Information injection-pump assembly
BOSCH
9 400 610 668
9400610668
ZEXEL
101603-8630
1016038630
ISUZU
8943959070
8943959070
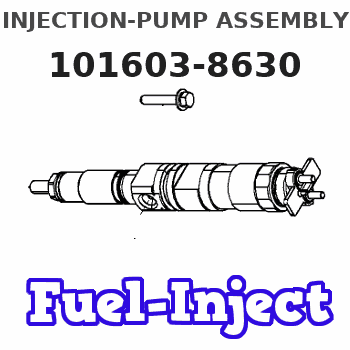
Rating:
Service parts 101603-8630 INJECTION-PUMP ASSEMBLY:
1.
_
7.
COUPLING PLATE
8.
_
9.
_
11.
Nozzle and Holder
8-94393-335-1
12.
Open Pre:MPa(Kqf/cm2)
16.2{165}/18.1{185}
15.
NOZZLE SET
Cross reference number
BOSCH
9 400 610 668
9400610668
ZEXEL
101603-8630
1016038630
ISUZU
8943959070
8943959070
Zexel num
Bosch num
Firm num
Name
9 400 610 668
8943959070 ISUZU
INJECTION-PUMP ASSEMBLY
6HH1-N K 14BF INJECTION PUMP ASSY PE6AD PE
6HH1-N K 14BF INJECTION PUMP ASSY PE6AD PE
Calibration Data:
Adjustment conditions
Test oil
1404 Test oil ISO4113 or {SAEJ967d}
1404 Test oil ISO4113 or {SAEJ967d}
Test oil temperature
degC
40
40
45
Nozzle and nozzle holder
105780-8140
Bosch type code
EF8511/9A
Nozzle
105780-0000
Bosch type code
DN12SD12T
Nozzle holder
105780-2080
Bosch type code
EF8511/9
Opening pressure
MPa
17.2
Opening pressure
kgf/cm2
175
Injection pipe
Outer diameter - inner diameter - length (mm) mm 6-2-600
Outer diameter - inner diameter - length (mm) mm 6-2-600
Overflow valve
131424-4920
Overflow valve opening pressure
kPa
127
107
147
Overflow valve opening pressure
kgf/cm2
1.3
1.1
1.5
Tester oil delivery pressure
kPa
157
157
157
Tester oil delivery pressure
kgf/cm2
1.6
1.6
1.6
Direction of rotation (viewed from drive side)
Left L
Left L
Injection timing adjustment
Direction of rotation (viewed from drive side)
Left L
Left L
Injection order
1-5-3-6-
2-4
Pre-stroke
mm
4.2
4.15
4.25
Rack position
After adjusting injection quantity. R=A
After adjusting injection quantity. R=A
Beginning of injection position
Governor side NO.1
Governor side NO.1
Difference between angles 1
Cal 1-5 deg. 60 59.5 60.5
Cal 1-5 deg. 60 59.5 60.5
Difference between angles 2
Cal 1-3 deg. 120 119.5 120.5
Cal 1-3 deg. 120 119.5 120.5
Difference between angles 3
Cal 1-6 deg. 180 179.5 180.5
Cal 1-6 deg. 180 179.5 180.5
Difference between angles 4
Cyl.1-2 deg. 240 239.5 240.5
Cyl.1-2 deg. 240 239.5 240.5
Difference between angles 5
Cal 1-4 deg. 300 299.5 300.5
Cal 1-4 deg. 300 299.5 300.5
Injection quantity adjustment
Adjusting point
-
Rack position
11.4
Pump speed
r/min
850
850
850
Average injection quantity
mm3/st.
77
75.4
78.6
Max. variation between cylinders
%
0
-2.5
2.5
Basic
*
Fixing the rack
*
Standard for adjustment of the maximum variation between cylinders
*
Injection quantity adjustment_02
Adjusting point
-
Rack position
9.6+-0.5
Pump speed
r/min
275
275
275
Average injection quantity
mm3/st.
9.4
8.1
10.7
Max. variation between cylinders
%
0
-14
14
Fixing the rack
*
Standard for adjustment of the maximum variation between cylinders
*
Remarks
Adjust only variation between cylinders; adjust governor according to governor specifications.
