Information injection-pump assembly
BOSCH
9 400 615 361
9400615361
ZEXEL
101605-3981
1016053981
KOMATSU
6138721153
6138721153
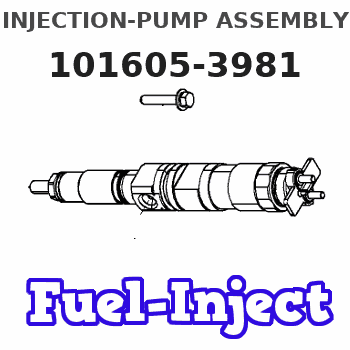
Rating:
Service parts 101605-3981 INJECTION-PUMP ASSEMBLY:
1.
_
5.
AUTOM. ADVANCE MECHANIS
7.
COUPLING PLATE
8.
_
9.
_
11.
Nozzle and Holder
6138-12-3300
12.
Open Pre:MPa(Kqf/cm2)
24.5{250}
15.
NOZZLE SET
Cross reference number
BOSCH
9 400 615 361
9400615361
ZEXEL
101605-3981
1016053981
KOMATSU
6138721153
6138721153
Zexel num
Bosch num
Firm num
Name
101605-3981
9 400 615 361
6138721153 KOMATSU
INJECTION-PUMP ASSEMBLY
S6D110 K 14BF INJECTION PUMP ASSY PE6AD PE
S6D110 K 14BF INJECTION PUMP ASSY PE6AD PE
Calibration Data:
Adjustment conditions
Test oil
1404 Test oil ISO4113 or {SAEJ967d}
1404 Test oil ISO4113 or {SAEJ967d}
Test oil temperature
degC
40
40
45
Nozzle and nozzle holder
105780-8140
Bosch type code
EF8511/9A
Nozzle
105780-0000
Bosch type code
DN12SD12T
Nozzle holder
105780-2080
Bosch type code
EF8511/9
Opening pressure
MPa
17.2
Opening pressure
kgf/cm2
175
Injection pipe
Outer diameter - inner diameter - length (mm) mm 6-2-600
Outer diameter - inner diameter - length (mm) mm 6-2-600
Tester oil delivery pressure
kPa
157
157
157
Tester oil delivery pressure
kgf/cm2
1.6
1.6
1.6
Direction of rotation (viewed from drive side)
Right R
Right R
Injection timing adjustment
Direction of rotation (viewed from drive side)
Right R
Right R
Injection order
1-5-3-6-
2-4
Pre-stroke
mm
4
3.95
4.05
Beginning of injection position
Drive side NO.1
Drive side NO.1
Difference between angles 1
Cal 1-5 deg. 60 59.5 60.5
Cal 1-5 deg. 60 59.5 60.5
Difference between angles 2
Cal 1-3 deg. 120 119.5 120.5
Cal 1-3 deg. 120 119.5 120.5
Difference between angles 3
Cal 1-6 deg. 180 179.5 180.5
Cal 1-6 deg. 180 179.5 180.5
Difference between angles 4
Cyl.1-2 deg. 240 239.5 240.5
Cyl.1-2 deg. 240 239.5 240.5
Difference between angles 5
Cal 1-4 deg. 300 299.5 300.5
Cal 1-4 deg. 300 299.5 300.5
Injection quantity adjustment
Adjusting point
A
Rack position
10.5
Pump speed
r/min
1100
1100
1100
Average injection quantity
mm3/st.
81.8
80.8
82.8
Max. variation between cylinders
%
0
-2
2
Basic
*
Fixing the lever
*
Boost pressure
kPa
40
40
Boost pressure
mmHg
300
300
Injection quantity adjustment_02
Adjusting point
C
Rack position
8.5+-0.5
Pump speed
r/min
380
380
380
Average injection quantity
mm3/st.
22.7
21.5
23.9
Max. variation between cylinders
%
0
-10
10
Fixing the rack
*
Boost pressure
kPa
0
0
0
Boost pressure
mmHg
0
0
0
Boost compensator adjustment
Pump speed
r/min
650
650
650
Rack position
10.75
Boost pressure
kPa
13.3
9.3
17.3
Boost pressure
mmHg
100
70
130
Boost compensator adjustment_02
Pump speed
r/min
650
650
650
Rack position
11.25
Boost pressure
kPa
26.7
26.7
26.7
Boost pressure
mmHg
200
200
200
Test data Ex:
Governor adjustment

N:Pump speed
R:Rack position (mm)
(1)Target notch: K
(2)Boost compensator stroke
(3)Rack difference between N = N1 and N = N2
----------
K=17 N1=1100r/min N2=750r/min
----------
----------
K=17 N1=1100r/min N2=750r/min
----------
Speed control lever angle
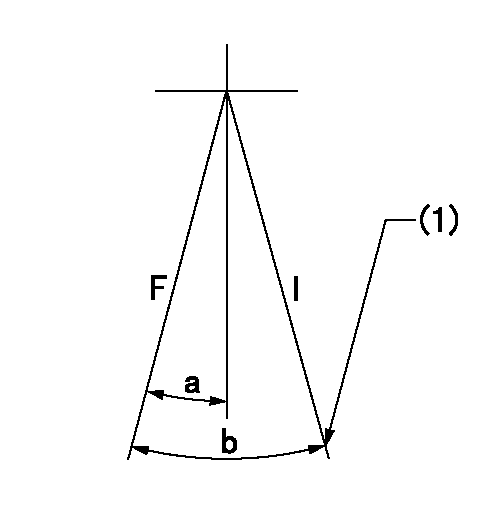
F:Full speed
I:Idle
(1)Stopper bolt setting
----------
----------
a=10deg+-5deg b=22deg+-5deg
----------
----------
a=10deg+-5deg b=22deg+-5deg
Stop lever angle

