Information injection-pump assembly
ZEXEL
101603-8992
1016038992
ISUZU
8943906046
8943906046
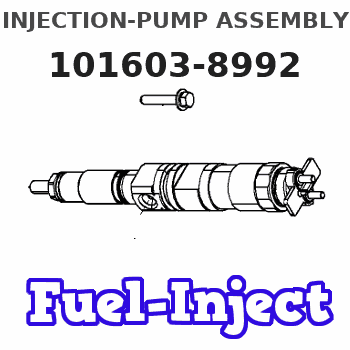
Rating:
Service parts 101603-8992 INJECTION-PUMP ASSEMBLY:
1.
_
7.
COUPLING PLATE
8.
_
9.
_
11.
Nozzle and Holder
8-94391-291-4
12.
Open Pre:MPa(Kqf/cm2)
16.2{165}/19.6{200}
14.
NOZZLE
Cross reference number
ZEXEL
101603-8992
1016038992
ISUZU
8943906046
8943906046
Zexel num
Bosch num
Firm num
Name
Calibration Data:
Adjustment conditions
Test oil
1404 Test oil ISO4113 or {SAEJ967d}
1404 Test oil ISO4113 or {SAEJ967d}
Test oil temperature
degC
40
40
45
Nozzle and nozzle holder
105780-8260
Bosch type code
9 430 610 133
Nozzle
105780-0120
Bosch type code
1 688 901 990
Nozzle holder
105780-2190
Opening pressure
MPa
18
Opening pressure
kgf/cm2
184
Injection pipe
Outer diameter - inner diameter - length (mm) mm 6-2-600
Outer diameter - inner diameter - length (mm) mm 6-2-600
Overflow valve
131424-8620
Overflow valve opening pressure
kPa
206
172
240
Overflow valve opening pressure
kgf/cm2
2.1
1.75
2.45
Tester oil delivery pressure
kPa
255
255
255
Tester oil delivery pressure
kgf/cm2
2.6
2.6
2.6
Direction of rotation (viewed from drive side)
Left L
Left L
Injection timing adjustment
Direction of rotation (viewed from drive side)
Left L
Left L
Injection order
1-5-3-6-
2-4
Pre-stroke
mm
3.8
3.75
3.85
Rack position
Point A R=A
Point A R=A
Beginning of injection position
Governor side NO.1
Governor side NO.1
Difference between angles 1
Cal 1-5 deg. 60 59.5 60.5
Cal 1-5 deg. 60 59.5 60.5
Difference between angles 2
Cal 1-3 deg. 120 119.5 120.5
Cal 1-3 deg. 120 119.5 120.5
Difference between angles 3
Cal 1-6 deg. 180 179.5 180.5
Cal 1-6 deg. 180 179.5 180.5
Difference between angles 4
Cyl.1-2 deg. 240 239.5 240.5
Cyl.1-2 deg. 240 239.5 240.5
Difference between angles 5
Cal 1-4 deg. 300 299.5 300.5
Cal 1-4 deg. 300 299.5 300.5
Injection quantity adjustment
Adjusting point
-
Rack position
14.5
Pump speed
r/min
850
850
850
Average injection quantity
mm3/st.
133.5
131.9
135.1
Max. variation between cylinders
%
0
-2.5
2.5
Basic
*
Fixing the rack
*
Standard for adjustment of the maximum variation between cylinders
*
Injection quantity adjustment_02
Adjusting point
Z
Rack position
9.5+-0.5
Pump speed
r/min
300
300
300
Average injection quantity
mm3/st.
15.5
14.2
16.8
Max. variation between cylinders
%
0
-14
14
Fixing the rack
*
Standard for adjustment of the maximum variation between cylinders
*
Injection quantity adjustment_03
Adjusting point
A
Rack position
R1(14.5)
Pump speed
r/min
850
850
850
Average injection quantity
mm3/st.
133.5
132.5
134.5
Basic
*
Fixing the lever
*
Injection quantity adjustment_04
Adjusting point
B
Rack position
[R1+1.05
]+0.05-0
.15
Pump speed
r/min
1450
1450
1450
Average injection quantity
mm3/st.
