Information injection-pump assembly
BOSCH
9 400 615 367
9400615367
ZEXEL
101605-9081
1016059081
NISSAN-DIESEL
1679095019
1679095019
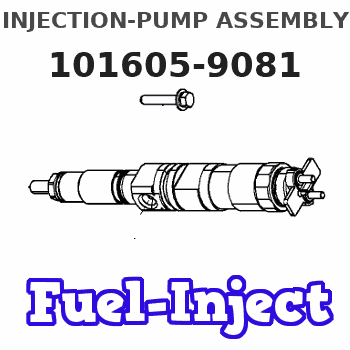
Rating:
Service parts 101605-9081 INJECTION-PUMP ASSEMBLY:
1.
_
5.
AUTOM. ADVANCE MECHANIS
7.
COUPLING PLATE
8.
_
9.
_
11.
Nozzle and Holder
16600-95015
12.
Open Pre:MPa(Kqf/cm2)
19.6{200}
15.
NOZZLE SET
Cross reference number
BOSCH
9 400 615 367
9400615367
ZEXEL
101605-9081
1016059081
NISSAN-DIESEL
1679095019
1679095019
Zexel num
Bosch num
Firm num
Name
9 400 615 367
1679095019 NISSAN-DIESEL
INJECTION-PUMP ASSEMBLY
NE6T * K 14BE PE6A PE
NE6T * K 14BE PE6A PE
Calibration Data:
Adjustment conditions
Test oil
1404 Test oil ISO4113 or {SAEJ967d}
1404 Test oil ISO4113 or {SAEJ967d}
Test oil temperature
degC
40
40
45
Nozzle and nozzle holder
105780-8140
Bosch type code
EF8511/9A
Nozzle
105780-0000
Bosch type code
DN12SD12T
Nozzle holder
105780-2080
Bosch type code
EF8511/9
Opening pressure
MPa
17.2
Opening pressure
kgf/cm2
175
Injection pipe
Outer diameter - inner diameter - length (mm) mm 6-2-600
Outer diameter - inner diameter - length (mm) mm 6-2-600
Overflow valve
131424-1520
Overflow valve opening pressure
kPa
157
123
191
Overflow valve opening pressure
kgf/cm2
1.6
1.25
1.95
Tester oil delivery pressure
kPa
157
157
157
Tester oil delivery pressure
kgf/cm2
1.6
1.6
1.6
Direction of rotation (viewed from drive side)
Right R
Right R
Injection timing adjustment
Direction of rotation (viewed from drive side)
Right R
Right R
Injection order
1-4-2-6-
3-5
Pre-stroke
mm
2.75
2.7
2.8
Beginning of injection position
Drive side NO.1
Drive side NO.1
Difference between angles 1
Cal 1-4 deg. 60 59.5 60.5
Cal 1-4 deg. 60 59.5 60.5
Difference between angles 2
Cyl.1-2 deg. 120 119.5 120.5
Cyl.1-2 deg. 120 119.5 120.5
Difference between angles 3
Cal 1-6 deg. 180 179.5 180.5
Cal 1-6 deg. 180 179.5 180.5
Difference between angles 4
Cal 1-3 deg. 240 239.5 240.5
Cal 1-3 deg. 240 239.5 240.5
Difference between angles 5
Cal 1-5 deg. 300 299.5 300.5
Cal 1-5 deg. 300 299.5 300.5
Injection quantity adjustment
Adjusting point
A
Rack position
10.9
Pump speed
r/min
700
700
700
Average injection quantity
mm3/st.
108
106.5
109.5
Max. variation between cylinders
%
0
-2
2
Basic
*
Fixing the lever
*
Boost pressure
kPa
58.7
58.7
Boost pressure
mmHg
440
440
Injection quantity adjustment_02
Adjusting point
B
Rack position
10.2
Pump speed
r/min
1100
1100
1100
Average injection quantity
mm3/st.
99.6
96.6
102.6
Fixing the lever
*
Boost pressure
kPa
58.7
58.7
Boost pressure
mmHg
440
440
Injection quantity adjustment_03
Adjusting point
C
Rack position
10.3
Pump speed
r/min
600
600
600
Average injection quantity
mm3/st.
91
87
95
Fixing the lever
*
Boost pressure
kPa
0
0
0
Boost pressure
mmHg
0
0
0
Injection quantity adjustment_04
Adjusting point
D
Rack position
6.9+-0.5
Pump speed
r/min
400
400
400
Average injection quantity
mm3/st.
