Information injection-pump assembly
ZEXEL
101606-9080
1016069080
NISSAN-DIESEL
16790Z5579
16790z5579
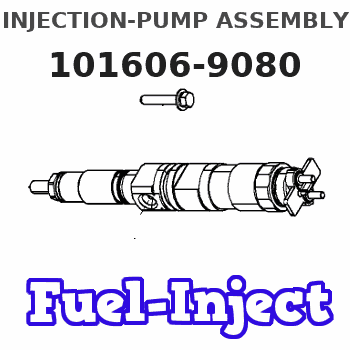
Rating:
Service parts 101606-9080 INJECTION-PUMP ASSEMBLY:
1.
_
6.
COUPLING PLATE
7.
COUPLING PLATE
8.
_
9.
_
11.
Nozzle and Holder
16600-Z5511
12.
Open Pre:MPa(Kqf/cm2)
19.6{200}
15.
NOZZLE SET
Cross reference number
ZEXEL
101606-9080
1016069080
NISSAN-DIESEL
16790Z5579
16790z5579
Zexel num
Bosch num
Firm num
Name
101606-9080
16790Z5579 NISSAN-DIESEL
INJECTION-PUMP ASSEMBLY
FD606 * K 14BE PE6A PE
FD606 * K 14BE PE6A PE
Calibration Data:
Adjustment conditions
Test oil
1404 Test oil ISO4113 or {SAEJ967d}
1404 Test oil ISO4113 or {SAEJ967d}
Test oil temperature
degC
40
40
45
Nozzle and nozzle holder
105780-8140
Bosch type code
EF8511/9A
Nozzle
105780-0000
Bosch type code
DN12SD12T
Nozzle holder
105780-2080
Bosch type code
EF8511/9
Opening pressure
MPa
17.2
Opening pressure
kgf/cm2
175
Injection pipe
Outer diameter - inner diameter - length (mm) mm 6-2-600
Outer diameter - inner diameter - length (mm) mm 6-2-600
Overflow valve
131424-1520
Overflow valve opening pressure
kPa
157
123
191
Overflow valve opening pressure
kgf/cm2
1.6
1.25
1.95
Tester oil delivery pressure
kPa
157
157
157
Tester oil delivery pressure
kgf/cm2
1.6
1.6
1.6
Direction of rotation (viewed from drive side)
Right R
Right R
Injection timing adjustment
Direction of rotation (viewed from drive side)
Right R
Right R
Injection order
1-4-2-6-
3-5
Pre-stroke
mm
3
2.95
3.05
Beginning of injection position
Drive side NO.1
Drive side NO.1
Difference between angles 1
Cal 1-4 deg. 60 59.5 60.5
Cal 1-4 deg. 60 59.5 60.5
Difference between angles 2
Cyl.1-2 deg. 120 119.5 120.5
Cyl.1-2 deg. 120 119.5 120.5
Difference between angles 3
Cal 1-6 deg. 180 179.5 180.5
Cal 1-6 deg. 180 179.5 180.5
Difference between angles 4
Cal 1-3 deg. 240 239.5 240.5
Cal 1-3 deg. 240 239.5 240.5
Difference between angles 5
Cal 1-5 deg. 300 299.5 300.5
Cal 1-5 deg. 300 299.5 300.5
Injection quantity adjustment
Adjusting point
A
Rack position
9.2
Pump speed
r/min
1350
1350
1350
Average injection quantity
mm3/st.
62
61
63
Max. variation between cylinders
%
0
-2.5
2.5
Basic
*
Fixing the lever
*
Injection quantity adjustment_02
Adjusting point
B
Rack position
7.5+-0.5
Pump speed
r/min
300
300
300
Average injection quantity
mm3/st.
8.2
7.2
9.2
Max. variation between cylinders
%
0
-12
12
Fixing the rack
*
Injection quantity adjustment_03
Adjusting point
C
Rack position
12+-0.1
Pump speed
r/min
100
100
100
Average injection quantity
mm3/st.
71
61
81
Fixing the lever
*
Rack limit
*
Timer adjustment
Pump speed
r/min
1250--
Advance angle
deg.
0
0
0
Remarks
Start
Start
Timer adjustment_02
Pump speed
r/min
1200
Advance angle
deg.
0.5
Timer adjustment_03
Pump speed
r/min
1400
Advance angle
deg.