Adjust only variation between cylinders; adjust governor according to governor specifications.
Injection quantity adjustment_03
Adjusting point
A
Rack position
R1(11.4)
Pump speed
r/min
850
850
850
Average injection quantity
mm3/st.
77
76
78
Basic
*
Fixing the lever
*
Injection quantity adjustment_04
Adjusting point
B
Rack position
R1-0.4
Pump speed
r/min
1400
1400
1400
Average injection quantity
mm3/st.
77
73
81
Fixing the lever
*
Injection quantity adjustment_05
Adjusting point
C
Rack position
R1(11.4)
Pump speed
r/min
600
600
600
Average injection quantity
mm3/st.
66.5
63.3
69.7
Fixing the lever
*
Injection quantity adjustment_06
Adjusting point
I
Rack position
-
Pump speed
r/min
150
150
150
Average injection quantity
mm3/st.
95
95
127
Fixing the lever
*
Timer adjustment
Pump speed
r/min
(1130)
Advance angle
deg.
0
0
0
Remarks
Start
Start
Timer adjustment_02
Pump speed
r/min
1200
Advance angle
deg.
1.5
1
2
Timer adjustment_03
Pump speed
r/min
1350
Advance angle
deg.
5.5
5
6
Remarks
Finish
Finish
Test data Ex:
Governor adjustment
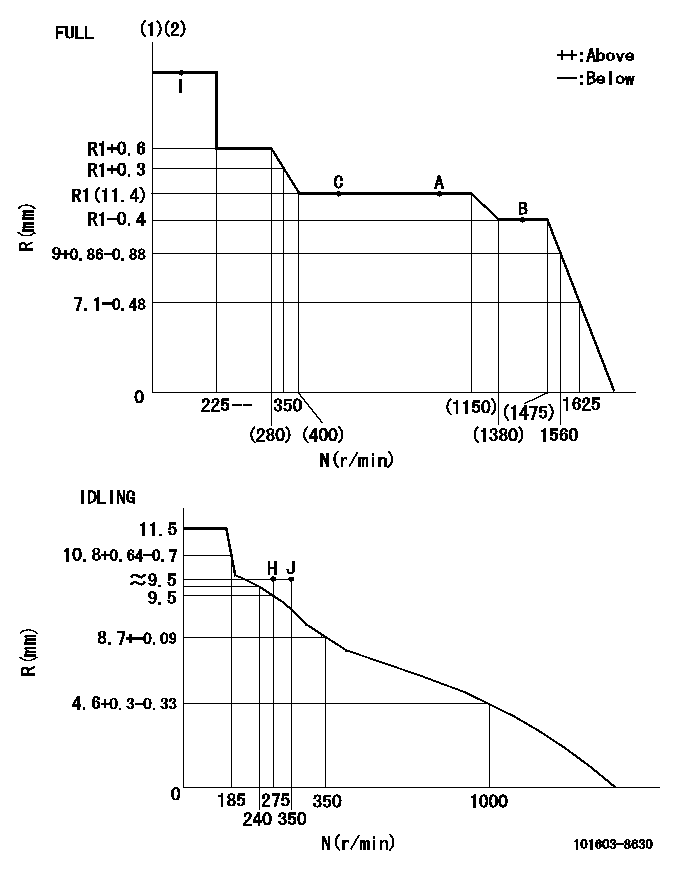
N:Pump speed
R:Rack position (mm)
(1)Torque cam stamping: T1
(2)Tolerance for racks not indicated: +-0.05mm.
