Information injection-pump assembly
ZEXEL
101606-1730
1016061730
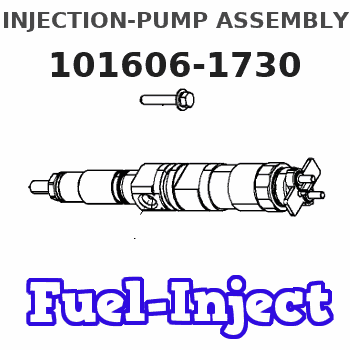
Rating:
Cross reference number
ZEXEL
101606-1730
1016061730
Zexel num
Bosch num
Firm num
Name
Calibration Data:
Adjustment conditions
Test oil
1404 Test oil ISO4113 or {SAEJ967d}
1404 Test oil ISO4113 or {SAEJ967d}
Test oil temperature
degC
40
40
45
Nozzle and nozzle holder
105780-8140
Bosch type code
EF8511/9A
Nozzle
105780-0000
Bosch type code
DN12SD12T
Nozzle holder
105780-2080
Bosch type code
EF8511/9
Opening pressure
MPa
17.2
Opening pressure
kgf/cm2
175
Injection pipe
Outer diameter - inner diameter - length (mm) mm 6-2-600
Outer diameter - inner diameter - length (mm) mm 6-2-600
Overflow valve
131424-5520
Overflow valve opening pressure
kPa
255
221
289
Overflow valve opening pressure
kgf/cm2
2.6
2.25
2.95
Tester oil delivery pressure
kPa
157
157
157
Tester oil delivery pressure
kgf/cm2
1.6
1.6
1.6
Direction of rotation (viewed from drive side)
Left L
Left L
Injection timing adjustment
Direction of rotation (viewed from drive side)
Left L
Left L
Injection order
1-5-3-6-
2-4
Pre-stroke
mm
3
2.95
3.05
Beginning of injection position
Governor side NO.1
Governor side NO.1
Difference between angles 1
Cal 1-5 deg. 60 59.5 60.5
Cal 1-5 deg. 60 59.5 60.5
Difference between angles 2
Cal 1-3 deg. 120 119.5 120.5
Cal 1-3 deg. 120 119.5 120.5
Difference between angles 3
Cal 1-6 deg. 180 179.5 180.5
Cal 1-6 deg. 180 179.5 180.5
Difference between angles 4
Cyl.1-2 deg. 240 239.5 240.5
Cyl.1-2 deg. 240 239.5 240.5
Difference between angles 5
Cal 1-4 deg. 300 299.5 300.5
Cal 1-4 deg. 300 299.5 300.5
Injection quantity adjustment
Adjusting point
-
Rack position
12.1
Pump speed
r/min
800
800
800
Each cylinder's injection qty
mm3/st.
88
85.4
90.6
Basic
*
Fixing the rack
*
Standard for adjustment of the maximum variation between cylinders
*
Injection quantity adjustment_02
Adjusting point
H
Rack position
9.5+-0.5
Pump speed
r/min
275
275
275
Each cylinder's injection qty
mm3/st.
10.5
9
12
Fixing the rack
*
Standard for adjustment of the maximum variation between cylinders
*
Injection quantity adjustment_03
Adjusting point
A
Rack position
R1(12.1)
Pump speed
r/min
800
800
800
Average injection quantity
mm3/st.
88
87
89
Basic
*
Fixing the lever
*
Boost pressure
kPa
49.3
49.3
Boost pressure
mmHg
370
370
Injection quantity adjustment_04
Adjusting point
C
Rack position
(R1-0.8)
Pump speed
r/min
600
600
600
Average injection quantity
mm3/st.
67
65
69
Fixing the lever
*
Boost pressure
kPa
18.7
18.7
Boost pressure
mmHg
140
140
Injection quantity adjustment_05
Adjusting point
I
Rack position
-
Pump speed
r/min
100
100
100
Average injection quantity
mm3/st.
