Information injection-pump assembly
BOSCH
9 400 613 033
9400613033
ZEXEL
101606-0130
1016060130
ISUZU
8976001800
8976001800
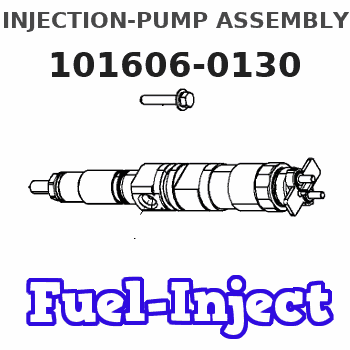
Rating:
Compare Prices: .
As an associate, we earn commssions on qualifying purchases through the links below
Service parts 101606-0130 INJECTION-PUMP ASSEMBLY:
1.
_
7.
COUPLING PLATE
8.
_
9.
_
11.
Nozzle and Holder
8-94395-498-2
12.
Open Pre:MPa(Kqf/cm2)
18.1{185}
15.
NOZZLE SET
Cross reference number
BOSCH
9 400 613 033
9400613033
ZEXEL
101606-0130
1016060130
ISUZU
8976001800
8976001800
Zexel num
Bosch num
Firm num
Name
101606-0130
9 400 613 033
8976001800 ISUZU
INJECTION-PUMP ASSEMBLY
6HH1-S K 14BN INJECTION PUMP ASSY PE
6HH1-S K 14BN INJECTION PUMP ASSY PE
Calibration Data:
Adjustment conditions
Test oil
1404 Test oil ISO4113 or {SAEJ967d}
1404 Test oil ISO4113 or {SAEJ967d}
Test oil temperature
degC
40
40
45
Nozzle and nozzle holder
105780-8260
Bosch type code
1 688 901 101
Nozzle
105780-0120
Bosch type code
1 688 901 990
Nozzle holder
105780-2190
Opening pressure
MPa
18
Opening pressure
kgf/cm2
184
Injection pipe
Outer diameter - inner diameter - length (mm) mm 6-2-600
Outer diameter - inner diameter - length (mm) mm 6-2-600
Overflow valve
131424-4920
Overflow valve opening pressure
kPa
127
107
147
Overflow valve opening pressure
kgf/cm2
1.3
1.1
1.5
Tester oil delivery pressure
kPa
255
255
255
Tester oil delivery pressure
kgf/cm2
2.6
2.6
2.6
Direction of rotation (viewed from drive side)
Left L
Left L
Injection timing adjustment
Direction of rotation (viewed from drive side)
Left L
Left L
Injection order
1-5-3-6-
2-4
Pre-stroke
mm
4
3.95
4.05
Beginning of injection position
Governor side NO.1
Governor side NO.1
Difference between angles 1
Cal 1-5 deg. 60 59.5 60.5
Cal 1-5 deg. 60 59.5 60.5
Difference between angles 2
Cal 1-3 deg. 120 119.5 120.5
Cal 1-3 deg. 120 119.5 120.5
Difference between angles 3
Cal 1-6 deg. 180 179.5 180.5
Cal 1-6 deg. 180 179.5 180.5
Difference between angles 4
Cyl.1-2 deg. 240 239.5 240.5
Cyl.1-2 deg. 240 239.5 240.5
Difference between angles 5
Cal 1-4 deg. 300 299.5 300.5
Cal 1-4 deg. 300 299.5 300.5
Injection quantity adjustment
Adjusting point
-
Rack position
11.6
Pump speed
r/min
850
850
850
Average injection quantity
mm3/st.
91.5
89.9
93.1
Max. variation between cylinders
%
0
-2.5
2.5
Basic
*
Fixing the rack
*
Standard for adjustment of the maximum variation between cylinders
*
Injection quantity adjustment_02
Adjusting point
Z
Rack position
9.6+-0.5
Pump speed
r/min
240
240
240
Average injection quantity
mm3/st.
9.4
8.1
10.7
Max. variation between cylinders
%
0
-14
14
Fixing the rack
*
Standard for adjustment of the maximum variation between cylinders
*
Injection quantity adjustment_03
Adjusting point
A
Rack position
R1(11.6)
Pump speed
r/min
850
850
850
Average injection quantity
mm3/st.
91.5
90.5
92.5
Basic
*
Fixing the lever
*
Injection quantity adjustment_04
Adjusting point
B
Rack position
R1+0.95
Pump speed
r/min
1425
1425
1425
Average injection quantity
mm3/st.
