Information injection-pump assembly
BOSCH
9 400 612 618
9400612618
ZEXEL
101606-0440
1016060440
ISUZU
8976021430
8976021430
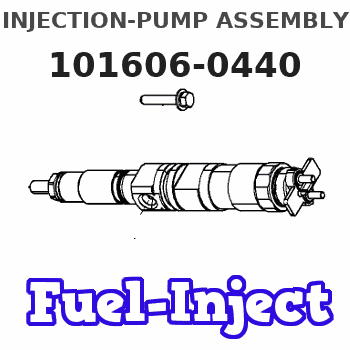
Rating:
Service parts 101606-0440 INJECTION-PUMP ASSEMBLY:
1.
_
7.
COUPLING PLATE
8.
_
9.
_
11.
Nozzle and Holder
8-94391-291-4
12.
Open Pre:MPa(Kqf/cm2)
16.2{165}/19.6{200}
14.
NOZZLE
Cross reference number
BOSCH
9 400 612 618
9400612618
ZEXEL
101606-0440
1016060440
ISUZU
8976021430
8976021430
Zexel num
Bosch num
Firm num
Name
9 400 612 618
8976021430 ISUZU
INJECTION-PUMP ASSEMBLY
6HL1-S K 14BN INJECTION PUMP ASSY PE
6HL1-S K 14BN INJECTION PUMP ASSY PE
Calibration Data:
Adjustment conditions
Test oil
1404 Test oil ISO4113 or {SAEJ967d}
1404 Test oil ISO4113 or {SAEJ967d}
Test oil temperature
degC
40
40
45
Nozzle and nozzle holder
105780-8310
Nozzle
105780-0120
Bosch type code
1 688 901 990
Nozzle holder
105780-2240
Opening pressure
MPa
18
Opening pressure
kgf/cm2
184
Injection pipe
Outer diameter - inner diameter - length (mm) mm 6-2-600
Outer diameter - inner diameter - length (mm) mm 6-2-600
Overflow valve
131424-8620
Overflow valve opening pressure
kPa
206
172
240
Overflow valve opening pressure
kgf/cm2
2.1
1.75
2.45
Tester oil delivery pressure
kPa
255
255
255
Tester oil delivery pressure
kgf/cm2
2.6
2.6
2.6
Direction of rotation (viewed from drive side)
Left L
Left L
Injection timing adjustment
Direction of rotation (viewed from drive side)
Left L
Left L
Injection order
1-5-3-6-
2-4
Pre-stroke
mm
3.8
3.75
3.85
Rack position
Point A R=A
Point A R=A
Beginning of injection position
Governor side NO.1
Governor side NO.1
Difference between angles 1
Cal 1-5 deg. 60 59.5 60.5
Cal 1-5 deg. 60 59.5 60.5
Difference between angles 2
Cal 1-3 deg. 120 119.5 120.5
Cal 1-3 deg. 120 119.5 120.5
Difference between angles 3
Cal 1-6 deg. 180 179.5 180.5
Cal 1-6 deg. 180 179.5 180.5
Difference between angles 4
Cyl.1-2 deg. 240 239.5 240.5
Cyl.1-2 deg. 240 239.5 240.5
Difference between angles 5
Cal 1-4 deg. 300 299.5 300.5
Cal 1-4 deg. 300 299.5 300.5
Injection quantity adjustment
Adjusting point
-
Rack position
14.2
Pump speed
r/min
850
850
850
Average injection quantity
mm3/st.
65
63.4
66.6
Max. variation between cylinders
%
0
-2.5
2.5
Basic
*
Fixing the rack
*
Standard for adjustment of the maximum variation between cylinders
*
Injection quantity adjustment_02
Adjusting point
Z
Rack position
9.7+-0.5
Pump speed
r/min
295
295
295
Average injection quantity
mm3/st.
13
11.7
14.3
Max. variation between cylinders
%
0
-14
14
Fixing the rack
*
Standard for adjustment of the maximum variation between cylinders
*
Injection quantity adjustment_03
Adjusting point
A
Rack position
R1(14.2)
Pump speed
r/min
850
850
850
Average injection quantity
mm3/st.