----------
T1=K51
----------
----------
T1=K51
----------
Speed control lever angle
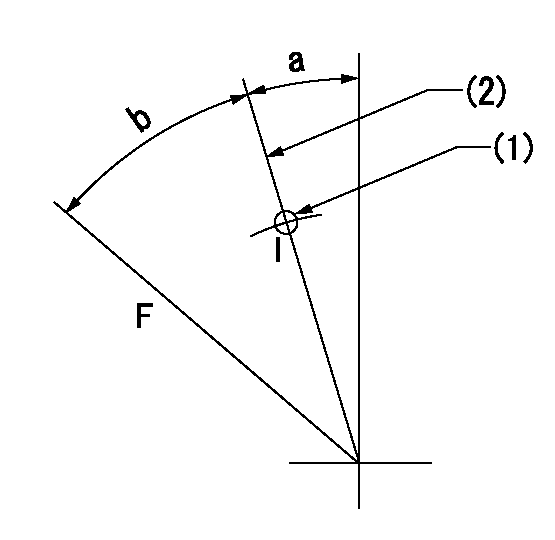
F:Full speed
I:Idle
(1)Use the pin at R = aa
(2)Stopper bolt set position 'H'
----------
aa=35mm
----------
a=12deg+-5deg b=35.5deg+-3deg
----------
aa=35mm
----------
a=12deg+-5deg b=35.5deg+-3deg
Stop lever angle
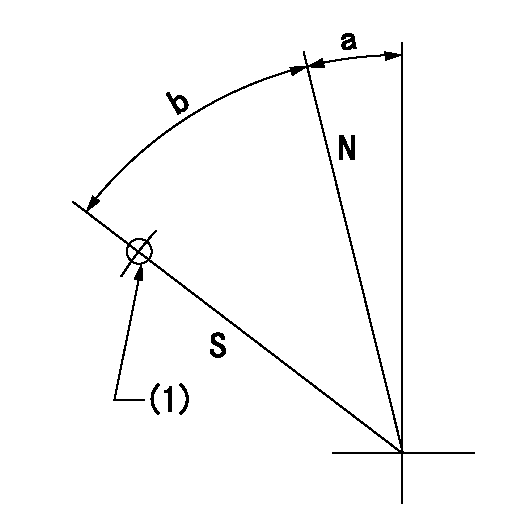
N:Pump normal
S:Stop the pump.
(1)Use the pin at R = aa
----------
aa=45mm
----------
a=12.5deg+-5deg b=40deg+-5deg
----------
aa=45mm
----------
a=12.5deg+-5deg b=40deg+-5deg
0000001501 I/P WITH LOAD PLUNGER ADJ
Plunger assembly number: PL (stamping: ST)
1. Adjustment procedures
(1)Insert the pre-stroke adjusting shims L1 for each cylinder.
(2)Adjust injection quantity.(max. var. bet. cyl. idling a1, full a2)
(3)At basic point A, adjust so that the pre-stroke is L2.
(4)Reconfirm the injection quantity.
----------
PL=131153-4520 ST=A724 L1=1mm L2=4.2+-0.05mm a1=+-14% a2=+-2.5%
----------
----------
PL=131153-4520 ST=A724 L1=1mm L2=4.2+-0.05mm a1=+-14% a2=+-2.5%
----------
Timing setting

(1)Pump vertical direction
(2)Position of timer's threaded hole at No 1 cylinder's beginning of injection
(3)B.T.D.C.: aa
(4)At rack position = bb
----------
aa=5deg bb=R1(11.4)mm
----------
a=(150deg)
----------
aa=5deg bb=R1(11.4)mm
----------
a=(150deg)
Information:
start by:a) remove turbocharger 1. Put the turbocharger in position on tool (A).2. Put a mark on the compressor cover and housings for installation purpose.3. Remove bolts (1) and plates from compressor housing.4. Remove the compressor housing. 5. Remove bolts (2) and locks from turbine housing. 6. Remove cartridge (3) from turbine housing.7. Install tool (B) in tool (C). Install cartridge in tool (C).8. Remove nut (4) from the compressor wheel.
When the nut is loosened, do not put a side force on the shaft.
