Information injection-pump assembly
BOSCH
9 400 615 493
9400615493
ZEXEL
101606-6150
1016066150
MITSUBISHI
ME076261
me076261
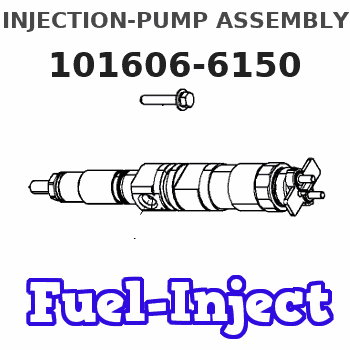
Rating:
Service parts 101606-6150 INJECTION-PUMP ASSEMBLY:
1.
_
6.
COUPLING PLATE
7.
COUPLING PLATE
8.
_
9.
_
11.
Nozzle and Holder
ME035655
12.
Open Pre:MPa(Kqf/cm2)
21.6{220}
15.
NOZZLE SET
Cross reference number
BOSCH
9 400 615 493
9400615493
ZEXEL
101606-6150
1016066150
MITSUBISHI
ME076261
me076261
Zexel num
Bosch num
Firm num
Name
101606-6150
9 400 615 493
ME076261 MITSUBISHI
INJECTION-PUMP ASSEMBLY
6D14 * K
6D14 * K
Calibration Data:
Adjustment conditions
Test oil
1404 Test oil ISO4113 or {SAEJ967d}
1404 Test oil ISO4113 or {SAEJ967d}
Test oil temperature
degC
40
40
45
Nozzle and nozzle holder
105780-8140
Bosch type code
EF8511/9A
Nozzle
105780-0000
Bosch type code
DN12SD12T
Nozzle holder
105780-2080
Bosch type code
EF8511/9
Opening pressure
MPa
17.2
Opening pressure
kgf/cm2
175
Injection pipe
Outer diameter - inner diameter - length (mm) mm 6-2-600
Outer diameter - inner diameter - length (mm) mm 6-2-600
Overflow valve
131424-5520
Overflow valve opening pressure
kPa
255
221
289
Overflow valve opening pressure
kgf/cm2
2.6
2.25
2.95
Tester oil delivery pressure
kPa
157
157
157
Tester oil delivery pressure
kgf/cm2
1.6
1.6
1.6
Direction of rotation (viewed from drive side)
Left L
Left L
Injection timing adjustment
Direction of rotation (viewed from drive side)
Left L
Left L
Injection order
1-5-3-6-
2-4
Pre-stroke
mm
3.3
3.25
3.35
Beginning of injection position
Governor side NO.1
Governor side NO.1
Difference between angles 1
Cal 1-5 deg. 60 59.5 60.5
Cal 1-5 deg. 60 59.5 60.5
Difference between angles 2
Cal 1-3 deg. 120 119.5 120.5
Cal 1-3 deg. 120 119.5 120.5
Difference between angles 3
Cal 1-6 deg. 180 179.5 180.5
Cal 1-6 deg. 180 179.5 180.5
Difference between angles 4
Cyl.1-2 deg. 240 239.5 240.5
Cyl.1-2 deg. 240 239.5 240.5
Difference between angles 5
Cal 1-4 deg. 300 299.5 300.5
Cal 1-4 deg. 300 299.5 300.5
Injection quantity adjustment
Adjusting point
-
Rack position
11
Pump speed
r/min
850
850
850
Each cylinder's injection qty
mm3/st.
65
65
67
Basic
*
Fixing the rack
*
Standard for adjustment of the maximum variation between cylinders
*
Injection quantity adjustment_02
Adjusting point
H
Rack position
9.5+-0.5
Pump speed
r/min
275
275
275
Each cylinder's injection qty
mm3/st.
10.5
9
12
Fixing the rack
*
Standard for adjustment of the maximum variation between cylinders
*
Injection quantity adjustment_03
Adjusting point
A
Rack position
R1(11)
Pump speed
r/min
850
850
850
Average injection quantity
mm3/st.
65
64
66
Basic
*
Fixing the lever
*
Injection quantity adjustment_04
Adjusting point
B
Rack position
R1(11)
Pump speed
r/min
1450
1450
1450
Average injection quantity
mm3/st.
77.5
75.5
79.5
Fixing the lever
*
Injection quantity adjustment_05
Adjusting point
C
Rack position
R1+0.4
Pump speed
r/min
600
600
600
Average injection quantity
mm3/st.
59.7
55.7
63.7
Fixing the lever
*
Injection quantity adjustment_06
Adjusting point
I
Rack position
-
Pump speed
r/min
100
100
100
Average injection quantity
mm3/st.
90
70
110
Fixing the lever
*
Rack limit
*
Timer adjustment
Pump speed
r/min
1250--
Advance angle
deg.
0
0
0
Remarks
Start
Start
Timer adjustment_02
Pump speed
r/min
1200
Advance angle
deg.
