Information injection-pump assembly
ZEXEL
101603-8990
1016038990
ISUZU
8943906043
8943906043
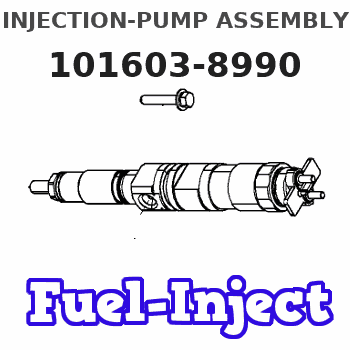
Rating:
Service parts 101603-8990 INJECTION-PUMP ASSEMBLY:
1.
_
7.
COUPLING PLATE
8.
_
9.
_
11.
Nozzle and Holder
8-94391-291-4
12.
Open Pre:MPa(Kqf/cm2)
16.2{165}/19.6{200}
14.
NOZZLE
Cross reference number
ZEXEL
101603-8990
1016038990
ISUZU
8943906043
8943906043
Zexel num
Bosch num
Firm num
Name
Calibration Data:
Adjustment conditions
Test oil
1404 Test oil ISO4113 or {SAEJ967d}
1404 Test oil ISO4113 or {SAEJ967d}
Test oil temperature
degC
40
40
45
Nozzle and nozzle holder
105780-8260
Bosch type code
9 430 610 133
Nozzle
105780-0120
Bosch type code
1 688 901 990
Nozzle holder
105780-2190
Opening pressure
MPa
18
Opening pressure
kgf/cm2
184
Injection pipe
Outer diameter - inner diameter - length (mm) mm 6-2-600
Outer diameter - inner diameter - length (mm) mm 6-2-600
Overflow valve
131424-8620
Overflow valve opening pressure
kPa
206
172
240
Overflow valve opening pressure
kgf/cm2
2.1
1.75
2.45
Tester oil delivery pressure
kPa
255
255
255
Tester oil delivery pressure
kgf/cm2
2.6
2.6
2.6
Direction of rotation (viewed from drive side)
Left L
Left L
Injection timing adjustment
Direction of rotation (viewed from drive side)
Left L
Left L
Injection order
1-5-3-6-
2-4
Pre-stroke
mm
3.8
3.75
3.85
Rack position
Point A R=A
Point A R=A
Beginning of injection position
Governor side NO.1
Governor side NO.1
Difference between angles 1
Cal 1-5 deg. 60 59.5 60.5
Cal 1-5 deg. 60 59.5 60.5
Difference between angles 2
Cal 1-3 deg. 120 119.5 120.5
Cal 1-3 deg. 120 119.5 120.5
Difference between angles 3
Cal 1-6 deg. 180 179.5 180.5
Cal 1-6 deg. 180 179.5 180.5
Difference between angles 4
Cyl.1-2 deg. 240 239.5 240.5
Cyl.1-2 deg. 240 239.5 240.5
Difference between angles 5
Cal 1-4 deg. 300 299.5 300.5
Cal 1-4 deg. 300 299.5 300.5
Injection quantity adjustment
Adjusting point
-
Rack position
14.5
Pump speed
r/min
850
850
850
Average injection quantity
mm3/st.
133.5
131.9
135.1
Max. variation between cylinders
%
0
-2.5
2.5
Basic
*
Fixing the rack
*
Standard for adjustment of the maximum variation between cylinders
*
Injection quantity adjustment_02
Adjusting point
Z
Rack position
9.5+-0.5
Pump speed
r/min
300
300
300
Average injection quantity
mm3/st.
15.5
14.2
16.8
Max. variation between cylinders
%
0
-14
14
Fixing the rack
*
Standard for adjustment of the maximum variation between cylinders
*
Injection quantity adjustment_03
Adjusting point
A
Rack position
R1(14.5)
Pump speed
r/min
850
850
850
Average injection quantity
mm3/st.
133.5
132.5
134.5
Basic
*
Fixing the lever
*
Injection quantity adjustment_04
Adjusting point
B
Rack position
(R1+1.05
)+0.05-0
.15
Pump speed
r/min
1450
1450
1450
Average injection quantity
mm3/st.
