Information injection-pump assembly
ZEXEL
101603-9980
1016039980
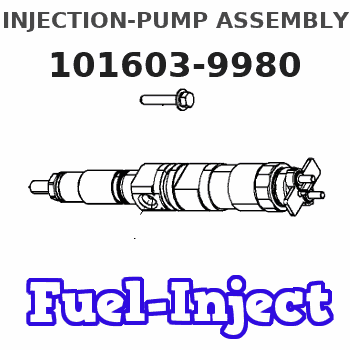
Rating:
Service parts 101603-9980 INJECTION-PUMP ASSEMBLY:
1.
_
7.
COUPLING PLATE
8.
_
9.
_
10.
NOZZLE AND HOLDER ASSY
11.
Nozzle and Holder
12.
Open Pre:MPa(Kqf/cm2)
13.
NOZZLE-HOLDER
14.
NOZZLE
15.
NOZZLE SET
Cross reference number
ZEXEL
101603-9980
1016039980
Zexel num
Bosch num
Firm num
Name
Calibration Data:
Adjustment conditions
Test oil
1404 Test oil ISO4113 or {SAEJ967d}
1404 Test oil ISO4113 or {SAEJ967d}
Test oil temperature
degC
40
40
45
Nozzle and nozzle holder
105780-8140
Bosch type code
EF8511/9A
Nozzle
105780-0000
Bosch type code
DN12SD12T
Nozzle holder
105780-2080
Bosch type code
EF8511/9
Opening pressure
MPa
17.2
Opening pressure
kgf/cm2
175
Injection pipe
Outer diameter - inner diameter - length (mm) mm 6-2-600
Outer diameter - inner diameter - length (mm) mm 6-2-600
Overflow valve
131424-1520
Overflow valve opening pressure
kPa
157
123
191
Overflow valve opening pressure
kgf/cm2
1.6
1.25
1.95
Tester oil delivery pressure
kPa
157
157
157
Tester oil delivery pressure
kgf/cm2
1.6
1.6
1.6
Direction of rotation (viewed from drive side)
Right R
Right R
Injection timing adjustment
Direction of rotation (viewed from drive side)
Right R
Right R
Injection order
6-2-4-1-
5-3
Pre-stroke
mm
4.6
4.55
4.65
Beginning of injection position
Drive side NO.1
Drive side NO.1
Difference between angles 1
Cal 6-2 deg. 60 59.5 60.5
Cal 6-2 deg. 60 59.5 60.5
Difference between angles 2
Cal 6-4 deg. 120 119.5 120.5
Cal 6-4 deg. 120 119.5 120.5
Difference between angles 3
Cal 6-1 deg. 180 179.5 180.5
Cal 6-1 deg. 180 179.5 180.5
Difference between angles 4
Cal 6-5 deg. 240 239.5 240.5
Cal 6-5 deg. 240 239.5 240.5
Difference between angles 5
Cal 6-3 deg. 300 299.5 300.5
Cal 6-3 deg. 300 299.5 300.5
Injection quantity adjustment
Adjusting point
-
Rack position
11.4
Pump speed
r/min
700
700
700
Average injection quantity
mm3/st.
74.8
73.2
76.4
Max. variation between cylinders
%
0
-2
2
Basic
*
Fixing the rack
*
Standard for adjustment of the maximum variation between cylinders
*
Injection quantity adjustment_02
Adjusting point
H
Rack position
10.2+-0.
5
Pump speed
r/min
250
250
250
Average injection quantity
mm3/st.
17
15.5
18.5
Max. variation between cylinders
%
0
-15
15
Fixing the rack
*
Standard for adjustment of the maximum variation between cylinders
*
Injection quantity adjustment_03
Adjusting point
A
Rack position
R1(11.4)
Pump speed
r/min
700
700
700
Average injection quantity
mm3/st.
74.8
73.8
75.8
Basic
*
Fixing the lever
*
Injection quantity adjustment_04
Adjusting point
B
Rack position
R1+0.1
Pump speed
r/min
1250
1250
1250
Average injection quantity
mm3/st.
80.2
76.2
84.2
Fixing the lever
*
Injection quantity adjustment_05
Adjusting point
C
Rack position
R1-0.25
Pump speed
r/min
500
500
500
Average injection quantity
mm3/st.
58.4
54.4
62.4
Fixing the lever
*
Injection quantity adjustment_06
Adjusting point
I
Rack position
-
Pump speed
r/min
100
100
100
Average injection quantity
mm3/st.
115
115
130
Fixing the lever
*
Rack limit
*
Timer adjustment
Pump speed
r/min
750--
Advance angle
deg.
0
0
0
Remarks
Start
Start
Timer adjustment_02
Pump speed
r/min
700
Advance angle
deg.
