Information injection-pump assembly
BOSCH
9 400 610 167
9400610167
ZEXEL
101605-3120
1016053120
KOMATSU
6137721120
6137721120
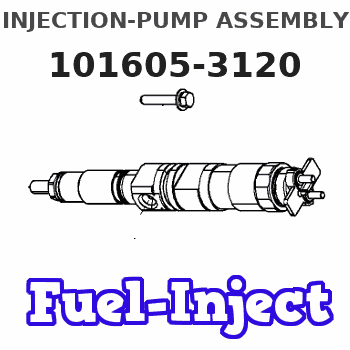
Rating:
Service parts 101605-3120 INJECTION-PUMP ASSEMBLY:
1.
_
5.
AUTOM. ADVANCE MECHANIS
7.
COUPLING PLATE
8.
_
9.
_
11.
Nozzle and Holder
6137-12-3200
12.
Open Pre:MPa(Kqf/cm2)
22.1{225}
15.
NOZZLE SET
Include in #1:
101605-3120
as INJECTION-PUMP ASSEMBLY
Include in #2:
104746-1142
as _
Cross reference number
BOSCH
9 400 610 167
9400610167
ZEXEL
101605-3120
1016053120
KOMATSU
6137721120
6137721120
Zexel num
Bosch num
Firm num
Name
101605-3120
9 400 610 167
6137721120 KOMATSU
INJECTION-PUMP ASSEMBLY
S6D105 K 14BE INJECTION PUMP ASSY PE6A PE
S6D105 K 14BE INJECTION PUMP ASSY PE6A PE
Calibration Data:
Adjustment conditions
Test oil
1404 Test oil ISO4113 or {SAEJ967d}
1404 Test oil ISO4113 or {SAEJ967d}
Test oil temperature
degC
40
40
45
Nozzle and nozzle holder
105780-8140
Bosch type code
EF8511/9A
Nozzle
105780-0000
Bosch type code
DN12SD12T
Nozzle holder
105780-2080
Bosch type code
EF8511/9
Opening pressure
MPa
17.2
Opening pressure
kgf/cm2
175
Injection pipe
Outer diameter - inner diameter - length (mm) mm 6-2-600
Outer diameter - inner diameter - length (mm) mm 6-2-600
Tester oil delivery pressure
kPa
157
157
157
Tester oil delivery pressure
kgf/cm2
1.6
1.6
1.6
Direction of rotation (viewed from drive side)
Right R
Right R
Injection timing adjustment
Direction of rotation (viewed from drive side)
Right R
Right R
Injection order
1-5-3-6-
2-4
Pre-stroke
mm
3.3
3.25
3.35
Beginning of injection position
Drive side NO.1
Drive side NO.1
Difference between angles 1
Cal 1-5 deg. 60 59.5 60.5
Cal 1-5 deg. 60 59.5 60.5
Difference between angles 2
Cal 1-3 deg. 120 119.5 120.5
Cal 1-3 deg. 120 119.5 120.5
Difference between angles 3
Cal 1-6 deg. 180 179.5 180.5
Cal 1-6 deg. 180 179.5 180.5
Difference between angles 4
Cyl.1-2 deg. 240 239.5 240.5
Cyl.1-2 deg. 240 239.5 240.5
Difference between angles 5
Cal 1-4 deg. 300 299.5 300.5
Cal 1-4 deg. 300 299.5 300.5
Injection quantity adjustment
Adjusting point
A
Rack position
10.5
Pump speed
r/min
1150
1150
1150
Average injection quantity
mm3/st.
70.5
69.5
71.5
Max. variation between cylinders
%
0
-2
2
Basic
*
Fixing the lever
*
Injection quantity adjustment_02
Adjusting point
B
Rack position
8+-0.5
Pump speed
r/min
365
365
365
Average injection quantity
mm3/st.