100.5
96.5
104.5
Fixing the lever
*
Injection quantity adjustment_05
Adjusting point
C
Rack position
R1+0.6
Pump speed
r/min
1150
1150
1150
Average injection quantity
mm3/st.
98.5
94.5
102.5
Fixing the lever
*
Injection quantity adjustment_06
Adjusting point
I
Rack position
-
Pump speed
r/min
150
150
150
Average injection quantity
mm3/st.
130
130
138
Fixing the lever
*
Rack limit
*
Timer adjustment
Pump speed
r/min
905--
Advance angle
deg.
0
0
0
Load
0/4
Remarks
Start
Start
Timer adjustment_02
Pump speed
r/min
855
Advance angle
deg.
0.3
Load
0/4
Timer adjustment_03
Pump speed
r/min
(900)
Advance angle
deg.
0
0
0
Load
4/4
Remarks
Start
Start
Timer adjustment_04
Pump speed
r/min
1425
Advance angle
deg.
5.5
5
6
Load
4/4
Remarks
Finish
Finish
Test data Ex:
Governor adjustment
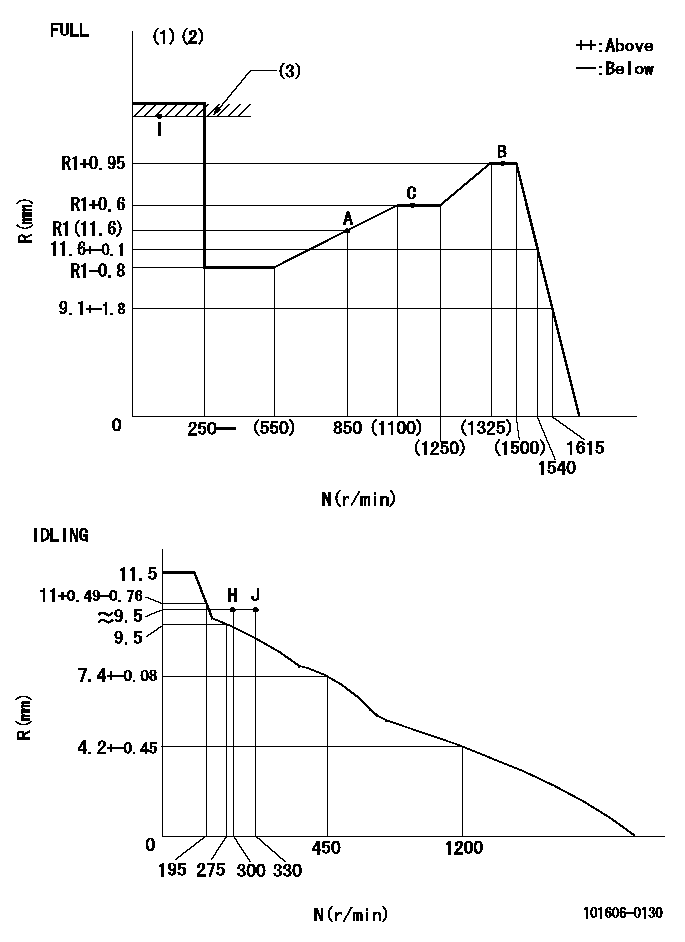
N:Pump speed
R:Rack position (mm)
(1)Torque cam stamping: T1
(2)Tolerance for racks not indicated: +-0.05mm.