0.5
Timer adjustment_03
Pump speed
r/min
1250
Advance angle
deg.
4
3.5
4.5
Remarks
Finish
Finish
Test data Ex:
Governor adjustment
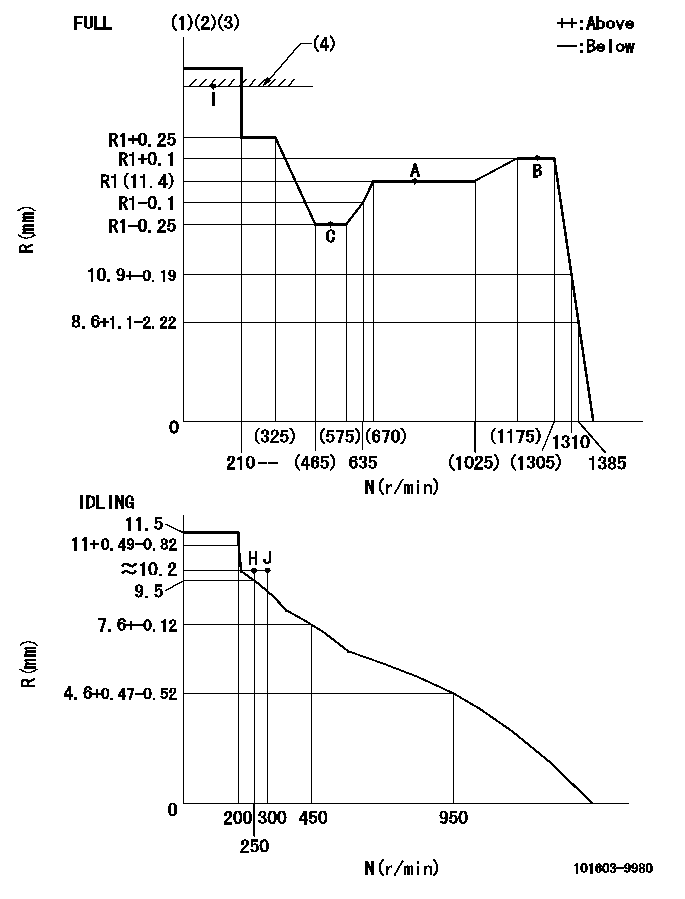
N:Pump speed
R:Rack position (mm)
(1)Torque cam stamping: T1
(2)Tolerance for racks not indicated: +-0.05mm.
(3)Microswitch adjustment unnecessary.
(4)RACK LIMIT
----------
T1=D58
----------
----------
T1=D58
----------
Speed control lever angle

F:Full speed
I:Idle
(1)Use the hole at R = aa
(2)Stopper bolt set position 'H'
----------
aa=65mm
----------
a=24deg+-5deg b=37deg+-3deg
----------
aa=65mm
----------
a=24deg+-5deg b=37deg+-3deg
Stop lever angle

N:Pump normal
S:Stop the pump.
----------
----------
a=25deg+-5deg b=40deg+-5deg
----------
----------
a=25deg+-5deg b=40deg+-5deg
Timing setting
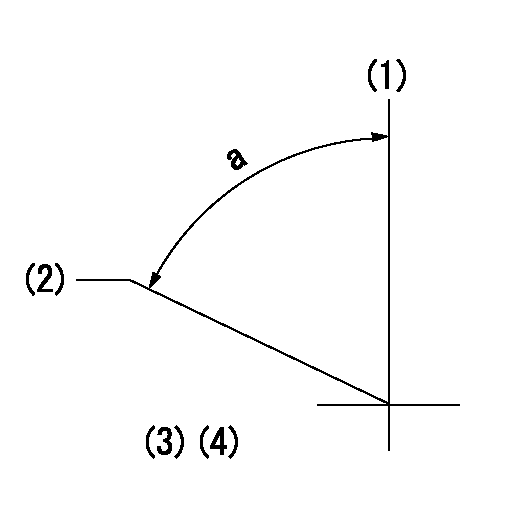
(1)Pump vertical direction
(2)Coupling's key groove position for the No. 6 cylinder's beginning of injection
(3)-
(4)-
----------
----------
a=(60deg)
----------
----------
a=(60deg)
Information:
Engine Crankshaft Will Not Turn
Possible Causes/Corrections
Low or No Battery Voltage/Check battery voltage. If battery voltage is less than 8 volts for a 12 volt system, or 16 volts for a 24 volt system, put a charge to the battery. If battery will not hold a charge, load test the battery as shown in the ELECTRICAL SYSTEM of the Testing and Adjusting section of this Service Manual. Bad Switch, Bad Wiring or Connection in Switch Circuit/With ignition switch in START position, check voltage at switch connection on starter solenoid. If there is no voltage, or if the voltage is low at this connection, check wiring, connections, ignition switch, and magnetic switch (if used). Bad Cable or Connection; Battery to Starter/With ignition switch in the START position, check voltage at connection of battery cable to starter. If there is no voltage, or if the voltage is low at this connection and there is good voltage at the battery, check for bad cable or connection between the battery and the starter. Bad Starter Solenoid/Remove and repair a solenoid which does not work when voltage is correct at both the battery and ignition switch connections. Bad Starter Motor/If the solenoid works and the starter motor does not turn the crankshaft, the starter motor is bad. Before removing the starter motor, turn the crankshaft by hand to be sure a mechanical failure inside the engine, transmission, or power take-off is not preventing the crankshaft from turning. If crankshaft turns freely by hand, engage the starter motor again. If the starter motor still will not work, remove the starter motor and repair it, or install a new starter motor. Transmission or Power Take-off (if so equipped) Problem Prevents Crankshaft From Turning/If crankshaft can not be turned by hand, disconnect the transmission and power take-off. If crankshaft will now turn, find the cause of the problem in the transmission or power take-off and make necessary corrections. Inside Problem Prevents Engine Crankshaft From Turning/If the crankshaft can not be turned after disconnecting the transmission and power take-off, remove the fuel nozzles and check for fluid in the cylinders while turning the crankshaft. If fluid in the cylinders is not the problem, the engine must be disassembled to check for other inside problems. Some of these inside problems are bearing seizure, piston seizure, and valves making contact with pistons.Engine Crankshaft Turns Too Slowly
Possible Causes/Corrections
