Information injection-pump assembly
BOSCH
9 400 615 326
9400615326
ZEXEL
101605-3060
1016053060
KOMATSU
6138711470
6138711470
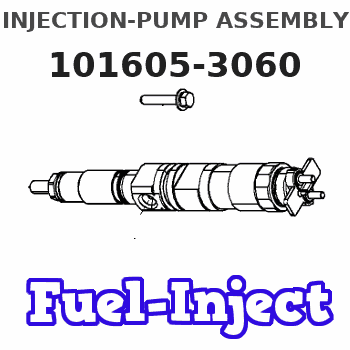
Rating:
Service parts 101605-3060 INJECTION-PUMP ASSEMBLY:
1.
_
5.
AUTOM. ADVANCE MECHANIS
7.
COUPLING PLATE
8.
_
9.
_
11.
Nozzle and Holder
6-13711-320-0
12.
Open Pre:MPa(Kqf/cm2)
22.1(225)
15.
NOZZLE SET
Cross reference number
BOSCH
9 400 615 326
9400615326
ZEXEL
101605-3060
1016053060
KOMATSU
6138711470
6138711470
Zexel num
Bosch num
Firm num
Name
101605-3060
9 400 615 326
6138711470 KOMATSU
INJECTION-PUMP ASSEMBLY
S6D110 K
S6D110 K
Calibration Data:
Adjustment conditions
Test oil
1404 Test oil ISO4113 or {SAEJ967d}
1404 Test oil ISO4113 or {SAEJ967d}
Test oil temperature
degC
40
40
45
Nozzle and nozzle holder
105780-8140
Bosch type code
EF8511/9A
Nozzle
105780-0000
Bosch type code
DN12SD12T
Nozzle holder
105780-2080
Bosch type code
EF8511/9
Opening pressure
MPa
17.2
Opening pressure
kgf/cm2
175
Injection pipe
Outer diameter - inner diameter - length (mm) mm 6-2-600
Outer diameter - inner diameter - length (mm) mm 6-2-600
Tester oil delivery pressure
kPa
157
157
157
Tester oil delivery pressure
kgf/cm2
1.6
1.6
1.6
Direction of rotation (viewed from drive side)
Right R
Right R
Injection timing adjustment
Direction of rotation (viewed from drive side)
Right R
Right R
Injection order
1-5-3-6-
2-4
Pre-stroke
mm
4
3.95
4.05
Beginning of injection position
Drive side NO.1
Drive side NO.1
Difference between angles 1
Cal 1-5 deg. 60 59.5 60.5
Cal 1-5 deg. 60 59.5 60.5
Difference between angles 2
Cal 1-3 deg. 120 119.5 120.5
Cal 1-3 deg. 120 119.5 120.5
Difference between angles 3
Cal 1-6 deg. 180 179.5 180.5
Cal 1-6 deg. 180 179.5 180.5
Difference between angles 4
Cyl.1-2 deg. 240 239.5 240.5
Cyl.1-2 deg. 240 239.5 240.5
Difference between angles 5
Cal 1-4 deg. 300 299.5 300.5
Cal 1-4 deg. 300 299.5 300.5
Injection quantity adjustment
Adjusting point
A
Rack position
10
Pump speed
r/min
900
900
900
Average injection quantity
mm3/st.
95.1
94.1
96.1
Max. variation between cylinders
%
0
-2
2
Basic
*
Fixing the rack
*
Injection quantity adjustment_02
Adjusting point
B
Rack position
7.7+-0.5
Pump speed
r/min
325
325
325
Average injection quantity
mm3/st.