133
129.8
136.2
Fixing the lever
*
Test data Ex:
Governor adjustment
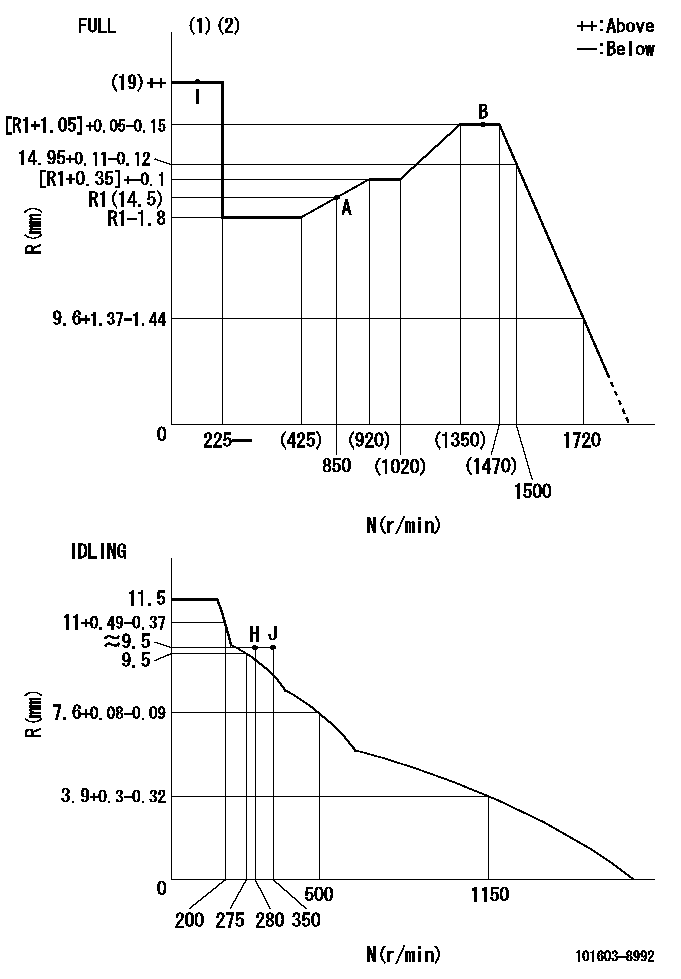
N:Pump speed
R:Rack position (mm)
(1)Torque cam stamping: T1
(2)Tolerance for racks not indicated: +-0.05mm.
----------
T1=N14
----------
----------
T1=N14
----------
Timer adjustment

(1)Adjusting range
(2)Step response time
(N): Speed of the pump
(L): Load
(theta) Advance angle
(Srd1) Step response time 1
(Srd2) Step response time 2
1. Adjusting conditions for the variable timer
(1)Adjust the clearance between the pickup and the protrusion to L.
----------
L=1.5+-0.2mm N2=800r/min C2=(8)deg t1=2--sec. t2=2--sec.
----------
N1=1300++r/min P1=0kPa(0kgf/cm2) P2=392kPa(4kgf/cm2) C1=8+-0.3deg R01=0/4load R02=4/4load
----------
L=1.5+-0.2mm N2=800r/min C2=(8)deg t1=2--sec. t2=2--sec.
----------
N1=1300++r/min P1=0kPa(0kgf/cm2) P2=392kPa(4kgf/cm2) C1=8+-0.3deg R01=0/4load R02=4/4load
Speed control lever angle
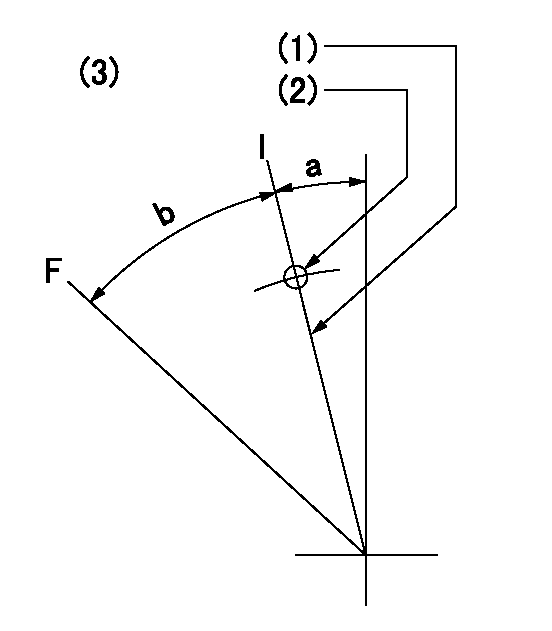
F:Full speed
I:Idle
(1)Use the pin at R = aa
(2)Stopper bolt setting
(3)Viewed from feed pump side.