Low Battery Voltage/Check battery voltage. If battery voltage is less than 8 volts for a 12 volt system, or 16 volts for a 24 volt system, put a charge to the battery. If the battery will not hold a charge, load test the battery as shown in the ELECTRICAL SYSTEM of the Testing and Adjusting section of this Service Manual. Bad Cable or Connection; Battery to Starter/With switch in START position, check voltage at battery cable connection to starter. If voltage is low at this connection and there is good voltage at the battery, check for bad cable or connection between the battery and
Possible Causes/Corrections
Low or No Battery Voltage/Check battery voltage. If battery voltage is less than 8 volts for a 12 volt system, or 16 volts for a 24 volt system, put a charge to the battery. If battery will not hold a charge, load test the battery as shown in the ELECTRICAL SYSTEM of the Testing and Adjusting section of this Service Manual. Bad Switch, Bad Wiring or Connection in Switch Circuit/With ignition switch in START position, check voltage at switch connection on starter solenoid. If there is no voltage, or if the voltage is low at this connection, check wiring, connections, ignition switch, and magnetic switch (if used). Bad Cable or Connection; Battery to Starter/With ignition switch in the START position, check voltage at connection of battery cable to starter. If there is no voltage, or if the voltage is low at this connection and there is good voltage at the battery, check for bad cable or connection between the battery and the starter. Bad Starter Solenoid/Remove and repair a solenoid which does not work when voltage is correct at both the battery and ignition switch connections. Bad Starter Motor/If the solenoid works and the starter motor does not turn the crankshaft, the starter motor is bad. Before removing the starter motor, turn the crankshaft by hand to be sure a mechanical failure inside the engine, transmission, or power take-off is not preventing the crankshaft from turning. If crankshaft turns freely by hand, engage the starter motor again. If the starter motor still will not work, remove the starter motor and repair it, or install a new starter motor. Transmission or Power Take-off (if so equipped) Problem Prevents Crankshaft From Turning/If crankshaft can not be turned by hand, disconnect the transmission and power take-off. If crankshaft will now turn, find the cause of the problem in the transmission or power take-off and make necessary corrections. Inside Problem Prevents Engine Crankshaft From Turning/If the crankshaft can not be turned after disconnecting the transmission and power take-off, remove the fuel nozzles and check for fluid in the cylinders while turning the crankshaft. If fluid in the cylinders is not the problem, the engine must be disassembled to check for other inside problems. Some of these inside problems are bearing seizure, piston seizure, and valves making contact with pistons.Engine Crankshaft Turns Too Slowly
Possible Causes/Corrections
Low Battery Voltage/Check battery voltage. If battery voltage is less than 8 volts for a 12 volt system, or 16 volts for a 24 volt system, put a charge to the battery. If the battery will not hold a charge, load test the battery as shown in the ELECTRICAL SYSTEM of the Testing and Adjusting section of this Service Manual. Bad Cable or Connection; Battery to Starter/With switch in START position, check voltage at battery cable connection to starter. If voltage is low at this connection and there is good voltage at the battery, check for bad cable or connection between the battery and