1
0.5
1.5
Remarks
Finish
Finish
Test data Ex:
Governor adjustment
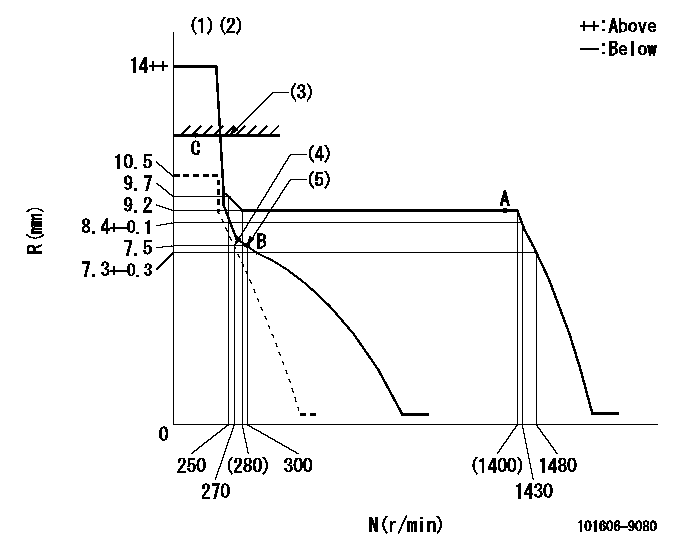
N:Pump speed
R:Rack position (mm)
(1)Target notch: K
(2)Tolerance for racks not indicated: +-0.05mm.
(3)RACK LIMIT: RAL
(4)Set idle sub-spring
(5)Main spring setting
----------
K=18 RAL=12+-0.1mm
----------
----------
K=18 RAL=12+-0.1mm
----------
Speed control lever angle
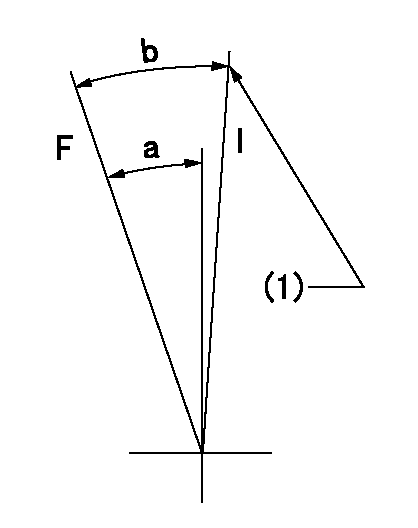
F:Full speed
I:Idle
(1)Stopper bolt setting
----------
----------
a=22deg+-5deg b=23deg+-5deg
----------
----------
a=22deg+-5deg b=23deg+-5deg
Stop lever angle
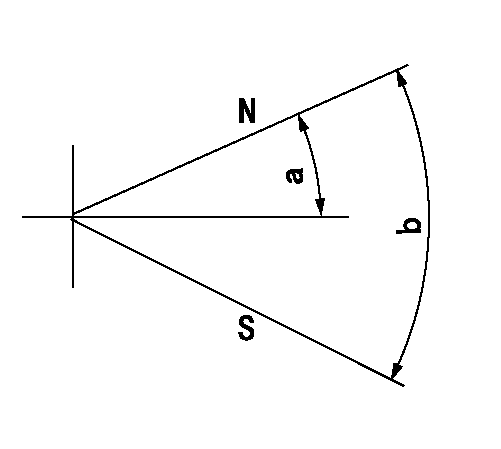
N:Pump normal
S:Stop the pump.
----------
----------
a=19deg+-5deg b=53deg+-5deg
----------
----------
a=19deg+-5deg b=53deg+-5deg
0000001501 GOV FULL LOAD ADJUSTMENT
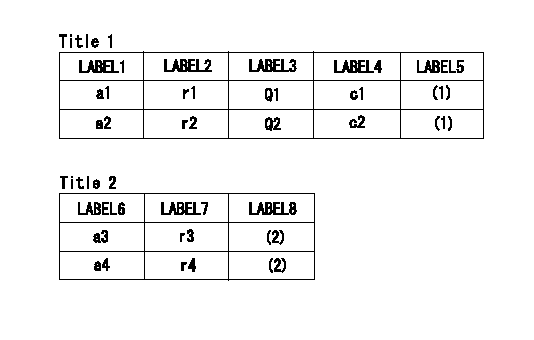
Title1:Full load stopper adjustment
Title2:Governor set speed
LABEL1:Distinguishing
LABEL2:Pump speed (r/min)
LABEL3:Ave. injection quantity (mm3/st)
LABEL4:Max. var. bet. cyl.
