Information injection-pump assembly
ZEXEL
101603-8991
1016038991
ISUZU
8943906044
8943906044
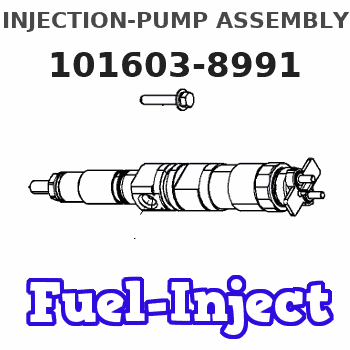
Rating:
Service parts 101603-8991 INJECTION-PUMP ASSEMBLY:
1.
_
7.
COUPLING PLATE
8.
_
9.
_
11.
Nozzle and Holder
8-94391-291-4
12.
Open Pre:MPa(Kqf/cm2)
16.2{165}/19.6{200}
14.
NOZZLE
Cross reference number
ZEXEL
101603-8991
1016038991
ISUZU
8943906044
8943906044
Zexel num
Bosch num
Firm num
Name
Calibration Data:
Adjustment conditions
Test oil
1404 Test oil ISO4113 or {SAEJ967d}
1404 Test oil ISO4113 or {SAEJ967d}
Test oil temperature
degC
40
40
45
Nozzle and nozzle holder
105780-8260
Bosch type code
9 430 610 133
Nozzle
105780-0120
Bosch type code
1 688 901 990
Nozzle holder
105780-2190
Opening pressure
MPa
18
Opening pressure
kgf/cm2
184
Injection pipe
Outer diameter - inner diameter - length (mm) mm 6-2-600
Outer diameter - inner diameter - length (mm) mm 6-2-600
Overflow valve
131424-8620
Overflow valve opening pressure
kPa
206
172
240
Overflow valve opening pressure
kgf/cm2
2.1
1.75
2.45
Tester oil delivery pressure
kPa
255
255
255
Tester oil delivery pressure
kgf/cm2
2.6
2.6
2.6
Direction of rotation (viewed from drive side)
Left L
Left L
Injection timing adjustment
Direction of rotation (viewed from drive side)
Left L
Left L
Injection order
1-5-3-6-
2-4
Pre-stroke
mm
3.8
3.75
3.85
Rack position
Point A R=A
Point A R=A
Beginning of injection position
Governor side NO.1
Governor side NO.1
Difference between angles 1
Cal 1-5 deg. 60 59.5 60.5
Cal 1-5 deg. 60 59.5 60.5
Difference between angles 2
Cal 1-3 deg. 120 119.5 120.5
Cal 1-3 deg. 120 119.5 120.5
Difference between angles 3
Cal 1-6 deg. 180 179.5 180.5
Cal 1-6 deg. 180 179.5 180.5
Difference between angles 4
Cyl.1-2 deg. 240 239.5 240.5
Cyl.1-2 deg. 240 239.5 240.5
Difference between angles 5
Cal 1-4 deg. 300 299.5 300.5
Cal 1-4 deg. 300 299.5 300.5
Injection quantity adjustment
Adjusting point
-
Rack position
14.5
Pump speed
r/min
850
850
850
Average injection quantity
mm3/st.
133.5
131.9
135.1
Max. variation between cylinders
%
0
-2.5
2.5
Basic
*
Fixing the rack
*
Standard for adjustment of the maximum variation between cylinders
*
Injection quantity adjustment_02
Adjusting point
Z
Rack position
9.5+-0.5
Pump speed
r/min
300
300
300
Average injection quantity
mm3/st.
15.5
14.2
16.8
Max. variation between cylinders
%
0
-14
14
Fixing the rack
*
Standard for adjustment of the maximum variation between cylinders
*
Injection quantity adjustment_03
Adjusting point
A
Rack position
R1(14.5)
Pump speed
r/min
850
850
850
Average injection quantity
mm3/st.
133.5
132.5
134.5
Basic
*
Fixing the lever
*
Injection quantity adjustment_04
Adjusting point
B
Rack position
(R1+1.05
)+0.05-0
.15
Pump speed
r/min
1450
1450
1450
Average injection quantity
mm3/st.