110
90
130
Fixing the lever
*
Rack limit
*
Boost compensator adjustment
Pump speed
r/min
600
600
600
Rack position
R1-1.1
Boost pressure
kPa
13.3
13.3
13.3
Boost pressure
mmHg
100
100
100
Boost compensator adjustment_02
Pump speed
r/min
600
600
600
Rack position
(R1-0.8)
Boost pressure
kPa
18.7
17.4
20
Boost pressure
mmHg
140
130
150
Boost compensator adjustment_03
Pump speed
r/min
600
600
600
Rack position
R1(12.1)
Boost pressure
kPa
36
29.3
42.7
Boost pressure
mmHg
270
220
320
Timer adjustment
Pump speed
r/min
1250--
Advance angle
deg.
0
0
0
Remarks
Start
Start
Timer adjustment_02
Pump speed
r/min
1200
Advance angle
deg.
0.5
Timer adjustment_03
Pump speed
r/min
1300
Advance angle
deg.
1.6
1.1
2.1
Timer adjustment_04
Pump speed
r/min
1400
Advance angle
deg.
3.5
3
4
Remarks
Finish
Finish
Test data Ex:
Governor adjustment
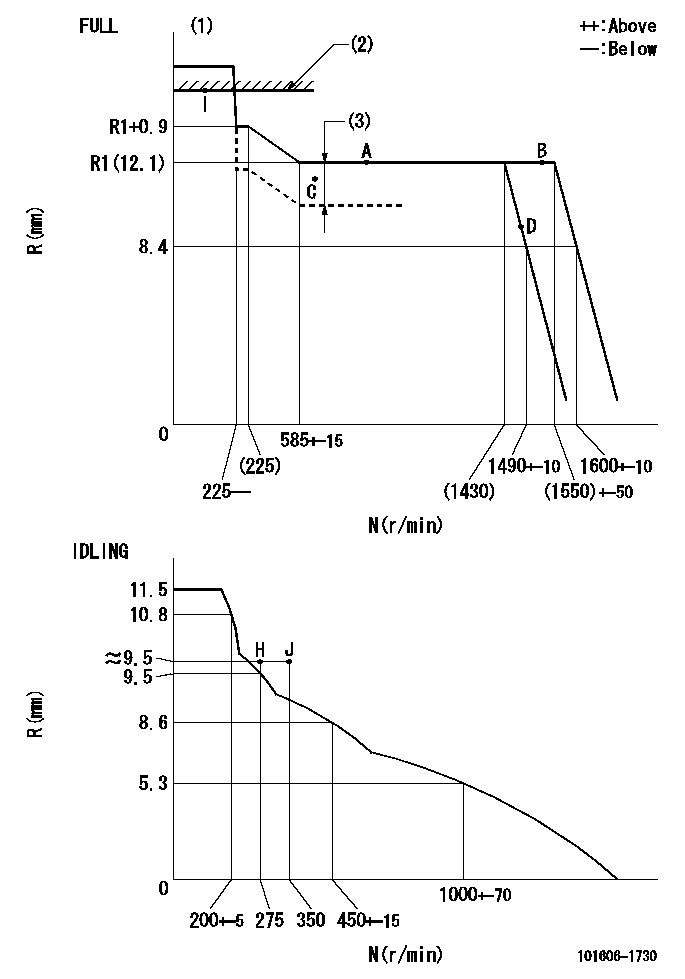
N:Pump speed
R:Rack position (mm)
(1)Torque cam stamping: T1
(2)RACK LIMIT
(3)Boost compensator stroke: BCL
----------
T1=B45 BCL=1.1+-0.1mm
----------
----------
T1=B45 BCL=1.1+-0.1mm
----------
Speed control lever angle
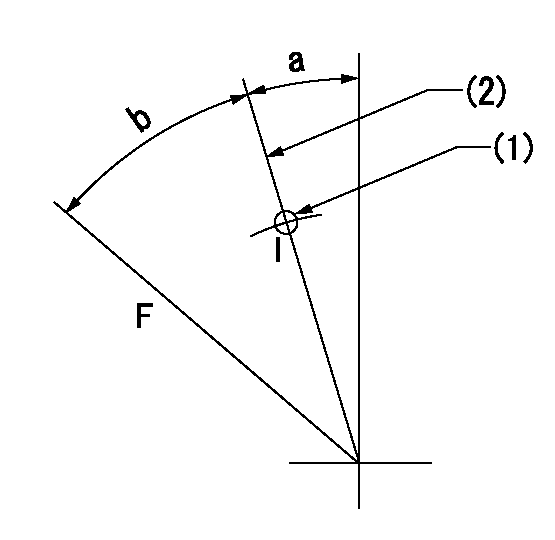
F:Full speed
I:Idle
(1)Use the hole at R = aa
(2)Stopper bolt set position 'H'
----------
aa=40mm
----------
a=18.5deg+-5deg b=(46deg)+-3deg
----------
aa=40mm
----------
a=18.5deg+-5deg b=(46deg)+-3deg
Stop lever angle

N:Engine manufacturer's normal use
S:Stop the pump.
