Information injection-pump assembly
BOSCH
9 400 610 696
9400610696
ZEXEL
101605-9331
1016059331
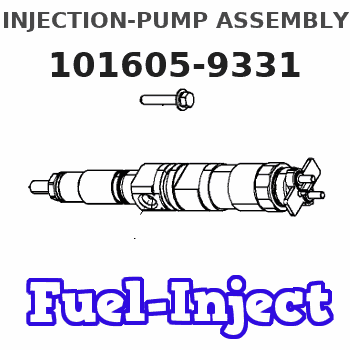
Rating:
Service parts 101605-9331 INJECTION-PUMP ASSEMBLY:
1.
_
5.
AUTOM. ADVANCE MECHANIS
7.
COUPLING PLATE
8.
_
9.
_
11.
Nozzle and Holder
16600-95015
12.
Open Pre:MPa(Kqf/cm2)
19.6{200}
15.
NOZZLE SET
Include in #1:
101605-9331
as INJECTION-PUMP ASSEMBLY
Include in #2:
104749-5390
as _
Cross reference number
BOSCH
9 400 610 696
9400610696
ZEXEL
101605-9331
1016059331
Zexel num
Bosch num
Firm num
Name
Calibration Data:
Adjustment conditions
Test oil
1404 Test oil ISO4113 or {SAEJ967d}
1404 Test oil ISO4113 or {SAEJ967d}
Test oil temperature
degC
40
40
45
Nozzle and nozzle holder
105780-8140
Bosch type code
EF8511/9A
Nozzle
105780-0000
Bosch type code
DN12SD12T
Nozzle holder
105780-2080
Bosch type code
EF8511/9
Opening pressure
MPa
17.2
Opening pressure
kgf/cm2
175
Injection pipe
Outer diameter - inner diameter - length (mm) mm 6-2-600
Outer diameter - inner diameter - length (mm) mm 6-2-600
Overflow valve
131424-1520
Overflow valve opening pressure
kPa
157
123
191
Overflow valve opening pressure
kgf/cm2
1.6
1.25
1.95
Tester oil delivery pressure
kPa
157
157
157
Tester oil delivery pressure
kgf/cm2
1.6
1.6
1.6
Direction of rotation (viewed from drive side)
Right R
Right R
Injection timing adjustment
Direction of rotation (viewed from drive side)
Right R
Right R
Injection order
1-4-2-6-
3-5
Pre-stroke
mm
2.75
2.7
2.8
Beginning of injection position
Drive side NO.1
Drive side NO.1
Difference between angles 1
Cal 1-4 deg. 60 59.5 60.5
Cal 1-4 deg. 60 59.5 60.5
Difference between angles 2
Cyl.1-2 deg. 120 119.5 120.5
Cyl.1-2 deg. 120 119.5 120.5
Difference between angles 3
Cal 1-6 deg. 180 179.5 180.5
Cal 1-6 deg. 180 179.5 180.5
Difference between angles 4
Cal 1-3 deg. 240 239.5 240.5
Cal 1-3 deg. 240 239.5 240.5
Difference between angles 5
Cal 1-5 deg. 300 299.5 300.5
Cal 1-5 deg. 300 299.5 300.5
Injection quantity adjustment
Adjusting point
A
Rack position
10.9
Pump speed
r/min
700
700
700
Average injection quantity
mm3/st.
105.5
104
107
Max. variation between cylinders
%
0
-2
2
Basic
*
Fixing the lever
*
Boost pressure
kPa
60
60
Boost pressure
mmHg
450
450
Injection quantity adjustment_02
Adjusting point
C
Rack position
R1(10.1)
Pump speed
r/min
600
600
600
Average injection quantity
mm3/st.
84.5
82.5
86.5
Fixing the lever
*
Boost pressure
kPa
0
0
0
Boost pressure
mmHg
0
0
0
Injection quantity adjustment_03
Adjusting point
D
Rack position
7+-0.5
Pump speed
r/min
400
400
400
Average injection quantity
mm3/st.
13
11.5
14.5
Max. variation between cylinders
%
0
-10
10
Fixing the rack
*
Boost pressure
kPa
0
0
0
Boost pressure
mmHg
0
0
0
Boost compensator adjustment
Pump speed
r/min
600
600
600
Rack position
R1(10.1)
Boost pressure
kPa
22.7
20
25.4
Boost pressure
mmHg
170
150
190
Boost compensator adjustment_02
Pump speed
r/min
600
600
600
Rack position
10.9
Boost pressure
kPa
48
42.7
53.3
Boost pressure
mmHg
360
320
400
Test data Ex:
Governor adjustment
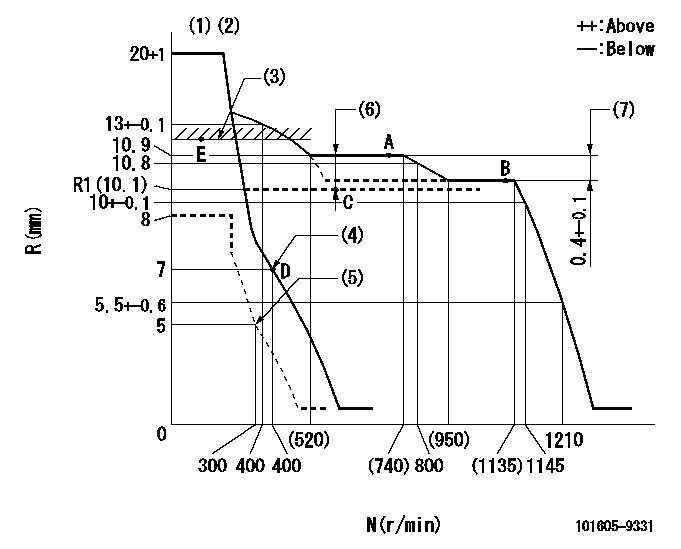
N:Pump speed
R:Rack position (mm)
(1)Target notch: K
(2)Tolerance for racks not indicated: +-0.05mm.
(3)Boost compensator excessive fuel lever at operation: L1 (at 0 boost pressure)
(4)Main spring setting
(5)Set idle sub-spring
(6)Boost compensator stroke: BCL
(7)Rack difference between N = N1 and N = N2
----------
K=16 L1=12.3+-0.2mm BCL=(0.8)mm N1=1100r/min N2=700r/min
----------
----------
K=16 L1=12.3+-0.2mm BCL=(0.8)mm N1=1100r/min N2=700r/min
----------
Speed control lever angle
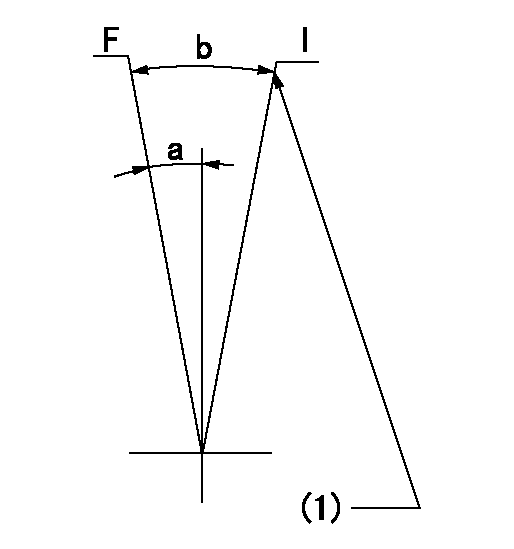
F:Full speed
I:Idle
(1)Stopper bolt setting
----------
----------
a=12deg+-5deg b=21deg+-5deg
----------
----------
a=12deg+-5deg b=21deg+-5deg
Stop lever angle