9. Install tool (D) on an oil heater. Heat the oil to 350°F (177°C). Install the cartridge on tool (D) with only the compressor wheel in the hot oil. Keep the compressor wheel in the hot oil for ten minutes. 10. Put tool (D) and cartridge on tool (E) under a press. Install driver (F) and push the shaft out of the compressor wheel. Step 10 must be done before the compressor wheel gets cold.11. Remove compressor wheel and shroud. Remove turbine wheel and shaft. 12. Remove the four bolts (5) and locks from plate (6). 13. Remove plate (6), spacer, collar and thrust bearing from cartridge.14. Remove seal from plate and ring from spacer. 15. Remove bearing (7), washer (11) and snap ring (8) from compressor side of cartridge.16. Remove snap ring (13), washer (10), bearing (12) and snap ring (9) from turbine side of cartridge.17. Check all the parts of the turbocharger for damage. If the parts have damage, use new parts for replacement. See SPECIAL INSTRUCTION, Form No. SMHS6854 for TURBOCHARGER RECONDITIONING. Also see GUIDELINE FOR REUSABLE PARTS, Form No. SEBF8018.Assemble Turbocharger (Airesearch T18)
1. Make sure all oil passages are open and clean. Put clean engine oil on all parts before assembly 2. Install snap ring (6), bearing (3), washer (7) and snap ring (4) in turbine side of cartridge. Install the two snap rings with tool (A). Install the snap rings with the rounded edge toward the bearing.3. Install snap ring (2), washer (5) and bearing (1) in compressor side of cartridge. 4. Install seal (12) on plate (8) and ring (9) on spacer.5. Install collar (10) in plate and spacer (11) in collar. 6. Install thrust bearing (13) with the three radial grooves toward the outside.7. Install plate (8), bolts and locks. Tighten bolts to a torque of 35 5 lb. in. (4.0 0.6 N m). Put 6V2055 High Vacuum Grease in the groove for seal ring (14) at assembly to one half or more of the depth of the groove all the way around.8. Install ring (14) on turbine wheel.9. Install turbine wheel and shaft in cartridge. Be careful not to break ring (14) when installing shaft. 10. Put cartridge on tool (C) and tool (C) on tool (B). Some compressor wheels (15) can be installed at room temperature. If the compressor wheel will go on the turbine shaft freely to within .31 in. (7.9 mm) of the seal carrier the compressor wheel can be installed at
When the nut is loosened, do not put a side force on the shaft.
9. Install tool (D) on an oil heater. Heat the oil to 350°F (177°C). Install the cartridge on tool (D) with only the compressor wheel in the hot oil. Keep the compressor wheel in the hot oil for ten minutes. 10. Put tool (D) and cartridge on tool (E) under a press. Install driver (F) and push the shaft out of the compressor wheel. Step 10 must be done before the compressor wheel gets cold.11. Remove compressor wheel and shroud. Remove turbine wheel and shaft. 12. Remove the four bolts (5) and locks from plate (6). 13. Remove plate (6), spacer, collar and thrust bearing from cartridge.14. Remove seal from plate and ring from spacer. 15. Remove bearing (7), washer (11) and snap ring (8) from compressor side of cartridge.16. Remove snap ring (13), washer (10), bearing (12) and snap ring (9) from turbine side of cartridge.17. Check all the parts of the turbocharger for damage. If the parts have damage, use new parts for replacement. See SPECIAL INSTRUCTION, Form No. SMHS6854 for TURBOCHARGER RECONDITIONING. Also see GUIDELINE FOR REUSABLE PARTS, Form No. SEBF8018.Assemble Turbocharger (Airesearch T18)
1. Make sure all oil passages are open and clean. Put clean engine oil on all parts before assembly 2. Install snap ring (6), bearing (3), washer (7) and snap ring (4) in turbine side of cartridge. Install the two snap rings with tool (A). Install the snap rings with the rounded edge toward the bearing.3. Install snap ring (2), washer (5) and bearing (1) in compressor side of cartridge. 4. Install seal (12) on plate (8) and ring (9) on spacer.5. Install collar (10) in plate and spacer (11) in collar. 6. Install thrust bearing (13) with the three radial grooves toward the outside.7. Install plate (8), bolts and locks. Tighten bolts to a torque of 35 5 lb. in. (4.0 0.6 N m). Put 6V2055 High Vacuum Grease in the groove for seal ring (14) at assembly to one half or more of the depth of the groove all the way around.8. Install ring (14) on turbine wheel.9. Install turbine wheel and shaft in cartridge. Be careful not to break ring (14) when installing shaft. 10. Put cartridge on tool (C) and tool (C) on tool (B). Some compressor wheels (15) can be installed at room temperature. If the compressor wheel will go on the turbine shaft freely to within .31 in. (7.9 mm) of the seal carrier the compressor wheel can be installed at