(1)Set the stopper bolt at pump speed = aa and rack position = bb (non-injection rack position). Confirm non-injection.
(2)After setting the stopper bolt, confirm non-injection at speed cc. Rack position = dd (non-injection rack position).
(3)Rack position = approximately ee.
(4)Free (at shipping)
(5)At hole above R = ff.
----------
aa=1550r/min bb=(7.5)mm cc=275r/min dd=(9)mm ee=17.4mm ff=50mm
----------
a=38.5deg+-5deg b=(27deg) c=17deg+-5deg
----------
aa=1550r/min bb=(7.5)mm cc=275r/min dd=(9)mm ee=17.4mm ff=50mm
----------
a=38.5deg+-5deg b=(27deg) c=17deg+-5deg
0000001201
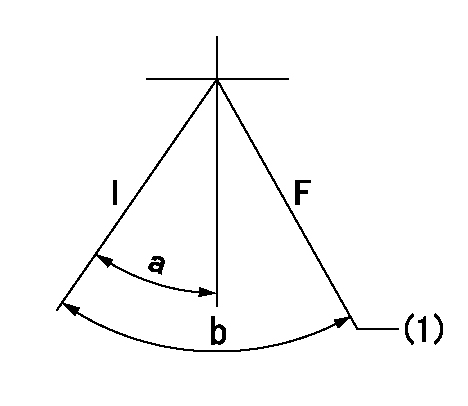
I:Idle
F:At operation, hold it in the full speed position.
(1)Rack position = aa, speed = bb.
----------
aa=8.4mm bb=1490r/min
----------
a=15deg+-5deg b=(41deg)+-3deg
----------
aa=8.4mm bb=1490r/min
----------
a=15deg+-5deg b=(41deg)+-3deg
0000001501 MICRO SWITCH
Adjustment of the micro-switch
Adjust the bolt to obtain the following lever position when the micro-switch is ON.
(1)Speed N1
(2)Rack position Ra
----------
N1=400+-5r/min Ra=9.2mm
----------
----------
N1=400+-5r/min Ra=9.2mm
----------
Timing setting

(1)Pump vertical direction
(2)Position of timer's tooth at No 1 cylinder's beginning of injection
(3)B.T.D.C.: aa
(4)-
----------
aa=15deg
----------
a=(0deg)
----------
aa=15deg
----------
a=(0deg)
Information:
Inspect/Replace
Alternator and Fan Drive Belts
Inspect the condition and adjustment of alternator and accessory drive belts. Examine all drive belts for wear and replace if they show any signs of wear. Loose or worn pulley grooves cause belt slippage and low accessory drive speed. If belts are too loose, they vibrate enough to cause unnecessary wear on the belts and pulleys and possibly slip enough to cause overheating.If belts are too tight, unnecessary stresses are placed upon the pulley bearings and belts which might shorten the life of both.If one belt in a set requires replacement, always install a new matched set of belts. Never replace just the worn belt. If only the worn belt is replaced, the new belt will carry all the load, as it will not be stretched as much as the older belts. All the belts will fail in rapid succession.Adjust
1. Remove belt guard. Inspect the condition and adjustment of alternator belts and accessory drive belts, if equipped.2. To check the belt tension, apply 110 Newton (25 lb) force, perpendicular to the belt, midway between the driving and driven pulley. Measure the belt deflection. Correctly adjusted belts will deflect 15 to 20 mm (9/16 to 7/8 inch).If the belt does not require replacement or adjustment, install the belt guard. If the belt requires adjustment or replacement, do not install the belt guard. Perform the following procedure to adjust the belt tension.