N:Pump normal
S:Stop the pump.
----------
----------
a=26.5deg+-5deg b=53deg+-5deg
----------
----------
a=26.5deg+-5deg b=53deg+-5deg
0000001101

N:Normal
B:When boosted
(1)Rack position = aa at boost pressure 0.
----------
aa=12.3+-0.2mm
----------
a=(15deg) b=(7deg)
----------
aa=12.3+-0.2mm
----------
a=(15deg) b=(7deg)
Timing setting

(1)Pump vertical direction
(2)Coupling's key groove position at No 1 cylinder's beginning of injection
(3)B.T.D.C.: aa
(4)-
----------
aa=16deg
----------
a=(30deg)
----------
aa=16deg
----------
a=(30deg)
Information:
Engine Lifting
When it is necessary to remove a component on an angle, remember that the capacity of an eyebolt is less as the angle between the supporting members and the object becomes less than 90°. Eyebolts and brackets should never be bent and should only be loaded in tension.
Use a hoist to remove heavy components. Lift the engine by using an adjustable lifting beam. All supporting members (chains and cables) should be parallel to each other, and as near perpendicular as possible to the top of the object being lifted.Some removals require the use of lifting fixtures to obtain proper balance and to provide safe handling. To remove the engine, use the two lifting eyes on the engine.Lifting eyes are designed for the arrangement as sold. Alterations to lifting eyes and/or arrangement weight make the lifting devices obsolete.If you make alterations, you are responsible for providing adequate lifting devices.Engine Storage
If the engine is not started for several weeks, the lubricating oil will drain from the cylinder walls and piston rings. Rust can form on the cylinder liner surface, which will increase engine wear and result in shorter engine life.To prevent excessive engine wear:
Be sure all lubrication recommendations mentioned in the Maintenance Management Schedule intervals chart are completed.If freezing temperatures can be expected, check the cooling system for adequate protection against freezing. A 50/50 solution of Caterpillar permanent-type antifreeze and approved water will give protection below -20°F (-29°C).If it will be impossible to start the engine every week, consult your Caterpillar dealer for instructions to prepare your engine for longer storage periods.If an engine remains out of service and its use is not immediately planned, special precautions should be taken.Refer to "Storage Procedures For Caterpillar Products," Form SEHS9031 for more detailed information on engine storage.
When it is necessary to remove a component on an angle, remember that the capacity of an eyebolt is less as the angle between the supporting members and the object becomes less than 90°. Eyebolts and brackets should never be bent and should only be loaded in tension.
Use a hoist to remove heavy components. Lift the engine by using an adjustable lifting beam. All supporting members (chains and cables) should be parallel to each other, and as near perpendicular as possible to the top of the object being lifted.Some removals require the use of lifting fixtures to obtain proper balance and to provide safe handling. To remove the engine, use the two lifting eyes on the engine.Lifting eyes are designed for the arrangement as sold. Alterations to lifting eyes and/or arrangement weight make the lifting devices obsolete.If you make alterations, you are responsible for providing adequate lifting devices.Engine Storage
If the engine is not started for several weeks, the lubricating oil will drain from the cylinder walls and piston rings. Rust can form on the cylinder liner surface, which will increase engine wear and result in shorter engine life.To prevent excessive engine wear:
Be sure all lubrication recommendations mentioned in the Maintenance Management Schedule intervals chart are completed.If freezing temperatures can be expected, check the cooling system for adequate protection against freezing. A 50/50 solution of Caterpillar permanent-type antifreeze and approved water will give protection below -20°F (-29°C).If it will be impossible to start the engine every week, consult your Caterpillar dealer for instructions to prepare your engine for longer storage periods.If an engine remains out of service and its use is not immediately planned, special precautions should be taken.Refer to "Storage Procedures For Caterpillar Products," Form SEHS9031 for more detailed information on engine storage.