Information injection-pump assembly
BOSCH
9 400 615 527
9400615527
ZEXEL
101606-6620
1016066620
MITSUBISHI
ME076339
me076339
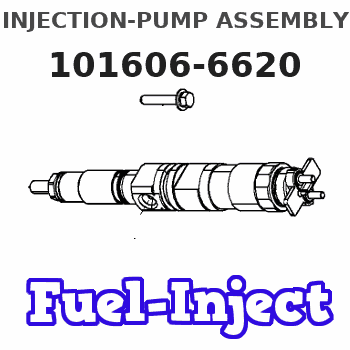
Rating:
Service parts 101606-6620 INJECTION-PUMP ASSEMBLY:
1.
_
6.
COUPLING PLATE
7.
COUPLING PLATE
8.
_
9.
_
11.
Nozzle and Holder
ME035655
12.
Open Pre:MPa(Kqf/cm2)
21.6{220}
15.
NOZZLE SET
Include in #1:
101606-6620
as INJECTION-PUMP ASSEMBLY
Include in #2:
104749-5500
as _
Cross reference number
BOSCH
9 400 615 527
9400615527
ZEXEL
101606-6620
1016066620
MITSUBISHI
ME076339
me076339
Zexel num
Bosch num
Firm num
Name
9 400 615 527
ME076339 MITSUBISHI
INJECTION-PUMP ASSEMBLY
6D14 * K 14BE INJECTION PUMP ASSY PE6A PE
6D14 * K 14BE INJECTION PUMP ASSY PE6A PE
Calibration Data:
Adjustment conditions
Test oil
1404 Test oil ISO4113 or {SAEJ967d}
1404 Test oil ISO4113 or {SAEJ967d}
Test oil temperature
degC
40
40
45
Nozzle and nozzle holder
105780-8140
Bosch type code
EF8511/9A
Nozzle
105780-0000
Bosch type code
DN12SD12T
Nozzle holder
105780-2080
Bosch type code
EF8511/9
Opening pressure
MPa
17.2
Opening pressure
kgf/cm2
175
Injection pipe
Outer diameter - inner diameter - length (mm) mm 6-2-600
Outer diameter - inner diameter - length (mm) mm 6-2-600
Overflow valve
131424-5520
Overflow valve opening pressure
kPa
255
221
289
Overflow valve opening pressure
kgf/cm2
2.6
2.25
2.95
Tester oil delivery pressure
kPa
157
157
157
Tester oil delivery pressure
kgf/cm2
1.6
1.6
1.6
Direction of rotation (viewed from drive side)
Left L
Left L
Injection timing adjustment
Direction of rotation (viewed from drive side)
Left L
Left L
Injection order
1-5-3-6-
2-4
Pre-stroke
mm
3.3
3.25
3.35
Beginning of injection position
Governor side NO.1
Governor side NO.1
Difference between angles 1
Cal 1-5 deg. 60 59.5 60.5
Cal 1-5 deg. 60 59.5 60.5
Difference between angles 2
Cal 1-3 deg. 120 119.5 120.5
Cal 1-3 deg. 120 119.5 120.5
Difference between angles 3
Cal 1-6 deg. 180 179.5 180.5
Cal 1-6 deg. 180 179.5 180.5
Difference between angles 4
Cyl.1-2 deg. 240 239.5 240.5
Cyl.1-2 deg. 240 239.5 240.5
Difference between angles 5
Cal 1-4 deg. 300 299.5 300.5
Cal 1-4 deg. 300 299.5 300.5
Injection quantity adjustment
Adjusting point
-
Rack position
11
Pump speed
r/min
850
850
850
Each cylinder's injection qty
mm3/st.
65
63
67
Basic
*
Fixing the rack
*
Standard for adjustment of the maximum variation between cylinders
*
Injection quantity adjustment_02
Adjusting point
H
Rack position
9.5+-0.5
Pump speed
r/min
275
275
275
Each cylinder's injection qty
mm3/st.
10.5
9
12
Fixing the rack
*
Standard for adjustment of the maximum variation between cylinders
*
Injection quantity adjustment_03
Adjusting point
A
Rack position
R1(11)
Pump speed
r/min
850
850
850
Average injection quantity
mm3/st.