65
64
66
Basic
*
Fixing the lever
*
Test data Ex:
Governor adjustment
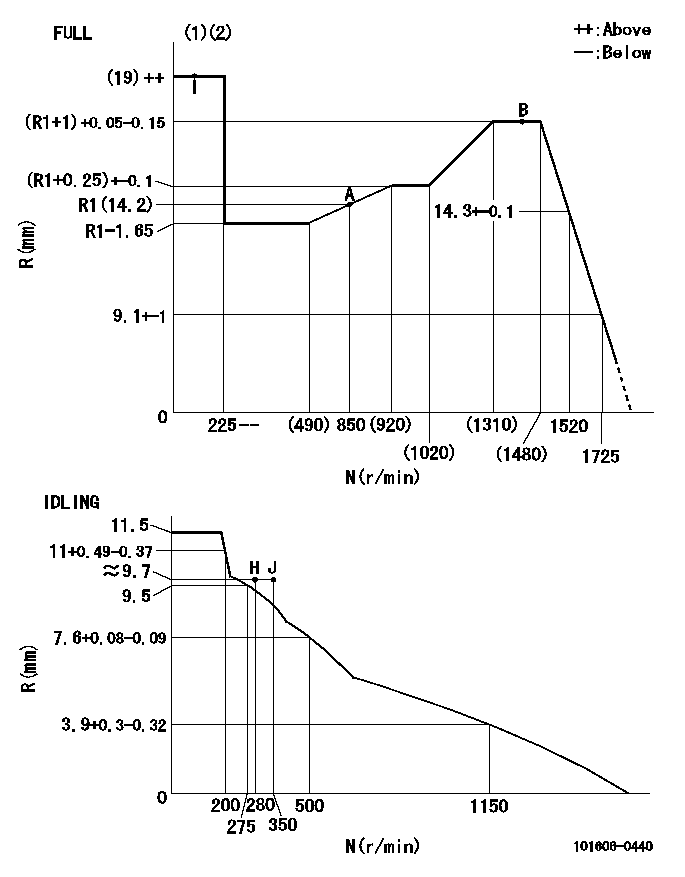
N:Pump speed
R:Rack position (mm)
(1)Torque cam stamping: T1
(2)Tolerance for racks not indicated: +-0.05mm.
----------
T1=P28
----------
----------
T1=P28
----------
Timer adjustment

(1)Adjusting range
(2)Step response time
(N): Speed of the pump
(L): Load
(theta) Advance angle
(Srd1) Step response time 1
(Srd2) Step response time 2
1. Adjusting conditions for the variable timer
(1)Adjust the clearance between the pickup and the protrusion to L.
----------
L=1.5+-0.2mm N2=800r/min C2=(8)deg t1=2--sec. t2=2--sec.
----------
N1=1300++r/min P1=0kPa(0kgf/cm2) P2=392kPa(4kgf/cm2) C1=8+-0.3deg R01=0/4load R02=4/4load
----------
L=1.5+-0.2mm N2=800r/min C2=(8)deg t1=2--sec. t2=2--sec.
----------
N1=1300++r/min P1=0kPa(0kgf/cm2) P2=392kPa(4kgf/cm2) C1=8+-0.3deg R01=0/4load R02=4/4load
Speed control lever angle
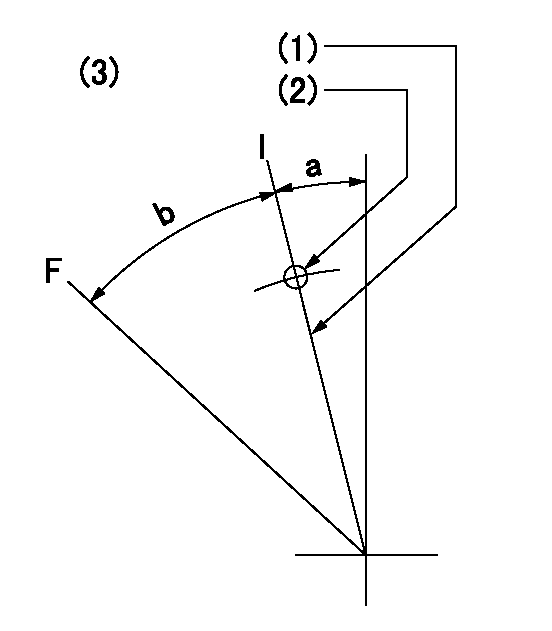
F:Full speed
I:Idle
(1)Stopper bolt set position 'H'
(2)Use the pin at R = aa
(3)Viewed from feed pump side.
