Information injection-pump assembly
BOSCH
9 400 615 382
9400615382
ZEXEL
101605-9470
1016059470
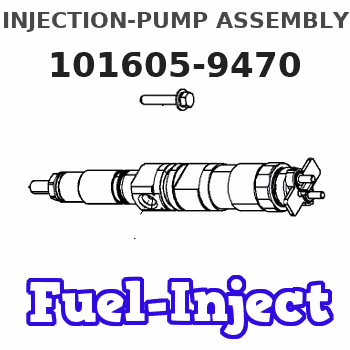
Rating:
Include in #1:
101401-4821
as _
Cross reference number
BOSCH
9 400 615 382
9400615382
ZEXEL
101605-9470
1016059470
Zexel num
Bosch num
Firm num
Name
9 400 615 382
DAEWOO
INJECTION-PUMP ASSEMBLY
DB58T K 14BE INJECTION PUMP ASSY PE6A PE
DB58T K 14BE INJECTION PUMP ASSY PE6A PE
Calibration Data:
Adjustment conditions
Test oil
1404 Test oil ISO4113 or {SAEJ967d}
1404 Test oil ISO4113 or {SAEJ967d}
Test oil temperature
degC
40
40
45
Nozzle and nozzle holder
105780-8140
Bosch type code
EF8511/9A
Nozzle
105780-0000
Bosch type code
DN12SD12T
Nozzle holder
105780-2080
Bosch type code
EF8511/9
Opening pressure
MPa
17.2
Opening pressure
kgf/cm2
175
Injection pipe
Outer diameter - inner diameter - length (mm) mm 6-2-600
Outer diameter - inner diameter - length (mm) mm 6-2-600
Overflow valve
131424-1520
Overflow valve opening pressure
kPa
157
123
191
Overflow valve opening pressure
kgf/cm2
1.6
1.25
1.95
Tester oil delivery pressure
kPa
157
157
157
Tester oil delivery pressure
kgf/cm2
1.6
1.6
1.6
Direction of rotation (viewed from drive side)
Right R
Right R
Injection timing adjustment
Direction of rotation (viewed from drive side)
Right R
Right R
Injection order
1-5-3-6-
2-4
Pre-stroke
mm
3.4
3.35
3.45
Beginning of injection position
Drive side NO.1
Drive side NO.1
Difference between angles 1
Cal 1-5 deg. 60 59.5 60.5
Cal 1-5 deg. 60 59.5 60.5
Difference between angles 2
Cal 1-3 deg. 120 119.5 120.5
Cal 1-3 deg. 120 119.5 120.5
Difference between angles 3
Cal 1-6 deg. 180 179.5 180.5
Cal 1-6 deg. 180 179.5 180.5
Difference between angles 4
Cyl.1-2 deg. 240 239.5 240.5
Cyl.1-2 deg. 240 239.5 240.5
Difference between angles 5
Cal 1-4 deg. 300 299.5 300.5
Cal 1-4 deg. 300 299.5 300.5
Injection quantity adjustment
Adjusting point
A
Rack position
9.1
Pump speed
r/min
1100
1100
1100
Average injection quantity
mm3/st.
73.5
72
75
Max. variation between cylinders
%
0
-2.5
2.5
Basic
*
Fixing the lever
*
Boost pressure
kPa
40
40
Boost pressure
mmHg
300
300
Injection quantity adjustment_02
Adjusting point
-
Rack position
6.8+-0.5
Pump speed
r/min
475
475
475
Average injection quantity
mm3/st.
9.4
8.1
10.7
Max. variation between cylinders
%
0
-14
14
Fixing the rack
*
Boost pressure
kPa
0
0
0
Boost pressure
mmHg
0
0
0
Remarks
Adjust only variation between cylinders; adjust governor according to governor specifications.
Adjust only variation between cylinders; adjust governor according to governor specifications.
Injection quantity adjustment_03
Adjusting point
E
Rack position
-
Pump speed
r/min
90
90
90
Average injection quantity
mm3/st.
