Information injection-pump assembly
BOSCH
9 400 615 448
9400615448
ZEXEL
101606-1442
1016061442
MITSUBISHI
ME056655
me056655
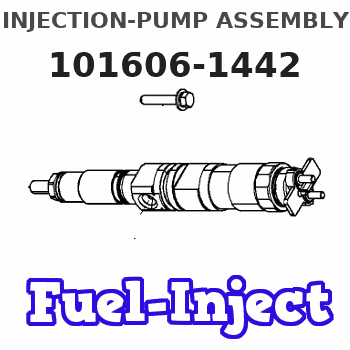
Rating:
Service parts 101606-1442 INJECTION-PUMP ASSEMBLY:
1.
_
7.
COUPLING PLATE
8.
_
9.
_
11.
Nozzle and Holder
12.
Open Pre:MPa(Kqf/cm2)
21.6{220}
15.
NOZZLE SET
Include in #1:
101606-1442
as INJECTION-PUMP ASSEMBLY
Include in #2:
104746-1850
as _
Cross reference number
BOSCH
9 400 615 448
9400615448
ZEXEL
101606-1442
1016061442
MITSUBISHI
ME056655
me056655
Zexel num
Bosch num
Firm num
Name
101606-1442
9 400 615 448
ME056655 MITSUBISHI
INJECTION-PUMP ASSEMBLY
6D22 K 14BF INJECTION PUMP ASSY PE6AD PE
6D22 K 14BF INJECTION PUMP ASSY PE6AD PE
Calibration Data:
Adjustment conditions
Test oil
1404 Test oil ISO4113 or {SAEJ967d}
1404 Test oil ISO4113 or {SAEJ967d}
Test oil temperature
degC
40
40
45
Nozzle and nozzle holder
105780-8140
Bosch type code
EF8511/9A
Nozzle
105780-0000
Bosch type code
DN12SD12T
Nozzle holder
105780-2080
Bosch type code
EF8511/9
Opening pressure
MPa
17.2
Opening pressure
kgf/cm2
175
Injection pipe
Outer diameter - inner diameter - length (mm) mm 6-2-600
Outer diameter - inner diameter - length (mm) mm 6-2-600
Overflow valve
131424-5120
Overflow valve opening pressure
kPa
255
221
289
Overflow valve opening pressure
kgf/cm2
2.6
2.25
2.95
Tester oil delivery pressure
kPa
157
157
157
Tester oil delivery pressure
kgf/cm2
1.6
1.6
1.6
Direction of rotation (viewed from drive side)
Right R
Right R
Injection timing adjustment
Direction of rotation (viewed from drive side)
Right R
Right R
Injection order
1-5-3-6-
2-4
Pre-stroke
mm
4.5
4.45
4.55
Beginning of injection position
Governor side NO.1
Governor side NO.1
Difference between angles 1
Cal 1-5 deg. 60 59.5 60.5
Cal 1-5 deg. 60 59.5 60.5
Difference between angles 2
Cal 1-3 deg. 120 119.5 120.5
Cal 1-3 deg. 120 119.5 120.5
Difference between angles 3
Cal 1-6 deg. 180 179.5 180.5
Cal 1-6 deg. 180 179.5 180.5
Difference between angles 4
Cyl.1-2 deg. 240 239.5 240.5
Cyl.1-2 deg. 240 239.5 240.5
Difference between angles 5
Cal 1-4 deg. 300 299.5 300.5
Cal 1-4 deg. 300 299.5 300.5
Injection quantity adjustment
Adjusting point
-
Rack position
9.6
Pump speed
r/min
700
700
700
Each cylinder's injection qty
mm3/st.
112
108.6
115.4
Basic
*
Fixing the rack
*
Standard for adjustment of the maximum variation between cylinders
*
Injection quantity adjustment_02
Adjusting point
C
Rack position
7.7+-0.5
Pump speed
r/min
225
225
225
Each cylinder's injection qty
mm3/st.
18.5
15.7
21.3
Fixing the rack
*
Standard for adjustment of the maximum variation between cylinders
*
Injection quantity adjustment_03
Adjusting point
A
Rack position
R1(9.6)
Pump speed
r/min
700
700
700
Average injection quantity
mm3/st.
112
111
113
Basic
*
Fixing the lever
*
Injection quantity adjustment_04
Adjusting point
B
Rack position
(R1)
Pump speed
r/min
1100
1100
1100
Average injection quantity
mm3/st.
112
109.5
114.5
Difference in delivery
mm3/st.
9
9
9
Fixing the lever
*
Timer adjustment
Pump speed
r/min
850--
Advance angle
deg.
