Information injection-pump assembly
BOSCH
9 400 612 751
9400612751
ZEXEL
101606-0461
1016060461
ISUZU
8976021451
8976021451
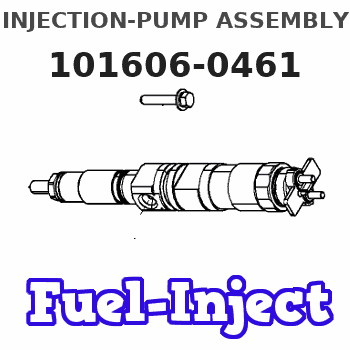
Rating:
Service parts 101606-0461 INJECTION-PUMP ASSEMBLY:
1.
_
7.
COUPLING PLATE
8.
_
9.
_
11.
Nozzle and Holder
8-94391-291-4
12.
Open Pre:MPa(Kqf/cm2)
16.2{165}/19.6{200}
14.
NOZZLE
Include in #1:
101606-0461
as INJECTION-PUMP ASSEMBLY
Include in #2:
104136-1000
as _
Cross reference number
BOSCH
9 400 612 751
9400612751
ZEXEL
101606-0461
1016060461
ISUZU
8976021451
8976021451
Zexel num
Bosch num
Firm num
Name
9 400 612 751
8976021451 ISUZU
INJECTION-PUMP ASSEMBLY
6HL1-S K 14BN INJECTION PUMP ASSY PE
6HL1-S K 14BN INJECTION PUMP ASSY PE
Calibration Data:
Adjustment conditions
Test oil
1404 Test oil ISO4113 or {SAEJ967d}
1404 Test oil ISO4113 or {SAEJ967d}
Test oil temperature
degC
40
40
45
Nozzle and nozzle holder
105780-8310
Nozzle
105780-0120
Bosch type code
1 688 901 990
Nozzle holder
105780-2240
Opening pressure
MPa
18
Opening pressure
kgf/cm2
184
Injection pipe
Outer diameter - inner diameter - length (mm) mm 6-2-600
Outer diameter - inner diameter - length (mm) mm 6-2-600
Overflow valve
131424-8620
Overflow valve opening pressure
kPa
206
206
206
Overflow valve opening pressure
kgf/cm2
2.1
2.1
2.1
Tester oil delivery pressure
kPa
255
255
255
Tester oil delivery pressure
kgf/cm2
2.6
2.6
2.6
Direction of rotation (viewed from drive side)
Left L
Left L
Injection timing adjustment
Direction of rotation (viewed from drive side)
Left L
Left L
Injection order
1-5-3-6-
2-4
Pre-stroke
mm
3.8
3.75
3.85
Rack position
Point A R=A
Point A R=A
Beginning of injection position
Governor side NO.1
Governor side NO.1
Difference between angles 1
Cal 1-5 deg. 60 59.5 60.5
Cal 1-5 deg. 60 59.5 60.5
Difference between angles 2
Cal 1-3 deg. 120 119.5 120.5
Cal 1-3 deg. 120 119.5 120.5
Difference between angles 3
Cal 1-6 deg. 180 179.5 180.5
Cal 1-6 deg. 180 179.5 180.5
Difference between angles 4
Cyl.1-2 deg. 240 239.5 240.5
Cyl.1-2 deg. 240 239.5 240.5
Difference between angles 5
Cal 1-4 deg. 300 299.5 300.5
Cal 1-4 deg. 300 299.5 300.5
Injection quantity adjustment
Adjusting point
-
Rack position
14.2
Pump speed
r/min
850
850
850
Average injection quantity
mm3/st.
65
63.4
66.6
Max. variation between cylinders
%
0
-2.5
2.5
Basic
*
Fixing the rack
*
Standard for adjustment of the maximum variation between cylinders
*
Injection quantity adjustment_02
Adjusting point
Z
Rack position
9.7+-0.5
Pump speed
r/min
295
295
295
Average injection quantity
mm3/st.
13
11.7
14.3
Max. variation between cylinders
%
0
-14
14
Fixing the rack
*
Standard for adjustment of the maximum variation between cylinders
*
Injection quantity adjustment_03
Adjusting point
A
Rack position
R1(14.2)
Pump speed
r/min
850
850
850
Average injection quantity
mm3/st.
