Information injection-pump assembly
ZEXEL
101603-8820
1016038820
ISUZU
8943958120
8943958120
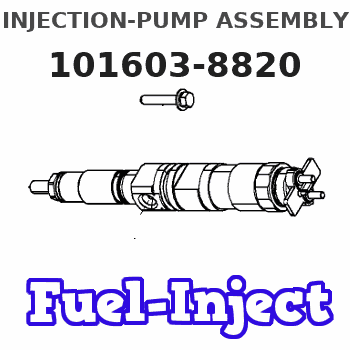
Rating:
Service parts 101603-8820 INJECTION-PUMP ASSEMBLY:
1.
_
7.
COUPLING PLATE
8.
_
9.
_
11.
Nozzle and Holder
8-94395-511-1
12.
Open Pre:MPa(Kqf/cm2)
18.1{185}
15.
NOZZLE SET
Cross reference number
ZEXEL
101603-8820
1016038820
ISUZU
8943958120
8943958120
Zexel num
Bosch num
Firm num
Name
Calibration Data:
Adjustment conditions
Test oil
1404 Test oil ISO4113 or {SAEJ967d}
1404 Test oil ISO4113 or {SAEJ967d}
Test oil temperature
degC
40
40
45
Nozzle and nozzle holder
105780-8140
Bosch type code
EF8511/9A
Nozzle
105780-0000
Bosch type code
DN12SD12T
Nozzle holder
105780-2080
Bosch type code
EF8511/9
Opening pressure
MPa
17.2
Opening pressure
kgf/cm2
175
Injection pipe
Outer diameter - inner diameter - length (mm) mm 6-2-600
Outer diameter - inner diameter - length (mm) mm 6-2-600
Overflow valve
131424-4920
Overflow valve opening pressure
kPa
127
107
147
Overflow valve opening pressure
kgf/cm2
1.3
1.1
1.5
Tester oil delivery pressure
kPa
157
157
157
Tester oil delivery pressure
kgf/cm2
1.6
1.6
1.6
Direction of rotation (viewed from drive side)
Left L
Left L
Injection timing adjustment
Direction of rotation (viewed from drive side)
Left L
Left L
Injection order
1-5-3-6-
2-4
Pre-stroke
mm
3.4
3.35
3.45
Beginning of injection position
Governor side NO.1
Governor side NO.1
Difference between angles 1
Cal 1-5 deg. 60 59.5 60.5
Cal 1-5 deg. 60 59.5 60.5
Difference between angles 2
Cal 1-3 deg. 120 119.5 120.5
Cal 1-3 deg. 120 119.5 120.5
Difference between angles 3
Cal 1-6 deg. 180 179.5 180.5
Cal 1-6 deg. 180 179.5 180.5
Difference between angles 4
Cyl.1-2 deg. 240 239.5 240.5
Cyl.1-2 deg. 240 239.5 240.5
Difference between angles 5
Cal 1-4 deg. 300 299.5 300.5
Cal 1-4 deg. 300 299.5 300.5
Injection quantity adjustment
Adjusting point
-
Rack position
10.7
Pump speed
r/min
850
850
850
Average injection quantity
mm3/st.
53
51.4
54.6
Max. variation between cylinders
%
0
-2.5
2.5
Basic
*
Fixing the rack
*
Standard for adjustment of the maximum variation between cylinders
*
Injection quantity adjustment_02
Adjusting point
-
Rack position
9.7+-0.5
Pump speed
r/min
275
275
275
Average injection quantity
mm3/st.
9.4
8.1
10.7
Max. variation between cylinders
%
0
-14
14
Fixing the rack
*
Standard for adjustment of the maximum variation between cylinders
*
Remarks
Adjust only variation between cylinders; adjust governor according to governor specifications.
Adjust only variation between cylinders; adjust governor according to governor specifications.
Injection quantity adjustment_03
Adjusting point
A
Rack position
R1(10.7)
Pump speed
r/min
850
850
850
Average injection quantity
mm3/st.
53
52
54
Basic
*
Fixing the lever
*
Injection quantity adjustment_04
Adjusting point
B
Rack position
R1+0.1
Pump speed
r/min
1400
1400
1400
Average injection quantity
mm3/st.
64.5
60.5
68.5
Fixing the lever
*
Injection quantity adjustment_05
Adjusting point
C
Rack position
R1+0.45
Pump speed
r/min
600
600
600
Average injection quantity
mm3/st.
48.7
45.5
51.9
Fixing the lever
*
Injection quantity adjustment_06
Adjusting point
I
Rack position
-
Pump speed
r/min
150
150
150
Average injection quantity
mm3/st.
130
130
138
Fixing the lever
*
Rack limit
*
Timer adjustment
Pump speed
r/min
550--
Advance angle
deg.