0
0
0
Remarks
Start
Start
Timer adjustment_02
Pump speed
r/min
800
Advance angle
deg.
0.5
Timer adjustment_03
Pump speed
r/min
1000
Advance angle
deg.
0.9
0.4
1.4
Timer adjustment_04
Pump speed
r/min
1150
Advance angle
deg.
3
2.5
3.5
Timer adjustment_05
Pump speed
r/min
-
Advance angle
deg.
4
4
5
Remarks
Measure the actual speed, stop
Measure the actual speed, stop
Test data Ex:
Governor adjustment
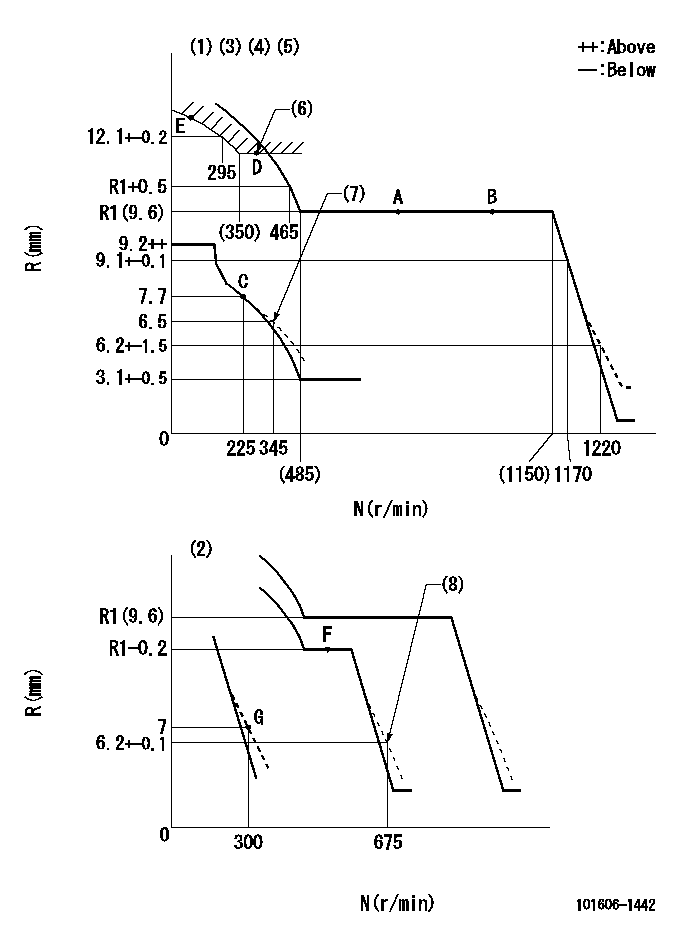
N:Pump speed
R:Rack position (mm)
(1)Adjust with speed control lever at full position (minimum-maximum speed specification)
(2)Adjust with the load control lever in the full position (variable speed specification).
(3)Lever ratio: RT
(4)Target shim dimension: TH
(5)Tolerance for racks not indicated: +-0.05mm.
(6)Excess fuel setting for starting: SXL
(7)Damper spring setting
(8)When air cylinder is operating.
----------
RT=1 TH=2.8mm SXL=11.6+-0.1mm
----------
----------
RT=1 TH=2.8mm SXL=11.6+-0.1mm
----------
Speed control lever angle
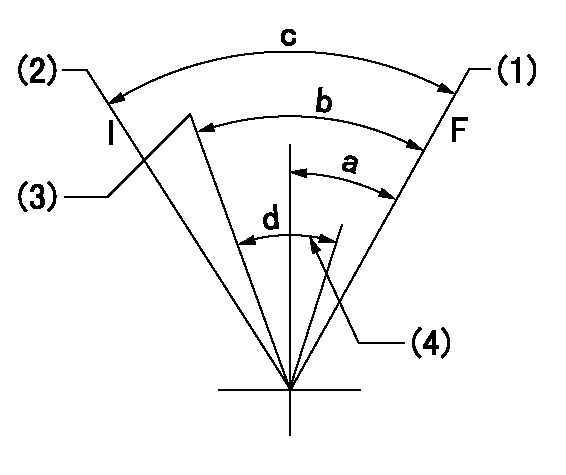
F:Full speed
I:Idle
(1)Pump speed = aa
(2)Pump speed = bb
(3)Pump speed cc
(4)Air cylinder's adjustable range
----------
aa=1170r/min bb=300r/min cc=675r/min
----------
a=4deg+-5deg b=11deg+-5deg c=(15deg)+-5deg b=(10deg)
----------
aa=1170r/min bb=300r/min cc=675r/min
----------
a=4deg+-5deg b=11deg+-5deg c=(15deg)+-5deg b=(10deg)
0000000901

F:Full load
I:Idle
(1)Stopper bolt setting
----------
----------
a=21deg+-5deg b=24.5deg+-3deg
----------
----------
a=21deg+-5deg b=24.5deg+-3deg
Stop lever angle
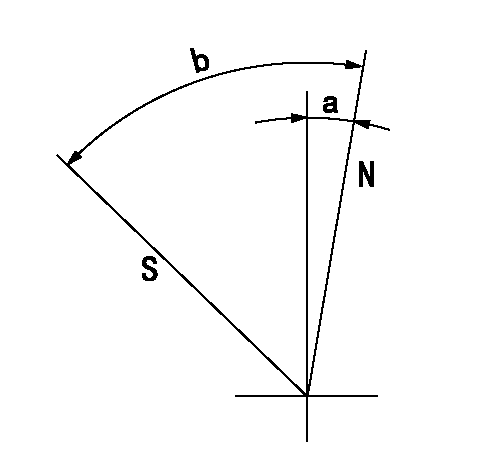
N:Pump normal
S:Stop the pump.