12.6
11.1
14.1
Max. variation between cylinders
%
0
-10
10
Fixing the rack
*
Boost pressure
kPa
0
0
0
Boost pressure
mmHg
0
0
0
Boost compensator adjustment
Pump speed
r/min
600
600
600
Rack position
10.3
Boost pressure
kPa
26
23.3
28.7
Boost pressure
mmHg
195
175
215
Boost compensator adjustment_02
Pump speed
r/min
600
600
600
Rack position
(10.9)
Boost pressure
kPa
45.3
38.6
52
Boost pressure
mmHg
340
290
390
Test data Ex:
Governor adjustment
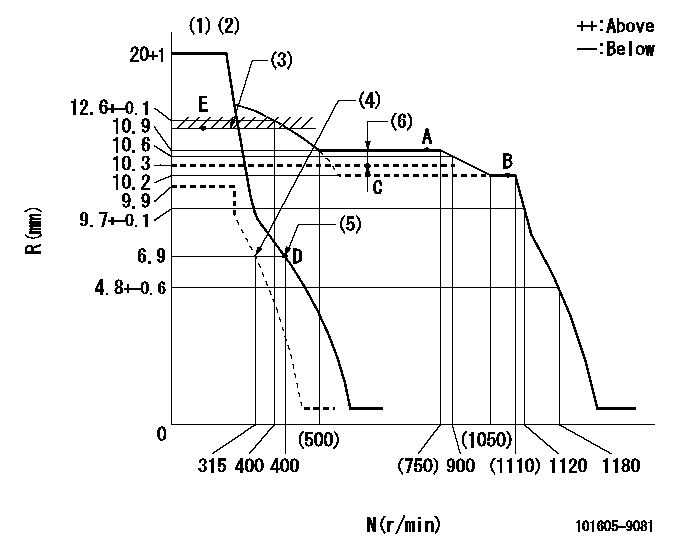
N:Pump speed
R:Rack position (mm)
(1)Target notch: K
(2)Tolerance for racks not indicated: +-0.05mm.
(3)Boost compensator excessive fuel lever at operation: L1 (at 0 boost pressure)
(4)Set idle sub-spring
(5)Main spring setting
(6)Boost compensator stroke: BCL
----------
K=12 L1=11.5+-0.2mm BCL=(0.6)mm
----------
----------
K=12 L1=11.5+-0.2mm BCL=(0.6)mm
----------
Speed control lever angle
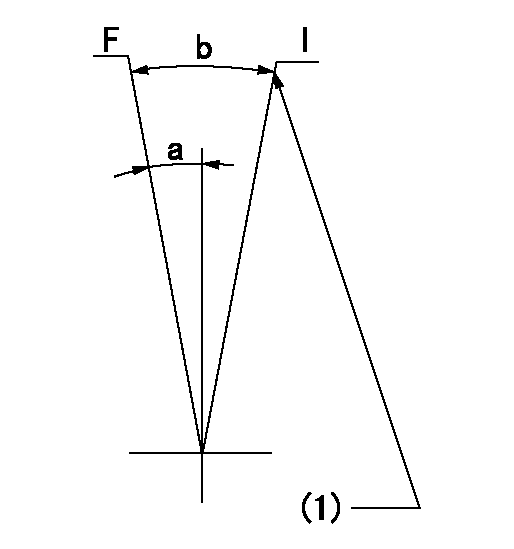
F:Full speed
I:Idle
(1)Stopper bolt setting
----------
----------
a=(7deg)+-5deg b=(21deg)+-5deg
----------
----------
a=(7deg)+-5deg b=(21deg)+-5deg
Stop lever angle

N:Pump normal
S:Stop the pump.
----------
----------
a=26.5deg+-5deg b=53deg+-5deg
----------
----------
a=26.5deg+-5deg b=53deg+-5deg
0000001101
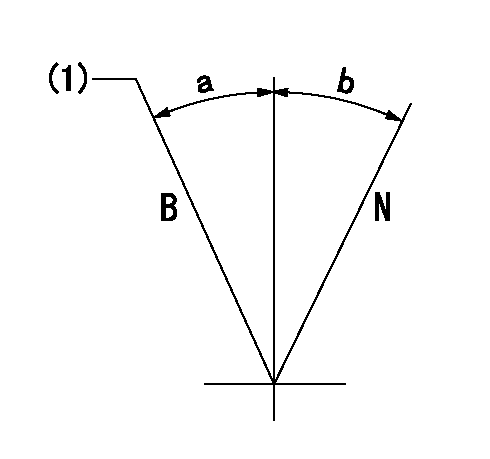
N:Normal
B:When boosted
(1)Rack position = aa at boost pressure 0.