11.7
10.5
12.9
Max. variation between cylinders
%
0
-10
10
Fixing the rack
*
Test data Ex:
Governor adjustment
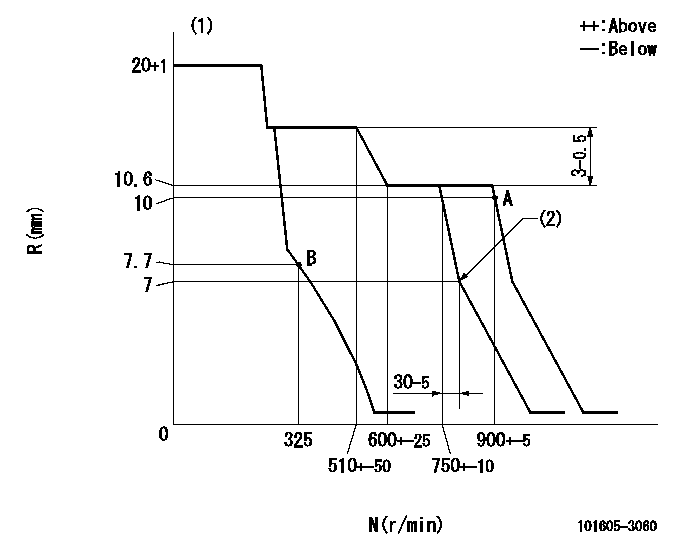
N:Pump speed
R:Rack position (mm)
(1)Target notch: K
(2)Idle sub spring setting: L1.
----------
K=16 L1=7-0.5mm
----------
----------
K=16 L1=7-0.5mm
----------
Speed control lever angle

F:Full speed
I:Idle
(1)Set the pump speed at aa. ( At delivery )
(2)Stopper bolt setting
(3)Set the pump speed at bb.
----------
aa=900r/min bb=750r/min
----------
a=29deg+-5deg b=7deg+-5deg c=6.5deg+-5deg
----------
aa=900r/min bb=750r/min
----------
a=29deg+-5deg b=7deg+-5deg c=6.5deg+-5deg
Stop lever angle
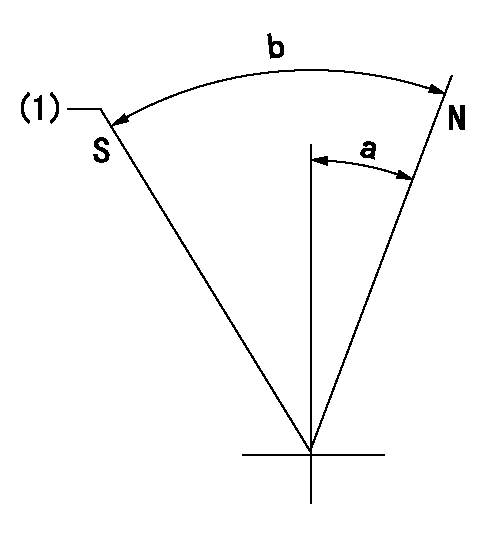
N:Pump normal
S:Stop the pump.
(1)At delivery
----------
----------
a=27deg+-5deg b=53deg+-5deg
----------
----------
a=27deg+-5deg b=53deg+-5deg
Information:
Engine Runs Smoothly
Possible Causes/Corrections Dirty Air CleanerIf the air cleaner has a restriction indicator, see if the red piston is in view. If there is no restriction indicator, restriction can be checked with a water manometer or a vacuum gauge (which measures in inches of water). Make a connection to the piping between the air cleaner and the inlet of the turbocharger. Check with the engine running at full load rpm. Maximum restriction is 635 mm (25 in) of water. If a gauge is not available, visually check the air cleaner element for dirt. If the element is dirty, clean the element or install a new element. Air Inlet Piping Damage Or RestrictionMake a visual inspection of the air inlet system and check for damage to piping, rags in the inlet piping, or damage to the rain cap or the cap pushed too far on the inlet pipe. If no damage is seen, check inlet restriction with a clean air cleaner element. Exhaust System RestrictionMake a visual inspection of the exhaust system. Check for damage to piping or for a defective muffler. If no damage is found, you can check the system by checking the back pressure from the exhaust (pressure difference measurement between exhaust outlet and atmosphere). The back pressure must not be more than 1016 mm (40 in) of water. You can also check by removing the exhaust pipes from the exhaust manifolds. With the exhaust pipes removed, start and load the engine on a chassis dynamometer to see if the problem is corrected. Fuel Injection Timing Not CorrectCheck and make necessary adjustments as in Testing and Adjusting Section of this Service Manual. Fuel Setting Is Not CorrectCheck and make necessary adjustments as in Testing and Adjusting Section of this Service Manual. See the Fuel Setting And Related Information Fiche for the correct fuel setting. Low Quality FuelTest the engine with fuel according to recommendations by Caterpillar Inc. For more information see Special Instruction, Form No. SEHS7067, Fuel Recommendations For Caterpillar Diesel Engines. Also, Special Instruction, Form No. SEHS6947 has fuel correction factors and tables. Defective Fuel Nozzle(s)Defective fuel nozzles will normally cause the engine to misfire and run rough, but can cause too much smoke with engine still running smooth. Remove the fuel nozzles and test as in Testing and Adjusting Section of this Service Manual. Wrong Seal Washer Installed Under Nozzle(s)The use of incorrect washers change the location of the fuel injection nozzles in the combustion chamber. This effects smoke. Check the Engine Arrangement for the correct part number to use. Valve Adjustment Not Correct Or Valve LeakageCheck and make necessary adjustments as in Testing and Adjusting Section of this Service Manual. Intake valve lash is 0.38 mm (.015 in) and exhaust valve lash is 0.64 mm (.025 in). Valve leakage normally causes the engine to misfire and run rough. Defective Fuel Injection PumpAn injection pump can have a good fuel flow coming from it but cause rough running because of slow timing that