65
65
85
Fixing the lever
*
Boost pressure
kPa
0
0
0
Boost pressure
mmHg
0
0
0
Rack limit
*
Boost compensator adjustment
Pump speed
r/min
500
500
500
Rack position
R1-0.25
Boost pressure
kPa
20
17.3
22.7
Boost pressure
mmHg
150
130
170
Boost compensator adjustment_02
Pump speed
r/min
500
500
500
Rack position
R1(9.1)
Boost pressure
kPa
26.7
26.7
26.7
Boost pressure
mmHg
200
200
200
Test data Ex:
Governor adjustment
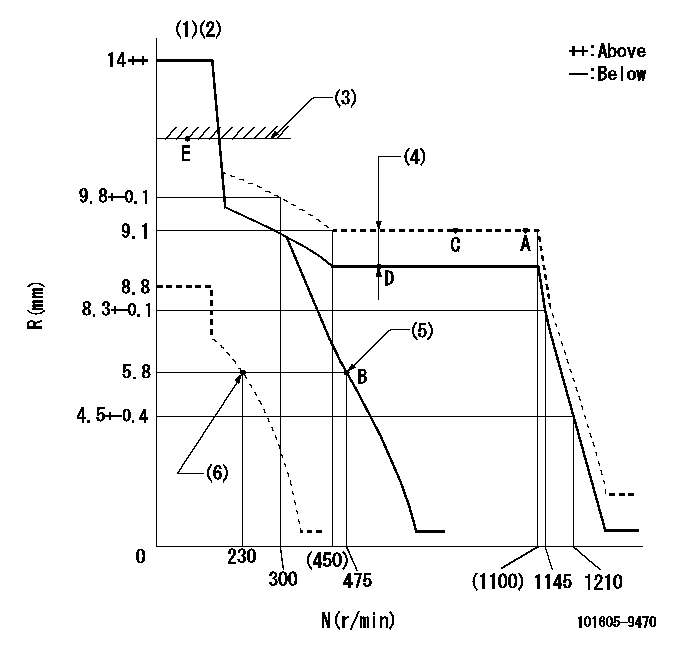
N:Pump speed
R:Rack position (mm)
(1)Target notch: K
(2)Tolerance for racks not indicated: +-0.05mm.
(3)RACK LIMIT
(4)Boost compensator stroke: BCL
(5)Main spring setting
(6)Set idle sub-spring
----------
K=5 BCL=0.25+-0.1mm
----------
----------
K=5 BCL=0.25+-0.1mm
----------
Speed control lever angle

F:Full speed
I:Idle
(1)Stopper bolt setting
----------
----------
a=1deg+-5deg b=17deg+-5deg
----------
----------
a=1deg+-5deg b=17deg+-5deg
Stop lever angle
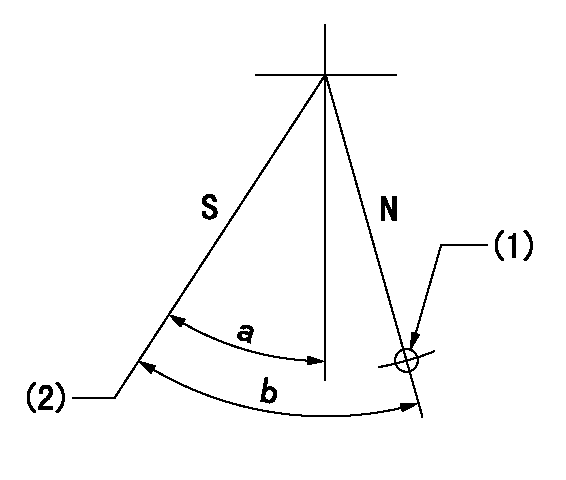
N:Pump normal
S:Stop the pump.
