Information injection-pump assembly
BOSCH
9 400 613 052
9400613052
ZEXEL
101606-0570
1016060570
ISUZU
8976026020
8976026020
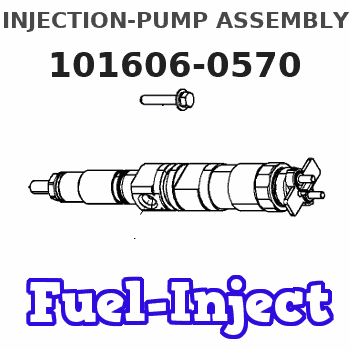
Rating:
Service parts 101606-0570 INJECTION-PUMP ASSEMBLY:
1.
_
7.
COUPLING PLATE
8.
_
9.
_
11.
Nozzle and Holder
8-94391-291-4
12.
Open Pre:MPa(Kqf/cm2)
16.2{165}/19.6{199}
14.
NOZZLE
Include in #1:
101606-0570
as INJECTION-PUMP ASSEMBLY
Include in #2:
104746-6202
as _
Cross reference number
BOSCH
9 400 613 052
9400613052
ZEXEL
101606-0570
1016060570
ISUZU
8976026020
8976026020
Zexel num
Bosch num
Firm num
Name
101606-0570
9 400 613 052
8976026020 ISUZU
INJECTION-PUMP ASSEMBLY
6HL1-S K 14BN INJECTION PUMP ASSY PE
6HL1-S K 14BN INJECTION PUMP ASSY PE
Calibration Data:
Adjustment conditions
Test oil
1404 Test oil ISO4113 or {SAEJ967d}
1404 Test oil ISO4113 or {SAEJ967d}
Test oil temperature
degC
40
40
45
Nozzle and nozzle holder
105780-8310
Nozzle
105780-0120
Bosch type code
1 688 901 990
Nozzle holder
105780-2240
Opening pressure
MPa
18
Opening pressure
kgf/cm2
184
Injection pipe
Outer diameter - inner diameter - length (mm) mm 6-2-600
Outer diameter - inner diameter - length (mm) mm 6-2-600
Overflow valve
131424-8620
Overflow valve opening pressure
kPa
206
172
240
Overflow valve opening pressure
kgf/cm2
2.1
1.75
2.45
Tester oil delivery pressure
kPa
255
255
255
Tester oil delivery pressure
kgf/cm2
2.6
2.6
2.6
Direction of rotation (viewed from drive side)
Left L
Left L
Injection timing adjustment
Direction of rotation (viewed from drive side)
Left L
Left L
Injection order
1-5-3-6-
2-4
Pre-stroke
mm
3.8
3.75
3.85
Rack position
Point A R=A
Point A R=A
Beginning of injection position
Governor side NO.1
Governor side NO.1
Difference between angles 1
Cal 1-5 deg. 60 59.5 60.5
Cal 1-5 deg. 60 59.5 60.5
Difference between angles 2
Cal 1-3 deg. 120 119.5 120.5
Cal 1-3 deg. 120 119.5 120.5
Difference between angles 3
Cal 1-6 deg. 180 179.5 180.5
Cal 1-6 deg. 180 179.5 180.5
Difference between angles 4
Cyl.1-2 deg. 240 239.5 240.5
Cyl.1-2 deg. 240 239.5 240.5
Difference between angles 5
Cal 1-4 deg. 300 299.5 300.5
Cal 1-4 deg. 300 299.5 300.5
Injection quantity adjustment
Adjusting point
-
Rack position
14.2
Pump speed
r/min
850
850
850
Average injection quantity
mm3/st.
65
63.4
66.6
Max. variation between cylinders
%
0
-2.5
2.5
Basic
*
Fixing the rack
*
Standard for adjustment of the maximum variation between cylinders
*
Injection quantity adjustment_02
Adjusting point
Z
Rack position
9.7+-0.5
Pump speed
r/min
295
295
295
Average injection quantity
mm3/st.
13
11.7
14.3
Max. variation between cylinders
%
0
-14
14
Fixing the rack
*
Standard for adjustment of the maximum variation between cylinders
*
Injection quantity adjustment_03
Adjusting point
A
Rack position
R1(14.2)
Pump speed
r/min
850
850
850
Average injection quantity
mm3/st.