0
0
0
Remarks
Start
Start
Timer adjustment_02
Pump speed
r/min
500
Advance angle
deg.
0.5
Timer adjustment_03
Pump speed
r/min
1000
Advance angle
deg.
3
2.5
3.5
Remarks
Finish
Finish
Test data Ex:
Governor adjustment
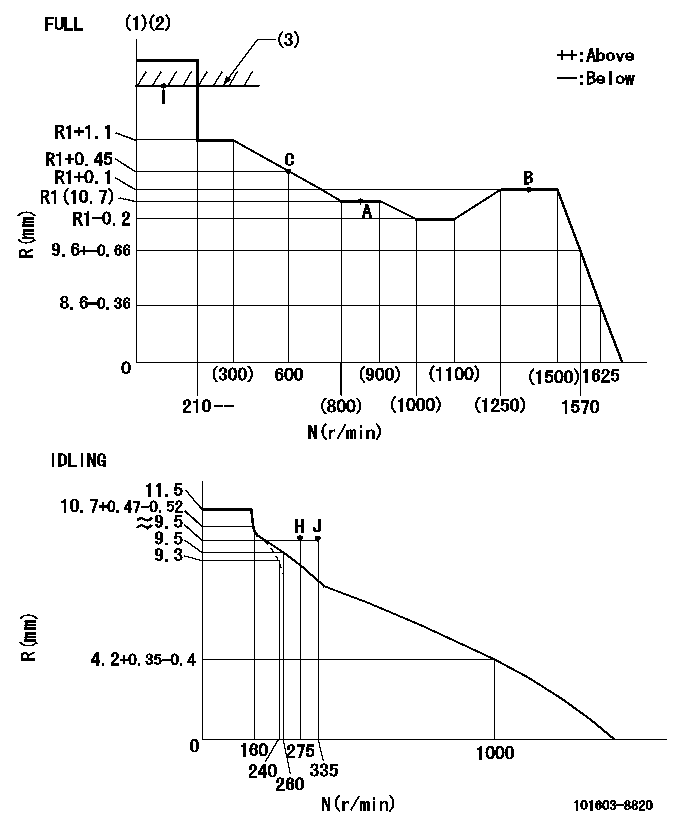
N:Pump speed
R:Rack position (mm)
(1)Torque cam stamping: T1
(2)Tolerance for racks not indicated: +-0.05mm.
(3)RACK LIMIT
----------
T1=K58
----------
----------
T1=K58
----------
Speed control lever angle
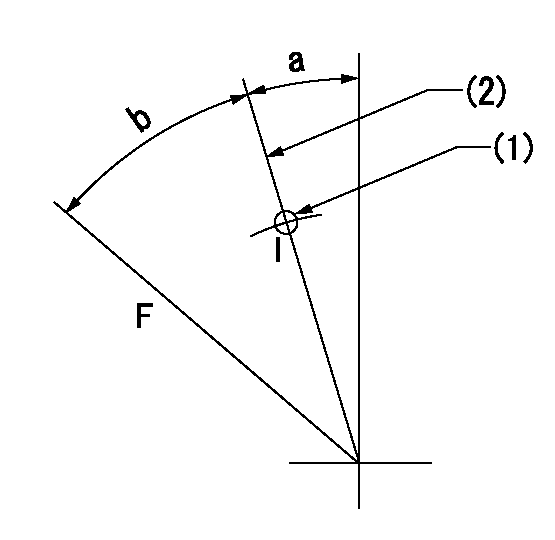
F:Full speed
I:Idle
(1)Use the pin at R = aa
(2)Stopper bolt set position 'H'
----------
aa=35mm
----------
a=11deg+-5deg b=37deg+-3deg
----------
aa=35mm
----------
a=11deg+-5deg b=37deg+-3deg
Stop lever angle
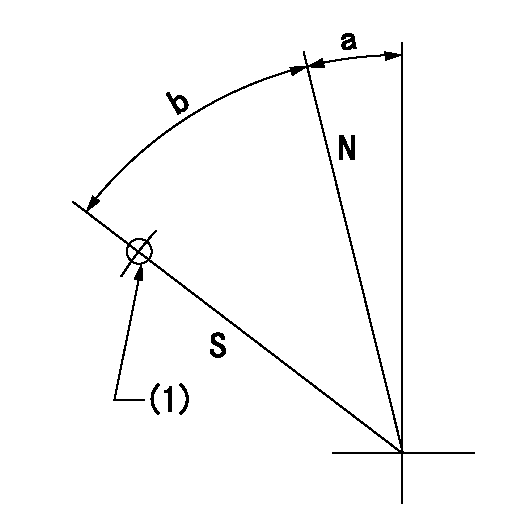
N:Pump normal
S:Stop the pump.
