Information injection-pump assembly
ZEXEL
101603-9371
1016039371
NISSAN-DIESEL
16713Z6105
16713z6105
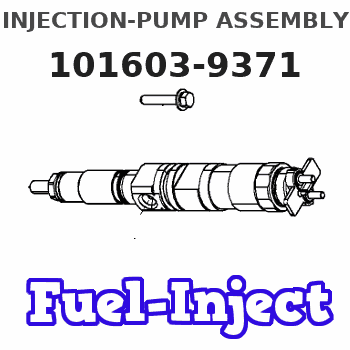
Rating:
Service parts 101603-9371 INJECTION-PUMP ASSEMBLY:
1.
_
7.
COUPLING PLATE
8.
_
9.
_
11.
Nozzle and Holder
16600-Z5519
12.
Open Pre:MPa(Kqf/cm2)
19.6{200}
15.
NOZZLE SET
Include in #1:
101603-9371
as INJECTION-PUMP ASSEMBLY
Include in #2:
104741-5861
as _
Cross reference number
ZEXEL
101603-9371
1016039371
NISSAN-DIESEL
16713Z6105
16713z6105
Zexel num
Bosch num
Firm num
Name
Calibration Data:
Adjustment conditions
Test oil
1404 Test oil ISO4113 or {SAEJ967d}
1404 Test oil ISO4113 or {SAEJ967d}
Test oil temperature
degC
40
40
45
Nozzle and nozzle holder
105780-8140
Bosch type code
EF8511/9A
Nozzle
105780-0000
Bosch type code
DN12SD12T
Nozzle holder
105780-2080
Bosch type code
EF8511/9
Opening pressure
MPa
17.2
Opening pressure
kgf/cm2
175
Injection pipe
Outer diameter - inner diameter - length (mm) mm 6-2-600
Outer diameter - inner diameter - length (mm) mm 6-2-600
Overflow valve
131424-1520
Overflow valve opening pressure
kPa
157
123
191
Overflow valve opening pressure
kgf/cm2
1.6
1.25
1.95
Tester oil delivery pressure
kPa
157
157
157
Tester oil delivery pressure
kgf/cm2
1.6
1.6
1.6
Direction of rotation (viewed from drive side)
Right R
Right R
Injection timing adjustment
Direction of rotation (viewed from drive side)
Right R
Right R
Injection order
1-4-2-6-
3-5
Pre-stroke
mm
3.4
3.35
3.45
Beginning of injection position
Drive side NO.1
Drive side NO.1
Difference between angles 1
Cal 1-4 deg. 60 59.5 60.5
Cal 1-4 deg. 60 59.5 60.5
Difference between angles 2
Cyl.1-2 deg. 120 119.5 120.5
Cyl.1-2 deg. 120 119.5 120.5
Difference between angles 3
Cal 1-6 deg. 180 179.5 180.5
Cal 1-6 deg. 180 179.5 180.5
Difference between angles 4
Cal 1-3 deg. 240 239.5 240.5
Cal 1-3 deg. 240 239.5 240.5
Difference between angles 5
Cal 1-5 deg. 300 299.5 300.5
Cal 1-5 deg. 300 299.5 300.5
Injection quantity adjustment
Adjusting point
-
Rack position
11.8
Pump speed
r/min
600
600
600
Average injection quantity
mm3/st.
66.3
64.7
67.9
Max. variation between cylinders
%
0
-3.5
3.5
Basic
*
Fixing the rack
*
Standard for adjustment of the maximum variation between cylinders
*
Injection quantity adjustment_02
Adjusting point
H
Rack position
9.5+-0.5
Pump speed
r/min
300
300
300
Average injection quantity
mm3/st.
9.5
7.7
11.3
Max. variation between cylinders
%
0
-10
10
Fixing the rack
*
Standard for adjustment of the maximum variation between cylinders
*
Injection quantity adjustment_03
Adjusting point
A
Rack position
R1(11.8)
Pump speed
r/min
600
600
600
Average injection quantity
mm3/st.
66.3
65.3
67.3
Basic
*
Fixing the lever
*
Injection quantity adjustment_04
Adjusting point
B
Rack position
R1-0.2
Pump speed
r/min
900
900
900
Average injection quantity
mm3/st.
73
69.8
76.2
Fixing the lever
*
Injection quantity adjustment_05
Adjusting point
C
Rack position
R1(11.8)
Pump speed
r/min
1500
1500
1500
Average injection quantity
mm3/st.
83.9
79.9
87.9
Fixing the lever
*
Injection quantity adjustment_06
Adjusting point
I
Rack position
-
Pump speed
r/min
100
100
100
Average injection quantity
mm3/st.
84
84
94
Fixing the lever
*
Rack limit
*
Timer adjustment
Pump speed
r/min
850--
Advance angle
deg.
0
0
0
Remarks
Start
Start
Timer adjustment_02
Pump speed
r/min
800
Advance angle
deg.
0.5
Timer adjustment_03
Pump speed
r/min
1500
Advance angle
deg.