133
129.8
136.2
Fixing the lever
*
Test data Ex:
Governor adjustment
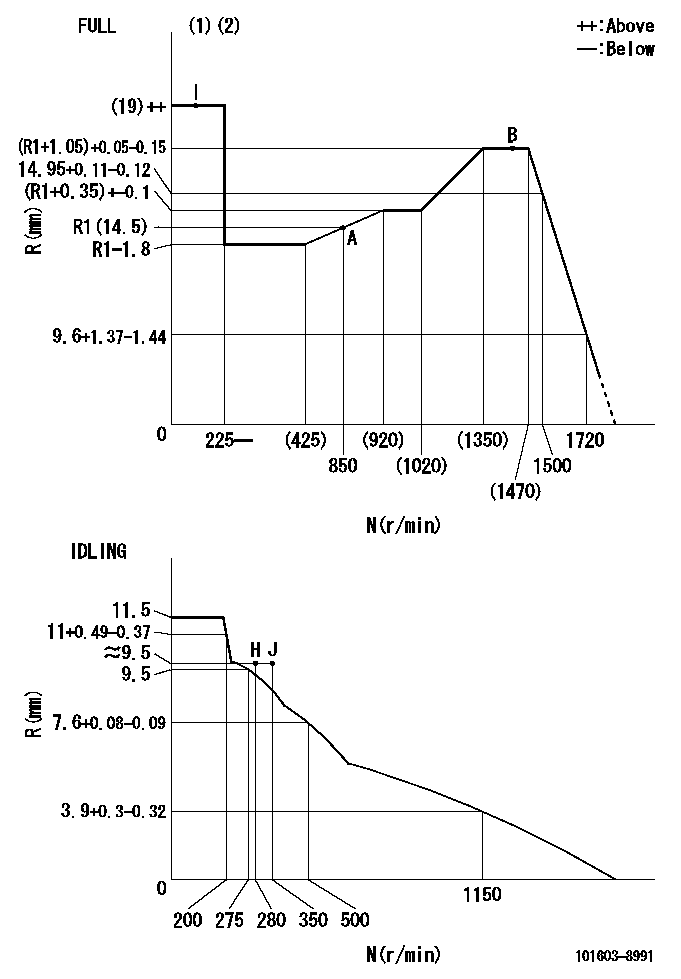
N:Pump speed
R:Rack position (mm)
(1)Torque cam stamping: T1
(2)Tolerance for racks not indicated: +-0.05mm.
----------
T1=N14
----------
----------
T1=N14
----------
Timer adjustment

(1)Adjusting range
(2)Step response time
(N): Speed of the pump
(L): Load
(theta) Advance angle
(Srd1) Step response time 1
(Srd2) Step response time 2
1. Adjusting conditions for the variable timer
(1)Adjust the clearance between the pickup and the protrusion to L.
----------
L=1.5+-0.2mm N2=800r/min C2=(8deg) t1=2--sec. t2=2--sec.
----------
N1=1300++r/min P1=0kPa(0kgf/cm2) P2=392kPa(4kgf/cm2) C1=8+-0.3deg R01=0/4load R02=4/4load
----------
L=1.5+-0.2mm N2=800r/min C2=(8deg) t1=2--sec. t2=2--sec.
----------
N1=1300++r/min P1=0kPa(0kgf/cm2) P2=392kPa(4kgf/cm2) C1=8+-0.3deg R01=0/4load R02=4/4load
Speed control lever angle
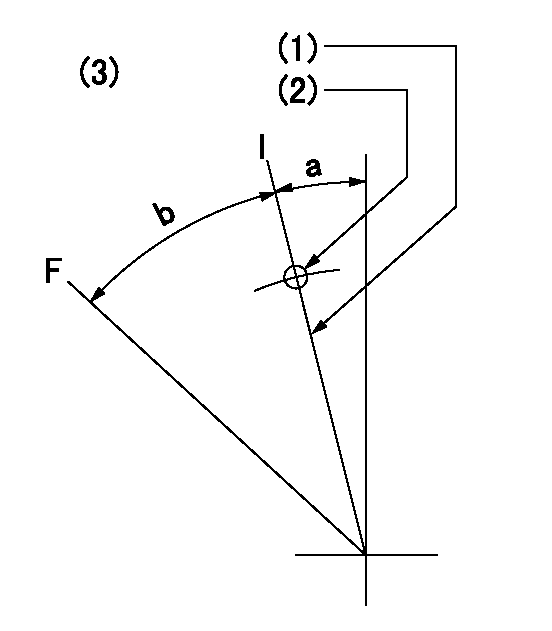
F:Full speed
I:Idle
(1)Stopper bolt set position 'H'
(2)Use the pin at R = aa
(3)Viewed from feed pump side.
