Information injection-pump assembly
BOSCH
F 019 Z10 507
f019z10507
ZEXEL
101605-9200
1016059200
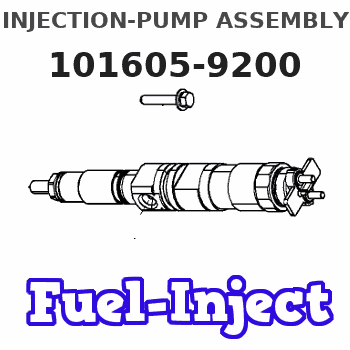
Rating:
Service parts 101605-9200 INJECTION-PUMP ASSEMBLY:
1.
_
5.
AUTOM. ADVANCE MECHANIS
6.
COUPLING PLATE
7.
COUPLING PLATE
8.
_
9.
_
11.
Nozzle and Holder
12.
Open Pre:MPa(Kqf/cm2)
21.6(220)
15.
NOZZLE SET
Include in #1:
101605-9200
as INJECTION-PUMP ASSEMBLY
Include in #2:
104746-1322
as _
Cross reference number
BOSCH
F 019 Z10 507
f019z10507
ZEXEL
101605-9200
1016059200
Zexel num
Bosch num
Firm num
Name
Calibration Data:
Adjustment conditions
Test oil
1404 Test oil ISO4113 or {SAEJ967d}
1404 Test oil ISO4113 or {SAEJ967d}
Test oil temperature
degC
40
40
45
Nozzle and nozzle holder
105780-8140
Bosch type code
EF8511/9A
Nozzle
105780-0000
Bosch type code
DN12SD12T
Nozzle holder
105780-2080
Bosch type code
EF8511/9
Opening pressure
MPa
17.2
Opening pressure
kgf/cm2
175
Injection pipe
Outer diameter - inner diameter - length (mm) mm 6-2-600
Outer diameter - inner diameter - length (mm) mm 6-2-600
Overflow valve
131424-5720
Overflow valve opening pressure
kPa
255
221
289
Overflow valve opening pressure
kgf/cm2
2.6
2.25
2.95
Tester oil delivery pressure
kPa
157
157
157
Tester oil delivery pressure
kgf/cm2
1.6
1.6
1.6
Direction of rotation (viewed from drive side)
Right R
Right R
Injection timing adjustment
Direction of rotation (viewed from drive side)
Right R
Right R
Injection order
1-5-3-6-
2-4
Pre-stroke
mm
3.6
3.55
3.65
Beginning of injection position
Drive side NO.1
Drive side NO.1
Difference between angles 1
Cal 1-5 deg. 60 59.5 60.5
Cal 1-5 deg. 60 59.5 60.5
Difference between angles 2
Cal 1-3 deg. 120 119.5 120.5
Cal 1-3 deg. 120 119.5 120.5
Difference between angles 3
Cal 1-6 deg. 180 179.5 180.5
Cal 1-6 deg. 180 179.5 180.5
Difference between angles 4
Cyl.1-2 deg. 240 239.5 240.5
Cyl.1-2 deg. 240 239.5 240.5
Difference between angles 5
Cal 1-4 deg. 300 299.5 300.5
Cal 1-4 deg. 300 299.5 300.5
Injection quantity adjustment
Adjusting point
A
Rack position
8.6
Pump speed
r/min
800
800
800
Average injection quantity
mm3/st.
71
70
72
Max. variation between cylinders
%
0
-2.5
2.5
Basic
*
Fixing the lever
*
Injection quantity adjustment_02
Adjusting point
-
Rack position
6.4+-0.5
Pump speed
r/min
400
400
400
Average injection quantity
mm3/st.
12
10.7
13.3
Max. variation between cylinders
%
0
-14
14
Fixing the rack
*
Remarks
Adjust only variation between cylinders; adjust governor according to governor specifications.
Adjust only variation between cylinders; adjust governor according to governor specifications.
Injection quantity adjustment_03
Adjusting point
C
Rack position
-
Pump speed
r/min
100
100
100
Average injection quantity
mm3/st.
58
58
63
Fixing the lever
*
Rack limit
*
Test data Ex:
Governor adjustment
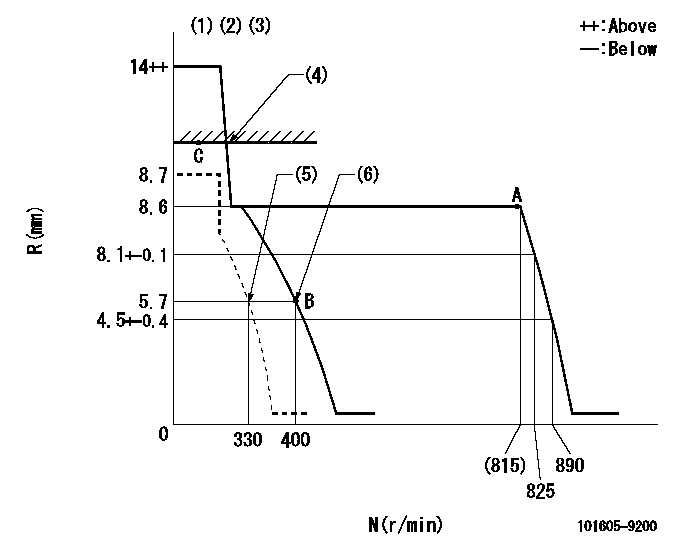
N:Pump speed
R:Rack position (mm)
(1)Target notch: K
(2)Tolerance for racks not indicated: +-0.05mm.