Possible Causes/Corrections Dirty Air CleanerIf the air cleaner has a restriction indicator, see if the red piston is in view. If there is no restriction indicator, restriction can be checked with a water manometer or a vacuum gauge (which measures in inches of water). Make a connection to the piping between the air cleaner and the inlet of the turbocharger. Check with the engine running at full load rpm. Maximum restriction is 635 mm (25 in) of water. If a gauge is not available, visually check the air cleaner element for dirt. If the element is dirty, clean the element or install a new element. Air Inlet Piping Damage Or RestrictionMake a visual inspection of the air inlet system and check for damage to piping, rags in the inlet piping, or damage to the rain cap or the cap pushed too far on the inlet pipe. If no damage is seen, check inlet restriction with a clean air cleaner element. Exhaust System RestrictionMake a visual inspection of the exhaust system. Check for damage to piping or for a defective muffler. If no damage is found, you can check the system by checking the back pressure from the exhaust (pressure difference measurement between exhaust outlet and atmosphere). The back pressure must not be more than 1016 mm (40 in) of water. You can also check by removing the exhaust pipes from the exhaust manifolds. With the exhaust pipes removed, start and load the engine on a chassis dynamometer to see if the problem is corrected. Fuel Injection Timing Not CorrectCheck and make necessary adjustments as in Testing and Adjusting Section of this Service Manual. Fuel Setting Is Not CorrectCheck and make necessary adjustments as in Testing and Adjusting Section of this Service Manual. See the Fuel Setting And Related Information Fiche for the correct fuel setting. Low Quality FuelTest the engine with fuel according to recommendations by Caterpillar Inc. For more information see Special Instruction, Form No. SEHS7067, Fuel Recommendations For Caterpillar Diesel Engines. Also, Special Instruction, Form No. SEHS6947 has fuel correction factors and tables. Defective Fuel Nozzle(s)Defective fuel nozzles will normally cause the engine to misfire and run rough, but can cause too much smoke with engine still running smooth. Remove the fuel nozzles and test as in Testing and Adjusting Section of this Service Manual. Wrong Seal Washer Installed Under Nozzle(s)The use of incorrect washers change the location of the fuel injection nozzles in the combustion chamber. This effects smoke. Check the Engine Arrangement for the correct part number to use. Valve Adjustment Not Correct Or Valve LeakageCheck and make necessary adjustments as in Testing and Adjusting Section of this Service Manual. Intake valve lash is 0.38 mm (.015 in) and exhaust valve lash is 0.64 mm (.025 in). Valve leakage normally causes the engine to misfire and run rough. Defective Fuel Injection PumpAn injection pump can have a good fuel flow coming from it but cause rough running because of slow timing that
Have questions with 101605-3060?
Group cross 101605-3060 ZEXEL
Komatsu
101605-3060
9 400 615 326
6138711470
INJECTION-PUMP ASSEMBLY
S6D110
S6D110