Information injection-pump assembly
BOSCH
9 400 615 485
9400615485
ZEXEL
101606-6061
1016066061
MITSUBISHI
ME076243
me076243
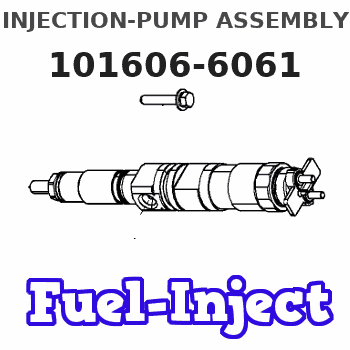
Rating:
Include in #2:
104742-1503
as _
Cross reference number
BOSCH
9 400 615 485
9400615485
ZEXEL
101606-6061
1016066061
MITSUBISHI
ME076243
me076243
Zexel num
Bosch num
Firm num
Name
Calibration Data:
Adjustment conditions
Test oil
1404 Test oil ISO4113 or {SAEJ967d}
1404 Test oil ISO4113 or {SAEJ967d}
Test oil temperature
degC
40
40
45
Nozzle and nozzle holder
105780-8140
Bosch type code
EF8511/9A
Nozzle
105780-0000
Bosch type code
DN12SD12T
Nozzle holder
105780-2080
Bosch type code
EF8511/9
Opening pressure
MPa
17.2
Opening pressure
kgf/cm2
175
Injection pipe
Outer diameter - inner diameter - length (mm) mm 6-2-600
Outer diameter - inner diameter - length (mm) mm 6-2-600
Overflow valve
131424-5520
Overflow valve opening pressure
kPa
255
221
289
Overflow valve opening pressure
kgf/cm2
2.6
2.25
2.95
Tester oil delivery pressure
kPa
157
157
157
Tester oil delivery pressure
kgf/cm2
1.6
1.6
1.6
Direction of rotation (viewed from drive side)
Left L
Left L
Injection timing adjustment
Direction of rotation (viewed from drive side)
Left L
Left L
Injection order
1-5-3-6-
2-4
Pre-stroke
mm
3.5
3.45
3.55
Beginning of injection position
Governor side NO.1
Governor side NO.1
Difference between angles 1
Cal 1-5 deg. 60 59.5 60.5
Cal 1-5 deg. 60 59.5 60.5
Difference between angles 2
Cal 1-3 deg. 120 119.5 120.5
Cal 1-3 deg. 120 119.5 120.5
Difference between angles 3
Cal 1-6 deg. 180 179.5 180.5
Cal 1-6 deg. 180 179.5 180.5
Difference between angles 4
Cyl.1-2 deg. 240 239.5 240.5
Cyl.1-2 deg. 240 239.5 240.5
Difference between angles 5
Cal 1-4 deg. 300 299.5 300.5
Cal 1-4 deg. 300 299.5 300.5
Injection quantity adjustment
Adjusting point
-
Rack position
11.1
Pump speed
r/min
850
850
850
Each cylinder's injection qty
mm3/st.
68
66
70
Basic
*
Fixing the rack
*
Standard for adjustment of the maximum variation between cylinders
*
Injection quantity adjustment_02
Adjusting point
H
Rack position
9.5+-0.5
Pump speed
r/min
275
275
275
Each cylinder's injection qty
mm3/st.
8.7
8.2
9.2
Fixing the rack
*
Standard for adjustment of the maximum variation between cylinders
*
Injection quantity adjustment_03
Adjusting point
A
Rack position
R1(11.1)
Pump speed
r/min
850
850
850
Average injection quantity
mm3/st.
68
67
69
Basic
*
Fixing the lever
*
Injection quantity adjustment_04
Adjusting point
B
Rack position
R1+0.2
Pump speed
r/min
1400
1400
1400
Average injection quantity
mm3/st.
79.9
75.9
83.9
Fixing the lever
*
Injection quantity adjustment_05
Adjusting point
D
Rack position
R1+0.2
Pump speed
r/min
500
500
500
Average injection quantity
mm3/st.
52.4
48.4
56.4
Fixing the lever
*
Injection quantity adjustment_06
Adjusting point
I
Rack position
-
Pump speed
r/min
100
100
100
Average injection quantity
mm3/st.
85
65
105
Fixing the lever
*
Rack limit
*
Timer adjustment
Pump speed
r/min
1150
Advance angle
deg.
0.5
Timer adjustment_02
Pump speed
r/min
1250
Advance angle
deg.
2.5
2
3
Timer adjustment_03
Pump speed
r/min
1350
Advance angle
deg.