(3)The torque control spring does not operate.
(4)RACK LIMIT
(5)Set idle sub-spring
(6)Main spring setting
----------
K=4
----------
----------
K=4
----------
Speed control lever angle

F:Full speed
I:Idle
(1)Stopper bolt setting
----------
----------
a=6deg+-5deg b=18deg+-5deg
----------
----------
a=6deg+-5deg b=18deg+-5deg
Stop lever angle
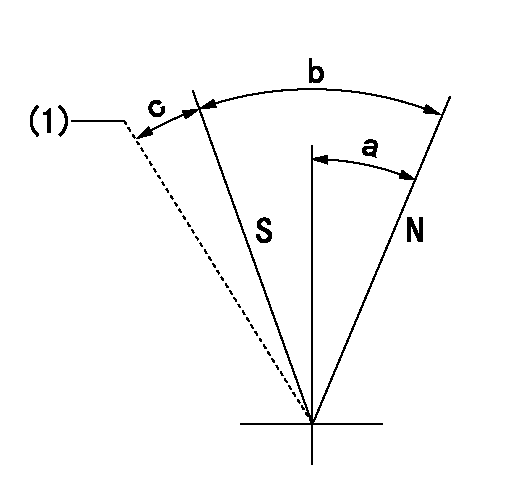
N:Pump normal
S:Stop the pump.
(1)Hold the boss against the stop side
----------
----------
a=26.5deg+-5deg b=53deg+-5deg c=(9deg)
----------
----------
a=26.5deg+-5deg b=53deg+-5deg c=(9deg)
Timing setting
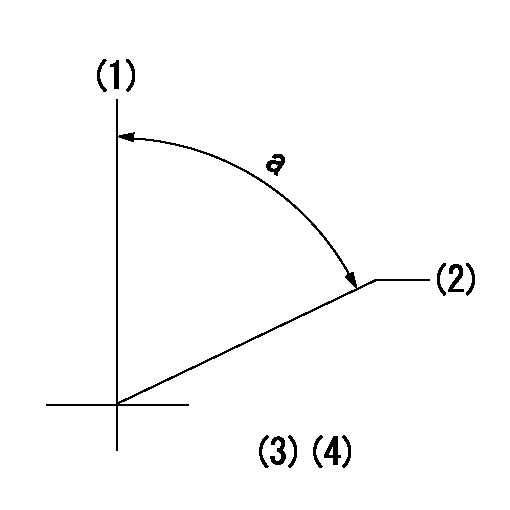
(1)Pump vertical direction
(2)Position of camshaft's key groove at No 1 cylinder's beginning of injection
(3)-
(4)-
----------
----------
a=(60deg)
----------
----------
a=(60deg)
Information:
The primary fuel filter should be cleaned, and the secondary (main) fuel filter element replaced, as follows: 1. When the fuel pressure gauge (if equipped) indicates low fuel pressure.2. When the engine has a noticable loss of power.3. Every 500 service hours of operation if the engine is not equipped with a fuel pressure gauge.
Fuel leaked or spilled onto hot surfaces or electrical components can cause a fire. Disconnect the battery (turn disconnect switch OFF) when changing fuel filters.
Do not fill fuel filters with fuel before installing them. Contaminated fuel will cause accelerated wear to fuel system parts.
Close the fuel supply valve at the tank before servicing filters. Open the valve after filter servicing is completed.Cleaning Primary Filter
Use all cleaning solutions with care.
1. Loosen the nut (1) on the filter cover and lower the filter case (3).2. Remove the element (2). Wash the cover and element in clean nonflammable solvent.3. Reinstall the element.4. Install the element and case onto the cover into the case.5. Tighten the bolt.Changing Secondary Filter
1. Unscrew filter element. Throw away the used element. 2. Make certain all of the used element seal is cleaned from the filter base. 3. Coat the seal of the new element with clean diesel fuel.4. Install the filter by hand. When the seal contacts the base, tighten 3/4 turn more.There are rotation marks 90° apart on the filter. Use these as a guide for proper tightening.5. Start the engine and check for leaks. If the engine will not start, prime the fuel system.
Fuel leaked or spilled onto hot surfaces or electrical components can cause a fire. Disconnect the battery (turn disconnect switch OFF) when changing fuel filters.
Do not fill fuel filters with fuel before installing them. Contaminated fuel will cause accelerated wear to fuel system parts.
Close the fuel supply valve at the tank before servicing filters. Open the valve after filter servicing is completed.Cleaning Primary Filter
Use all cleaning solutions with care.
1. Loosen the nut (1) on the filter cover and lower the filter case (3).2. Remove the element (2). Wash the cover and element in clean nonflammable solvent.3. Reinstall the element.4. Install the element and case onto the cover into the case.5. Tighten the bolt.Changing Secondary Filter
1. Unscrew filter element. Throw away the used element. 2. Make certain all of the used element seal is cleaned from the filter base. 3. Coat the seal of the new element with clean diesel fuel.4. Install the filter by hand. When the seal contacts the base, tighten 3/4 turn more.There are rotation marks 90° apart on the filter. Use these as a guide for proper tightening.5. Start the engine and check for leaks. If the engine will not start, prime the fuel system.