Information injection-pump assembly
BOSCH
9 400 613 370
9400613370
ZEXEL
101606-0541
1016060541
ISUZU
8976023531
8976023531
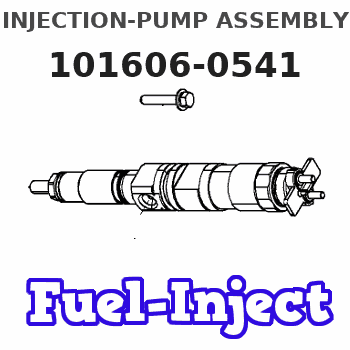
Rating:
Service parts 101606-0541 INJECTION-PUMP ASSEMBLY:
1.
_
7.
COUPLING PLATE
8.
_
9.
_
11.
Nozzle and Holder
8-94391-291-4
12.
Open Pre:MPa(Kqf/cm2)
16.2{165}/19.6{200}
14.
NOZZLE
Include in #1:
101606-0541
as INJECTION-PUMP ASSEMBLY
Include in #2:
104746-1990
as _
Cross reference number
BOSCH
9 400 613 370
9400613370
ZEXEL
101606-0541
1016060541
ISUZU
8976023531
8976023531
Zexel num
Bosch num
Firm num
Name
101606-0541
9 400 613 370
8976023531 ISUZU
INJECTION-PUMP ASSEMBLY
6HL1-S K 14BN INJECTION PUMP ASSY PE
6HL1-S K 14BN INJECTION PUMP ASSY PE
Calibration Data:
Adjustment conditions
Test oil
1404 Test oil ISO4113 or {SAEJ967d}
1404 Test oil ISO4113 or {SAEJ967d}
Test oil temperature
degC
40
40
45
Nozzle and nozzle holder
105780-8260
Bosch type code
9 430 610 133
Nozzle
105780-0120
Bosch type code
1 688 901 990
Nozzle holder
105780-2190
Opening pressure
MPa
18
Opening pressure
kgf/cm2
184
Injection pipe
Outer diameter - inner diameter - length (mm) mm 6-2-600
Outer diameter - inner diameter - length (mm) mm 6-2-600
Overflow valve
131424-8620
Overflow valve opening pressure
kPa
206
172
240
Overflow valve opening pressure
kgf/cm2
2.1
1.75
2.45
Tester oil delivery pressure
kPa
255
255
255
Tester oil delivery pressure
kgf/cm2
2.6
2.6
2.6
Direction of rotation (viewed from drive side)
Left L
Left L
Injection timing adjustment
Direction of rotation (viewed from drive side)
Left L
Left L
Injection order
1-5-3-6-
2-4
Pre-stroke
mm
3.8
3.75
3.85
Rack position
Point A R=A
Point A R=A
Beginning of injection position
Governor side NO.1
Governor side NO.1
Difference between angles 1
Cal 1-5 deg. 60 59.5 60.5
Cal 1-5 deg. 60 59.5 60.5
Difference between angles 2
Cal 1-3 deg. 120 119.5 120.5
Cal 1-3 deg. 120 119.5 120.5
Difference between angles 3
Cal 1-6 deg. 180 179.5 180.5
Cal 1-6 deg. 180 179.5 180.5
Difference between angles 4
Cyl.1-2 deg. 240 239.5 240.5
Cyl.1-2 deg. 240 239.5 240.5
Difference between angles 5
Cal 1-4 deg. 300 299.5 300.5
Cal 1-4 deg. 300 299.5 300.5
Injection quantity adjustment
Adjusting point
-
Rack position
14.1
Pump speed
r/min
850
850
850
Average injection quantity
mm3/st.
128.5
126.9
130.1
Max. variation between cylinders
%
0
-2.5
2.5
Basic
*
Fixing the rack
*
Standard for adjustment of the maximum variation between cylinders
*
Injection quantity adjustment_02
Adjusting point
Z
Rack position
9.5+-0.5
Pump speed
r/min
300
300
300
Average injection quantity
mm3/st.
15.5
14.2
16.8
Max. variation between cylinders
%
0
-14
14
Fixing the rack
*
Standard for adjustment of the maximum variation between cylinders
*
Injection quantity adjustment_03
Adjusting point
A
Rack position
R1(14.1)
Pump speed
r/min
850
850
850
Average injection quantity
mm3/st.
