Information injection-pump assembly
BOSCH
9 400 615 360
9400615360
ZEXEL
101605-3961
1016053961
KOMATSU
6221711810
6221711810
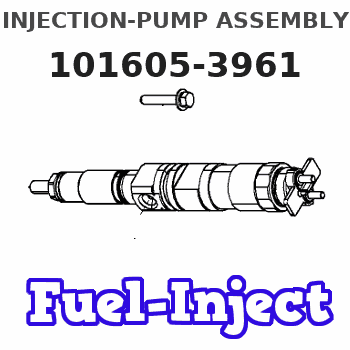
Rating:
Service parts 101605-3961 INJECTION-PUMP ASSEMBLY:
1.
_
5.
AUTOM. ADVANCE MECHANIS
6.
COUPLING PLATE
7.
COUPLING PLATE
8.
_
9.
_
11.
Nozzle and Holder
6221-11-3100
12.
Open Pre:MPa(Kqf/cm2)
23.0{235}
15.
NOZZLE SET
Cross reference number
BOSCH
9 400 615 360
9400615360
ZEXEL
101605-3961
1016053961
KOMATSU
6221711810
6221711810
Zexel num
Bosch num
Firm num
Name
101605-3961
9 400 615 360
6221711810 KOMATSU
INJECTION-PUMP ASSEMBLY
S6D108 K 14BF INJECTION PUMP ASSY PE6AD PE
S6D108 K 14BF INJECTION PUMP ASSY PE6AD PE
Calibration Data:
Adjustment conditions
Test oil
1404 Test oil ISO4113 or {SAEJ967d}
1404 Test oil ISO4113 or {SAEJ967d}
Test oil temperature
degC
40
40
45
Nozzle and nozzle holder
105780-8140
Bosch type code
EF8511/9A
Nozzle
105780-0000
Bosch type code
DN12SD12T
Nozzle holder
105780-2080
Bosch type code
EF8511/9
Opening pressure
MPa
17.2
Opening pressure
kgf/cm2
175
Injection pipe
Outer diameter - inner diameter - length (mm) mm 6-2-600
Outer diameter - inner diameter - length (mm) mm 6-2-600
Overflow valve opening pressure
kPa
157
123
191
Overflow valve opening pressure
kgf/cm2
1.6
1.25
1.95
Tester oil delivery pressure
kPa
157
157
157
Tester oil delivery pressure
kgf/cm2
1.6
1.6
1.6
Direction of rotation (viewed from drive side)
Right R
Right R
Injection timing adjustment
Direction of rotation (viewed from drive side)
Right R
Right R
Injection order
1-5-3-6-
2-4
Pre-stroke
mm
3.6
3.55
3.65
Beginning of injection position
Drive side NO.1
Drive side NO.1
Difference between angles 1
Cal 1-5 deg. 60 59.5 60.5
Cal 1-5 deg. 60 59.5 60.5
Difference between angles 2
Cal 1-3 deg. 120 119.5 120.5
Cal 1-3 deg. 120 119.5 120.5
Difference between angles 3
Cal 1-6 deg. 180 179.5 180.5
Cal 1-6 deg. 180 179.5 180.5
Difference between angles 4
Cyl.1-2 deg. 240 239.5 240.5
Cyl.1-2 deg. 240 239.5 240.5
Difference between angles 5
Cal 1-4 deg. 300 299.5 300.5
Cal 1-4 deg. 300 299.5 300.5
Injection quantity adjustment
Adjusting point
A
Rack position
10.2
Pump speed
r/min
1050
1050
1050
Average injection quantity
mm3/st.
88.5
87.5
89.5
Max. variation between cylinders
%
0
-2
2
Basic
*
Fixing the lever
*
Boost pressure
kPa
45.3
45.3
Boost pressure
mmHg
340
340
Injection quantity adjustment_02
Adjusting point
C
Rack position
6+-0.5
Pump speed
r/min
350
350
350
Average injection quantity
mm3/st.