----------
aa=35mm
----------
a=10deg+-5deg b=41deg+-3deg
----------
aa=35mm
----------
a=10deg+-5deg b=41deg+-3deg
Stop lever angle
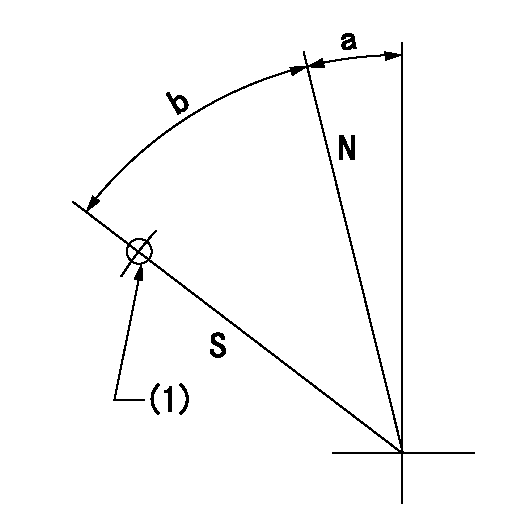
N:Pump normal
S:Stop the pump.
(1)Use the pin at R = aa
----------
aa=45mm
----------
a=12.5deg+-5deg b=40deg+-5deg
----------
aa=45mm
----------
a=12.5deg+-5deg b=40deg+-5deg
0000001501 RACK SENSOR

Rack sensor adjustment
1. Flange type rack sensor (rack sensor adjustment -5*20)
(1)These types of rack sensors do not need adjustment. Confirm the performance with the following procedures.
(2)Mount the rack sensor main body to the pump main body.
(3)Fix the pump lever at full.
(4)At supply voltage V1, pump speed N1 and rack position Ra, confirm that the amp's output voltage is Vist.
(5)Move the pump lever two or three times.
(6)Set again to full.
(7)Confirm that the amplifier output voltage is Vist.
(8)Fix the caution plate to the upper part of the rack sensor.
(For those without the caution plate instructions, make sure the nameplate of the rack sensor carries the "Don't hold here" caution.)
(9)Apply red paint to the rack sensor mounting bolts (2 places).
----------
V1=5+-0.01V N1=850r/min Ra=R1(14.5)mm Vist=3.74+-0.28V
----------
----------
V1=5+-0.01V N1=850r/min Ra=R1(14.5)mm Vist=3.74+-0.28V
----------
Timing setting

(1)Pump vertical direction
(2)Positions of coupling's threaded installation holes at No 1 cylinder's beginning of injection
(3)B.T.D.C.: aa
(4)-
----------
aa=6deg
----------
a=(160deg)
----------
aa=6deg
----------
a=(160deg)
Information:
Crankshaft Gear Removal
Remove the gear using an 8B7548 Push Puller, 8B7551 Bearing Pulling Attachment, 8B7561 Step Plate, and 8H684 Ratchet Box Wrench.
PULLING CRANKSHAFT GEARThe 1P820 Hydraulic Puller Group can also be used to pull gear from crankshaft. Tools required are 1P820 Hydraulic Puller Group, 8B7551 Bearing Pulling Attachment, 8B7549 Puller legs (two), 8B7561 Step Plate, 3H465 Plate (four), 1B4207 Nut (two), and 9S5800 Pump Group.
USING HYDRAULIC PULLERCrankshaft Gear Installation
1. Install the key in keyway of crankshaft. Remove all burrs from key and keyway inside of crankshaft gear.2. Heat gear to 500° F. (260° C) maximum.3. Install gear on crankshaft with timing mark on gear facing front of crankshaft.Crankshaft Wear Sleeve Removal
REMOVING WEAR SLEEVEUse the 8S7164 Wear Sleeve Puller Group to remove the wear sleeve.Crankshaft Wear Sleeve Installation
WEAR SLEEVE INSTALLATION TOOLS
1. 5P290 Pilot. 2. 5P286 Ring. 3. 9S8858 Nut. 4. 1P5515 Bolts. 5. 9S8864 Pusher Plate.To install the wear sleeve, use the following procedure:1. Install 5P290 Pilot (1) on the end of the crankshaft. Install 1P5515 Bolts (4) and tighten just enough to hold pilot (1) yet allow some side movement. Put the wear sleeve on pilot (1) with the chamfer toward the rear of the engine. Push the wear sleeve on the crankshaft to put pilot (1) in the center, then tighten bolts (4).2. Put 5P286 Ring (2) on 9S8864 Pusher Plate (5) and place this assembly on the stud of pilot (1). Install 9S8858 Nut (3) and tighten nut to push wear sleeve on to the crankshaft.Crankshaft Rear Oil Seal Removal
Use the 1P3075 Puller Group to remove the crankshaft rear seal.