N:Pump normal
S:Stop the pump.
(1)Set the stopper bolt at speed = aa and rack position = bb (seal for delivery after setting the stopper bolt).
----------
aa=0r/min bb=1-0.2mm
----------
a=42.5deg+-5deg b=(55deg)
----------
aa=0r/min bb=1-0.2mm
----------
a=42.5deg+-5deg b=(55deg)
Timing setting

(1)Pump vertical direction
(2)Coupling's key groove position at No 1 cylinder's beginning of injection
(3)-
(4)-
----------
----------
a=(0deg)
----------
----------
a=(0deg)
Information:
Storage Procedure
1. Clean the outside of the engine and repaint areas that have paint damage with a good quality paint.2. Remove the batteries and use them in some other place or put them in storage where they can be checked and electrically charged again when needed. If the batteries are not removed, wash the tops. Put an electrical charge to the battery to a specific gravity of 1.275. Disconnect the battery terminals. Put a plastic cover over the battery.3. Loosen all fan, alternator belts, etc. Attach a tag to indicate what work has been done.4. Put a waterproof cover over engines with enclosures stored outdoors. Make the cover tight, but loose enough to allow air to circulate around the engine to prevent damage to exposed metal parts from condensation. Remove the waterproof cover every two or three months and check the engine for corrosion. If the engine has signs of corrosion at the check period, follow the protection procedure again. To operate the engine, it is not necessary to remove the preservative oil mixture. If a compartment under protection of VCI vapors is opened, put more VCI mixture in to make up for the vapor loss. Install all covers and/or put tape over all openings, air intake, exhaust openings, flywheel housing, crankcase breathers, dipstick tubes, etc. Make sure all covers are air tight and weatherproof. Use a waterproof, weather resistant tape.5. Put lubricant on all points given in the Lubrication and Maintenance Chart.6. Put a heavy amount of multipurpose grease on all outside parts that move; rod threads, ball joints, linkage, etc.7. Oil and oil filter elements used less than 50 hours in the engine do not need to be changed. (Otherwise, change the oil, filling the engine to the "add oil" mark on the dipstick.) Add 3% to 4% of VCI oil per engine volume. If the engine is drained, install a mixture of 50% VCI oil and 50% engine oil in the crankcase and in all lubricating oil compartments at the rate of one part VCI oil mixture per fifteen parts of compartment capacity at full level. If possible, operate the engine three to five minutes. Put tape over all openings to seal VCI vapors in the engine. If necessary, drain some lubricant to add to the mixture.8. Remove any dirt from the air cleaner. Check all seals and gaskets.9. Remove the air filter elements. Turn the engine at cranking speed with throttle control in fuel OFF position, remove pressure plug for boost pressure and use a sprayer to add a mixture of 50% VCI oil and 50% engine oil. Minimum application rate is 5.5 milliliters per liter (3 oz. per
1. Clean the outside of the engine and repaint areas that have paint damage with a good quality paint.2. Remove the batteries and use them in some other place or put them in storage where they can be checked and electrically charged again when needed. If the batteries are not removed, wash the tops. Put an electrical charge to the battery to a specific gravity of 1.275. Disconnect the battery terminals. Put a plastic cover over the battery.3. Loosen all fan, alternator belts, etc. Attach a tag to indicate what work has been done.4. Put a waterproof cover over engines with enclosures stored outdoors. Make the cover tight, but loose enough to allow air to circulate around the engine to prevent damage to exposed metal parts from condensation. Remove the waterproof cover every two or three months and check the engine for corrosion. If the engine has signs of corrosion at the check period, follow the protection procedure again. To operate the engine, it is not necessary to remove the preservative oil mixture. If a compartment under protection of VCI vapors is opened, put more VCI mixture in to make up for the vapor loss. Install all covers and/or put tape over all openings, air intake, exhaust openings, flywheel housing, crankcase breathers, dipstick tubes, etc. Make sure all covers are air tight and weatherproof. Use a waterproof, weather resistant tape.5. Put lubricant on all points given in the Lubrication and Maintenance Chart.6. Put a heavy amount of multipurpose grease on all outside parts that move; rod threads, ball joints, linkage, etc.7. Oil and oil filter elements used less than 50 hours in the engine do not need to be changed. (Otherwise, change the oil, filling the engine to the "add oil" mark on the dipstick.) Add 3% to 4% of VCI oil per engine volume. If the engine is drained, install a mixture of 50% VCI oil and 50% engine oil in the crankcase and in all lubricating oil compartments at the rate of one part VCI oil mixture per fifteen parts of compartment capacity at full level. If possible, operate the engine three to five minutes. Put tape over all openings to seal VCI vapors in the engine. If necessary, drain some lubricant to add to the mixture.8. Remove any dirt from the air cleaner. Check all seals and gaskets.9. Remove the air filter elements. Turn the engine at cranking speed with throttle control in fuel OFF position, remove pressure plug for boost pressure and use a sprayer to add a mixture of 50% VCI oil and 50% engine oil. Minimum application rate is 5.5 milliliters per liter (3 oz. per
Have questions with 101605-3981?
Group cross 101605-3981 ZEXEL
Komatsu
Komatsu
101605-3981
9 400 615 361
6138721153
INJECTION-PUMP ASSEMBLY
S6D110
S6D110