65
64
66
Basic
*
Fixing the lever
*
Test data Ex:
Governor adjustment
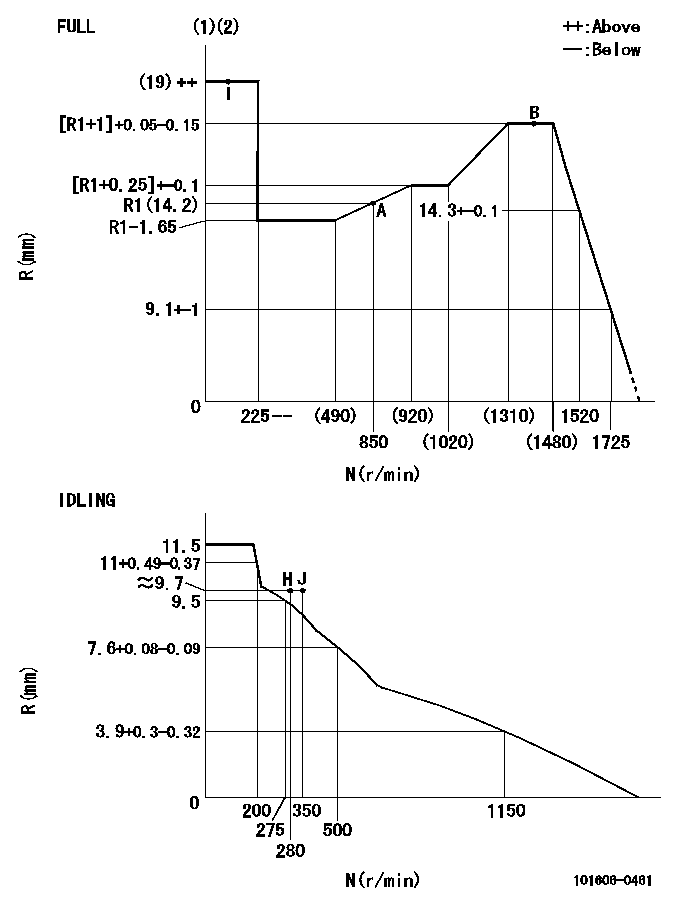
N:Pump speed
R:Rack position (mm)
(1)Torque cam stamping: T1
(2)Tolerance for racks not indicated: +-0.05mm.
----------
T1=P28
----------
----------
T1=P28
----------
Timer adjustment

(1)Adjusting range
(2)Step response time
(N): Speed of the pump
(L): Load
(theta) Advance angle
(Srd1) Step response time 1
(Srd2) Step response time 2
1. Adjusting conditions for the variable timer
(1)Adjust the clearance between the pickup and the protrusion to L.
----------
L=1.5+-0.2mm N2=800r/min C2=(8)deg t1=2--sec. t2=2--sec.
----------
N1=1300++r/min P1=0kPa(0kgf/cm2) P2=392kPa(4kgf/cm2) C1=8+-0.3deg R01=0/4load R02=4/4load
----------
L=1.5+-0.2mm N2=800r/min C2=(8)deg t1=2--sec. t2=2--sec.
----------
N1=1300++r/min P1=0kPa(0kgf/cm2) P2=392kPa(4kgf/cm2) C1=8+-0.3deg R01=0/4load R02=4/4load
Speed control lever angle
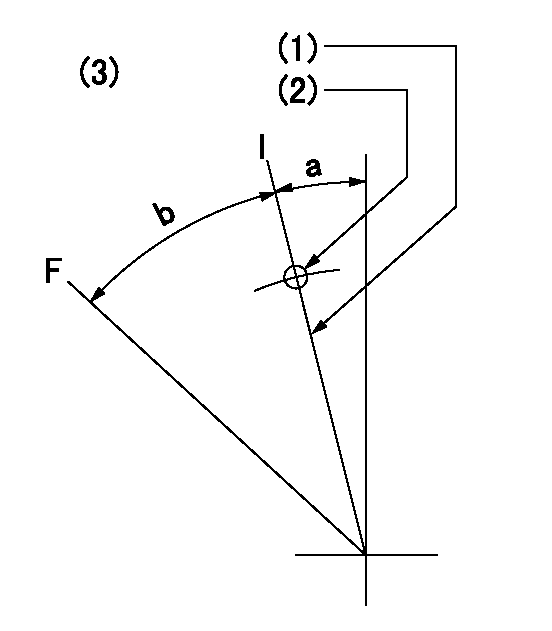
F:Full speed
I:Idle
(1)Stopper bolt setting
(2)Use the pin at R = aa
(3)Viewed from feed pump side.