14.4
13.2
15.6
Max. variation between cylinders
%
0
-10
10
Fixing the rack
*
Boost pressure
kPa
0
0
0
Boost pressure
mmHg
0
0
0
Boost compensator adjustment
Pump speed
r/min
700
700
700
Rack position
9.5
Boost pressure
kPa
10.7
8
13.4
Boost pressure
mmHg
80
60
100
Boost compensator adjustment_02
Pump speed
r/min
700
700
700
Rack position
10.5
Boost pressure
kPa
32
32
32
Boost pressure
mmHg
240
240
240
Test data Ex:
Governor adjustment
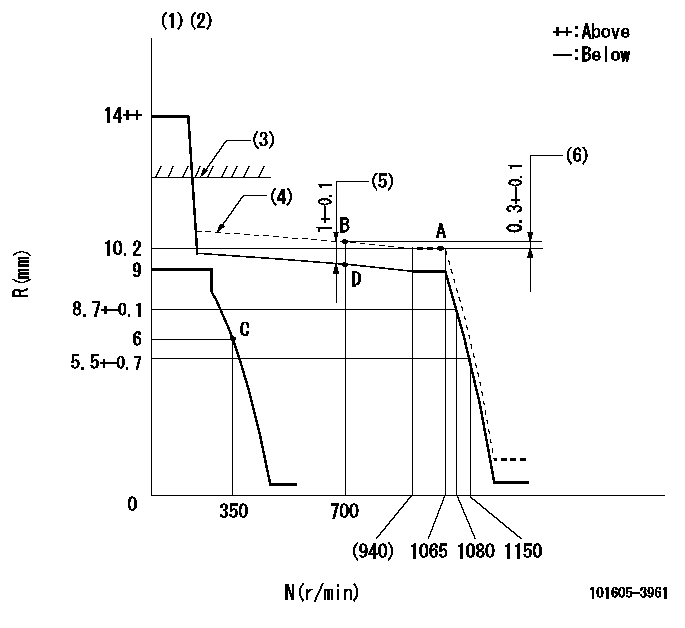
N:Pump speed
R:Rack position (mm)
(1)Target notch: K
(2)Tolerance for racks not indicated: +-0.05mm.
(3)RACK LIMIT: RAL
(4)No set force
(5)Boost compensator stroke
(6)Rack difference from N = N1
----------
K=8 RAL=13+0.2mm N1=1050r/min
----------
----------
K=8 RAL=13+0.2mm N1=1050r/min
----------
Speed control lever angle
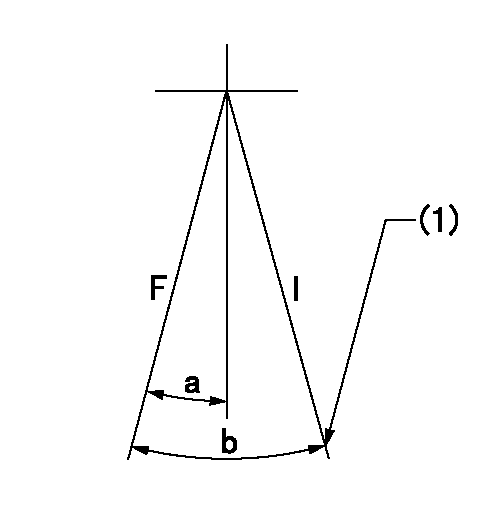
F:Full speed
I:Idle
(1)Stopper bolt setting
----------
----------
a=2deg+-5deg b=24deg+-5deg
----------
----------
a=2deg+-5deg b=24deg+-5deg
Stop lever angle
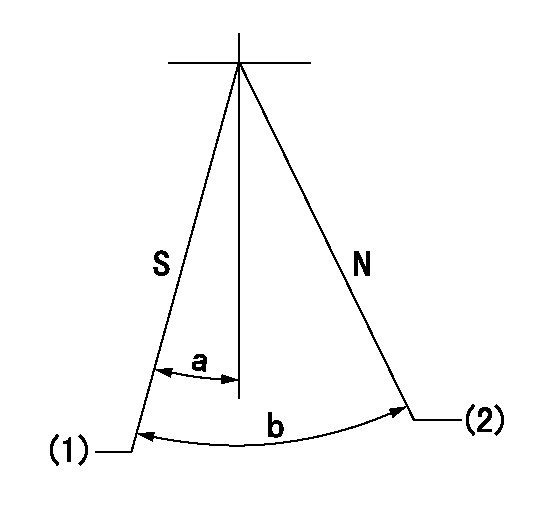
N:Pump normal
S:Stop the pump.
