Information injection-pump assembly
BOSCH
9 400 615 364
9400615364
ZEXEL
101605-9010
1016059010
NISSAN-DIESEL
16700L9200
16700l9200
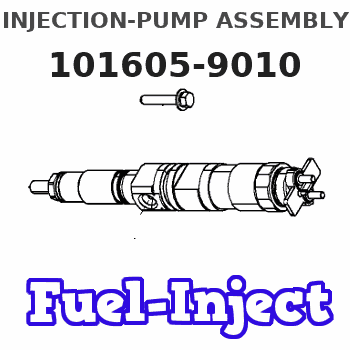
Rating:
Service parts 101605-9010 INJECTION-PUMP ASSEMBLY:
1.
_
5.
AUTOM. ADVANCE MECHANIS
6.
COUPLING PLATE
8.
_
9.
_
11.
Nozzle and Holder
16600-L9200
12.
Open Pre:MPa(Kqf/cm2)
19.6{200}
15.
NOZZLE SET
Cross reference number
BOSCH
9 400 615 364
9400615364
ZEXEL
101605-9010
1016059010
NISSAN-DIESEL
16700L9200
16700l9200
Zexel num
Bosch num
Firm num
Name
101605-9010
9 400 615 364
16700L9200 NISSAN-DIESEL
INJECTION-PUMP ASSEMBLY
FD6 K 14BE INJECTION PUMP ASSY PE6A PE
FD6 K 14BE INJECTION PUMP ASSY PE6A PE
Calibration Data:
Adjustment conditions
Test oil
1404 Test oil ISO4113 or {SAEJ967d}
1404 Test oil ISO4113 or {SAEJ967d}
Test oil temperature
degC
40
40
45
Nozzle and nozzle holder
105780-8140
Bosch type code
EF8511/9A
Nozzle
105780-0000
Bosch type code
DN12SD12T
Nozzle holder
105780-2080
Bosch type code
EF8511/9
Opening pressure
MPa
17.2
Opening pressure
kgf/cm2
175
Injection pipe
Outer diameter - inner diameter - length (mm) mm 6-2-600
Outer diameter - inner diameter - length (mm) mm 6-2-600
Overflow valve opening pressure
kPa
157
123
191
Overflow valve opening pressure
kgf/cm2
1.6
1.25
1.95
Tester oil delivery pressure
kPa
157
157
157
Tester oil delivery pressure
kgf/cm2
1.6
1.6
1.6
Direction of rotation (viewed from drive side)
Right R
Right R
Injection timing adjustment
Direction of rotation (viewed from drive side)
Right R
Right R
Injection order
1-4-2-6-
3-5
Pre-stroke
mm
3
2.95
3.05
Beginning of injection position
Drive side NO.1
Drive side NO.1
Difference between angles 1
Cal 1-4 deg. 60 59.5 60.5
Cal 1-4 deg. 60 59.5 60.5
Difference between angles 2
Cyl.1-2 deg. 120 119.5 120.5
Cyl.1-2 deg. 120 119.5 120.5
Difference between angles 3
Cal 1-6 deg. 180 179.5 180.5
Cal 1-6 deg. 180 179.5 180.5
Difference between angles 4
Cal 1-3 deg. 240 239.5 240.5
Cal 1-3 deg. 240 239.5 240.5
Difference between angles 5
Cal 1-5 deg. 300 299.5 300.5
Cal 1-5 deg. 300 299.5 300.5
Injection quantity adjustment
Adjusting point
-
Rack position
10.1
Pump speed
r/min
1000
1000
1000
Average injection quantity
mm3/st.
48.7
47.1
50.3
Max. variation between cylinders
%
0
-3.5
3.5
Basic
*
Fixing the rack
*
Standard for adjustment of the maximum variation between cylinders
*
Injection quantity adjustment_02
Adjusting point
-
Rack position
9.8+-0.5
Pump speed
r/min
335
335
335
Average injection quantity
mm3/st.