65
64
66
Basic
*
Fixing the lever
*
Test data Ex:
Governor adjustment
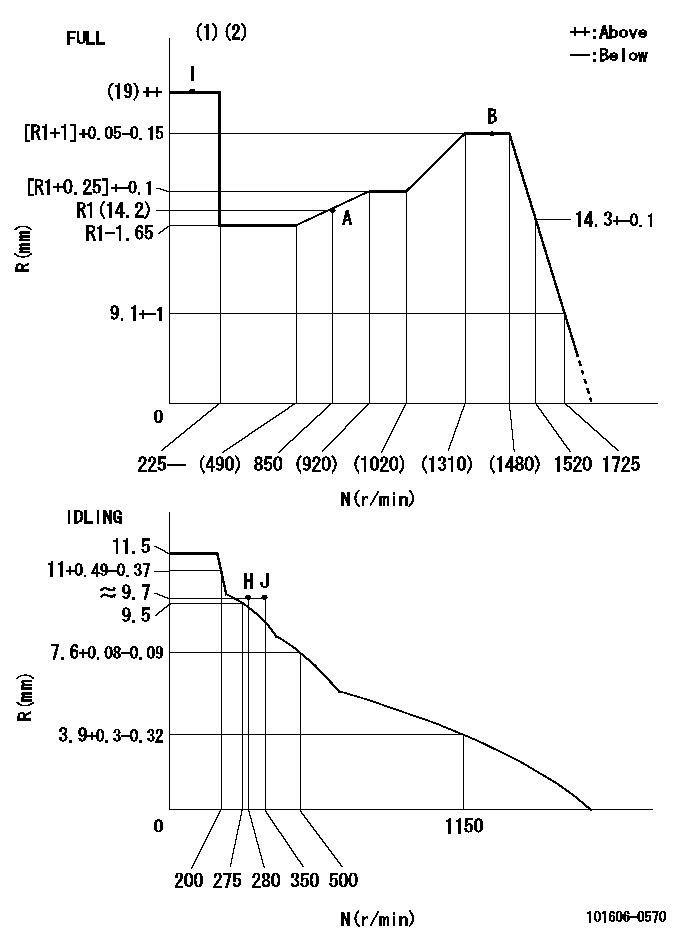
N:Pump speed
R:Rack position (mm)
(1)Torque cam stamping: T1
(2)Tolerance for racks not indicated: +-0.05mm.
----------
T1=P28
----------
----------
T1=P28
----------
Timer adjustment

(1)Adjusting range
(2)Step response time
(N): Speed of the pump
(L): Load
(theta) Advance angle
(Srd1) Step response time 1
(Srd2) Step response time 2
1. Adjusting conditions for the variable timer
(1)Adjust the clearance between the pickup and the protrusion to L.
----------
L=1.5+-0.2mm N2=800r/min C2=(8deg) t1=2--sec. t2=2--sec.
----------
N1=1300++r/min P1=0kPa(0kgf/cm2) P2=392kPa(4kgf/cm2) C1=8+-0.3deg R01=0/4 load R02=4/4 load
----------
L=1.5+-0.2mm N2=800r/min C2=(8deg) t1=2--sec. t2=2--sec.
----------
N1=1300++r/min P1=0kPa(0kgf/cm2) P2=392kPa(4kgf/cm2) C1=8+-0.3deg R01=0/4 load R02=4/4 load
Speed control lever angle
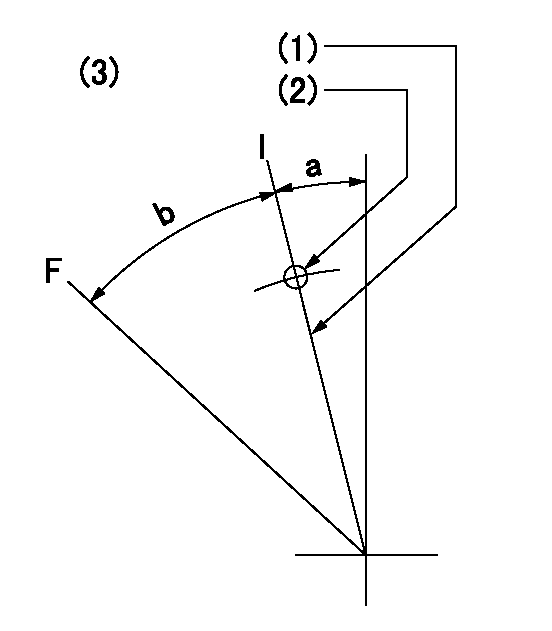
F:Full speed
I:Idle
(1)Stopper bolt setting
(2)Use the pin at R = aa
(3)Viewed from feed pump side.