5
4.5
5.5
Remarks
Finish
Finish
Test data Ex:
Governor adjustment
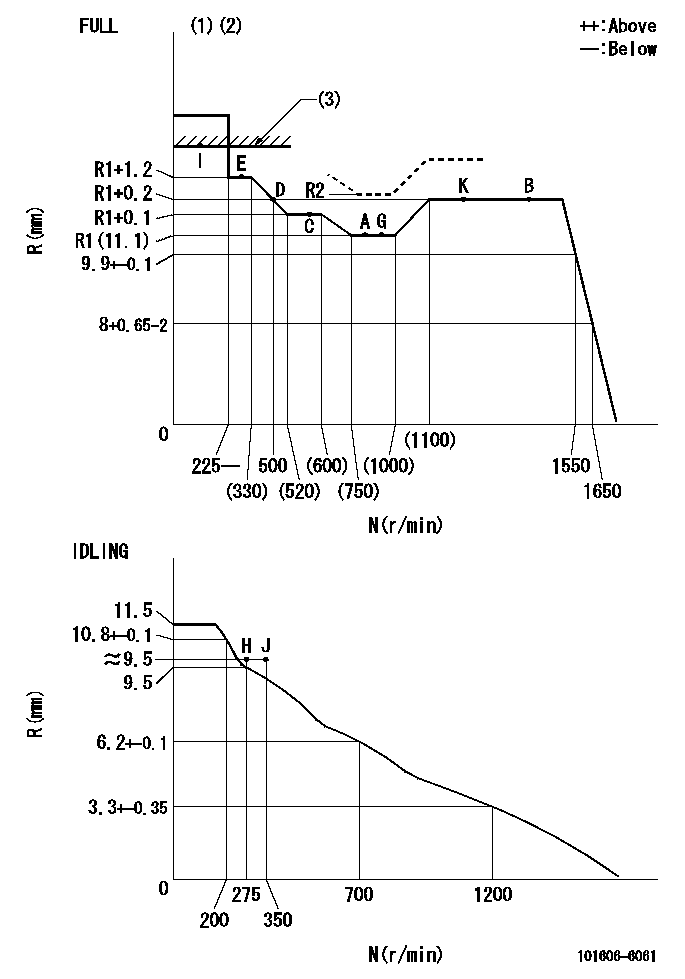
N:Pump speed
R:Rack position (mm)
(1)Torque cam stamping: T1
(2)Tolerance for racks not indicated: +-0.05mm.
(3)RACK LIMIT
----------
T1=C85
----------
----------
T1=C85
----------
Speed control lever angle
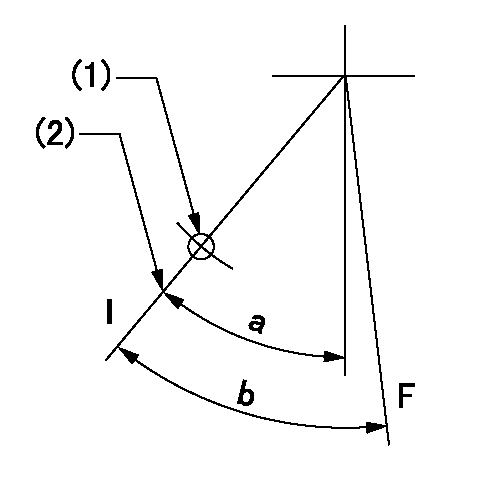
F:Full speed
I:Idle
(1)Use the hole at R = aa
(2)Stopper bolt set position 'H'
----------
aa=35mm
----------
a=33deg+-5deg b=39deg+-3deg
----------
aa=35mm
----------
a=33deg+-5deg b=39deg+-3deg
Stop lever angle
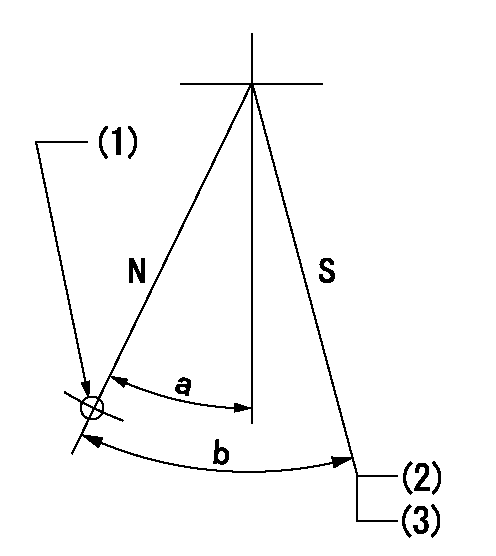
N:Pump normal
S:Stop the pump.
(1)Use the hole at R = aa
(2)Set the stopper bolt at speed = bb and rack position = cc (non-injection rack position). Confirm non-injection.