(3)RACK LIMIT
----------
T1=K97
----------
----------
T1=K97
----------
Speed control lever angle
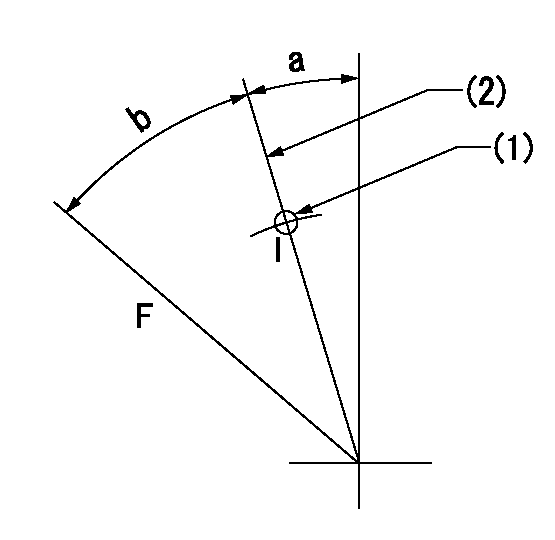
F:Full speed
I:Idle
(1)Use the pin at R = aa
(2)Stopper bolt set position 'H'
----------
aa=35mm
----------
a=11deg+-5deg b=38deg+-3deg
----------
aa=35mm
----------
a=11deg+-5deg b=38deg+-3deg
Stop lever angle
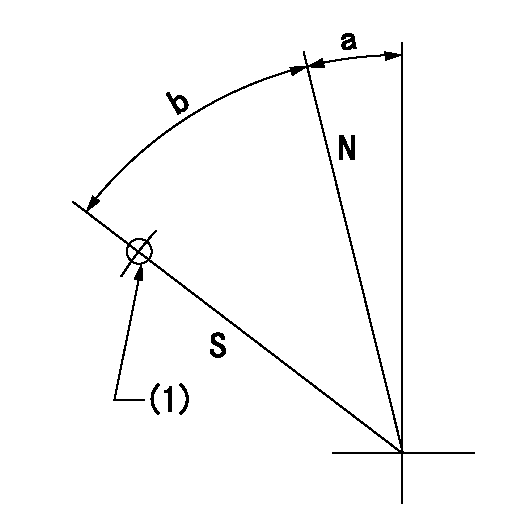
N:Pump normal
S:Stop the pump.
(1)Use the pin at R = aa
----------
aa=45mm
----------
a=12.5deg+-5deg b=40deg+-5deg
----------
aa=45mm
----------
a=12.5deg+-5deg b=40deg+-5deg
0000001501 ACS

(A) Housing
(B) Snap ring
(C) adjusting screw
(D) Set screw
(E): Push rod
(F) Spacer
1. Adjustment of the aneroid compensator
(1)Adjust with the (D) set screw so that the clearance between the (A) housing and (B) snap ring is L1.
(2)Select the push rod (E) so that the distance from the end surface of the (F) spacer becomes L2.
(3)(C) Turn the screw to adjust the beginning of aneroid compensator operation.
2. Adjustment when mounting the governor.
(1)Set the speed of the pump to N1 r/min and fix the control lever at the full set position.
(2)Adjust using screw C to obtain the performance shown in the graph above.
(3)After final adjustment, confirm that the gap between housing (A) and snapring (B) is L3.
----------
N1=1425r/min L1=1.4~1.7mm L2=0.5+-0.5mm L3=0.1~0.5mm
----------
Ra=R2(R1+0.95)mm Rb=(R2-0.8)mm Pa=(89.8)+-2.7kPa((674)+-20mmHg) Pb=70.1+-0.7kPa(526+-5mmHg) Q1=(100.5)+-2cm3/1000st Q2=85.5+-2cm3/1000st
----------
N1=1425r/min L1=1.4~1.7mm L2=0.5+-0.5mm L3=0.1~0.5mm
----------
Ra=R2(R1+0.95)mm Rb=(R2-0.8)mm Pa=(89.8)+-2.7kPa((674)+-20mmHg) Pb=70.1+-0.7kPa(526+-5mmHg) Q1=(100.5)+-2cm3/1000st Q2=85.5+-2cm3/1000st
Timing setting

(1)Pump vertical direction
(2)Position of timer's threaded hole at No 1 cylinder's beginning of injection
(3)B.T.D.C.: aa
(4)-
----------
aa=7deg
----------
a=(150deg)
----------
aa=7deg
----------
a=(150deg)
Information:
Oiler Feed Adjustment
If necessary, adjust the lubricator to release approximately four drops of fluid per minute into the starting motor air stream. Be sure there is NO fuel supply to the engine. 1. Push on the air start control lever (1) to crank the engine.2. Count the drops of fluid per minute that are released into the air stream. Turn the needle valve knob (3) counterclockwise to increase the flow and clockwise to decrease the flow of fluid into the air stream.Collector Bowl
Some air starters may be equipped with a collector bowl. The bowl collects used oil after the oil has lubricated the vanes. The bowl also collects moisture condensation from the compressed air. When the collector bowl becomes half full, drain the used lubricant. Never fill the lubricator bowl with oil from the collector bowl- use clean lubricant.Air Tank (If Equipped)
For good life of the air starting motor, the air supply must be free of dirt and water. The air starter requires adequate air pressure in order to operate.* Drain water from the air tank (if equipped). Open the drain valve on the bottom of the air tank to drain the condensation and oil carryover.* Check the air supply pressure. The air starting motor requires a minimum of 620 kPa (90 psi) of air pressure to operate properly. The maximum air pressure must not exceed 1550 kPa (225 psi). The normal air pressure will be 758 kPa (110 psi) to 965 kPa (140 psi).Engine Air Cleaner
Check Air Cleaner Service Indicator
Typical air cleaner indicator, mounted on the air cleaner housing. Your engine may be equipped with a different indicator.A service indicator (if equipped) may be mounted on the air cleaner or in a remote location. A colored piston showing in the window indicates the need for servicing the air cleaner. Observe the air cleaner service indicator. Clean or replace the air cleaner element when the yellow diaphragm enters the red zone or the red piston locks in the visible position. If the air cleaner indicator shows red at any time, clean the filter element or install a new air cleaner element.