(1)Use the hole at R = aa
(2)Speed = bb, rack position = cc (sealed at delivery)
----------
aa=40mm bb=0r/min cc=1-0.5mm
----------
a=44.5deg+-5deg b=(50deg)
----------
aa=40mm bb=0r/min cc=1-0.5mm
----------
a=44.5deg+-5deg b=(50deg)
Timing setting

(1)Pump vertical direction
(2)Position of gear mark 'CC' at No 1 cylinder's beginning of injection
(3)B.T.D.C.: aa
(4)-
----------
aa=18deg
----------
a=(90deg)
----------
aa=18deg
----------
a=(90deg)
Information:
Caterpillar's Scheduled Oil Sampling (S O S) is the best indicator for determining what is happening inside your engine.S O S is a diagnostic tool designed to identify and measure contamination and condition of oil, oil performance and component wear rates. The program identifies and measures contamination such as soot, sulfur, etc., and the presence of fuel, water and antifreeze in a sample of oil. The tests also determine the amount of wear metals present in the oil sample, which is compared to established Caterpillar norms to determine acceptability.Caterpillar recommends using Scheduled Oil Sampling (S O S), at regularly scheduled intervals, to compliment your preventive maintenance program. To be effective as an indicator, S O S MUST be performed on a continuing basis. Intermittent sampling will NOT allow wear rate trend lines to be established. The Caterpillar Scheduled Oil Sampling Program (S O S), was developed to help Caterpillar users realize the highest possible value from their equipment by minimizing repair costs and maximizing availability.Obtain S O S samples at regularly scheduled intervals to monitor the condition and maintenance requirements of your engine. Consult your Caterpillar dealer for complete information and assistance in establishing an S O S program for your engine(s). Infrared analysis should always be accompanied by wear element analysis and chemical and physical tests to assure accurate diagnosis. Infrared analysis must be used to determine oil change intervals. S O S must include Infrared (IR) in the analysis.S O S Analysis
S O S is composed of three basic tests:* Wear Analysis* Chemical and Physical Tests* Oil Condition Analysis Wear Analysis is performed with an atomic absorption spectrophotometer to monitor component wear rates by identifying and measuring concentrations, in parts per million, of wear elements present in the used oil.Based on known normal concentration data, maximum limits of wear elements are established. Impending failures can be identified when test results deviate from concentration levels established as acceptable, based on normal wear. Through monitoring the used oil, normal component wear trends are determined. Many failures can be identified when wear trends and/or contaminants significantly exceed past trends.Detectable failures are those caused by component wear and gradual contamination from dirt, fuel, water or antifreeze. Wear analysis is not able to predict failures due to component fatigue, sudden loss of lubrication, or sudden ingestion of a large amount of dirt or contaminants since failures of this nature occur too rapidly. Chemical and Physical Tests detect the presence of water, fuel and/or glycol (antifreeze) in the oil and determine whether or not their concentrations exceed established maximum limits. Oil Condition Analysis is evaluated with Infrared Analysis and determines the degree of deterioration of the used oil by measuring the amount of contaminants such as sulfur products, oxidation, nitration products and soot present in the used oil.It also monitors additive depletion and detects ethylene glycol and butyl cellosolve contamination and can assist in customizing (reducing, maintaining or extending) oil change intervals for particular conditions and applications.Oil Condition Analysis can help
S O S is composed of three basic tests:* Wear Analysis* Chemical and Physical Tests* Oil Condition Analysis Wear Analysis is performed with an atomic absorption spectrophotometer to monitor component wear rates by identifying and measuring concentrations, in parts per million, of wear elements present in the used oil.Based on known normal concentration data, maximum limits of wear elements are established. Impending failures can be identified when test results deviate from concentration levels established as acceptable, based on normal wear. Through monitoring the used oil, normal component wear trends are determined. Many failures can be identified when wear trends and/or contaminants significantly exceed past trends.Detectable failures are those caused by component wear and gradual contamination from dirt, fuel, water or antifreeze. Wear analysis is not able to predict failures due to component fatigue, sudden loss of lubrication, or sudden ingestion of a large amount of dirt or contaminants since failures of this nature occur too rapidly. Chemical and Physical Tests detect the presence of water, fuel and/or glycol (antifreeze) in the oil and determine whether or not their concentrations exceed established maximum limits. Oil Condition Analysis is evaluated with Infrared Analysis and determines the degree of deterioration of the used oil by measuring the amount of contaminants such as sulfur products, oxidation, nitration products and soot present in the used oil.It also monitors additive depletion and detects ethylene glycol and butyl cellosolve contamination and can assist in customizing (reducing, maintaining or extending) oil change intervals for particular conditions and applications.Oil Condition Analysis can help