4
3.5
4.5
Remarks
Finish
Finish
Test data Ex:
Governor adjustment
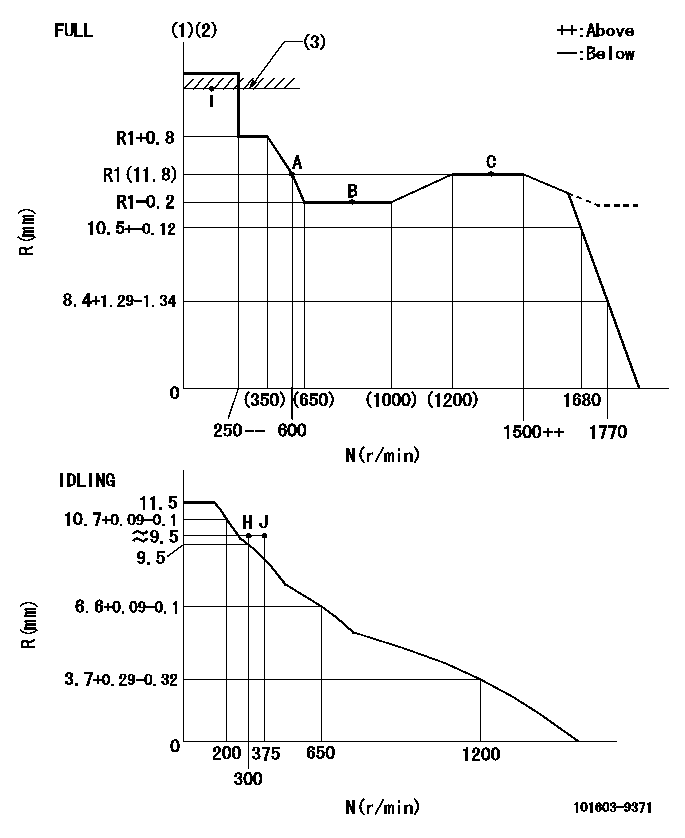
N:Pump speed
R:Rack position (mm)
(1)Torque cam stamping: T1
(2)Tolerance for racks not indicated: +-0.05mm.
(3)RACK LIMIT
----------
T1=C43
----------
----------
T1=C43
----------
Speed control lever angle
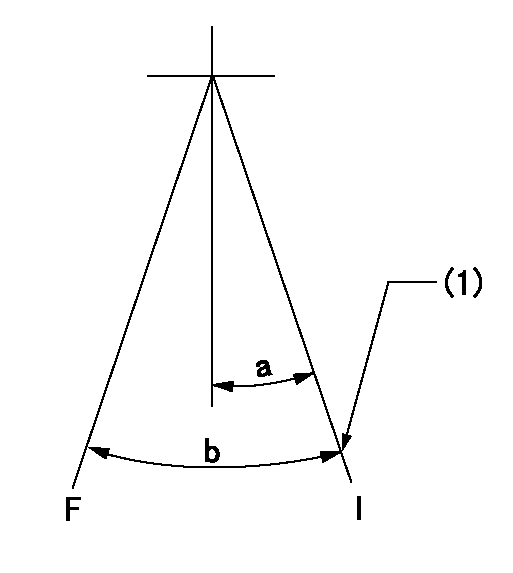
F:Full speed
I:Idle
(1)Stopper bolt set position 'H'
----------
----------
a=26.5deg+-5deg b=40deg+-3deg
----------
----------
a=26.5deg+-5deg b=40deg+-3deg
Stop lever angle
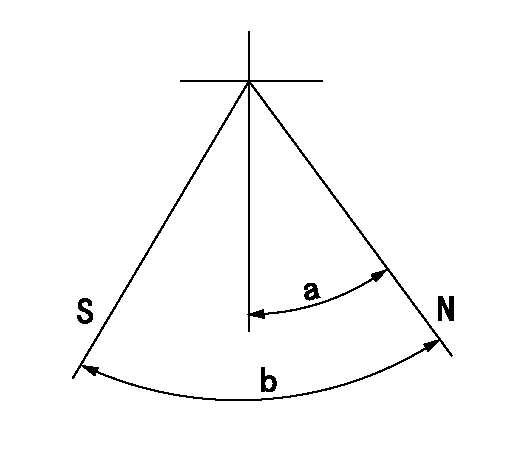
N:Pump normal
S:Stop the pump.
