Information injection-pump assembly
BOSCH
F 01G 09U 04T
f01g09u04t
ZEXEL
101606-9030
1016069030
NISSAN-DIESEL
16713Z5967
16713z5967
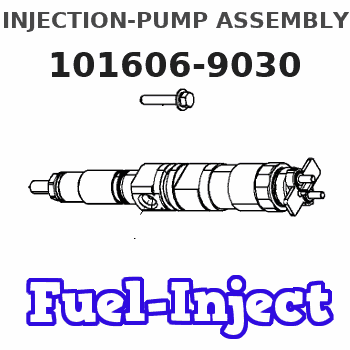
Rating:
Cross reference number
BOSCH
F 01G 09U 04T
f01g09u04t
ZEXEL
101606-9030
1016069030
NISSAN-DIESEL
16713Z5967
16713z5967
Zexel num
Bosch num
Firm num
Name
Calibration Data:
Adjustment conditions
Test oil
1404 Test oil ISO4113 or {SAEJ967d}
1404 Test oil ISO4113 or {SAEJ967d}
Test oil temperature
degC
40
40
45
Nozzle and nozzle holder
105780-8140
Bosch type code
EF8511/9A
Nozzle
105780-0000
Bosch type code
DN12SD12T
Nozzle holder
105780-2080
Bosch type code
EF8511/9
Opening pressure
MPa
17.2
Opening pressure
kgf/cm2
175
Injection pipe
Outer diameter - inner diameter - length (mm) mm 6-2-600
Outer diameter - inner diameter - length (mm) mm 6-2-600
Overflow valve
131424-1520
Overflow valve opening pressure
kPa
157
123
191
Overflow valve opening pressure
kgf/cm2
1.6
1.25
1.95
Tester oil delivery pressure
kPa
157
157
157
Tester oil delivery pressure
kgf/cm2
1.6
1.6
1.6
Direction of rotation (viewed from drive side)
Right R
Right R
Injection timing adjustment
Direction of rotation (viewed from drive side)
Right R
Right R
Injection order
1-4-2-6-
3-5
Pre-stroke
mm
3
2.95
3.05
Beginning of injection position
Drive side NO.1
Drive side NO.1
Difference between angles 1
Cal 1-4 deg. 60 59.5 60.5
Cal 1-4 deg. 60 59.5 60.5
Difference between angles 2
Cyl.1-2 deg. 120 119.5 120.5
Cyl.1-2 deg. 120 119.5 120.5
Difference between angles 3
Cal 1-6 deg. 180 179.5 180.5
Cal 1-6 deg. 180 179.5 180.5
Difference between angles 4
Cal 1-3 deg. 240 239.5 240.5
Cal 1-3 deg. 240 239.5 240.5
Difference between angles 5
Cal 1-5 deg. 300 299.5 300.5
Cal 1-5 deg. 300 299.5 300.5
Injection quantity adjustment
Adjusting point
-
Rack position
11.2
Pump speed
r/min
900
900
900
Average injection quantity
mm3/st.
61.6
60
63.2
Max. variation between cylinders
%
0
-3.5
3.5
Basic
*
Fixing the rack
*
Standard for adjustment of the maximum variation between cylinders
*
Injection quantity adjustment_02
Adjusting point
H
Rack position
9.5+-0.5
Pump speed
r/min
275
275
275
Average injection quantity
mm3/st.
8.7
6.9
10.5
Max. variation between cylinders
%
0
-10
10
Fixing the rack
*
Standard for adjustment of the maximum variation between cylinders
*
Injection quantity adjustment_03
Adjusting point
A
Rack position
R1(11.2)
Pump speed
r/min
900
900
900
Average injection quantity
mm3/st.
61.6
60.6
62.6
Basic
*
Fixing the lever
*
Injection quantity adjustment_04
Adjusting point
B
Rack position
R1+0.2
Pump speed
r/min
1500
1500
1500
Average injection quantity
mm3/st.