133
129.8
136.2
Fixing the lever
*
Timer adjustment
Remarks
Image
Image
Test data Ex:
Governor adjustment
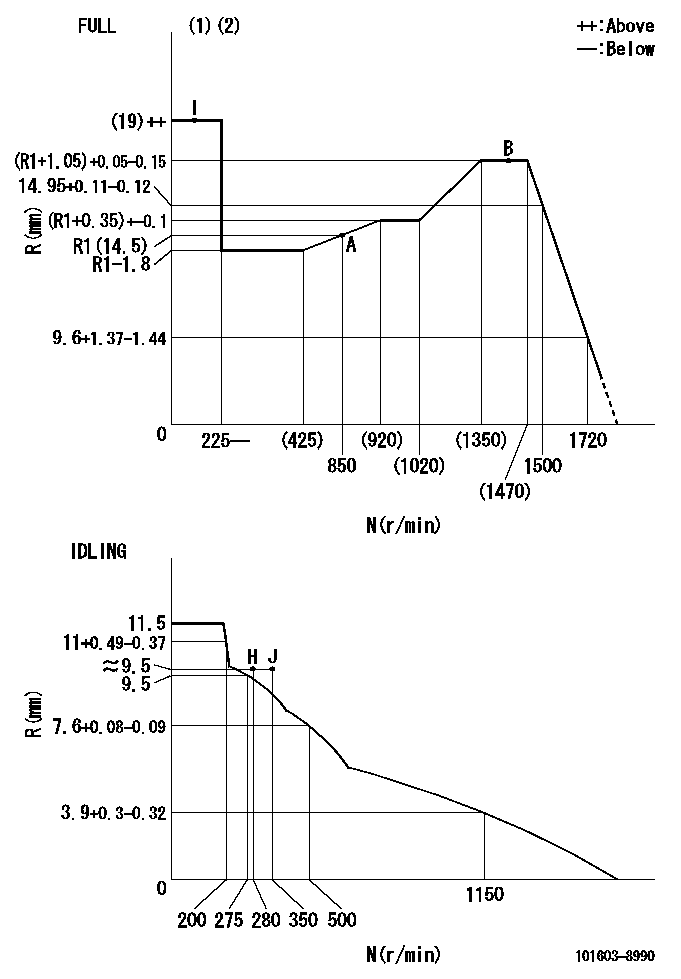
N:Pump speed
R:Rack position (mm)
(1)Torque cam stamping: T1
(2)Tolerance for racks not indicated: +-0.05mm.
----------
T1=N14
----------
----------
T1=N14
----------
Timer adjustment

(1)Adjusting range
(2)Step response time
(N): Speed of the pump
(L): Load
(theta) Advance angle
(Srd1) Step response time 1
(Srd2) Step response time 2
1. Adjusting conditions for the variable timer
(1)Adjust the clearance between the pickup and the protrusion to L.
----------
L=1-0.2mm N2=800r/min C2=(8deg) t1=2--sec. t2=2--sec.
----------
N1=1300++r/min P1=0kPa(0kgf/cm2) P2=392kPa(4kgf/cm2) C1=8+-0.3deg R01=0/4load R02=4/4load
----------
L=1-0.2mm N2=800r/min C2=(8deg) t1=2--sec. t2=2--sec.
----------
N1=1300++r/min P1=0kPa(0kgf/cm2) P2=392kPa(4kgf/cm2) C1=8+-0.3deg R01=0/4load R02=4/4load
Speed control lever angle
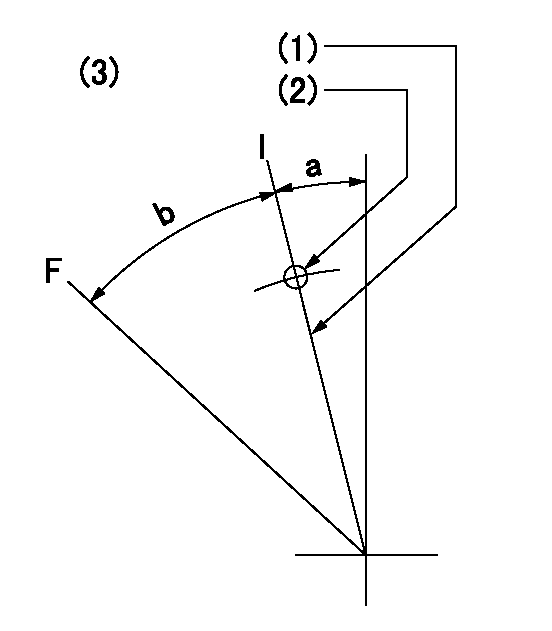
F:Full speed
I:Idle
(1)Stopper bolt set position 'H'
(2)Use the pin at R = aa
(3)Viewed from feed pump side.