128.5
127.5
129.5
Basic
*
Fixing the lever
*
Test data Ex:
Governor adjustment
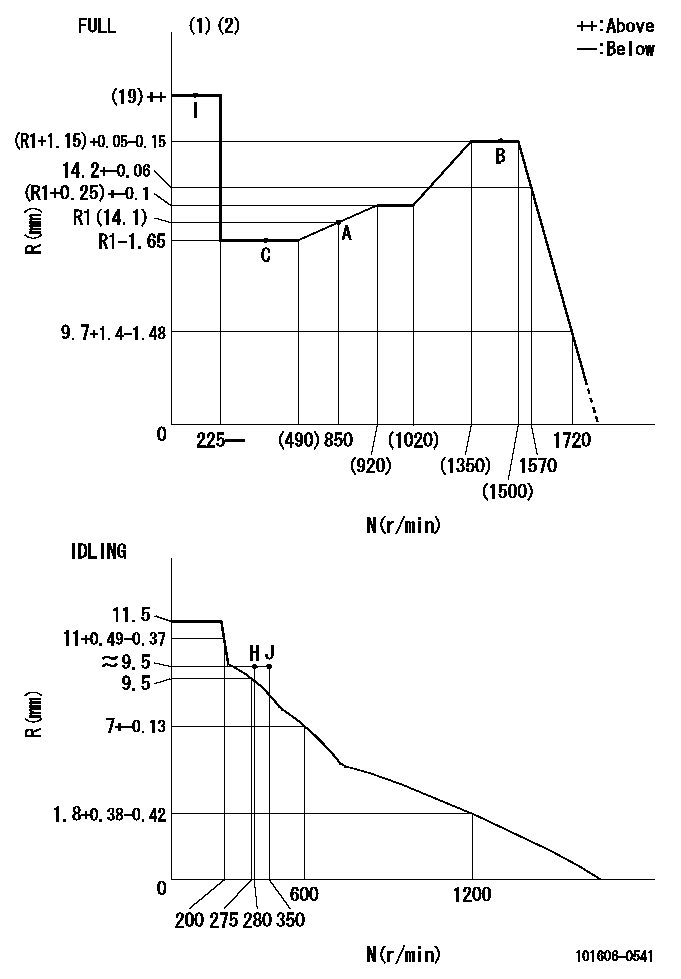
N:Pump speed
R:Rack position (mm)
(1)Torque cam stamping: T1
(2)Tolerance for racks not indicated: +-0.05mm.
----------
T1=N97
----------
----------
T1=N97
----------
Timer adjustment

(1)Adjusting range
(2)Step response time
(N): Speed of the pump
(L): Load
(theta) Advance angle
(Srd1) Step response time 1
(Srd2) Step response time 2
1. Adjusting conditions for the variable timer
(1)Adjust the clearance between the pickup and the protrusion to L.
----------
L=1.5+-0.2mm N2=800r/min C2=(8)deg t1=2--sec. t2=2--sec.
----------
N1=1300++r/min P1=0kPa(0kgf/cm2) P2=392kPa(4kgf/cm2) C1=8+-0.3deg R01=0/4load R02=4/4load
----------
L=1.5+-0.2mm N2=800r/min C2=(8)deg t1=2--sec. t2=2--sec.
----------
N1=1300++r/min P1=0kPa(0kgf/cm2) P2=392kPa(4kgf/cm2) C1=8+-0.3deg R01=0/4load R02=4/4load
Speed control lever angle
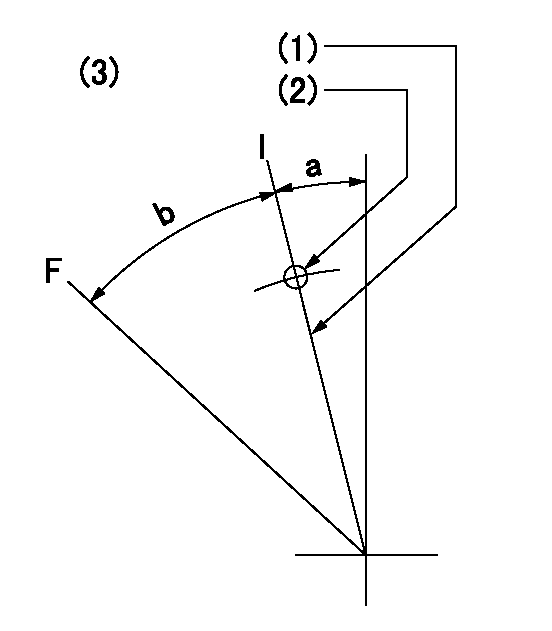
F:Full speed
I:Idle
(1)Stopper bolt set position 'H'
(2)Use the pin at R = aa
(3)Viewed from feed pump side.