0.5
Timer adjustment_03
Pump speed
r/min
1350
Advance angle
deg.
2.4
1.9
2.9
Timer adjustment_04
Pump speed
r/min
1500
Advance angle
deg.
5
4.5
5.5
Remarks
Finish
Finish
Test data Ex:
Governor adjustment
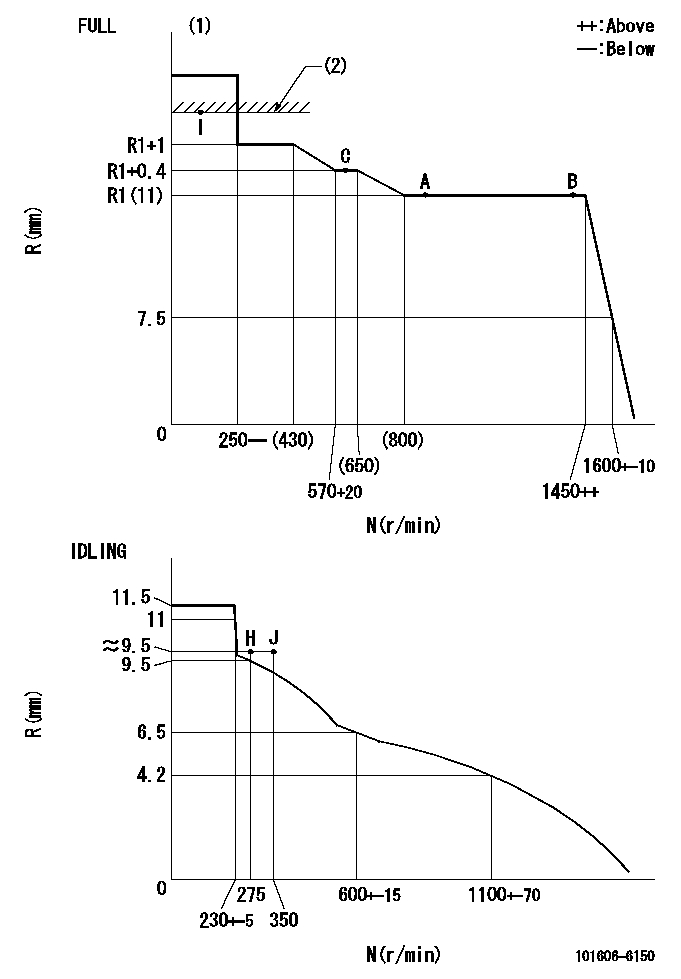
N:Pump speed
R:Rack position (mm)
(1)Torque cam stamping: T1
(2)RACK LIMIT
----------
T1=C67
----------
----------
T1=C67
----------
Speed control lever angle
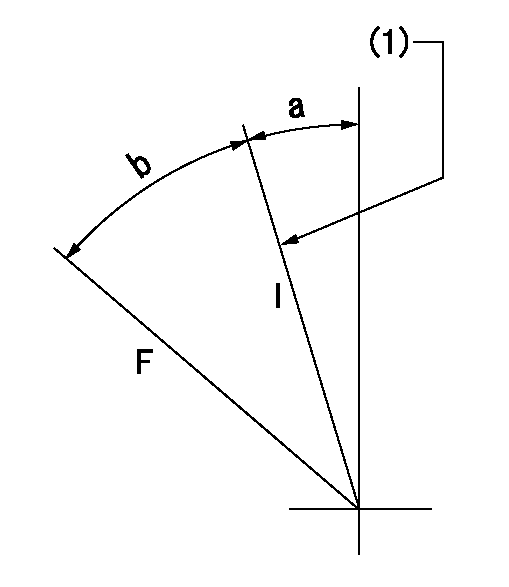
F:Full speed
I:Idle
(1)Stopper bolt set position 'H'
----------
----------
a=18.5deg+-5deg b=40.5deg+-3deg
----------
----------
a=18.5deg+-5deg b=40.5deg+-3deg
Stop lever angle
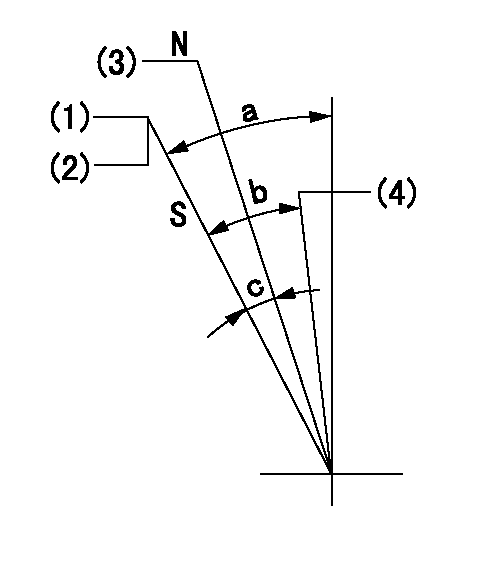
N:Engine manufacturer's normal use
S:Stop the pump.