(3)After setting the stopper bolt, confirm non-injection at speed dd. Rack position = ee (non-injection rack position)
----------
aa=50mm bb=1400r/min cc=(6.5)mm dd=275r/min ee=(6.5)mm
----------
a=25deg+-5deg b=(27deg)+-5deg
----------
aa=50mm bb=1400r/min cc=(6.5)mm dd=275r/min ee=(6.5)mm
----------
a=25deg+-5deg b=(27deg)+-5deg
0000001501 MICRO SWITCH
Adjustment of the micro-switch
Adjust the bolt to obtain the following lever position when the micro-switch is ON.
(1)Speed N1
(2)Rack position Ra
----------
N1=400r/min Ra=9.2+-0.1mm
----------
----------
N1=400r/min Ra=9.2+-0.1mm
----------
0000001601 TAMPER PROOF
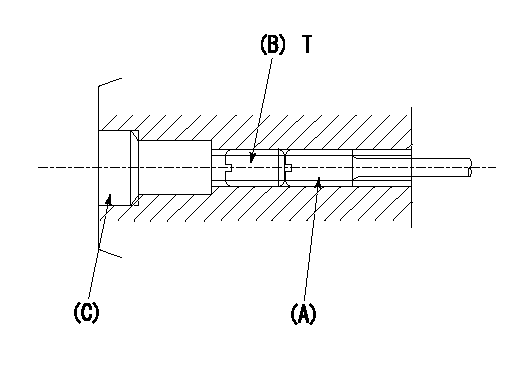
1. Method for setting tamperproof proofing
(1)After governor adjustment (torque cam phase adjustment), move the load lever to increase the full rack position to Ra.
(2)At speed N1 screw in screw (A) to obtain the rack position (actual measurement: Rb) for injection quantity Q1.
(3)Temporarily caulk using the tip of a screwdriver
(4)Confirm that the rack at that time is at Rc.
(5)Lock using setscrew (B). (Tightening torque = T)
(6)Next, coat (C) with adhesive and then pressfit.
(7)Then, readjust the full rack position using the load lever.
----------
N1=850r/min Q1=80.1+-1mm3/st Ra=(0.4)mm Rb=R2mm Rc=R3mm
----------
T=3.4~4.9N-m(0.35~0.5Kgf-m)
----------
N1=850r/min Q1=80.1+-1mm3/st Ra=(0.4)mm Rb=R2mm Rc=R3mm
----------
T=3.4~4.9N-m(0.35~0.5Kgf-m)
0000001701 LEVER

(A) Accelerator lever stopper bolt
(B) Link
(c) Nut
(D) Lever
(E) Pin
(f) lever
(G) Stopper bolt
(H) Return spring
(J) Pin (E) contacts lever.
(K) Load sensor terminal
(1)Black
(2)Blue-yellow
(3)Blue-red
Setting the accelerator lever angle, load sensor adjustment
1. Accelerator lever setting method
(1)Position the speed lever against the idle stopper bolt and fix.
(2)Screw in the accelerator lever stopper bolt (A) and back off the stopper bolt (A) from the position where the accelerator lever pin contacts the speed lever and set. (Gap: approx. 1 mm)
Tightening torque: 4.9~7 N.m {0.5~0.7 kgf.m}
2. Load sensor adjustment (See fig 1)
(1)Load sensor output measuring circuit
Apply DC5+-0.01V to the load sensor terminals and measure the output voltage.
(2)Load sensor output adjustment procedure
Hold the speed lever against the full side stopper bolt and fix. Adjust the load sensor output voltage to VF = 0.417+-0.1 V using the link (B) and then fix temporarily using nut (C).
Turn the speed lever from the idle side to the full side and confirm that output voltage VF = 0.417+-0.1 V is obtained. Confirm several times and then fix using nut (C).
Tightening torque: 3.4~4.9 N.m {0.35~0.5 kgf.m}
3. Setting the step motor's idle side stopper bolt
After adjustment in previous 1 and 2, position speed lever against idle stopper bolt and fix. Then, screw in stopper bolt G until step motor lever D's pin E contacts lever F. Back off 10+2 deg (approx. 3.5 mm) from this position and fix G. (See fig. 3)
4. Speed lever return confirmation
(1)Remove return spring (H) and confirm that the speed lever is returned to the idle position by the torsion spring.
(2)Reinstall the return spring (H) in its original position.