----------
aa=33mm
----------
a=12deg+-5deg b=47.5deg+-3deg
----------
aa=33mm
----------
a=12deg+-5deg b=47.5deg+-3deg
Stop lever angle
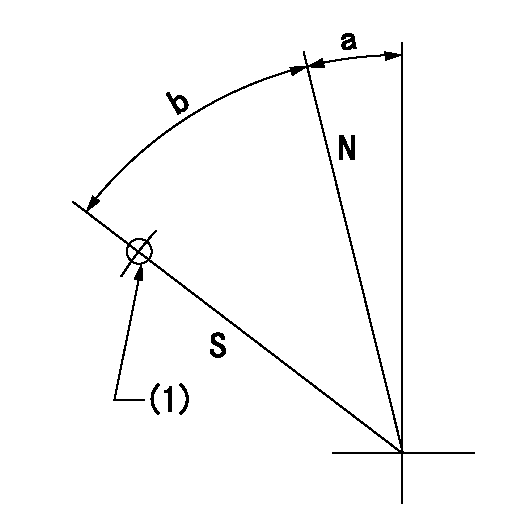
N:Pump normal
S:Stop the pump.
(1)Use the pin at R = aa
----------
aa=45mm
----------
a=12.5deg+-5deg b=40deg+-5deg
----------
aa=45mm
----------
a=12.5deg+-5deg b=40deg+-5deg
0000001501 RACK SENSOR

Rack sensor adjustment
1. Flange type rack sensor (rack sensor adjustment -5*20)
(1)These types of rack sensors do not need adjustment. Confirm the performance with the following procedures.
(2)Mount the rack sensor main body to the pump main body.
(3)Fix the pump lever at full.
(4)At supply voltage V1, pump speed N1 and rack position Ra, confirm that the amp's output voltage is Vist.
(5)Move the pump lever two or three times.
(6)Set again to full.
(7)Confirm that the amplifier output voltage is Vist.
(8)Fix the caution plate to the upper part of the rack sensor.
(For those without the caution plate instructions, make sure the nameplate of the rack sensor carries the "Don't hold here" caution.)
(9)Apply red paint to the rack sensor mounting bolts (2 places).
----------
V1=5+-0.01V N1=850r/min Ra=R1(14.1)mm Vist=3.55+-0.28V
----------
----------
V1=5+-0.01V N1=850r/min Ra=R1(14.1)mm Vist=3.55+-0.28V
----------
Timing setting

(1)Pump vertical direction
(2)Positions of coupling's threaded installation holes at No 1 cylinder's beginning of injection
(3)B.T.D.C.: aa
(4)-
----------
aa=6deg
----------
a=(160deg)
----------
aa=6deg
----------
a=(160deg)
Information:
You must read and understand the warnings and instructions contained in the Safety section of this manual before performing any operation or maintenance procedures.Walk-Around Inspection
Inspect Engine for Leaks and Loose Connections
For maximum service life of your truck engine, make a thorough under the hood inspection before starting the engine. Look for such items as oil or coolant leaks, loose bolts, worn fan belts, loose connections and trash build-up. Remove trash build-up and have repairs made as needed.Check the fluid levels more frequently than the recommended maintenance intervals and continue to monitor fluid levels until any leak is found and fixed.* Wipe all fittings, caps and plugs before performing maintenance to reduce the chance of system contamination. Inspect:* Radiator and ATAAC core for leaks and trash build-up.* Radiator and ATAAC air intake system hoses and elbows for cracks and loose clamps.* Fan and accessory drive belts for cracks, breaks or other damage.Belts for multiple groove pulleys must be replaced as matched sets. If only one belt of a two or three belt set is replaced, it will carry more of a load than the belts not replaced since the older belts are stretched. The additional load on the new belt could cause it to break. Inspect:* Water pump for coolant leaks. The water pump seal is lubricated by coolant in the cooling system. It is normal for a small amount of leakage to occur as the engine cools down and parts contract. If leaks are found, check the coolant level frequently and continue to monitor the level until the water pump is repaired. Excessive coolant leakage may indicate the need to replace the water pump seal.For removal and installation of water pumps and/or seals, see the Service Manual for this engine or consult your Caterpillar dealer. Inspect:* Lube system for leaks, such as front and rear crankshaft seals, oil pan, oil filters and valve covers.* Fuel system for leaks, loose fuel line clamps and fittings and loose or worn hoses.