----------
aa=35mm
----------
a=10deg+-5deg b=41deg+-3deg
----------
aa=35mm
----------
a=10deg+-5deg b=41deg+-3deg
Stop lever angle
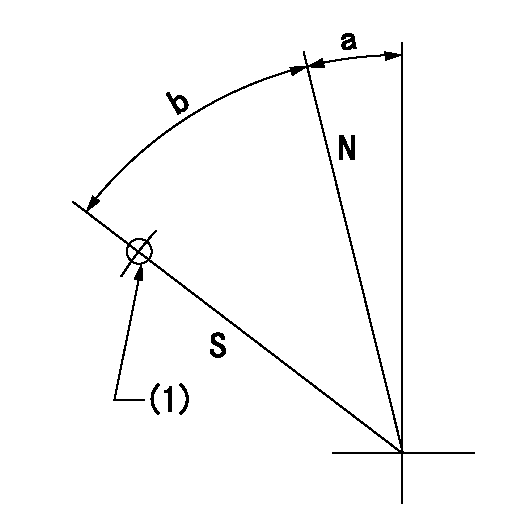
N:Pump normal
S:Stop the pump.
(1)Use the pin at R = aa
----------
aa=45mm
----------
a=12.5deg+-5deg b=40deg+-5deg
----------
aa=45mm
----------
a=12.5deg+-5deg b=40deg+-5deg
0000001501 RACK SENSOR

Rack sensor adjustment
1. Flange type rack sensor (rack sensor adjustment -5*20)
(1)These types of rack sensors do not need adjustment. Confirm the performance with the following procedures.
(2)Mount the rack sensor main body to the pump main body.
(3)Fix the pump lever at full.
(4)At supply voltage V1, pump speed N1 and rack position Ra, confirm that the amp's output voltage is Vist.
(5)Move the pump lever two or three times.
(6)Set again to full.
(7)Confirm that the amplifier output voltage is Vist.
(8)Fix the caution plate to the upper part of the rack sensor.
(For those without the caution plate instructions, make sure the nameplate of the rack sensor carries the "Don't hold here" caution.)
(9)Apply red paint to the rack sensor mounting bolts (2 places).
----------
V1=5+-0.01V N1=850r/min Ra=R1(14.5)mm Vist=3.74+-0.28V
----------
----------
V1=5+-0.01V N1=850r/min Ra=R1(14.5)mm Vist=3.74+-0.28V
----------
Timing setting

(1)Pump vertical direction
(2)Positions of coupling's threaded installation holes at No 1 cylinder's beginning of injection
(3)B.T.D.C.: aa
(4)-
----------
aa=6deg
----------
a=(160deg)
----------
aa=6deg
----------
a=(160deg)
Information:
Cylinder Head And Valve Components
Check cylinder head for cracks before reconditioning.Flatness of the cylinder head should be within .006 in. (0.15 mm) total, and a maximum of .003 in. (0.08 mm) for any 6 in. (152.4 mm) span. A maximum stock removal of .010 in. (0.25 mm) is permissible when resurfacing the head.Always check the thickness of a cylinder head before resurfacing. The cylinder head may have been resurfaced before and would not have enough stock to be resurfaced again.To check the thickness of a cylinder head, measure through the fuel injection nozzle holes at each end of the cylinder head. For the correct thickness of the cylinder head, see the topic CYLINDER HEAD in the SPECIFICATIONS.The exhaust valve seats have replaceable inserts. To remove, use the 8S7170 Valve Seat Insert Puller Group.