----------
----------
----------
----------
Timing setting

(1)Pump vertical direction
(2)Position of timer's tooth at No 1 cylinder's beginning of injection
(3)B.T.D.C.: aa
(4)-
----------
aa=12deg
----------
a=(1deg)
----------
aa=12deg
----------
a=(1deg)
Information:
Introduction
The 7C8966, 7C8972, 8N5651, 8N5887, 9N0495, and 9N5864 Fuel Injection Pump Groups (new), or the 0R0766, 0R0902, 0R0903, 0R2374, and 0R2385 Fuel Injection Pump Group [remanufactured - (reconditioning has been done to a used fuel injection pump and governor group to give the same quality as a new pump group)] are service replacements for the fuel injection pump and governor groups used on 3208 engines, according to the adaptability shown in the chart. These service groups have only those gaskets and seals that are needed to install the fuel injection pump and governor on the engine.Reference: Parts Manual, Service Manual, Engine Information Plate, Fuel Setting Information Microfiche, Fuel System and Related Information MicroficheDo not perform any procedure, outlined in this publication, or order any parts until you read and understand the information contained within.Service Group Chart
Removal and Installation
1. Remove the pump and governor from the engine. Refer to the Service Manual.
When a replacement fuel injection pump and governor is installed on an engine (or when replacement parts are put in a fuel injection pump and governor), use the information on the engine information plate and always check engine low idle speed, set point and the fuel setting dimension. These settings and dimensions must be checked and adjustments made by a mechanic that has the necessary training in fuel system maintenance. Before the fuel system checks and adjustment are made, remove the original factory fuel system seal. After all fuel system work has been completed, install your Dealer seal as a replacement seal. Refer to Fuel System and Related Information or Fuel Setting Information for additional specifications.
2. Put the new service pump group in a 2P8315 Bracket Assembly (1) so it will be easier to work on. Remove the shut-off solenoid and the solenoid ground wire from the old fuel system. Remove the fuel line fittings from the old fuel system. Install these parts in the same location on the new fuel system.3. Locate the engine serial number and write it down. Make reference to the Fuel Setting Information or Fuel System and Related Information to find the part number of the governor high idle spring that is needed for the engine. The same part number governor high idle spring given in the Fuel Setting Information, or the Fuel System and Related Information must be installed in the new service pump group. The 9L6508 High Idle Spring is already installed in the service pump and governor groups. The governor high idle spring needs to be changed only if the needed part number is different than 9L6508. If it is necessary to change the high idle spring, refer to the Service Manual. The part number of the low idle spring is 4N5663 and is the same for all fuel systems.4. A 4N0527 Overfueling Spring is installed in the service pump and governor groups. Refer to the Parts Manual to determine which overfueling spring is required. If the overfueling spring must be changed, refer to the Service Manual for the
The 7C8966, 7C8972, 8N5651, 8N5887, 9N0495, and 9N5864 Fuel Injection Pump Groups (new), or the 0R0766, 0R0902, 0R0903, 0R2374, and 0R2385 Fuel Injection Pump Group [remanufactured - (reconditioning has been done to a used fuel injection pump and governor group to give the same quality as a new pump group)] are service replacements for the fuel injection pump and governor groups used on 3208 engines, according to the adaptability shown in the chart. These service groups have only those gaskets and seals that are needed to install the fuel injection pump and governor on the engine.Reference: Parts Manual, Service Manual, Engine Information Plate, Fuel Setting Information Microfiche, Fuel System and Related Information MicroficheDo not perform any procedure, outlined in this publication, or order any parts until you read and understand the information contained within.Service Group Chart
Removal and Installation
1. Remove the pump and governor from the engine. Refer to the Service Manual.
When a replacement fuel injection pump and governor is installed on an engine (or when replacement parts are put in a fuel injection pump and governor), use the information on the engine information plate and always check engine low idle speed, set point and the fuel setting dimension. These settings and dimensions must be checked and adjustments made by a mechanic that has the necessary training in fuel system maintenance. Before the fuel system checks and adjustment are made, remove the original factory fuel system seal. After all fuel system work has been completed, install your Dealer seal as a replacement seal. Refer to Fuel System and Related Information or Fuel Setting Information for additional specifications.
2. Put the new service pump group in a 2P8315 Bracket Assembly (1) so it will be easier to work on. Remove the shut-off solenoid and the solenoid ground wire from the old fuel system. Remove the fuel line fittings from the old fuel system. Install these parts in the same location on the new fuel system.3. Locate the engine serial number and write it down. Make reference to the Fuel Setting Information or Fuel System and Related Information to find the part number of the governor high idle spring that is needed for the engine. The same part number governor high idle spring given in the Fuel Setting Information, or the Fuel System and Related Information must be installed in the new service pump group. The 9L6508 High Idle Spring is already installed in the service pump and governor groups. The governor high idle spring needs to be changed only if the needed part number is different than 9L6508. If it is necessary to change the high idle spring, refer to the Service Manual. The part number of the low idle spring is 4N5663 and is the same for all fuel systems.4. A 4N0527 Overfueling Spring is installed in the service pump and governor groups. Refer to the Parts Manual to determine which overfueling spring is required. If the overfueling spring must be changed, refer to the Service Manual for the