76.1
72.1
80.1
Fixing the lever
*
Injection quantity adjustment_05
Adjusting point
I
Rack position
-
Pump speed
r/min
100
100
100
Average injection quantity
mm3/st.
81
81
91
Fixing the lever
*
Rack limit
*
Timer adjustment
Pump speed
r/min
(1140)
Advance angle
deg.
0
0
0
Remarks
Start
Start
Timer adjustment_02
Pump speed
r/min
1500
Advance angle
deg.
4
3.5
4.5
Remarks
Finish
Finish
Test data Ex:
Governor adjustment
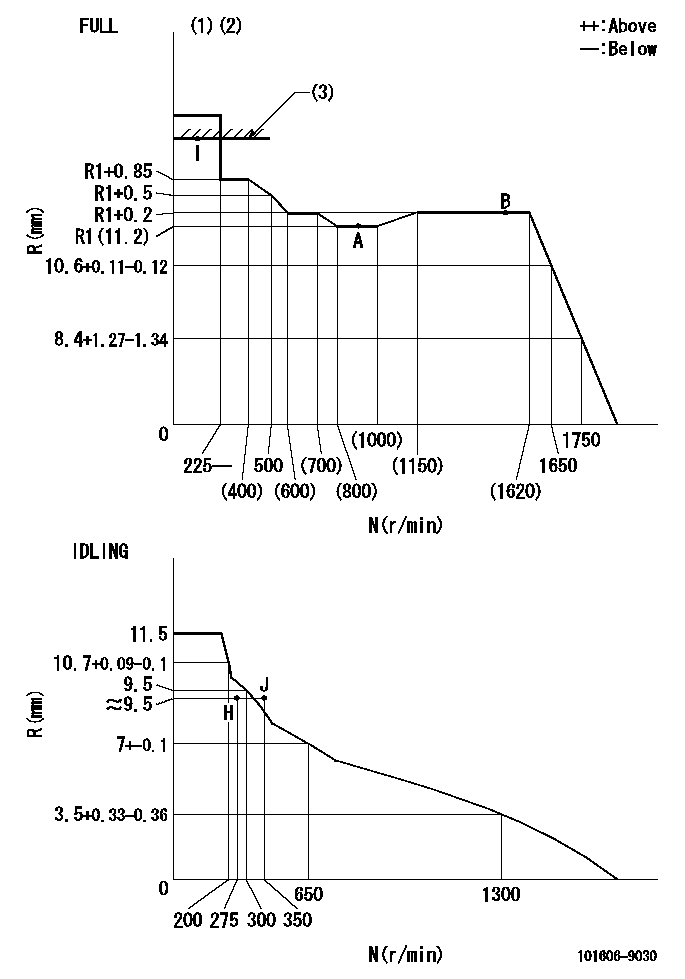
N:Pump speed
R:Rack position (mm)
(1)Torque cam stamping: T1
(2)Tolerance for racks not indicated: +-0.05mm.
(3)RACK LIMIT
----------
T1=H02
----------
----------
T1=H02
----------
Speed control lever angle

F:Full speed
I:Idle
(1)Use the hole at R = aa
(2)Stopper bolt set position 'H'
----------
aa=33mm
----------
a=27.5deg+-5deg b=40deg+-3deg
----------
aa=33mm
----------
a=27.5deg+-5deg b=40deg+-3deg
Stop lever angle
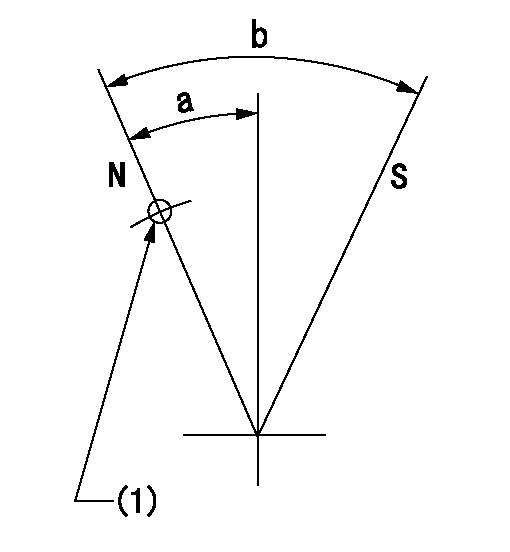
N:Pump normal
S:Stop the pump.