Never service the air cleaner with the engine running since this will allow dirt to enter the engine.
If your air cleaner element becomes plugged, the air can split the element filter material. Unfiltered air will drastically accelerate internal engine wear. Your Caterpillar dealer has air filter elements to service this unit. Contact your Caterpillar dealer for the correct filter element. If equipped with a Light Duty air cleaner element, refer to the 50 Hour interval for information.Single Stage Air Cleaner Elements
Remove and Install Air Cleaner Elements
1. Remove the air cleaner cover (1) and element (2).2. Seal the turbocharger air inlet (3) so that debris can not enter the inlet. Use tape, or secure a clean cloth over the opening.3. Clean the inside of the air cleaner cover and body.4. Inspect the replacement element for damage, dirt or debris.5. Remove the seal from the turbocharger inlet.6. Install a clean,
If necessary, adjust the lubricator to release approximately four drops of fluid per minute into the starting motor air stream. Be sure there is NO fuel supply to the engine. 1. Push on the air start control lever (1) to crank the engine.2. Count the drops of fluid per minute that are released into the air stream. Turn the needle valve knob (3) counterclockwise to increase the flow and clockwise to decrease the flow of fluid into the air stream.Collector Bowl
Some air starters may be equipped with a collector bowl. The bowl collects used oil after the oil has lubricated the vanes. The bowl also collects moisture condensation from the compressed air. When the collector bowl becomes half full, drain the used lubricant. Never fill the lubricator bowl with oil from the collector bowl- use clean lubricant.Air Tank (If Equipped)
For good life of the air starting motor, the air supply must be free of dirt and water. The air starter requires adequate air pressure in order to operate.* Drain water from the air tank (if equipped). Open the drain valve on the bottom of the air tank to drain the condensation and oil carryover.* Check the air supply pressure. The air starting motor requires a minimum of 620 kPa (90 psi) of air pressure to operate properly. The maximum air pressure must not exceed 1550 kPa (225 psi). The normal air pressure will be 758 kPa (110 psi) to 965 kPa (140 psi).Engine Air Cleaner
Check Air Cleaner Service Indicator
Typical air cleaner indicator, mounted on the air cleaner housing. Your engine may be equipped with a different indicator.A service indicator (if equipped) may be mounted on the air cleaner or in a remote location. A colored piston showing in the window indicates the need for servicing the air cleaner. Observe the air cleaner service indicator. Clean or replace the air cleaner element when the yellow diaphragm enters the red zone or the red piston locks in the visible position. If the air cleaner indicator shows red at any time, clean the filter element or install a new air cleaner element.
Never service the air cleaner with the engine running since this will allow dirt to enter the engine.
If your air cleaner element becomes plugged, the air can split the element filter material. Unfiltered air will drastically accelerate internal engine wear. Your Caterpillar dealer has air filter elements to service this unit. Contact your Caterpillar dealer for the correct filter element. If equipped with a Light Duty air cleaner element, refer to the 50 Hour interval for information.Single Stage Air Cleaner Elements
Remove and Install Air Cleaner Elements
1. Remove the air cleaner cover (1) and element (2).2. Seal the turbocharger air inlet (3) so that debris can not enter the inlet. Use tape, or secure a clean cloth over the opening.3. Clean the inside of the air cleaner cover and body.4. Inspect the replacement element for damage, dirt or debris.5. Remove the seal from the turbocharger inlet.6. Install a clean,
Have questions with 101606-0130?
Group cross 101606-0130 ZEXEL
Isuzu
101606-0130
9 400 613 033
8976001800
INJECTION-PUMP ASSEMBLY
6HH1-S
6HH1-S