----------
aa=35mm
----------
a=11deg+-5deg b=40deg+-3deg
----------
aa=35mm
----------
a=11deg+-5deg b=40deg+-3deg
Stop lever angle
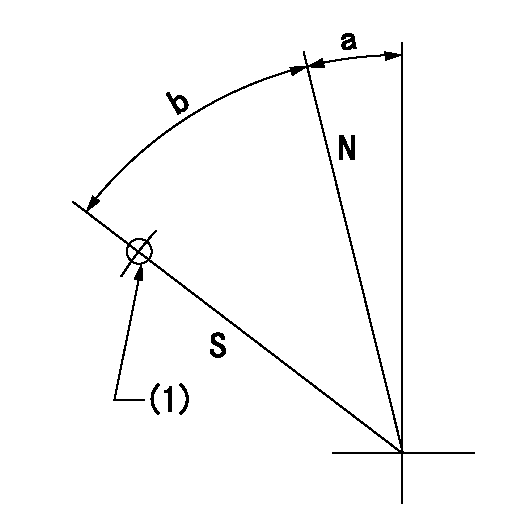
N:Pump normal
S:Stop the pump.
(1)Use the pin at R = aa
----------
aa=45mm
----------
a=12.5deg+-5deg b=40deg+-5deg
----------
aa=45mm
----------
a=12.5deg+-5deg b=40deg+-5deg
0000001501 RACK SENSOR

Rack sensor adjustment
1. Flange type rack sensor (rack sensor adjustment -5*20)
(1)These types of rack sensors do not need adjustment. Confirm the performance with the following procedures.
(2)Mount the rack sensor main body to the pump main body.
(3)Fix the pump lever at full.
(4)At supply voltage V1, pump speed N1 and rack position Ra, confirm that the amp's output voltage is Vist.
(5)Move the pump lever two or three times.
(6)Set again to full.
(7)Confirm that the amplifier output voltage is Vist.
(8)Fix the caution plate to the upper part of the rack sensor.
(For those without the caution plate instructions, make sure the nameplate of the rack sensor carries the "Don't hold here" caution.)
(9)Apply red paint to the rack sensor mounting bolts (2 places).
----------
V1=5+-0.01V N1=850r/min Ra=R1(14.2)mm Vist=3.49+-0.28V
----------
----------
V1=5+-0.01V N1=850r/min Ra=R1(14.2)mm Vist=3.49+-0.28V
----------
Timing setting

(1)Pump vertical direction
(2)Positions of coupling's threaded installation holes at No 1 cylinder's beginning of injection
(3)B.T.D.C.: aa
(4)-
----------
aa=6deg
----------
a=(160deg)
----------
aa=6deg
----------
a=(160deg)
Information:
Coolant Water
The minerals (calcium and magnesium) in hard water can combine with cooling system conditioner additives (silicates and phosphates) to drop out of solution and collect inside the radiator.The minerals (silicates, phosphates, calcium and magnesium) can also accumulate onto hot engine surfaces and reduce the effectiveness of the cooling system, especially after a number of heating and cooling cycles.Distilled water is recommended because of less mineral drop out (potential or severity) than hard or tap water. Tap water, artificially softened with salt, is not recommended for use in your engine's cooling system. Use water that meets the minimum acceptable water requirement to prevent drop-out of these chemical compounds.To determine your water characteristics, contact the local water department, agricultural agent or an independent laboratory to perform the testing service.Antifreeze
Caterpillar recommends that the coolant mix contain a minimum of 30% Caterpillar Antifreeze, or equivalent and acceptable water to maintain an adequate cavitation temperature for efficient water pump performance.Premix coolant solution to provide protection to the lowest expected outside (ambient) temperature. Pure undiluted antifreeze will freeze at -10°F (-23°C).Only use a greater concentration (above 30%) of Caterpillar Antifreeze as needed for anticipated outside (ambient) temperatures. Do not exceed a coolant mixture of 60% antifreeze to water since a concentration above 60% antifreeze will reduce the engine's freeze protection and increase the possibility of deposit formation in the cooling system.