8
6.2
9.8
Max. variation between cylinders
%
0
-10
10
Fixing the rack
*
Standard for adjustment of the maximum variation between cylinders
*
Remarks
Adjust only variation between cylinders; adjust governor according to governor specifications.
Adjust only variation between cylinders; adjust governor according to governor specifications.
Injection quantity adjustment_03
Adjusting point
A
Rack position
R1(10.1)
Pump speed
r/min
1000
1000
1000
Average injection quantity
mm3/st.
48.7
47.7
49.7
Basic
*
Fixing the lever
*
Injection quantity adjustment_04
Adjusting point
I
Rack position
-
Pump speed
r/min
100
100
100
Average injection quantity
mm3/st.
62
62
72
Fixing the lever
*
Rack limit
*
Test data Ex:
Governor adjustment
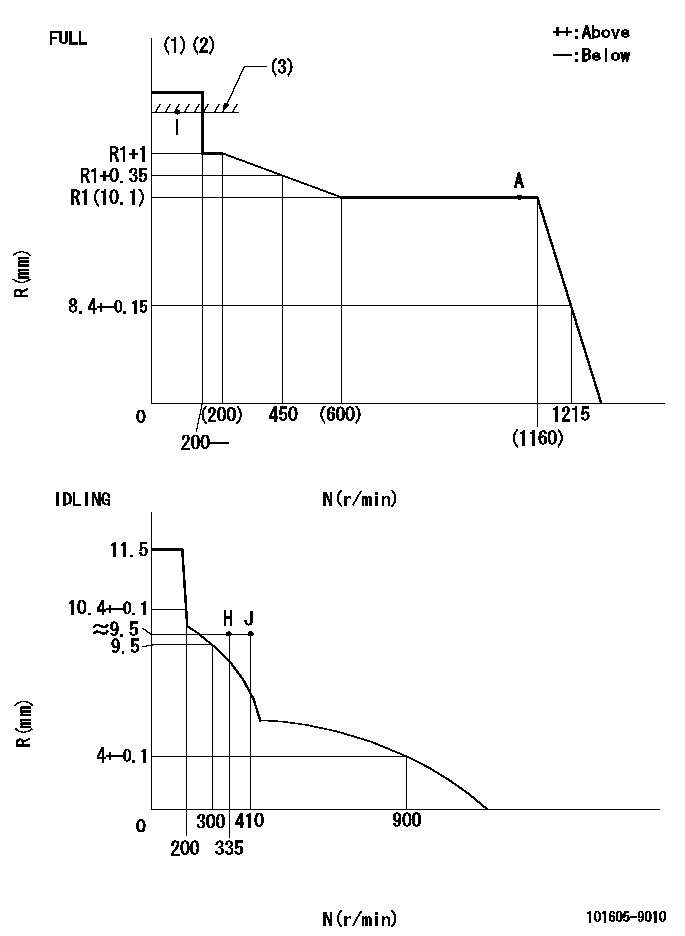
N:Pump speed
R:Rack position (mm)
(1)Torque cam stamping: T1
(2)Tolerance for racks not indicated: +-0.05mm.
(3)RACK LIMIT
----------
T1=G11
----------
----------
T1=G11
----------
Speed control lever angle
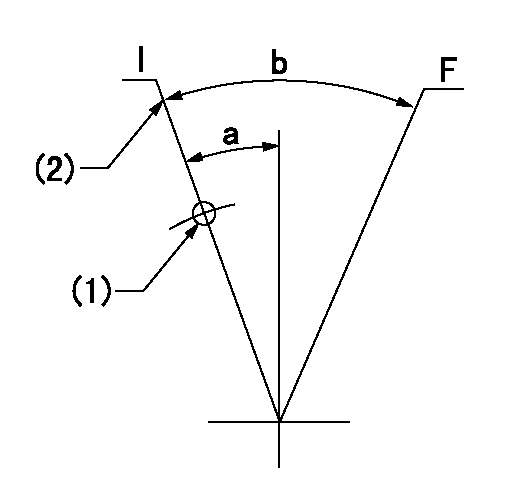
F:Full speed
I:Idle
(1)Use the pin at R = aa
(2)Stopper bolt set position 'H'
----------
aa=39mm
----------
a=17deg+-5deg b=34.5deg+-3deg
----------
aa=39mm
----------
a=17deg+-5deg b=34.5deg+-3deg
Stop lever angle

N:Pump normal
S:Stop the pump.