9.6
8.1
11.1
Max. variation between cylinders
%
0
-10
10
Fixing the rack
*
Test data Ex:
Governor adjustment
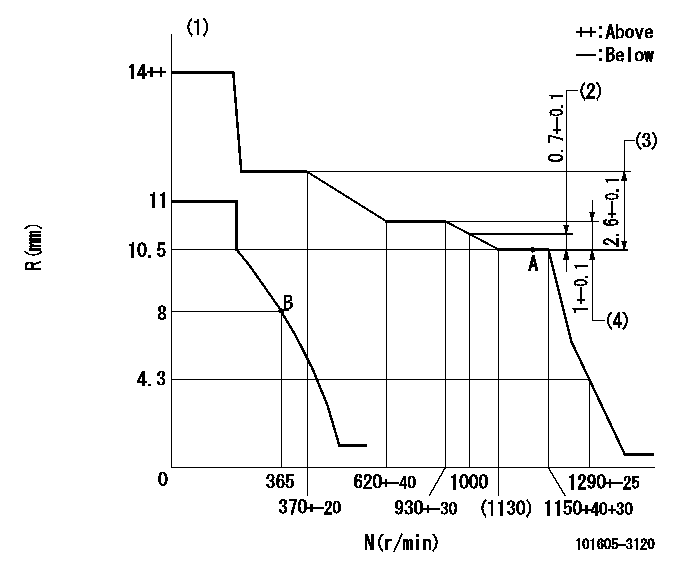
N:Pump speed
R:Rack position (mm)
(1)Target notch: K
(2)Rack difference between N = N1 and N = N2
(3)Rack difference between N = N3 and N = N4
(4)Rack difference between N = N5 and N = N6.
----------
K=10 N1=1150r/min N2=1000r/min N3=1150r/min N4=350r/min N5=1150r/min N6=800r/min
----------
----------
K=10 N1=1150r/min N2=1000r/min N3=1150r/min N4=350r/min N5=1150r/min N6=800r/min
----------
Speed control lever angle
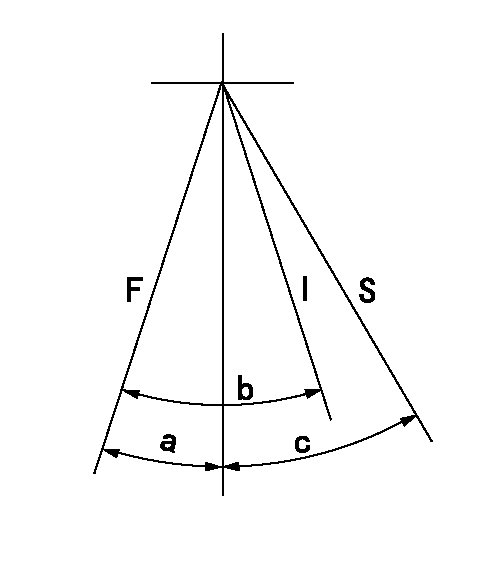
F:Full speed
I:Idle
S:Stop
----------
----------
a=(5deg)+-5deg b=(25deg)+-5deg c=32deg+-3deg
----------
----------
a=(5deg)+-5deg b=(25deg)+-5deg c=32deg+-3deg
0000001501 LEVER

(F) P/N: Part number of the shim
L1:Thickness (mm)
1. Adjustment of the control lever
(1)Perform idling with the control lever (A) contacting the pushrod (B). At this time, confirm that the spring (C) is not compressed by control lever (A)'s operating torque.
(2)To set the stop position, compress spring (C) using the control lever (A) and adjust the rack so that it contacts the guide screw (D) at position L2. Then, set and fix using the lock nut (E). Adjust the rack position L2 at this time using the shim (F).
(3)Confirm that the control lever (A) returns to the idling position when pulled in the stop direction and then released.
----------
L2=0.2~2mm
----------
----------
L2=0.2~2mm
----------
Information:
Start By:
Do not let the tops of the nozzles turn while the fuel lines are loosened. The nozzles will be damaged if the top of the nozzle turns in the body. Defective fuel nozzles will damage the engine due to improper spray patterns.
a. remove fuel injection lines
Keep all parts clean from contaminants. Contaminants put into the system may cause rapid wear and shortened component life.
1. Remove clamp (1). 2. Install tool (A). Turn screw (2) out until the button on the screw almost makes contact with the inside of the nozzle puller. Tilt the tool approximately 45° and place it over the nozzle.3. Tilt the nozzle puller (A) up so the inside lip of the puller is under the stepped diameter of the nozzle.4. Turn screw (2) down until the button goes into the bolt hole for the nozzle hold down clamp.