----------
aa=11.5+-0.2mm
----------
a=(8deg) b=(15deg)
----------
aa=11.5+-0.2mm
----------
a=(8deg) b=(15deg)
Timing setting

(1)Pump vertical direction
(2)Coupling's key groove position at No 1 cylinder's beginning of injection
(3)B.T.D.C.: aa
(4)-
----------
aa=16deg
----------
a=(30deg)
----------
aa=16deg
----------
a=(30deg)
Information:
Most commercial antifreezes are formulated for gasoline engine applications and will, therefore, have high silicate content. ASTM D4985 antifreeze is a low silicate antifreeze and should be used if not using Caterpillar Antifreeze. The percentage of antifreeze and water should be determined by the amount of freeze protection required. Follow the instructions provided by the antifreeze supplier.When using any antifreeze (except Caterpillar Antifreeze) supplemental coolant additive is required at initial fill. Caterpillar or other manufacturer's products can be used as the supplemental coolant additive.Add 1 liter (1 U.S. quart) of liquid supplemental coolant additive for every 15 liter (4 U.S. gallon) so that the cooling system will have a three to six percent concentration of supplemental coolant additive.DO NOT mix Caterpillar Supplemental Coolant Additive (Conditioner) or supplemental coolant additive elements with the other products available; select a cooling system treatment and use it exclusively. If other than Caterpillar products are used as the supplemental coolant additive, follow the manufacturers' recommendation for cooling system treatment and test evaluation.Supplemental Coolant Additive (Conditioner or Inhibitor)
Never use coolant in Caterpillar engines without supplemental coolant additive regardless of antifreeze concentration.Caterpillar or other manufacturer's products can be used as the supplemental coolant additive. DO NOT mix Caterpillar Supplemental Coolant Additive (Conditioner) liquid or elements with the other commercial products available; select a cooling system treatment and use it exclusively.Excessive concentration of supplemental coolant additive can form deposits which may cause engine damage, reduce the engine's heat transfer characteristics and could also accelerate water pump seal wear.
The cooling system MUST contain supplemental coolant additives (conditioner or inhibitor) to control corrosion, cavitation and deposits. It is also necessary to prevent rust, scale, pitting and/or corrosion of engine parts contacted by coolant. The cooling system should be protected with a minimum of three percent concentration at all times, regardless of the concentration of antifreeze. Use supplemental coolant additive liquid OR an element (if equipped) to maintain a three to six percent concentration in the cooling system.Use the 8T5296 Test Kit to check and monitor the SCA concentration for antifreeze/water coolant mixture. The Caterpillar 8T5296 Test Kit checks for concentration of nitrates in the coolant solution. Some other manufacturers' supplemental coolant additive (SCA) are phosphate based and the 8T5296 Test Kit will NOT provide accurate results. Caterpillar recommends that their test kit be used to check coolant solution concentration.If other than Caterpillar products are used as the supplemental coolant additive, follow the manufacturers' recommendation for cooling system treatment and test evaluation. Commercial supplemental coolant additive products must contain silicates and a minimum of 70 gr/U.S. gallon (1200 ppm) nitrites.Caterpillar liquid supplemental coolant additive (Conditioner) is available through your Caterpillar dealer in quantities that follow. Pre-chargeCaterpillar Antifreeze DOES NOT require supplemental coolant additive added at initial fill, however additive is required on a maintenance basis. For engines equipped with supplemental coolant additive elements, the last MAINTENANCE element should not be replaced at FLUSH & FILL or Overhaul until the next oil change interval. Corrosion in raw (sea) water
Never use coolant in Caterpillar engines without supplemental coolant additive regardless of antifreeze concentration.Caterpillar or other manufacturer's products can be used as the supplemental coolant additive. DO NOT mix Caterpillar Supplemental Coolant Additive (Conditioner) liquid or elements with the other commercial products available; select a cooling system treatment and use it exclusively.Excessive concentration of supplemental coolant additive can form deposits which may cause engine damage, reduce the engine's heat transfer characteristics and could also accelerate water pump seal wear.
The cooling system MUST contain supplemental coolant additives (conditioner or inhibitor) to control corrosion, cavitation and deposits. It is also necessary to prevent rust, scale, pitting and/or corrosion of engine parts contacted by coolant. The cooling system should be protected with a minimum of three percent concentration at all times, regardless of the concentration of antifreeze. Use supplemental coolant additive liquid OR an element (if equipped) to maintain a three to six percent concentration in the cooling system.Use the 8T5296 Test Kit to check and monitor the SCA concentration for antifreeze/water coolant mixture. The Caterpillar 8T5296 Test Kit checks for concentration of nitrates in the coolant solution. Some other manufacturers' supplemental coolant additive (SCA) are phosphate based and the 8T5296 Test Kit will NOT provide accurate results. Caterpillar recommends that their test kit be used to check coolant solution concentration.If other than Caterpillar products are used as the supplemental coolant additive, follow the manufacturers' recommendation for cooling system treatment and test evaluation. Commercial supplemental coolant additive products must contain silicates and a minimum of 70 gr/U.S. gallon (1200 ppm) nitrites.Caterpillar liquid supplemental coolant additive (Conditioner) is available through your Caterpillar dealer in quantities that follow. Pre-chargeCaterpillar Antifreeze DOES NOT require supplemental coolant additive added at initial fill, however additive is required on a maintenance basis. For engines equipped with supplemental coolant additive elements, the last MAINTENANCE element should not be replaced at FLUSH & FILL or Overhaul until the next oil change interval. Corrosion in raw (sea) water