(1)Speed = aa, rack position = bb (sealed at shipping)
(2)Normal
----------
aa=0r/min bb=1-0.2mm
----------
a=27.5deg+-5deg b=55deg+-5deg
----------
aa=0r/min bb=1-0.2mm
----------
a=27.5deg+-5deg b=55deg+-5deg
Timing setting

(1)Pump vertical direction
(2)Position of camshaft's key groove at No 1 cylinder's beginning of injection
(3)-
(4)-
----------
----------
a=(50deg)
----------
----------
a=(50deg)
Information:
INSTALLING ENGINE TURNING TOOLBoth the inlet and exhaust valves will be closed on compression stroke. First check the bridge adjustment and then the valve lash adjustment. Bridge Adjustment
Check the bridge adjustment screw and locknut for tightness. If the adjusting screw and locknut are tight, proceed with the valve lash adjustment. If the bridge adjusting screw can be turned with a screwdriver without holding the locknut, the bridge requires adjustment. The bridge adjustment must be made before the valve lash is checked for proper clearance.Make bridge adjustment as follows:1. Back off adjusting screw several turns (counterclockwise) making sure it is not in contact with the valve stem.2. Firmly press straight down on the rocker arm above point of contact with bridge.
ADJUSTING BRIDGE3. Turn the adjusting screw clockwise until contact is made with the valve stem, then turn the adjusting screw an additional 30° or 1/12 turn (1/2 the distance between the two points on the locknut).4. Hold the adjusting screw in this position and tighten the locknut to 20 lb. ft. (27.2 N m).
TIGHTENING ADJUSTING SCREW LOCKNUTValve Lash Adjustment
To prevent possible injury, do not use the starter motor to turn the flywheel.Hot engine components can cause burns. Allow additional time for the engine to cool before measuring valve clearance.
Measure the valve lash with the engine stopped. To obtain an accurate measurement, allow at least 20 minutes for the valves to cool to cylinder head and block temperature.
If the valve clearance is within 0.08 mm (.003 in) of the nominal clearance given, adjustment is not required. If the clearance is not within these limits, set the clearance as given in the chart. After checking the bridge adjustment, make the valve lash adjustment.1. With No. 1 piston at TDC on compression, check valve lash between the bridge and rocker arm. See chart for cylinder and valve adjusting sequence.2. To adjust, loosen valve adjusting locknut and turn adjusting screw to allow feeler gauge to pass between top of bridge and the valve rocker arm. Set the inlet valve lash at .015" (0.38 mm) and exhaust valve lash at .030" (0.76 mm). 3. After proper adjustment, tighten the adjusting screw locknut to 22 lb. ft. (29.9 N m) and recheck lash clearance. 4. Turn flywheel 360° in direction of engine rotation. Align flywheel timing bolt with the timing hole in the flywheel. 3408-No. 6 Cylinder will be at TDC on compression stroke (all valves closed)3412-No. 11 Cylinder will be at TDC on compression stroke (all valves closed).5. Check lash and adjust as necessary on all remaining valves, see valve adjusting sequence chart.6. Tighten locknut and recheck lash clearance.7. Remove engine turning tool and install timing access cover, timing bolt and plug.Check Valve Rotation: After checking valve lash and before the valve covers are installed, check the valves for rotation.1. Mark a line on each valve retainer.2. Start the engine and run at low idle.3. Watch the line mark on each valve retainer. Each valve retainer should turn slightly each time the valve
Have questions with 101605-3961?
Group cross 101605-3961 ZEXEL
Komatsu
101605-3961
9 400 615 360
6221711810
INJECTION-PUMP ASSEMBLY
S6D108
S6D108