Do not exceed a torque of 17 N m (13 lb ft) on the screw in tooling (A) to remove the nozzle. Added force can cause the stem of the nozzle to bend or break off.
5. Turn screw (2) to lift the nozzle out of its bore. If necessary, after the nozzle is loose in its bore, move it up and down to help loosen any carbon and make removal easier. 6. If the nozzle can not be removed with tooling (A), tooling (B) must be used. When tooling (B) is used, the nozzle normally can not be used again, and a new nozzle will need to be installed as a replacement.
Hold tool (B) so the center line of tool (B) is the same as the extended center line of fuel injection nozzle (2). This will prevent distortion of the fuel injection nozzle which can cause the nozzle to bend or break off.
7. Remove the protective cap and install tooling (B).8. Use the slide hammer to remove fuel injection nozzle (3).9. Remove the compression seal.10. For nozzles removed using tool (A), remove the carbon dam seal on the end of the nozzle. The following steps are for the installation of the fuel injection nozzles. Tool (C) must be modified by drilling it out to a diameter of 8.5 mm (.344 in) and to a depth of 1.5 mm (.060 in) before it can be used on the 8N7002 Fuel Injection Nozzle.11. Use tool (C) to install carbon dam seal (4).12. To clean the nozzles, see Special Instruction SEHS7292 for the use of tooling (D).13. Install new compression seal (5). 14. Use tool (E) to clean the bore for the fuel injection nozzle. 15. Install fuel injection nozzle (6).
Do not let the tops of the fuel nozzles turn when the fuel lines are tightened. The nozzles will be damaged if the top of the nozzle turns in the body.
End By:a. install fuel injection lines
Do not let the tops of the nozzles turn while the fuel lines are loosened. The nozzles will be damaged if the top of the nozzle turns in the body. Defective fuel nozzles will damage the engine due to improper spray patterns.
a. remove fuel injection lines
Keep all parts clean from contaminants. Contaminants put into the system may cause rapid wear and shortened component life.
1. Remove clamp (1). 2. Install tool (A). Turn screw (2) out until the button on the screw almost makes contact with the inside of the nozzle puller. Tilt the tool approximately 45° and place it over the nozzle.3. Tilt the nozzle puller (A) up so the inside lip of the puller is under the stepped diameter of the nozzle.4. Turn screw (2) down until the button goes into the bolt hole for the nozzle hold down clamp.
Do not exceed a torque of 17 N m (13 lb ft) on the screw in tooling (A) to remove the nozzle. Added force can cause the stem of the nozzle to bend or break off.
5. Turn screw (2) to lift the nozzle out of its bore. If necessary, after the nozzle is loose in its bore, move it up and down to help loosen any carbon and make removal easier. 6. If the nozzle can not be removed with tooling (A), tooling (B) must be used. When tooling (B) is used, the nozzle normally can not be used again, and a new nozzle will need to be installed as a replacement.
Hold tool (B) so the center line of tool (B) is the same as the extended center line of fuel injection nozzle (2). This will prevent distortion of the fuel injection nozzle which can cause the nozzle to bend or break off.
7. Remove the protective cap and install tooling (B).8. Use the slide hammer to remove fuel injection nozzle (3).9. Remove the compression seal.10. For nozzles removed using tool (A), remove the carbon dam seal on the end of the nozzle. The following steps are for the installation of the fuel injection nozzles. Tool (C) must be modified by drilling it out to a diameter of 8.5 mm (.344 in) and to a depth of 1.5 mm (.060 in) before it can be used on the 8N7002 Fuel Injection Nozzle.11. Use tool (C) to install carbon dam seal (4).12. To clean the nozzles, see Special Instruction SEHS7292 for the use of tooling (D).13. Install new compression seal (5). 14. Use tool (E) to clean the bore for the fuel injection nozzle. 15. Install fuel injection nozzle (6).
Do not let the tops of the fuel nozzles turn when the fuel lines are tightened. The nozzles will be damaged if the top of the nozzle turns in the body.
End By:a. install fuel injection lines
Have questions with 101605-3120?
Group cross 101605-3120 ZEXEL
Komatsu
101605-3120
9 400 610 167
6137721120
INJECTION-PUMP ASSEMBLY
S6D105
S6D105