REMOVING EXHAUST VALVE SEAT INSERTFreeze the exhaust valve seat inserts or use the 8S7170 Valve Seat Insert Puller Group to install inserts into head. Be sure bores are clean, free of burrs, and the insert has a good press fit into the bore.After inserts are installed, grind the seat face of the insert to be sure it is flat, has the correct angle, and is in alignment with the bore in the valve guide. For specifications, see VALVE GRINDING SPECIFICATIONS CHART. Replace exhaust valve seat inserts when valve seat width or valve head-to-cylinder head face cannot be machined to the correct specification. For specifications, see VALVE GRINDING SPECIFICATIONS CHART.A 2N8943 Valve Seat Insert for the intake valve is available. This insert can be used in the repair of cylinder heads which have an intake valve seat with damage. Before, damage to an intake valve seat made replacement of the cylinder head assembly necessary.To use a 2N8943 Valve Seat Insert, the inlet port of the cylinder head must be machined to a diameter of 2.1470 .0005 in. (54.534 0.013 mm) and to a depth of .442 .002 in. (11.23 0.05 mm).To install a 2N8943 Valve Seat Insert into the cylinder head, freeze the insert or use a 2P2343 Extractor with the 8S7170 Valve Seat Insert Puller Group. After an insert is installed, grind the seat face of the insert to be sure it is flat, has the correct angle, and is in alignment with the bore in the valve guide. For specifications, see VALVE GRINDING SPECIFICATIONS CHART.Clean valve guides of all carbon and oil, using the 5P5176 Brush and a solvent.The valve guides are cast in the cylinder heads. Check each valve guide bore size 3/4 in. (19.1 mm) deep from each end. The bore size is .3745 .0005 in. (9.512 0.013 mm) and the maximum size worn is .3760 in. (9.550 mm). Valve guides worn more than the maximum wear size, can be restored to original tolerances through knurling.Use the 5P3536 Valve Guide Gauge Group to check the bore of the valve guides. Special Instructions GMG02562 gives complete and detailed instructions for use of the 5P3536 Valve Guide Gauge Group.
USING
Check cylinder head for cracks before reconditioning.Flatness of the cylinder head should be within .006 in. (0.15 mm) total, and a maximum of .003 in. (0.08 mm) for any 6 in. (152.4 mm) span. A maximum stock removal of .010 in. (0.25 mm) is permissible when resurfacing the head.Always check the thickness of a cylinder head before resurfacing. The cylinder head may have been resurfaced before and would not have enough stock to be resurfaced again.To check the thickness of a cylinder head, measure through the fuel injection nozzle holes at each end of the cylinder head. For the correct thickness of the cylinder head, see the topic CYLINDER HEAD in the SPECIFICATIONS.The exhaust valve seats have replaceable inserts. To remove, use the 8S7170 Valve Seat Insert Puller Group.
REMOVING EXHAUST VALVE SEAT INSERTFreeze the exhaust valve seat inserts or use the 8S7170 Valve Seat Insert Puller Group to install inserts into head. Be sure bores are clean, free of burrs, and the insert has a good press fit into the bore.After inserts are installed, grind the seat face of the insert to be sure it is flat, has the correct angle, and is in alignment with the bore in the valve guide. For specifications, see VALVE GRINDING SPECIFICATIONS CHART. Replace exhaust valve seat inserts when valve seat width or valve head-to-cylinder head face cannot be machined to the correct specification. For specifications, see VALVE GRINDING SPECIFICATIONS CHART.A 2N8943 Valve Seat Insert for the intake valve is available. This insert can be used in the repair of cylinder heads which have an intake valve seat with damage. Before, damage to an intake valve seat made replacement of the cylinder head assembly necessary.To use a 2N8943 Valve Seat Insert, the inlet port of the cylinder head must be machined to a diameter of 2.1470 .0005 in. (54.534 0.013 mm) and to a depth of .442 .002 in. (11.23 0.05 mm).To install a 2N8943 Valve Seat Insert into the cylinder head, freeze the insert or use a 2P2343 Extractor with the 8S7170 Valve Seat Insert Puller Group. After an insert is installed, grind the seat face of the insert to be sure it is flat, has the correct angle, and is in alignment with the bore in the valve guide. For specifications, see VALVE GRINDING SPECIFICATIONS CHART.Clean valve guides of all carbon and oil, using the 5P5176 Brush and a solvent.The valve guides are cast in the cylinder heads. Check each valve guide bore size 3/4 in. (19.1 mm) deep from each end. The bore size is .3745 .0005 in. (9.512 0.013 mm) and the maximum size worn is .3760 in. (9.550 mm). Valve guides worn more than the maximum wear size, can be restored to original tolerances through knurling.Use the 5P3536 Valve Guide Gauge Group to check the bore of the valve guides. Special Instructions GMG02562 gives complete and detailed instructions for use of the 5P3536 Valve Guide Gauge Group.
USING