----------
----------
a=20deg+-5deg b=40deg+-5deg
----------
----------
a=20deg+-5deg b=40deg+-5deg
Timing setting
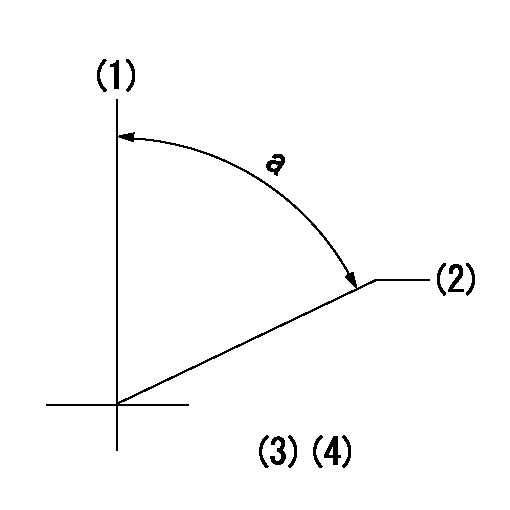
(1)Pump vertical direction
(2)Position of timer's threaded hole at No 1 cylinder's beginning of injection
(3)-
(4)-
----------
----------
a=(60deg)
----------
----------
a=(60deg)
Information:
start by:a) remove cylinder headsb) remove oil pan1. Remove the carbon from the top inside surface of the cylinders with tool (A). 2. Turn the crankshaft until two pistons are at bottom center.3. Remove connecting rod caps (1) from the two connecting rods. Put pieces of rubber hose or tape on the threads of the connecting rod bolts as protection for the crankshaft. 4. Push the pistons and connecting rods away from the crankshaft until the piston rings are above the cylinder block.5. Remove the two pistons (2) and the connecting rods. Keep each connecting rod cap with its respective connecting rod and piston. Put identification on each connecting rod as to its location for use at installation.
Do not turn the crankshaft while any of the connecting rods are in the engine without the caps installed.
6. Do Steps 2 through 5 for the remainder of the pistons.Install Pistons
Two different pistons are used in 3208 Truck Engines. One piston has a crater volume of 50.4 1.3 cm3 (3.08 .07 in.3), and the other piston has a crater volume of 58.8 1.2 cm3 (3.59 .07 in.3). Check the part number stamped on the top of the piston and refer to the parts book to be sure the correct replacement piston is used. The correct piston must be installed in the engine. If the wrong piston is installed, much damage to the engine will be the result.
1. Put clean engine oil on the piston rings, connecting rod bearings, cylinder walls and crankshaft bearing journals.2. Turn the crankshaft until the bearing journal for the pistons to be installed is at bottom center.3. Make sure the piston ring gaps are at least 120° apart on the piston. 4. Use tool (A) and install the piston in position in the same cylinder bore from which it was removed. The hole (crater) in the top of the piston must be toward (nearest) the center of the engine. For more detail about the installation of connecting rod bearings, see REMOVE AND INSTALL CONNECTING ROD BEARINGS.5. Check the bearing clearances with tool (B).6. Put 2P2506 Thread Lubricant on the threads of the bolts and contact surfaces of the nuts for the connecting rod caps.
When the connecting rod caps are installed, make sure that the number on the side of the cap is next to and respective with the number on the side of the connecting rod.
7. Put the cap (1) in position on the connecting rod and install the nuts. Tighten the nuts to a torque of 40 4 N m (30 3 lb.ft.). Put a mark on each nut and the end of each bolt. Tighten the nuts 60 5° more. 8. Check the side clearance between two connecting rods on the same crankshaft journal. Clearance must be 0.08 to 0.84 mm (.003 to .033 in.) for new rods.9. Do Steps 1 through 8 for the remainder of the pistons.end by:a) install cylinder headsb) install oil panDisassemble Pistons
start by:a)
Do not turn the crankshaft while any of the connecting rods are in the engine without the caps installed.
6. Do Steps 2 through 5 for the remainder of the pistons.Install Pistons
Two different pistons are used in 3208 Truck Engines. One piston has a crater volume of 50.4 1.3 cm3 (3.08 .07 in.3), and the other piston has a crater volume of 58.8 1.2 cm3 (3.59 .07 in.3). Check the part number stamped on the top of the piston and refer to the parts book to be sure the correct replacement piston is used. The correct piston must be installed in the engine. If the wrong piston is installed, much damage to the engine will be the result.
1. Put clean engine oil on the piston rings, connecting rod bearings, cylinder walls and crankshaft bearing journals.2. Turn the crankshaft until the bearing journal for the pistons to be installed is at bottom center.3. Make sure the piston ring gaps are at least 120° apart on the piston. 4. Use tool (A) and install the piston in position in the same cylinder bore from which it was removed. The hole (crater) in the top of the piston must be toward (nearest) the center of the engine. For more detail about the installation of connecting rod bearings, see REMOVE AND INSTALL CONNECTING ROD BEARINGS.5. Check the bearing clearances with tool (B).6. Put 2P2506 Thread Lubricant on the threads of the bolts and contact surfaces of the nuts for the connecting rod caps.
When the connecting rod caps are installed, make sure that the number on the side of the cap is next to and respective with the number on the side of the connecting rod.
7. Put the cap (1) in position on the connecting rod and install the nuts. Tighten the nuts to a torque of 40 4 N m (30 3 lb.ft.). Put a mark on each nut and the end of each bolt. Tighten the nuts 60 5° more. 8. Check the side clearance between two connecting rods on the same crankshaft journal. Clearance must be 0.08 to 0.84 mm (.003 to .033 in.) for new rods.9. Do Steps 1 through 8 for the remainder of the pistons.end by:a) install cylinder headsb) install oil panDisassemble Pistons
start by:a)