----------
aa=35mm
----------
a=11deg+-5deg b=40deg+-3deg
----------
aa=35mm
----------
a=11deg+-5deg b=40deg+-3deg
Stop lever angle
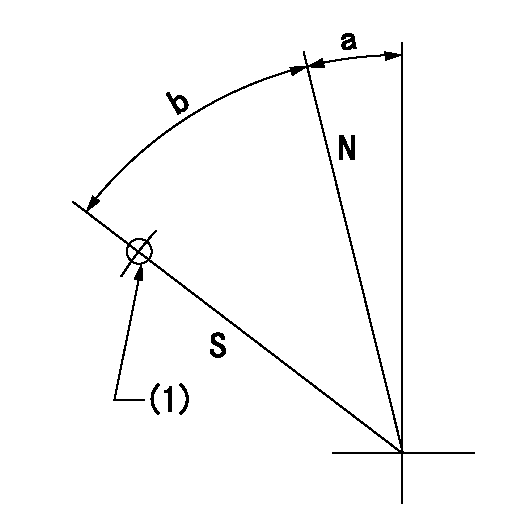
N:Pump normal
S:Stop the pump.
(1)Use the pin at R = aa
----------
aa=45mm
----------
a=12.5deg+-5deg b=40deg+-5deg
----------
aa=45mm
----------
a=12.5deg+-5deg b=40deg+-5deg
0000001501 RACK SENSOR

Rack sensor adjustment
1. Flange type rack sensor (rack sensor adjustment -5*20)
(1)These types of rack sensors do not need adjustment. Confirm the performance with the following procedures.
(2)Mount the rack sensor main body to the pump main body.
(3)Fix the pump lever at full.
(4)At supply voltage V1, pump speed N1 and rack position Ra, confirm that the amp's output voltage is Vist.
(5)Move the pump lever two or three times.
(6)Set again to full.
(7)Confirm that the amplifier output voltage is Vist.
(8)Fix the caution plate to the upper part of the rack sensor.
(For those without the caution plate instructions, make sure the nameplate of the rack sensor carries the "Don't hold here" caution.)
(9)Apply red paint to the rack sensor mounting bolts (2 places).
----------
V1=5+-0.01V N1=850r/min Ra=R1(14.2)mm Vist=3.49+-0.28V
----------
----------
V1=5+-0.01V N1=850r/min Ra=R1(14.2)mm Vist=3.49+-0.28V
----------
Timing setting

(1)Pump vertical direction
(2)Positions of coupling's threaded installation holes at No 1 cylinder's beginning of injection
(3)B.T.D.C.: aa
(4)-
----------
aa=6deg
----------
a=(160deg)
----------
aa=6deg
----------
a=(160deg)
Information:
3176 ATAAC Truck Engine Model Views
Oil Filter (1), Coolant Conditioner Element (2), Thermostat Housing (3), Oil Filter (4) and Turbocharger (5).
Fuel Filter and Priming Pump (6), Electronic Governor and Personality Module (7), Crankcase Breather (8), Grounding Stud (9).Engine Information
The Caterpillar 3176 ATAAC Diesel Truck engine is an 629 cu.in. (10.3 L) displacement, 4.9 in. (125 mm) bore, 5.5 in. (140 mm) stroke, four stroke cycle, 6 cylinder engine. The firing order is 1-5-3-6-2-4 and the direction of rotation is counterclockwise, as viewed from the flywheel. The 3176 is an electronically controlled, mechanically actuated unit injector diesel engine. Timing advance is achieved by precise control of injector firing. Engine speed is controlled by adjusting the firing duration. A speed timing sensor provides information to the fuel cooled ECM (Electronic Control Module) for detection of cylinder position and engine speed.The 3176 electronic engine control system was designed to provide electronic governing, automatic air-fuel ratio control, torque rise shaping, injection timing control and system diagnostics.Additional benefits such as improved cold starting capability, tamper resistance, diagnostics, cruise control, vehicle speed limiting, progressive shift engine speed control, PTO governor and American Trucking Association (ATA) data link and an Engine Monitoring Package (if equipped) provide for additional engine fuel economy, driver comfort and serviceability.The fuel system is a mechanically actuated, electronically controlled unit injector combining the pumping, electronic fuel metering and injecting elements in a single unit to produce higher injection pressures (22,000 psi [151 600 kPa]). High injection pressures help to reduce fuel consumption and particulate emissions.The use of this type of unit injector provides total electronic control of injection timing. The injection timing is varied as a function of engine operating conditions. This optimizes the engine's performance for starting, emissions, noise, fuel consumption and driveability.The 3176 has built-in diagnostics to assure that all components are functioning and operating properly. In the event of a system component deviation from programmed limits, the operator will be alerted to the condition by a dashboard mounted CHECK ENGINE/DIAGNOSTIC lamp.A Caterpillar service tool may be used to read the numerical code of the faulty component. Intermittent faults are logged and stored in the system memory. Refer to Engine Diagnostics section of this publication for alternative methods.The cooling system consists of a gear driven