----------
aa=35mm
----------
a=11deg+-5deg b=40deg+-3deg
----------
aa=35mm
----------
a=11deg+-5deg b=40deg+-3deg
Stop lever angle
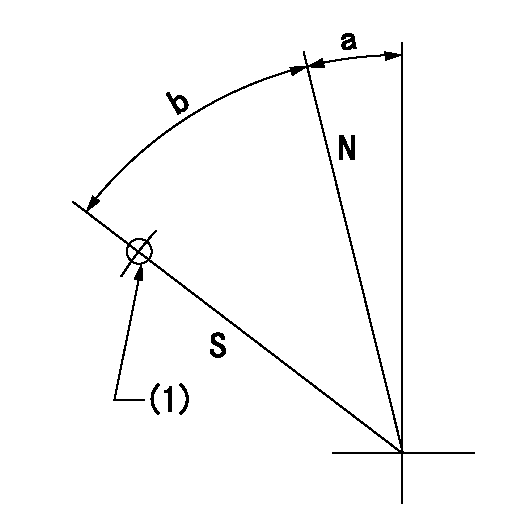
N:Pump normal
S:Stop the pump.
(1)Use the pin at R = aa
----------
aa=45mm
----------
a=12.5deg+-5deg b=40deg+-5deg
----------
aa=45mm
----------
a=12.5deg+-5deg b=40deg+-5deg
0000001501 RACK SENSOR

Rack sensor adjustment
1. Flange type rack sensor (rack sensor adjustment -5*20)
(1)These types of rack sensors do not need adjustment. Confirm the performance with the following procedures.
(2)Mount the rack sensor main body to the pump main body.
(3)Fix the pump lever at full.
(4)At supply voltage V1, pump speed N1 and rack position Ra, confirm that the amp's output voltage is Vist.
(5)Move the pump lever two or three times.
(6)Set again to full.
(7)Confirm that the amplifier output voltage is Vist.
(8)Fix the caution plate to the upper part of the rack sensor.
(For those without the caution plate instructions, make sure the nameplate of the rack sensor carries the "Don't hold here" caution.)
(9)Apply red paint to the rack sensor mounting bolts (2 places).
----------
V1=5+-0.01V N1=850r/min Ra=R1(14.2)mm Vist=3.49+-0.28V
----------
----------
V1=5+-0.01V N1=850r/min Ra=R1(14.2)mm Vist=3.49+-0.28V
----------
Timing setting

(1)Pump vertical direction
(2)Positions of coupling's threaded installation holes at No 1 cylinder's beginning of injection
(3)B.T.D.C.: aa
(4)-
----------
aa=6deg
----------
a=(160deg)
----------
aa=6deg
----------
a=(160deg)
Information:
Crankcase Breather
Clean
This maintenance is to be performed every other oil change or 600 hours. 1. Loosen hose clamp (1) and remove the hose from the cover.2. Loosen three breather cover bolts (2) and remove cover (3). 3. Remove breather element (4), and wash in clean, nonflammable solvent and allow to dry. 4. Install clean, dry breather element (4).5. Install cover (3) and bolts (2).5. Install hose and clamp (1). Tighten clamp (1) to 27 4.5 lb in (3.0 0.5 N m). Refer to topic Torque Specifications for the proper torque of hose clamp-worm drive band type. If the crankcase breather is not maintained on a regular basis, it will become plugged. A plugged crankcase breather would result in excessive crankcase pressure that may cause crankshaft seal leakage.Refer to the Torque Specifications section of this manual for Torque for Standard Hose Clamps-Worm Drive Band Type hose clamps if your engine is equipped.Alternator, Fan and Accessory Drive Belts
Inspect/Replace
Inspect the condition and adjustment of alternator belts and fan drive belts.Inspect all drive belts for wear and replace if they show any signs of wear.If one belt in a set requires replacement, always install a new matched set of belts. Never replace just the worn belt. If only the worn belt is replaced, the new belt will carry all the load, as it will not be stretched as much as the older belts. All the belts will fail in rapid succession.Belt Adjustment
If belts are too loose, they vibrate enough to cause unnecessary wear on the belts and pulleys.If belts are too tight, unnecessary stresses are placed upon the pulley bearings and belts which might shorten the life of both.The engine is equipped with an automatic belt tensioner, adjustments should not be necessary.To check the belt tension if NOT equipped with an automatic belt tensioner, refer to the vehicle manufacturer's recommendations. Correctly adjusted belts will deflect approximately 3/8 to 5/8 inch (9 to 15 mm).Hoses and Clamps
Inspect
* Inspect all hoses for leaks due to cracking, softness and loose clamps.* Replace hoses that are cracked or soft and tighten loose clamps.Before Replacing Hoses