(1)Use the pin at R = aa
----------
aa=45mm
----------
a=12.5deg+-5deg b=40deg+-5deg
----------
aa=45mm
----------
a=12.5deg+-5deg b=40deg+-5deg
0000001501 ACS

(A) Housing
(B) Snap ring
(C) adjusting screw
(D) Set screw
(E): Push rod
(F) Spacer
1. Adjustment of the aneroid compensator
(1)Adjust with the (D) set screw so that the clearance between the (A) housing and (B) snap ring is L1.
(2)Select the push rod (E) so that the distance from the end surface of the (F) spacer becomes L2.
(3)(C) Turn the screw to adjust the beginning of aneroid compensator operation.
2. Adjustment when mounting the governor.
(1)Set the speed of the pump to N1 r/min and fix the control lever at the full set position.
(2)Adjust using screw C to obtain the performance shown in the graph above.
(3)After final adjustment, confirm that the gap between housing (A) and snapring (B) is L3.
----------
N1=850r/min L1=1.4~1.7mm L2=0.5+-0.5mm L3=(0.1~0.5)mm
----------
Ra=R1(10.7)mm Rb=R1-0.9mm Pa=89.8+-2.7kPa(674+-20mmHg) Pb=70.1+-0.7kPa(526+-5mmHg) Q1=53+-1cm3/1000st Q2=(34)+-1.6cm3/1000st
----------
N1=850r/min L1=1.4~1.7mm L2=0.5+-0.5mm L3=(0.1~0.5)mm
----------
Ra=R1(10.7)mm Rb=R1-0.9mm Pa=89.8+-2.7kPa(674+-20mmHg) Pb=70.1+-0.7kPa(526+-5mmHg) Q1=53+-1cm3/1000st Q2=(34)+-1.6cm3/1000st
Timing setting

(1)Pump vertical direction
(2)Position of timer's threaded hole at No 1 cylinder's beginning of injection
(3)B.T.D.C.: aa
(4)-
----------
aa=14deg
----------
a=(160deg)
----------
aa=14deg
----------
a=(160deg)
Information:
INJECTION NOZZLE (Right side illustrated)
1. Lines (eight, four each side). 2. Injection nozzles (eight, four each side). 3. Clamps (eight, four each side).4. Remove the adapter (4) and lift injection nozzle (2) out of the cylinder head.
ADAPTER AND NOZZLE REMOVAL
2. Injection nozzle. 4. Adapter. 5. O-ring seal. 6. O-ring seal.
Pull nozzle straight out, by hand, to remove. Slight twisting action is permissible if necessary. Never pry out a nozzle with a screwdriver or other similar tool.
Always replace O-ring seals (5) and (6) before installing nozzle.5. Use needle-nose pliers to remove carbon seal dam (8). Always install a new compression seal (7) and carbon seal dam (8) before installing injection nozzle.
REMOVING CARBON SEAL DAM (Typical Example)
7. Compression seal. 8. Carbon seal dam.Install Fuel Injection Nozzles
1. Be sure the bore in the cylinder head and fuel inlet fittings are clean.
Never install an injection nozzle that has been dropped, without first testing it with the 8S2242 Nozzle Tester Group. The injector tips are very hard and brittle and break easily.
2. Install a new compression seal and carbon seal dam. Use carbon seal dam installation tool (9) to install the carbon seal dam.
INSTALLING CARBON SEAL DAM (Typical Example)
9. 8S2252 Carbon Seal Dam Installation Tool.3. Install a new O-ring seal (6) on the injection nozzle (2) and a new O-ring seal (5) on the adapter (4).4. Install the injection nozzle (2) into the cylinder head using a twisting motion. Do not use lubricant in the cylinder head bore or on the nozzle body.
INSTALLING NOZZLE
2. Injection nozzle. 4. Adapter. 5. O-ring seal. 6. O-ring seal.
Do not bend the injector inlet connection when installing injector into cylinder head. Bending of the inlet connection creates tension on the injector and causes binding of the needle in the guide.
5. Install the adapter (4) and tighten the injection nozzle-to-adapter retaining nut. Tighten retaining nut to 30 5 lb. ft. (4.1 0.7 mkg). Hand tighten the fuel injection line.6. Install the injection nozzle clamp.7. Install the fuel return manifold and rocker arm assembly. Install retaining bolts and locks. Tighten bolts to 18 5 lb. ft. (2.5 0.7 mkg) and bend locks.8. Adjust the intake valve clearance to .015 in. (0.38 mm) and the exhaust valve clearance to .025 in. (0.64 mm).9. Install valve cover. Install mounting bolts and tighten to 120 24 lb. in. (138 28 cm.kg).10. Purge the fuel lines of air by motoring the engine until fuel, free of air, flows from the connections.11. Use 5P144 Fuel Line Socket to tighten the fuel line connections to 30 5 lb. ft. (4.1 0.7 mkg).12. Start the engine and correct any fuel leaks that may occur.