LABEL5:Remarks
LABEL6:Distinguishing
LABEL7:Governor set speed (r/min)
LABEL8:Remarks
(1)Adjustment conditions are the same as those for measuring injection quantity.
(2)-
----------
----------
a1=M a2=F r1=1350r/min r2=1350r/min Q1=62+-1mm3/st Q2=54+-1mm3/st c1=+-2.5% c2=+-2.5% a3=M a4=F r3=1400r/min r4=1350r/min
----------
----------
a1=M a2=F r1=1350r/min r2=1350r/min Q1=62+-1mm3/st Q2=54+-1mm3/st c1=+-2.5% c2=+-2.5% a3=M a4=F r3=1400r/min r4=1350r/min
Timing setting
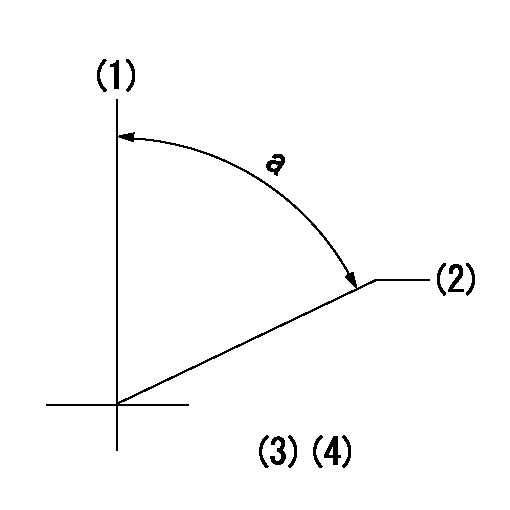
(1)Pump vertical direction
(2)Position of gear mark 'G' at No 1 cylinder's beginning of injection
(3)B.T.D.C.: aa
(4)-
----------
aa=15deg
----------
a=(60deg)
----------
aa=15deg
----------
a=(60deg)
Information:
Repeat Steps 4 through 6 to remove (bleed) air from the rear table lift cylinder (not shown).
Open (CCW) hand pump control knob (11) to completely lower the DPF cleaner table. Close (CW) the hand pump control knob.
Illustration 38 g02728258
(28) Hydraulic Oil Level 51 to 102 mm (2.0 to 4.0 inch)
Check the oil level in the pump reservoir. Remove fill cap (13) located on the end cap of the hand pump. Hydraulic oil level (28) should be 51 to 102 mm (2.0 to 4.0 inch) from the bottom of the fill hole. Add high-grade hydraulic oil, if needed.Note: A clean wire tie can be used as a dipstick to measure the hydraulic oil level in the pump reservoir.Troubleshooting Guide
Table 3
Symptom     Solution    
Air dryer desiccant is a pinkish color.     1. Replace or regenerate the desiccant. Refer to ""Maintenance Section"".    
Bursting does not occur.     1. Check display screen for error message.
2. Check power connection to burst valve solenoid.    
Cabinet doors do not close correctly.     1. Look for damaged door hinges, seals, and latches.
2. Verify that vehicle sensors have been removed from DPF.    
Cabinet doors open during burst process.     1. Verify that doors are correctly latched.
2. Look for damage to door latches.
3. Check seals between DPF and adapters.    
Clamping force cannot be obtained.     1. Look for hydraulic fluid leaks.
2. Check fluid level in hydraulic pump. Refer to ""Maintenance Section"".    
Clamping force does not hold.     1. Upon initial clamping, it is possible for clamp load to drop
689 to 1379 kPa (99.9 to 200.0 psi) within the first minute, due to temperature effects. After reclamping, the drop should be virtually zero.
2. Look for hydraulic fluid leaks.    
Display screen is blank.     1. Verify that machine is ON, plugged into an outlet, and power is available to the outlet.
2. Reset circuit breakers located on left side of control cabinet.    
DPF does not line up correctly on the table.     1. Verify that correct adapters are being used.
2. Verify DPF is correctly seated on to lower adapter.    
DPF is damaged after cleaning process.     1. Check DPFs for damage before cleaning.
2. Look for damage on adapters.
3. Verify that correct cleaning protocol was entered into machine.    
DPF is not cleaned.     1. Check orientation of DPF. Refer to ""General Information"" Section.
2. Verify that correct cleaning protocol was entered into machine.
3. Look for other DPF conditions that may prevent successful cleaning.  
Have questions with 101606-9080?
Group cross 101606-9080 ZEXEL
Hyundai
Nissan-Diesel
Nissan-Diesel
101606-9080
16790Z5579
INJECTION-PUMP ASSEMBLY
FD606
FD606