----------
aa=35mm
----------
a=10deg+-5deg b=41deg+-3deg
----------
aa=35mm
----------
a=10deg+-5deg b=41deg+-3deg
Stop lever angle
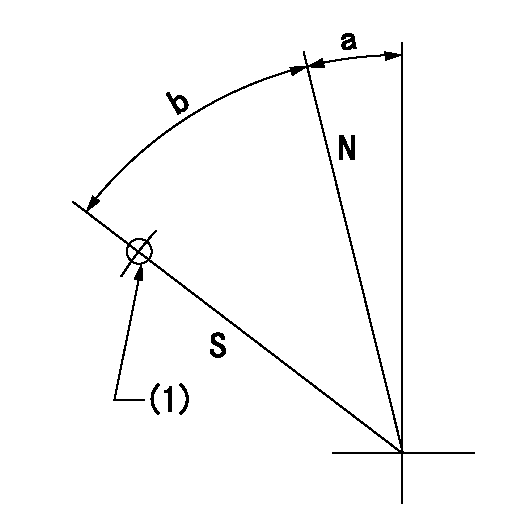
N:Pump normal
S:Stop the pump.
(1)Use the pin at R = aa
----------
aa=45mm
----------
a=12.5deg+-5deg b=40deg+-5deg
----------
aa=45mm
----------
a=12.5deg+-5deg b=40deg+-5deg
0000001501 RACK SENSOR

Rack sensor adjustment
1. Flange type rack sensor (rack sensor adjustment -5*20)
(1)These types of rack sensors do not need adjustment. Confirm the performance with the following procedures.
(2)Mount the rack sensor main body to the pump main body.
(3)Fix the pump lever at full.
(4)At supply voltage V1, pump speed N1 and rack position Ra, confirm that the amp's output voltage is Vist.
(5)Move the pump lever two or three times.
(6)Set again to full.
(7)Confirm that the amplifier output voltage is Vist.
(8)Fix the caution plate to the upper part of the rack sensor.
(For those without the caution plate instructions, make sure the nameplate of the rack sensor carries the "Don't hold here" caution.)
(9)Apply red paint to the rack sensor mounting bolts (2 places).
----------
V1=5+-0.01V N1=850r/min Ra=R1(14.5)mm Vist=3.74+-0.28V
----------
----------
V1=5+-0.01V N1=850r/min Ra=R1(14.5)mm Vist=3.74+-0.28V
----------
Timing setting

(1)Pump vertical direction
(2)Positions of coupling's threaded installation holes at No 1 cylinder's beginning of injection
(3)B.T.D.C.: aa
(4)-
----------
aa=6deg
----------
a=(160deg)
----------
aa=6deg
----------
a=(160deg)
Information:
Connecting Rod
Use the 2H6782 Connecting Rod Boring Machine to recondition connecting rods and to check for connecting rod distortion. The 5P2009 Rework Group is available for the 2H6782 Connecting Rod Boring Machine. To install the rework group see Special Instruction GMG02394.Press a new piston pin bushing into the connecting rod. Assemble new rod bearings and the expansion sleeve. Tighten rod bolt nuts in the following step sequence.1. Put crankcase oil on bolt threads and seating faces of cap and nut.2. Tighten both nuts to 30 3 lb. ft. (40 4 N m).3. Put a mark on each nut and cap.4. Tighten each nut 60° from the mark.Clean spindle and slide the expansion sleeve and connecting rod into place. Install and tighten nut hand tight.Adjust the carrier to the distance between center of the bores, [center-to-center distance is 7.900 .001 in. (200.66 0.03 mm)]. Position the locating rods .25 in. (6.4 mm) from the connecting rod. Install front bushing in bracket and insert locating arbor through front bushing. Slide the centering sleeve over the end of the locating arbor. Slide the locating arbor through the rear bushing, centering sleeve, and into the connecting rod. Tighten knobs until locating rods lightly contact the connecting rod. Lock the locating rods and carrier.To check connecting rod distortion, slide locating arbor in and out of rear bushing. If the locating arbor does not slide freely, recheck horizontal location. If the locating arbor still binds, loosen the carrier clamp and raise or lower the carrier until the locating arbor slides freely. Read the vernier scale and note the variation from the nominal dimension. If the variation exceeds .010 in. (0.25 mm) the rod is distorted and should be replaced. Mark replacement rods for cylinder identification on bearing tab slot side of rod and cap.With the center-to-center distance set to the nominal dimension, set tool in boring bar and