65
64
66
Basic
*
Fixing the lever
*
Injection quantity adjustment_04
Adjusting point
B
Rack position
R1(11)
Pump speed
r/min
1450
1450
1450
Average injection quantity
mm3/st.
77.5
75.5
79.5
Fixing the lever
*
Injection quantity adjustment_05
Adjusting point
C
Rack position
R1+0.4
Pump speed
r/min
600
600
600
Average injection quantity
mm3/st.
59.7
55.7
63.7
Fixing the lever
*
Injection quantity adjustment_06
Adjusting point
I
Rack position
14.1+-0.
5
Pump speed
r/min
100
100
100
Average injection quantity
mm3/st.
90
70
110
Fixing the lever
*
Rack limit
*
Timer adjustment
Pump speed
r/min
900--
Advance angle
deg.
0
0
0
Remarks
Start
Start
Timer adjustment_02
Pump speed
r/min
850
Advance angle
deg.
0.5
Timer adjustment_03
Pump speed
r/min
900
Advance angle
deg.
0.8
Timer adjustment_04
Pump speed
r/min
1200
Advance angle
deg.
2.6
2.1
3.1
Timer adjustment_05
Pump speed
r/min
1500
Advance angle
deg.
5.5
5
6
Remarks
Finish
Finish
Test data Ex:
Governor adjustment
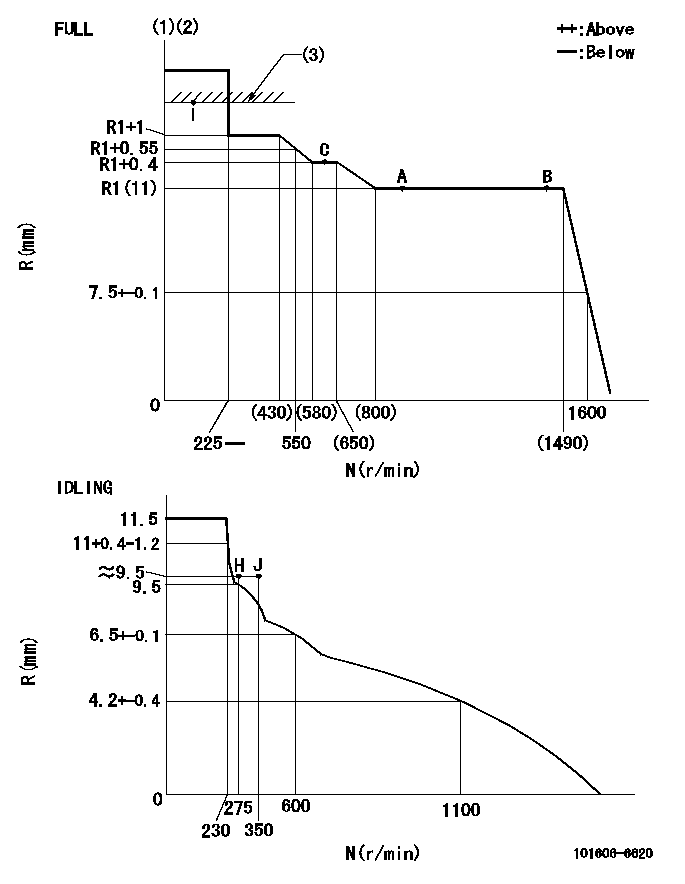
N:Pump speed
R:Rack position (mm)
(1)Torque cam stamping: T1
(2)Tolerance for racks not indicated: +-0.05mm.
(3)RACK LIMIT
----------
T1=D52
----------
----------
T1=D52
----------
Speed control lever angle

F:Full speed
I:Idle
(1)Use the hole at R = aa
(2)Stopper bolt set position 'H'
----------
aa=35mm
----------
a=33deg+-5deg b=40.5deg+-3deg
----------
aa=35mm
----------
a=33deg+-5deg b=40.5deg+-3deg
Stop lever angle

N:Engine manufacturer's normal use
S:Stop the pump.
(1)Set the stopper bolt at pump speed = aa and rack position = bb (non-injection rack position). Confirm non-injection.