----------
----------
a=20deg+-5deg b=40deg+-5deg
----------
----------
a=20deg+-5deg b=40deg+-5deg
Timing setting
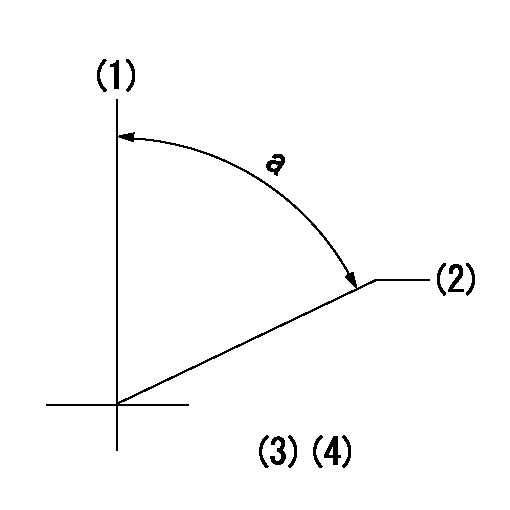
(1)Pump vertical direction
(2)Position of gear mark 'P' at No 1 cylinder's beginning of injection
(3)B.T.D.C.: aa
(4)-
----------
aa=18.5deg
----------
a=(60deg)
----------
aa=18.5deg
----------
a=(60deg)
Information:
Tachometer Drive
Use a short fiber grease, No. 2 Grade for most temperatures, or No. 0 or No. 1 for extremely low temperatures. Wipe surrounding area with a clean rag before removing plug. Remove plug. Install grease fitting. Apply two strokes of lubricant through the fitting. Remove grease fitting. Replace plug.Governor Control Cross Shaft Bearings (1673)
Engines Before 69D3625)
Use a short fiber grease No. 2 Grade for most temperatures, or No. 0 or No. 1 for extremely low temperatures. Apply 1 stroke of lubricant through fitting at each end of shaft.Valve Adjustment
1673C
Make valve adjustment with engine stopped and cold. Remove the flywheel timing cover and rotate flywheel in direction of engine rotation until "TC 1-6 cyl" mark aligns with timing pointer. Remove valve cover and observe position of valves to determine if No. 1 or No. 6 piston is on compression stroke. Both the inlet and exhaust valves will be closed on compression stroke.1. With No. 1 piston at TDC on compression, check lash on exhaust valves for cylinders 1, 3 and 5, and inlet valves for cylinders 1, 2 and 4.2. To adjust, loosen valve adjusting locknut and turn adjusting screw to allow feeler gauge to pass between top of valve stem and the valve rocker arm.3. Set lash at .015" (0.38 mm) for inlet and .025" (0.63 mm) for exhaust valves.4. Tighten adjusting screw locknut and check lash clearance.5. Turn flywheel 360° in direction of engine rotation. Align flywheel timing mark with pointer. No. 6 cylinder will be at TDC compression stroke (valves closed).6. Check lash on exhaust valves for cylinders 2, 4 and 6, and inlet valves for cylinders 3, 5 and 6. Adjust valves if necessary.1674
Make valve lash adjustment with engine stopped. TDC of the No. 1 piston on the compression stroke is the reference point. The No. 1 piston will be at TDC when the No. 1 and No. 6 flywheel timing mark aligns with the timing pointer. Compression stroke is when all the No. 1 piston valves are closed.1. With No. 1 piston at TDC compression stroke, adjust lash on 1, 3 and 5 exhaust and 1, 2 and 4 inlet valves.2. Turn adjusting screw counterclockwise 2 clicks or more to provide clearance between rocker assembly and valve.3. Turn adjusting screw clockwise to obtain zero lash. There should be no free rocker movement or adjusting screw button lateral movement. The adjusting screw button can still be rotated by finger pressure even when it is in contact with valve stem and clearance is zero. Turning the adjusting screw clockwise beyond this point will force the valve off its seat, and final lash setting will be incorrect.4. To adjust, turn adjustment screw counterclockwise 10 clicks (.020") (0.51 mm) for the exhaust valves and 4 clicks (.008") (0.20 mm) for the inlet valves. (One click is equal to .002") (0.05 mm).5. Turn crankshaft 360° clockwise, (direction of normal rotation) viewing from front. Align flywheel timing mark with timing pointer. a) Adjust 2, 4 and 6 exhaust