insert the boring bar and front bushing. Connect boring bar to the feed mechanism and engage the feed lever. Install the hand crank or an electric drill and flexible adapter and bore the bushing. Use a slow feed rate. Check the bore size. The size is 1.5010 .0003 in. (48.125 0.008 mm). A 5P2050 Connecting Rod Checking Fixture is available for checking connecting rods. For instructions for the use of the checking fixture see Special Instruction SMHS7366.Install connecting rod into piston with boss on rod on same side as crater in piston crown.
CONNECTING ROD AND PISTONWhen installing connecting rod and piston assemblies, inspect the threads of the rod bolts and nuts for damage. The contact surface of the nuts must be flat and free from damage. Damaged parts must be replaced.
Use the 2H6782 Connecting Rod Boring Machine to recondition connecting rods and to check for connecting rod distortion. The 5P2009 Rework Group is available for the 2H6782 Connecting Rod Boring Machine. To install the rework group see Special Instruction GMG02394.Press a new piston pin bushing into the connecting rod. Assemble new rod bearings and the expansion sleeve. Tighten rod bolt nuts in the following step sequence.1. Put crankcase oil on bolt threads and seating faces of cap and nut.2. Tighten both nuts to 30 3 lb. ft. (40 4 N m).3. Put a mark on each nut and cap.4. Tighten each nut 60° from the mark.Clean spindle and slide the expansion sleeve and connecting rod into place. Install and tighten nut hand tight.Adjust the carrier to the distance between center of the bores, [center-to-center distance is 7.900 .001 in. (200.66 0.03 mm)]. Position the locating rods .25 in. (6.4 mm) from the connecting rod. Install front bushing in bracket and insert locating arbor through front bushing. Slide the centering sleeve over the end of the locating arbor. Slide the locating arbor through the rear bushing, centering sleeve, and into the connecting rod. Tighten knobs until locating rods lightly contact the connecting rod. Lock the locating rods and carrier.To check connecting rod distortion, slide locating arbor in and out of rear bushing. If the locating arbor does not slide freely, recheck horizontal location. If the locating arbor still binds, loosen the carrier clamp and raise or lower the carrier until the locating arbor slides freely. Read the vernier scale and note the variation from the nominal dimension. If the variation exceeds .010 in. (0.25 mm) the rod is distorted and should be replaced. Mark replacement rods for cylinder identification on bearing tab slot side of rod and cap.With the center-to-center distance set to the nominal dimension, set tool in boring bar and insert the boring bar and front bushing. Connect boring bar to the feed mechanism and engage the feed lever. Install the hand crank or an electric drill and flexible adapter and bore the bushing. Use a slow feed rate. Check the bore size. The size is 1.5010 .0003 in. (48.125 0.008 mm). A 5P2050 Connecting Rod Checking Fixture is available for checking connecting rods. For instructions for the use of the checking fixture see Special Instruction SMHS7366.Install connecting rod into piston with boss on rod on same side as crater in piston crown.
CONNECTING ROD AND PISTONWhen installing connecting rod and piston assemblies, inspect the threads of the rod bolts and nuts for damage. The contact surface of the nuts must be flat and free from damage. Damaged parts must be replaced.