(2)After setting the stopper bolt, confirm non-injection at speed cc. Rack position = dd (non-injection rack position).
(3)Rack position = approximately ee.
(4)Free (at shipping)
----------
aa=1550r/min bb=5.4-0.5mm cc=275r/min dd=(7.4)mm ee=17.4mm
----------
a=17deg+-5deg b=2deg+-5deg c=(27deg)
----------
aa=1550r/min bb=5.4-0.5mm cc=275r/min dd=(7.4)mm ee=17.4mm
----------
a=17deg+-5deg b=2deg+-5deg c=(27deg)
0000001501 MICRO SWITCH
Adjustment of the micro-switch
Adjust the bolt to obtain the following lever position when the micro-switch is ON.
(1)Speed N1
(2)Rack position Ra
----------
N1=400r/min Ra=9.2+-0.1mm
----------
----------
N1=400r/min Ra=9.2+-0.1mm
----------
Timing setting

(1)Pump vertical direction
(2)Position of timer's tooth at No 1 cylinder's beginning of injection
(3)B.T.D.C.: aa
(4)-
----------
aa=16deg
----------
a=(1deg)
----------
aa=16deg
----------
a=(1deg)
Information:
Diagnostic Code 52 ECM or Personality Module Fault
Conditions Which Generate This Code:
The Electronic Control Module (ECM) has detected a fault in the Personality Module (PM), the ECM itself or the connector between them.System Response:
Diagnostic Code 52 is current (Diagnostic Lamp, ECAP or DDT) and is LOGGED in memory.Troubleshooting:
Refer to P-220: ECM And Personality Module Test.Diagnostic Code 53 ECM Fault
Conditions Which Generate This Code:
The ECM has detected an internal fault.System Response:
Diagnostic Code 53 is current (Diagnostic Lamp, ECAP, or DDT), and is LOGGED in memory.Troubleshooting:
The ECM must be replaced.Diagnostic Code 55 No Detected Faults
Conditions Which Generate This Code:
There are no ACTIVE Diagnostic Codes in the 3176 System.System Response:
Normal engine operation.Troubleshooting:
Diagnostic Code 55 does NOT indicate a 3176 System fault. It only shows that the system is operating correctly. The ECAP will display a Code 55 if no faults are currently ACTIVE. The Diagnostic Lamp will also flash Code 55 (on demand) if no faults have occurred since power-up.Diagnostic Code 56 Check Customer Or System Parameters
Conditions Which Generate This Code:
One or more of the Customer Specified Parameters and/or System Configuration Parameters are not correctly programmed for the system. Diagnostic Code 56 will be generated if the Electronic Control Module (ECM) has been replaced and any of the parameters have not been programmed.System Response:
1. Diagnostic Code 56 is current (Diagnostic Lamp, ECAP, or DDT), but is NOT LOGGED in memory.2. Engine power may be limited and/or the ECM may limit engine speed to low idle, depending on the parameter causing the Code 56.Troubleshooting:
1. Using an ECAP, read the parameters that triggered the code, shown along with the Diagnostic Code 56 on the " Current Diagnostic Messages" screen.2. Reprogram the displayed parameter(s). Refer to "Programming 3176 Parameters" in Section 2 of this manual.Diagnostic Code 57 Parking Brake Switch Fault
Conditions Which Generate This Code:
1. The Parking Brake Switch indicates the parking brake is ON.-AND-2. Diagnostic Code 36 (Vehicle Speed Signal Out Of Range) is NOT ACTIVE.-AND-3. The ECM reads a vehicle speed greater than 10 mph for at least five seconds.System Response:
1. Diagnostic Code 57 is current (Diagnostic Lamp, ECAP, or DDT), and IS LOGGED in memory.-AND-2. The Idle Shutdown Timer is disabled.Troubleshooting:
Follow P-216: Parking Brake Switch Test, in this manual.Diagnostic Code 63 Low Fuel Pressure Warning
Conditions Which Generate This Code:
1. The engine has been running at least 20 seconds.-AND-2. Diagnostic Code 37 (Fuel Pressure Sensor Fault) is not ACTIVE.-AND-3. Fuel pressure falls below the minimum specified for a given rpm for at least two minutes. Refer to the Chart below for minimum fuel pressure vs. rpm.System Response:
1. Diagnostic Code 63 is current (Diagnostic Lamp, ECAP, or DDT) and is LOGGED in memory.Troubleshooting:
1. Diagnostic Code 63 does NOT indicate a 3176 System fault. It only gives warning that a low fuel pressure condition exists.2. Use the procedures in the "Fuel System Inspection" and "Fuel Transfer Pump" sections of the 3176 Systems Operation Testing And Adjusting Manual, Form SENR3909, to determine the cause of the low fuel pressure condition. Diagnostic Code 72 Cylinder 1
Conditions Which Generate This Code:
The Electronic Control Module (ECM) has detected a fault in the Personality Module (PM), the ECM itself or the connector between them.System Response:
Diagnostic Code 52 is current (Diagnostic Lamp, ECAP or DDT) and is LOGGED in memory.Troubleshooting:
Refer to P-220: ECM And Personality Module Test.Diagnostic Code 53 ECM Fault
Conditions Which Generate This Code:
The ECM has detected an internal fault.System Response:
Diagnostic Code 53 is current (Diagnostic Lamp, ECAP, or DDT), and is LOGGED in memory.Troubleshooting:
The ECM must be replaced.Diagnostic Code 55 No Detected Faults
Conditions Which Generate This Code:
There are no ACTIVE Diagnostic Codes in the 3176 System.System Response:
Normal engine operation.Troubleshooting:
Diagnostic Code 55 does NOT indicate a 3176 System fault. It only shows that the system is operating correctly. The ECAP will display a Code 55 if no faults are currently ACTIVE. The Diagnostic Lamp will also flash Code 55 (on demand) if no faults have occurred since power-up.Diagnostic Code 56 Check Customer Or System Parameters
Conditions Which Generate This Code:
One or more of the Customer Specified Parameters and/or System Configuration Parameters are not correctly programmed for the system. Diagnostic Code 56 will be generated if the Electronic Control Module (ECM) has been replaced and any of the parameters have not been programmed.System Response:
1. Diagnostic Code 56 is current (Diagnostic Lamp, ECAP, or DDT), but is NOT LOGGED in memory.2. Engine power may be limited and/or the ECM may limit engine speed to low idle, depending on the parameter causing the Code 56.Troubleshooting:
1. Using an ECAP, read the parameters that triggered the code, shown along with the Diagnostic Code 56 on the " Current Diagnostic Messages" screen.2. Reprogram the displayed parameter(s). Refer to "Programming 3176 Parameters" in Section 2 of this manual.Diagnostic Code 57 Parking Brake Switch Fault
Conditions Which Generate This Code:
1. The Parking Brake Switch indicates the parking brake is ON.-AND-2. Diagnostic Code 36 (Vehicle Speed Signal Out Of Range) is NOT ACTIVE.-AND-3. The ECM reads a vehicle speed greater than 10 mph for at least five seconds.System Response:
1. Diagnostic Code 57 is current (Diagnostic Lamp, ECAP, or DDT), and IS LOGGED in memory.-AND-2. The Idle Shutdown Timer is disabled.Troubleshooting:
Follow P-216: Parking Brake Switch Test, in this manual.Diagnostic Code 63 Low Fuel Pressure Warning
Conditions Which Generate This Code:
1. The engine has been running at least 20 seconds.-AND-2. Diagnostic Code 37 (Fuel Pressure Sensor Fault) is not ACTIVE.-AND-3. Fuel pressure falls below the minimum specified for a given rpm for at least two minutes. Refer to the Chart below for minimum fuel pressure vs. rpm.System Response:
1. Diagnostic Code 63 is current (Diagnostic Lamp, ECAP, or DDT) and is LOGGED in memory.Troubleshooting:
1. Diagnostic Code 63 does NOT indicate a 3176 System fault. It only gives warning that a low fuel pressure condition exists.2. Use the procedures in the "Fuel System Inspection" and "Fuel Transfer Pump" sections of the 3176 Systems Operation Testing And Adjusting Manual, Form SENR3909, to determine the cause of the low fuel pressure condition. Diagnostic Code 72 Cylinder 1