(1)Use the pin at R = aa
----------
aa=42mm
----------
a=20deg+-5deg b=40deg+-5deg
----------
aa=42mm
----------
a=20deg+-5deg b=40deg+-5deg
Timing setting
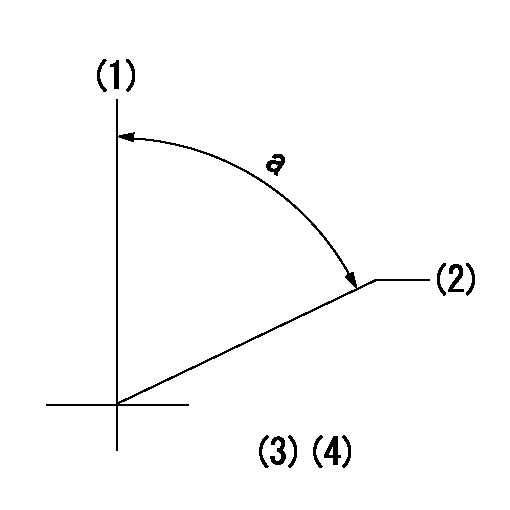
(1)Pump vertical direction
(2)Position of timer's threaded hole at No 1 cylinder's beginning of injection
(3)-
(4)-
----------
----------
a=(60deg)
----------
----------
a=(60deg)
Information:
Performance Analysis Report (PAR) Chassis Dynamometer Test
Required Equipment For Test:
Optional Equipment:
Refer to the latest PAR instructions, Special Instruction Form No. SEHS8025, for more detailed instructions concerning preparation of the truck, proper use of the dynamometer and use of the Technical Information File microfiche.Use the following procedure for the PAR Chassis Dynamomenter test:1. Check the fuel API if not done in another procedure. Refer to, Special Instruction, Form No. GMGO0977.2. Record data from the Engine Information Plate.3. Install the required measurement instruments on the engine.4. Operate the engine at partial throttle and load to obtain the normal operating temperature, and then operate the engine at full load for two minutes. While operating at full load, check the fuel pressure [approximately 550 kPa (80 psi)]. If the pressure is low, perform Procedure No. 113T (part of Truck Performance Diagnostic Guide, Form No. SEBD0808), before continuing the test.5. Beginning from Top Engine Limit, load the engine to each test rpm, 5 rpm, for at least two minutes for proper stabilization.6. Record engine test information, in sequence if possible, on the record sheets. If repeat runs are required to complete the sheets, be sure temperatures and conditions are as equal as possible.7.
Required Equipment For Test:
Optional Equipment:
Refer to the latest PAR instructions, Special Instruction Form No. SEHS8025, for more detailed instructions concerning preparation of the truck, proper use of the dynamometer and use of the Technical Information File microfiche.Use the following procedure for the PAR Chassis Dynamomenter test:1. Check the fuel API if not done in another procedure. Refer to, Special Instruction, Form No. GMGO0977.2. Record data from the Engine Information Plate.3. Install the required measurement instruments on the engine.4. Operate the engine at partial throttle and load to obtain the normal operating temperature, and then operate the engine at full load for two minutes. While operating at full load, check the fuel pressure [approximately 550 kPa (80 psi)]. If the pressure is low, perform Procedure No. 113T (part of Truck Performance Diagnostic Guide, Form No. SEBD0808), before continuing the test.5. Beginning from Top Engine Limit, load the engine to each test rpm, 5 rpm, for at least two minutes for proper stabilization.6. Record engine test information, in sequence if possible, on the record sheets. If repeat runs are required to complete the sheets, be sure temperatures and conditions are as equal as possible.7.