Refer to the "Systems Operation Testing And Adjusting" module, Form No. SENR5561, for checking Cylinder Liner Projection.10. With rod (3) in this position, install the upper half of rod bearing (4). Be sure the bearing tab properly engages with the slot in the connecting rod. Lubricate the bearing surface with clean engine oil. Tap the piston down with a soft faced hammer until the rod and bearing contacts the crankshaft.11. With rod cap bearing in place and lubricated, install rod cap (2). Lubricate rod bolts (1) with 2P2506 Thread Lubricant. Install rod bolts (1), and tighten them to a torque of 130 7 N m (95 5 lb ft). Mark each bolt head, and tighten each bolt an additional 1/6 60 5 ( turn).End By:a. install piston cooling jetsb. install oil panc. install cylinder head assembly