1. After engine is cool, loosen the radiator filler cap slowly to relieve any pressure and remove the cap.2. Drain the coolant from the cooling system to a level below the hose being replaced.3. Remove the hose clamps, disconnect the old hose and replace with a new hose.4. Install hose clamps. (See the Torque for Standard Hose Clamps-Worm Band Type chart in the Torque Specifications section of this publication for the appropriate torque value.) For constant torque hose clamps, also refer to the Torque Specifications section in this publication.After Replacing Hoses
Refer to Cooling System Specifications in this publication and/or consult your Caterpillar dealer for more detailed specifications.5. Add coolant water mixture to the cooling system. Fill to the proper level by mixing a solution of acceptable water and Caterpillar Antifreeze. Test for supplemental additive (Conditioner) concentration. Add proper amount, or if equipped with a coolant additive element, install the appropriate
Clean
This maintenance is to be performed every other oil change or 600 hours. 1. Loosen hose clamp (1) and remove the hose from the cover.2. Loosen three breather cover bolts (2) and remove cover (3). 3. Remove breather element (4), and wash in clean, nonflammable solvent and allow to dry. 4. Install clean, dry breather element (4).5. Install cover (3) and bolts (2).5. Install hose and clamp (1). Tighten clamp (1) to 27 4.5 lb in (3.0 0.5 N m). Refer to topic Torque Specifications for the proper torque of hose clamp-worm drive band type. If the crankcase breather is not maintained on a regular basis, it will become plugged. A plugged crankcase breather would result in excessive crankcase pressure that may cause crankshaft seal leakage.Refer to the Torque Specifications section of this manual for Torque for Standard Hose Clamps-Worm Drive Band Type hose clamps if your engine is equipped.Alternator, Fan and Accessory Drive Belts
Inspect/Replace
Inspect the condition and adjustment of alternator belts and fan drive belts.Inspect all drive belts for wear and replace if they show any signs of wear.If one belt in a set requires replacement, always install a new matched set of belts. Never replace just the worn belt. If only the worn belt is replaced, the new belt will carry all the load, as it will not be stretched as much as the older belts. All the belts will fail in rapid succession.Belt Adjustment
If belts are too loose, they vibrate enough to cause unnecessary wear on the belts and pulleys.If belts are too tight, unnecessary stresses are placed upon the pulley bearings and belts which might shorten the life of both.The engine is equipped with an automatic belt tensioner, adjustments should not be necessary.To check the belt tension if NOT equipped with an automatic belt tensioner, refer to the vehicle manufacturer's recommendations. Correctly adjusted belts will deflect approximately 3/8 to 5/8 inch (9 to 15 mm).Hoses and Clamps
Inspect
* Inspect all hoses for leaks due to cracking, softness and loose clamps.* Replace hoses that are cracked or soft and tighten loose clamps.Before Replacing Hoses
1. After engine is cool, loosen the radiator filler cap slowly to relieve any pressure and remove the cap.2. Drain the coolant from the cooling system to a level below the hose being replaced.3. Remove the hose clamps, disconnect the old hose and replace with a new hose.4. Install hose clamps. (See the Torque for Standard Hose Clamps-Worm Band Type chart in the Torque Specifications section of this publication for the appropriate torque value.) For constant torque hose clamps, also refer to the Torque Specifications section in this publication.After Replacing Hoses
Refer to Cooling System Specifications in this publication and/or consult your Caterpillar dealer for more detailed specifications.5. Add coolant water mixture to the cooling system. Fill to the proper level by mixing a solution of acceptable water and Caterpillar Antifreeze. Test for supplemental additive (Conditioner) concentration. Add proper amount, or if equipped with a coolant additive element, install the appropriate
Have questions with 101606-0570?
Group cross 101606-0570 ZEXEL
Isuzu
101606-0570
9 400 613 052
8976026020
INJECTION-PUMP ASSEMBLY
6HL1-S
6HL1-S