(1)Set the stopper bolt at speed = rated point and rack position = aa (non-injection rack position). Confirm non-injection.
(2)After setting the stopper bolt , confirm non-injection at pump speed bb. Rack position = cc (non-injection rack position).
(3)Rack position = approximately dd
(4)Free (at shipping)
----------
aa=5.4-0.5mm bb=275r/min cc=(7.4)mm dd=15mm
----------
a=41deg+-5deg b=(29.5deg) c=15.5deg+-3deg
----------
aa=5.4-0.5mm bb=275r/min cc=(7.4)mm dd=15mm
----------
a=41deg+-5deg b=(29.5deg) c=15.5deg+-3deg
0000001501 MICRO SWITCH
Adjustment of the micro-switch
Adjust the bolt to obtain the following lever position when the micro-switch is ON.
(1)Speed N1
(2)Rack position Ra
----------
N1=400+-5r/min Ra=9.2mm
----------
----------
N1=400+-5r/min Ra=9.2mm
----------
Timing setting

(1)Pump vertical direction
(2)Position of timer's tooth at No 1 cylinder's beginning of injection
(3)B.T.D.C.: aa
(4)-
----------
aa=13deg
----------
a=(0deg)
----------
aa=13deg
----------
a=(0deg)
Information:
Illustration 4 g01781374
Illustration 5 g01781397
Relocate the ether canister to the other side. Refer to Illustration 4 and Illustration 5.
Illustration 6 g01781413
(4) 322-7177 Bracket As (15) 8T-4121 Hard Washer (17) 8T-4196 Bolt
Install 322-7177 Bracket As (4) in the same location as the former muffler support bracket (30) by using four 8T-4121 Hard Washers (15), and four 8T-4196 Bolts (17). Refer to Illustration 3 and Illustration 6.
Illustration 7 g01781434
(6) 322-7180 Bracket As (8) 324-1454 Bracket Adapter (10) 5P-4116 Hard Washer (12) 6V-3822 Bolt (15) 8T-4121 Hard Washer (18) 8T-6870 Bolt
Install 322-7180 Bracket As (6) by using two 8T-4121 Hard Washers (15), and two 6V-3822 Bolts (12) to the exhaust elbow mounting holes. Place 324-1454 Bracket Adapter (8) between bracket assembly (6) and the aftercooler core assembly. Secure bracket assembly (6) to bracket adapter (8), and to the aftercooler core assembly by using two 5P-4116 Hard Washers (10), and two 8T-6870 Bolts (18). Refer to Illustration 7.
Illustration 8 g01781454
(5) 322-7179 Plate (15) 8T-4121 Hard Washer (16) 8T-4133 Nut (17) 8T-4196 Bolt
Install 322-7179 Plate (5) on top of bracket assembly (4), and bracket assembly (6). Secure plate (5) loosely using eight 8T-4121 Hard Washers (15), four 8T-4196 Bolts (17), four 8T-4133 Nuts (16). Refer to Illustration 8.
Illustration 9 g01781475
(2) 253-4495 Clamp As
Install two 253-4495 Clamp As (2) on top of plate (5). Use eight hard washers (15), four bolts (17), and four nuts (16). Secure the brackets loosely so that you are able to make adjustments. Refer to Illustration 9.
Illustration 10 g01781478
(c) Inlet tube (7) 322-9842 Diesel Particulate Filter Gp
Install 322-9842 Diesel Particulate Filter Gp (7) on top of the two bottom clamp assemblies (2). Insert inlet tube (c) on top of the exhaust elbow. The weight of the diesel particulate filter group is approximately 60 kg (132 lb). Refer to Illustration 10.
Illustration 11 g01781493
Cut off material from the bracket that originally supported the ether canister (if needed), to fit the diesel particulate filter group. Refer to Illustration 11.
Make sure that the filter is properly placed on top of clamp assemblies (2) and the exhaust elbow. If needed, adjust plate (5), and bracket assemblies (4) and (6). Once diesel particulate filter group (7) is properly positioned, tighten the bolts between the plate and the two bracket assemblies. Also, tighten the bolts of the bottom clamp assemblies (2) .
Illustration 12 g01781513
(d) Outlet tube (1) 7E-3870 Muffler Clamp (3) 277-4718 Clamp As (9) 3B-4508 Lockwasher (11) 5P-8245 Hard Washer (13) 6V-3823 Bolt (14) 6V-8149 Nut
Secure inlet tube (c) of the diesel particulate filter group to the exhaust elbow with one 7E-3870 Muffler Clamp (1). Refer to Illustration 12.
Position one 277-4718 Clamp As (3) over the diesel particulate filter group, and secure the clamp assembly to the bottom clamp assembly (2)
Have questions with 101606-6150?
Group cross 101606-6150 ZEXEL
Mitsubishi
101606-6150
9 400 615 493
ME076261
INJECTION-PUMP ASSEMBLY
6D14
6D14