REMOVING REAR OIL SEAL (Typical Example)Crankshaft Rear Oil Seal Installation
REAR OIL SEAL INSTALLATION TOOLS
1. 5P290 Pilot. 2. 1P5515 Bolts. 3. 5P285 Ring. 4. 9S8858 Nut. 5. 5P288 Ring. 6. 9S8864 Pusher Plate.To install the crankshaft rear oil seal, use the following procedure:1. Install 5P290 Pilot (1) on the crankshaft with 1P5515 Bolts (2). Install 5P288 Ring (5) on pilot (1).2. Put 7F2770 Cement on the outer diameter of the seal metal shell. Put engine oil on the lip of the seal. Install the seal on the pilot with the lip of the seal toward the front of the engine.3. Install 9S8864 Pusher Plate (6) and 5P285 Ring (3) over pilot (1). Install 9S8858 Nut (4). Tighten nut (4) until ring (5) makes contact with the flywheel housing. To prevent possible oil leakage, install a new wear sleeve each time the rear oil seal is replaced.Crankshaft Front Oil Seal (1100, 3100, and 3208 Engines 79V1-79V1407)
The crankshaft front oil seal can be removed with the timing gear cover on or off the engine. To install the seal to the proper depth, the timing gear cover must be on the engine.A new timing gear cover permits the crankshaft front oil seal to be installed to two depths.Use the 9S6030 Installation Group which includes the 8S2276 Installer and 9S6012 Spacer to install the seal. To install seal to the original depth, use only the 8S2276 Installer. To obtain an additional wear
Remove the gear using an 8B7548 Push Puller, 8B7551 Bearing Pulling Attachment, 8B7561 Step Plate, and 8H684 Ratchet Box Wrench.
PULLING CRANKSHAFT GEARThe 1P820 Hydraulic Puller Group can also be used to pull gear from crankshaft. Tools required are 1P820 Hydraulic Puller Group, 8B7551 Bearing Pulling Attachment, 8B7549 Puller legs (two), 8B7561 Step Plate, 3H465 Plate (four), 1B4207 Nut (two), and 9S5800 Pump Group.
USING HYDRAULIC PULLERCrankshaft Gear Installation
1. Install the key in keyway of crankshaft. Remove all burrs from key and keyway inside of crankshaft gear.2. Heat gear to 500° F. (260° C) maximum.3. Install gear on crankshaft with timing mark on gear facing front of crankshaft.Crankshaft Wear Sleeve Removal
REMOVING WEAR SLEEVEUse the 8S7164 Wear Sleeve Puller Group to remove the wear sleeve.Crankshaft Wear Sleeve Installation
WEAR SLEEVE INSTALLATION TOOLS
1. 5P290 Pilot. 2. 5P286 Ring. 3. 9S8858 Nut. 4. 1P5515 Bolts. 5. 9S8864 Pusher Plate.To install the wear sleeve, use the following procedure:1. Install 5P290 Pilot (1) on the end of the crankshaft. Install 1P5515 Bolts (4) and tighten just enough to hold pilot (1) yet allow some side movement. Put the wear sleeve on pilot (1) with the chamfer toward the rear of the engine. Push the wear sleeve on the crankshaft to put pilot (1) in the center, then tighten bolts (4).2. Put 5P286 Ring (2) on 9S8864 Pusher Plate (5) and place this assembly on the stud of pilot (1). Install 9S8858 Nut (3) and tighten nut to push wear sleeve on to the crankshaft.Crankshaft Rear Oil Seal Removal
Use the 1P3075 Puller Group to remove the crankshaft rear seal.
REMOVING REAR OIL SEAL (Typical Example)Crankshaft Rear Oil Seal Installation
REAR OIL SEAL INSTALLATION TOOLS
1. 5P290 Pilot. 2. 1P5515 Bolts. 3. 5P285 Ring. 4. 9S8858 Nut. 5. 5P288 Ring. 6. 9S8864 Pusher Plate.To install the crankshaft rear oil seal, use the following procedure:1. Install 5P290 Pilot (1) on the crankshaft with 1P5515 Bolts (2). Install 5P288 Ring (5) on pilot (1).2. Put 7F2770 Cement on the outer diameter of the seal metal shell. Put engine oil on the lip of the seal. Install the seal on the pilot with the lip of the seal toward the front of the engine.3. Install 9S8864 Pusher Plate (6) and 5P285 Ring (3) over pilot (1). Install 9S8858 Nut (4). Tighten nut (4) until ring (5) makes contact with the flywheel housing. To prevent possible oil leakage, install a new wear sleeve each time the rear oil seal is replaced.Crankshaft Front Oil Seal (1100, 3100, and 3208 Engines 79V1-79V1407)
The crankshaft front oil seal can be removed with the timing gear cover on or off the engine. To install the seal to the proper depth, the timing gear cover must be on the engine.A new timing gear cover permits the crankshaft front oil seal to be installed to two depths.Use the 9S6030 Installation Group which includes the 8S2276 Installer and 9S6012 Spacer to install the seal. To install seal to the original depth, use only the 8S2276 Installer. To obtain an additional wear