(1) Typical belt assembly mounting bolt(2) adjusting nut3. Loosen the mounting bolt (1).4. Loosen the bracket adjusting nut(s) (2).5. Tighten or loosen the bracket adjusting nut(s) to obtain the correct adjustment.6. Tighten nuts (1) and (2).7. Check the belt tension. If the belt tension requires further adjustment, repeat steps 3 through 6.8. Install the belt guard.If new belts are installed, check the belt adjustment again after 30 minutes of engine operation.Hoses and Clamps
* Inspect all hoses for leaks due to cracking, softness and loose clamps. Replace hoses that are cracked or soft and tighten loose clamps.
Do not bend or strike high pressure lines. Do not install bent or damaged lines, tubes or hoses. Repair any loose or damaged fuel and oil lines, tubes and hoses. Leaks can cause fires. Inspect all lines, tubes and hoses carefully. Tighten all connections to the recommended torque.
Check for the following:* End fittings damaged, leaking or displaced.* Outer covering chafed or cut and wire reinforcing exposed.* Outer covering ballooning locally.* Evidence of kinking or crushing of the flexible part of the hose.* Armoring embedded in the outer cover.A constant torque hose clamp can be used in place of any standard hose clamp. Make sure the constant torque hose clamp is the same size as the standard clamp. Due to extreme temperature changes, hose will heat set. Heat setting causes hose clamps to loosen. Loose hose clamps can result in leaks. There have been reports of component failures caused by hose clamps loosening. The new, constant torque hose clamp will help prevent these failures.Each installation application can be different depending on
Alternator and Fan Drive Belts
Inspect the condition and adjustment of alternator and accessory drive belts. Examine all drive belts for wear and replace if they show any signs of wear. Loose or worn pulley grooves cause belt slippage and low accessory drive speed. If belts are too loose, they vibrate enough to cause unnecessary wear on the belts and pulleys and possibly slip enough to cause overheating.If belts are too tight, unnecessary stresses are placed upon the pulley bearings and belts which might shorten the life of both.If one belt in a set requires replacement, always install a new matched set of belts. Never replace just the worn belt. If only the worn belt is replaced, the new belt will carry all the load, as it will not be stretched as much as the older belts. All the belts will fail in rapid succession.Adjust
1. Remove belt guard. Inspect the condition and adjustment of alternator belts and accessory drive belts, if equipped.2. To check the belt tension, apply 110 Newton (25 lb) force, perpendicular to the belt, midway between the driving and driven pulley. Measure the belt deflection. Correctly adjusted belts will deflect 15 to 20 mm (9/16 to 7/8 inch).If the belt does not require replacement or adjustment, install the belt guard. If the belt requires adjustment or replacement, do not install the belt guard. Perform the following procedure to adjust the belt tension.
(1) Typical belt assembly mounting bolt(2) adjusting nut3. Loosen the mounting bolt (1).4. Loosen the bracket adjusting nut(s) (2).5. Tighten or loosen the bracket adjusting nut(s) to obtain the correct adjustment.6. Tighten nuts (1) and (2).7. Check the belt tension. If the belt tension requires further adjustment, repeat steps 3 through 6.8. Install the belt guard.If new belts are installed, check the belt adjustment again after 30 minutes of engine operation.Hoses and Clamps
* Inspect all hoses for leaks due to cracking, softness and loose clamps. Replace hoses that are cracked or soft and tighten loose clamps.
Do not bend or strike high pressure lines. Do not install bent or damaged lines, tubes or hoses. Repair any loose or damaged fuel and oil lines, tubes and hoses. Leaks can cause fires. Inspect all lines, tubes and hoses carefully. Tighten all connections to the recommended torque.
Check for the following:* End fittings damaged, leaking or displaced.* Outer covering chafed or cut and wire reinforcing exposed.* Outer covering ballooning locally.* Evidence of kinking or crushing of the flexible part of the hose.* Armoring embedded in the outer cover.A constant torque hose clamp can be used in place of any standard hose clamp. Make sure the constant torque hose clamp is the same size as the standard clamp. Due to extreme temperature changes, hose will heat set. Heat setting causes hose clamps to loosen. Loose hose clamps can result in leaks. There have been reports of component failures caused by hose clamps loosening. The new, constant torque hose clamp will help prevent these failures.Each installation application can be different depending on