Use Caterpillar Antifreeze or ASTM D4985-89 (GM Specification 6038-M) Antifreeze. Caterpillar Antifreeze is available through your Caterpillar dealer in quantities that follow. Most commercial antifreezes are formulated for gasoline engine applications and will, therefore, have high silicate content. Caterpillar Antifreeze is formulated with a low silicate content and the proper coolant additives for heavy duty diesel engines. Caterpillar does not recommend use of high silicate antifreeze in the 3176 engine.ASTM D4985-89 (GM Specification 6038-M) is a low silicate antifreeze, but supplemental coolant additive must be added. Make proper antifreeze additions.Adding pure antifreeze as a makeup solution for cooling system top-off is an unacceptable practice. It increases the concentration of antifreeze in the cooling system which increases the concentration of dissolved solids and undissolved chemical inhibitors in the cooling system. Add antifreeze mixed with acceptable water to the same freeze protection as your cooling system. Use the chart below to assist in determining the concentration of antifreeze to use. Check the coolant solution frequently in cold weather for glycol concentration with the 5P0957 or 5P3514 Coolant Tester to ensure adequate protection. Both testers are identical except temperature scale. They give immediate, accurate readings and can be used for antifreeze/coolants that contain ethylene or propylene glycol. Both are available at your Caterpillar dealer.If propylene glycol based antifreeze is used, DO NOT allow concentration greater than a 50/50 antifreeze to water mixture. The measurement of freeze protection must be made with a refractive-type tester (5P0957 or 5P3514) rather than a hydrometer-type, which can be used to test ethylene glycol based antifreeze.Supplemental Coolant Additive (Conditioner)
Supplemental coolant additive (conditioner) is necessary to prevent rust, scale, pitting and/or corrosion
The minerals (calcium and magnesium) in hard water can combine with cooling system conditioner additives (silicates and phosphates) to drop out of solution and collect inside the radiator.The minerals (silicates, phosphates, calcium and magnesium) can also accumulate onto hot engine surfaces and reduce the effectiveness of the cooling system, especially after a number of heating and cooling cycles.Distilled water is recommended because of less mineral drop out (potential or severity) than hard or tap water. Tap water, artificially softened with salt, is not recommended for use in your engine's cooling system. Use water that meets the minimum acceptable water requirement to prevent drop-out of these chemical compounds.To determine your water characteristics, contact the local water department, agricultural agent or an independent laboratory to perform the testing service.Antifreeze
Caterpillar recommends that the coolant mix contain a minimum of 30% Caterpillar Antifreeze, or equivalent and acceptable water to maintain an adequate cavitation temperature for efficient water pump performance.Premix coolant solution to provide protection to the lowest expected outside (ambient) temperature. Pure undiluted antifreeze will freeze at -10°F (-23°C).Only use a greater concentration (above 30%) of Caterpillar Antifreeze as needed for anticipated outside (ambient) temperatures. Do not exceed a coolant mixture of 60% antifreeze to water since a concentration above 60% antifreeze will reduce the engine's freeze protection and increase the possibility of deposit formation in the cooling system.
Use Caterpillar Antifreeze or ASTM D4985-89 (GM Specification 6038-M) Antifreeze. Caterpillar Antifreeze is available through your Caterpillar dealer in quantities that follow. Most commercial antifreezes are formulated for gasoline engine applications and will, therefore, have high silicate content. Caterpillar Antifreeze is formulated with a low silicate content and the proper coolant additives for heavy duty diesel engines. Caterpillar does not recommend use of high silicate antifreeze in the 3176 engine.ASTM D4985-89 (GM Specification 6038-M) is a low silicate antifreeze, but supplemental coolant additive must be added. Make proper antifreeze additions.Adding pure antifreeze as a makeup solution for cooling system top-off is an unacceptable practice. It increases the concentration of antifreeze in the cooling system which increases the concentration of dissolved solids and undissolved chemical inhibitors in the cooling system. Add antifreeze mixed with acceptable water to the same freeze protection as your cooling system. Use the chart below to assist in determining the concentration of antifreeze to use. Check the coolant solution frequently in cold weather for glycol concentration with the 5P0957 or 5P3514 Coolant Tester to ensure adequate protection. Both testers are identical except temperature scale. They give immediate, accurate readings and can be used for antifreeze/coolants that contain ethylene or propylene glycol. Both are available at your Caterpillar dealer.If propylene glycol based antifreeze is used, DO NOT allow concentration greater than a 50/50 antifreeze to water mixture. The measurement of freeze protection must be made with a refractive-type tester (5P0957 or 5P3514) rather than a hydrometer-type, which can be used to test ethylene glycol based antifreeze.Supplemental Coolant Additive (Conditioner)
Supplemental coolant additive (conditioner) is necessary to prevent rust, scale, pitting and/or corrosion