Use a short fiber grease, No. 2 Grade for most temperatures, or No. 0 or No. 1 for extremely low temperatures. Wipe surrounding area with a clean rag before removing plug. Remove plug. Install grease fitting. Apply two strokes of lubricant through the fitting. Remove grease fitting. Replace plug.Governor Control Cross Shaft Bearings (1673)
Engines Before 69D3625)
Use a short fiber grease No. 2 Grade for most temperatures, or No. 0 or No. 1 for extremely low temperatures. Apply 1 stroke of lubricant through fitting at each end of shaft.Valve Adjustment
1673C
Make valve adjustment with engine stopped and cold. Remove the flywheel timing cover and rotate flywheel in direction of engine rotation until "TC 1-6 cyl" mark aligns with timing pointer. Remove valve cover and observe position of valves to determine if No. 1 or No. 6 piston is on compression stroke. Both the inlet and exhaust valves will be closed on compression stroke.1. With No. 1 piston at TDC on compression, check lash on exhaust valves for cylinders 1, 3 and 5, and inlet valves for cylinders 1, 2 and 4.2. To adjust, loosen valve adjusting locknut and turn adjusting screw to allow feeler gauge to pass between top of valve stem and the valve rocker arm.3. Set lash at .015" (0.38 mm) for inlet and .025" (0.63 mm) for exhaust valves.4. Tighten adjusting screw locknut and check lash clearance.5. Turn flywheel 360° in direction of engine rotation. Align flywheel timing mark with pointer. No. 6 cylinder will be at TDC compression stroke (valves closed).6. Check lash on exhaust valves for cylinders 2, 4 and 6, and inlet valves for cylinders 3, 5 and 6. Adjust valves if necessary.1674
Make valve lash adjustment with engine stopped. TDC of the No. 1 piston on the compression stroke is the reference point. The No. 1 piston will be at TDC when the No. 1 and No. 6 flywheel timing mark aligns with the timing pointer. Compression stroke is when all the No. 1 piston valves are closed.1. With No. 1 piston at TDC compression stroke, adjust lash on 1, 3 and 5 exhaust and 1, 2 and 4 inlet valves.2. Turn adjusting screw counterclockwise 2 clicks or more to provide clearance between rocker assembly and valve.3. Turn adjusting screw clockwise to obtain zero lash. There should be no free rocker movement or adjusting screw button lateral movement. The adjusting screw button can still be rotated by finger pressure even when it is in contact with valve stem and clearance is zero. Turning the adjusting screw clockwise beyond this point will force the valve off its seat, and final lash setting will be incorrect.4. To adjust, turn adjustment screw counterclockwise 10 clicks (.020") (0.51 mm) for the exhaust valves and 4 clicks (.008") (0.20 mm) for the inlet valves. (One click is equal to .002") (0.05 mm).5. Turn crankshaft 360° clockwise, (direction of normal rotation) viewing from front. Align flywheel timing mark with timing pointer. a) Adjust 2, 4 and 6 exhaust
Have questions with 101605-9010?
Group cross 101605-9010 ZEXEL
Daewoo
Nissan-Diesel
101605-9010
9 400 615 364
16700L9200
INJECTION-PUMP ASSEMBLY
FD6
FD6