centrifugal pump, with one thermostat which regulates the engine coolant water temperature, a plate type oil cooler and a radiator incorporating a shunt system.The 3176 does not have a cylinder block water cooling system. Instead, the cast water manifold in the spacer deck distributes 65% of the coolant volume to each of the cylinder liners and the remaining 35% flows directly to the cylinder head.The engine lubricating oil, which is both cooled and filtered, is supplied by a gear-type pump. Bypass valves provide unrestricted flow of lubrication oil to the engine parts when oil viscosity is high, or if either the oil cooler or the oil filter elements (paper cartridge) should become plugged.Engine efficiency, efficiency of emission controls and engine performance depend on adherence
Oil Filter (1), Coolant Conditioner Element (2), Thermostat Housing (3), Oil Filter (4) and Turbocharger (5).
Fuel Filter and Priming Pump (6), Electronic Governor and Personality Module (7), Crankcase Breather (8), Grounding Stud (9).Engine Information
The Caterpillar 3176 ATAAC Diesel Truck engine is an 629 cu.in. (10.3 L) displacement, 4.9 in. (125 mm) bore, 5.5 in. (140 mm) stroke, four stroke cycle, 6 cylinder engine. The firing order is 1-5-3-6-2-4 and the direction of rotation is counterclockwise, as viewed from the flywheel. The 3176 is an electronically controlled, mechanically actuated unit injector diesel engine. Timing advance is achieved by precise control of injector firing. Engine speed is controlled by adjusting the firing duration. A speed timing sensor provides information to the fuel cooled ECM (Electronic Control Module) for detection of cylinder position and engine speed.The 3176 electronic engine control system was designed to provide electronic governing, automatic air-fuel ratio control, torque rise shaping, injection timing control and system diagnostics.Additional benefits such as improved cold starting capability, tamper resistance, diagnostics, cruise control, vehicle speed limiting, progressive shift engine speed control, PTO governor and American Trucking Association (ATA) data link and an Engine Monitoring Package (if equipped) provide for additional engine fuel economy, driver comfort and serviceability.The fuel system is a mechanically actuated, electronically controlled unit injector combining the pumping, electronic fuel metering and injecting elements in a single unit to produce higher injection pressures (22,000 psi [151 600 kPa]). High injection pressures help to reduce fuel consumption and particulate emissions.The use of this type of unit injector provides total electronic control of injection timing. The injection timing is varied as a function of engine operating conditions. This optimizes the engine's performance for starting, emissions, noise, fuel consumption and driveability.The 3176 has built-in diagnostics to assure that all components are functioning and operating properly. In the event of a system component deviation from programmed limits, the operator will be alerted to the condition by a dashboard mounted CHECK ENGINE/DIAGNOSTIC lamp.A Caterpillar service tool may be used to read the numerical code of the faulty component. Intermittent faults are logged and stored in the system memory. Refer to Engine Diagnostics section of this publication for alternative methods.The cooling system consists of a gear driven centrifugal pump, with one thermostat which regulates the engine coolant water temperature, a plate type oil cooler and a radiator incorporating a shunt system.The 3176 does not have a cylinder block water cooling system. Instead, the cast water manifold in the spacer deck distributes 65% of the coolant volume to each of the cylinder liners and the remaining 35% flows directly to the cylinder head.The engine lubricating oil, which is both cooled and filtered, is supplied by a gear-type pump. Bypass valves provide unrestricted flow of lubrication oil to the engine parts when oil viscosity is high, or if either the oil cooler or the oil filter elements (paper cartridge) should become plugged.Engine efficiency, efficiency of emission controls and engine performance depend on adherence