----------
----------
a=12deg+-5deg b=71deg+-5deg
----------
----------
a=12deg+-5deg b=71deg+-5deg
0000001501 MICRO SWITCH
Adjustment of the micro-switch
Adjust the bolt to obtain the following lever position when the micro-switch is ON.
(1)Speed N1
(2)Rack position Ra
----------
N1=325r/min Ra=7+-0.1mm
----------
----------
N1=325r/min Ra=7+-0.1mm
----------
0000001601 2-STAGE CHANGEOVER DEVICE

RFD governor 2 stage changeover mechanism adjustment outline
(A) Bolt
(B) bolt
(c) Nut
(D) Return spring
(E) Bolt
(F) Bolt
(G) Screw
(H) Bolt
(I) Load lever
(J) Speed lever
(K) Air cylinder
(M Air inlet
Figure 1 is only for reference. Lever shape, etc, may vary.
1. Minimum-maximum speed specification adjustment (when running)
(a) Without applying air to the air cylinder, loosen bolts (A) and (B).
(1)High speed return L setting
(a) In the speed range Nf~Nf - 300r/min, adjust using the speed adjusting bolt to determine the temporary beginning of high speed control speed.
(b) Determine the rack position in the vicinity of Rf using the full load lever.
(c) Increase speed and confirm return distance L.
(d) Adjust using the tension lever bolt to obtain L.
(2)Setting full load rack position Rf
(a) Move the load control lever to the full side.
(b) Adjust the full load adjusting bolt so that Rf can be obtained, then fix.
(3)Setting the beginning of high speed operation Nf
(a) Adjust using bolt (E) so that Nf can be obtained, and then fix.
(4)Idle control setting (Re, Ni, Rc)
(a) Set the speed at Ns + 200r/min and move the load control lever to the idle side.
(b) Fix the lever in the position where Re can be obtained.
(c) Next, decrease speed to Ni and screw in the idle spring.
(d) Adjust to obtain rack position Ri.
(e) Increase the speed and after confirming that the rack position is Re at Ns, set the speed at 0.
(f) Confirm protrusion position Rc at idle.
(5)Damper spring adjustment
(a) Increase speed and set the speed at the rack position Rd - 0.1 mm
(b) Set using the damper spring so that the rack position Rd can be obtained.
(c) When Rd is not specified, Rd = Ri - 0.5 mm.
(6)High speed droop confirmation
(a) Return the load control lever to the full load lever position.
(b) Increase the speed and confirm that Rf can be obtained at Nf r/min.
(c) Confirm that speed is Nh at rack position Rh.
2. Variable speed specification adjustment (at operation)
(a) Remove return spring (D).
(b) Apply air pressure of 245~294 kPa {2.5~3 kg/cm2} to the air cylinder.
(c) Perform the following adjustment in this condition.
(1)Setting full load rack position Rf'
(a) Pull the load lever to the idle side.
(b) Obtain rack position Rf' using the nut (C). (Pump speed is Nf'-50 r/min.)
(2)Setting full speed Nf'
(a) Adjust using bolt (B) so that Nf can be obtained, and then fix.
(3)Low speed side setting
(a) At 350r/min, set bolt (F) at beginning of governor operation position, then fix.
3. Bolt (A) adjustment
(1)Install return spring (D) and perform the adjustments below at air pressure 0.
(a) Set at speed Nf using bolt (E).
(b) Screw in bolt (A).
(c) Screw in 1 more turn from the speed lever contact position
(d) Fix bolt (A).
(e) At this time confirm that the air cylinder's shaft moves approximately 1 mm towards the governor.