Fuel line clamps should not be over torqued. Over torqueing causes the clamps to butterfly, which results in low clamping force and fuel line vibration and eventual failure.
Tighten fuel line clamps as required using 6V4980 Torque Screwdriver Tool Group. The standard torque for these fasteners (#10 screw) is 20 lb inch (2.26 N m).* Inspect wiring and wiring harnesses for loose connections and worn or frayed wires. Inspect:* Air intake system hoses and elbows for cracks and loose clamps. * ECM to cylinder head ground strap and starter negative cable for good connection and condition.All guards must be in place. Repair or replace missing or damaged guards.Check condition of batteries and the level of electrolyte, unless equipped with a maintenance free battery.Refer to OEM truck owner manual or manufacturers' recommendations for battery maintenance.
Inspect Engine for Leaks and Loose Connections
For maximum service life of your truck engine, make a thorough under the hood inspection before starting the engine. Look for such items as oil or coolant leaks, loose bolts, worn fan belts, loose connections and trash build-up. Remove trash build-up and have repairs made as needed.Check the fluid levels more frequently than the recommended maintenance intervals and continue to monitor fluid levels until any leak is found and fixed.* Wipe all fittings, caps and plugs before performing maintenance to reduce the chance of system contamination. Inspect:* Radiator and ATAAC core for leaks and trash build-up.* Radiator and ATAAC air intake system hoses and elbows for cracks and loose clamps.* Fan and accessory drive belts for cracks, breaks or other damage.Belts for multiple groove pulleys must be replaced as matched sets. If only one belt of a two or three belt set is replaced, it will carry more of a load than the belts not replaced since the older belts are stretched. The additional load on the new belt could cause it to break. Inspect:* Water pump for coolant leaks. The water pump seal is lubricated by coolant in the cooling system. It is normal for a small amount of leakage to occur as the engine cools down and parts contract. If leaks are found, check the coolant level frequently and continue to monitor the level until the water pump is repaired. Excessive coolant leakage may indicate the need to replace the water pump seal.For removal and installation of water pumps and/or seals, see the Service Manual for this engine or consult your Caterpillar dealer. Inspect:* Lube system for leaks, such as front and rear crankshaft seals, oil pan, oil filters and valve covers.* Fuel system for leaks, loose fuel line clamps and fittings and loose or worn hoses.
Fuel line clamps should not be over torqued. Over torqueing causes the clamps to butterfly, which results in low clamping force and fuel line vibration and eventual failure.
Tighten fuel line clamps as required using 6V4980 Torque Screwdriver Tool Group. The standard torque for these fasteners (#10 screw) is 20 lb inch (2.26 N m).* Inspect wiring and wiring harnesses for loose connections and worn or frayed wires. Inspect:* Air intake system hoses and elbows for cracks and loose clamps. * ECM to cylinder head ground strap and starter negative cable for good connection and condition.All guards must be in place. Repair or replace missing or damaged guards.Check condition of batteries and the level of electrolyte, unless equipped with a maintenance free battery.Refer to OEM truck owner manual or manufacturers' recommendations for battery maintenance.
Have questions with 101606-0541?
Group cross 101606-0541 ZEXEL
Isuzu
101606-0541
9 400 613 370
8976023531
INJECTION-PUMP ASSEMBLY
6HL1-S
6HL1-S