4. Lever operation confirmation using the air cylinder
(1)Apply 588 kPa {6 kg/cm2} air pressure to the air cylinder.
(2)Confirm that the cylinder piston is moved 50 mm by the spring (D).
----------
----------
----------
----------
Timing setting

(1)Pump vertical direction
(2)Coupling's key groove position at No 1 cylinder's beginning of injection
(3)-
(4)-
----------
----------
a=(7deg)
----------
----------
a=(7deg)
Information:
Caterpillar's Scheduled Oil Sampling (S O S) is the best indicator for determining what is happening inside your engine.S O S is a diagnostic tool designed to identify and measure contamination and condition of oil, oil performance and component wear rates. The program identifies and measures contamination such as soot, sulfur, etc., and the presence of fuel, water and antifreeze in a sample of oil. The tests also determine the amount of wear metals present in the oil sample, which is compared to established Caterpillar norms to determine acceptability.Caterpillar recommends using Scheduled Oil Sampling (S O S), at regularly scheduled intervals, to compliment your preventive maintenance program. To be effective as an indicator, S O S MUST be performed on a continuing basis. Intermittent sampling will NOT allow wear rate trend lines to be established. The Caterpillar Scheduled Oil Sampling Program (S O S), was developed to help Caterpillar users realize the highest possible value from their equipment by minimizing repair costs and maximizing availability. Obtain S O S samples at regularly scheduled intervals to monitor the condition and maintenance requirements of your engine. Consult your Caterpillar dealer for complete information and assistance in establishing an S O S program for your engine(s). Infrared analysis should always be accompanied by wear element analysis and chemical and physical tests to assure accurate diagnosis. Infrared analysis must be used to determine oil change intervals. S O S must include Infrared (IR) in the analysis. S O S Analysis
S O S is composed of three basic tests:* Wear Analysis* Chemical and Physical Tests* Oil Condition Analysis Wear Analysis is performed with an atomic absorption spectrophotometer to monitor component wear rates by identifying and measuring concentrations, in parts per million, of wear elements present in the used oil.Based on known normal concentration data, maximum limits of wear elements are established. Impending failures can be identified when test results deviate from concentration levels established as acceptable, based on normal wear. Through monitoring the used oil, normal component wear trends are determined. Many failures can be identified when wear trends and/or contaminants significantly exceed past trends.Detectable failures are those caused by component wear and gradual contamination from dirt, fuel, water or antifreeze. Wear analysis is not able to predict failures due to component fatigue, sudden loss of lubrication, or sudden ingestion of a large amount of dirt or contaminants since failures of this nature occur too rapidly. Chemical and Physical Tests detect the presence of water, fuel and/or glycol (antifreeze) in the oil and determine whether or not their concentrations exceed established maximum limits. Oil Condition Analysis is evaluated with Infrared Analysis and determines the degree of deterioration of the used oil by measuring the amount of contaminants such as sulfur products, oxidation, nitration products and soot present in the used oil.It also monitors additive depletion and detects ethylene glycol and butyl cellosolve contamination and can assist in customizing (reducing, maintaining or extending) oil change intervals for particular conditions
S O S is composed of three basic tests:* Wear Analysis* Chemical and Physical Tests* Oil Condition Analysis Wear Analysis is performed with an atomic absorption spectrophotometer to monitor component wear rates by identifying and measuring concentrations, in parts per million, of wear elements present in the used oil.Based on known normal concentration data, maximum limits of wear elements are established. Impending failures can be identified when test results deviate from concentration levels established as acceptable, based on normal wear. Through monitoring the used oil, normal component wear trends are determined. Many failures can be identified when wear trends and/or contaminants significantly exceed past trends.Detectable failures are those caused by component wear and gradual contamination from dirt, fuel, water or antifreeze. Wear analysis is not able to predict failures due to component fatigue, sudden loss of lubrication, or sudden ingestion of a large amount of dirt or contaminants since failures of this nature occur too rapidly. Chemical and Physical Tests detect the presence of water, fuel and/or glycol (antifreeze) in the oil and determine whether or not their concentrations exceed established maximum limits. Oil Condition Analysis is evaluated with Infrared Analysis and determines the degree of deterioration of the used oil by measuring the amount of contaminants such as sulfur products, oxidation, nitration products and soot present in the used oil.It also monitors additive depletion and detects ethylene glycol and butyl cellosolve contamination and can assist in customizing (reducing, maintaining or extending) oil change intervals for particular conditions
Have questions with 101606-1442?
Group cross 101606-1442 ZEXEL
Mitsubishi
Mitsubishi
101606-1442
9 400 615 448
ME056655
INJECTION-PUMP ASSEMBLY
6D22
6D22