Information injection-pump assembly
BOSCH
F 019 Z10 363
f019z10363
ZEXEL
101603-8241
1016038241
ISUZU
8943937531
8943937531
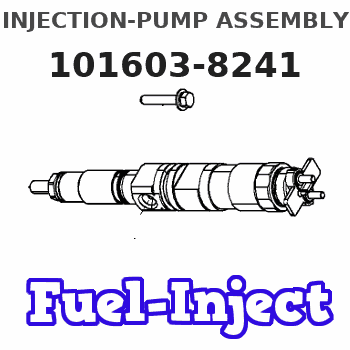
Rating:
Service parts 101603-8241 INJECTION-PUMP ASSEMBLY:
1.
_
7.
COUPLING PLATE
8.
_
9.
_
11.
Nozzle and Holder
8-94394-906-0
12.
Open Pre:MPa(Kqf/cm2)
18.1{185}/22.1{225}
14.
NOZZLE
Cross reference number
BOSCH
F 019 Z10 363
f019z10363
ZEXEL
101603-8241
1016038241
ISUZU
8943937531
8943937531
Zexel num
Bosch num
Firm num
Name
Calibration Data:
Adjustment conditions
Test oil
1404 Test oil ISO4113 or {SAEJ967d}
1404 Test oil ISO4113 or {SAEJ967d}
Test oil temperature
degC
40
40
45
Nozzle and nozzle holder
105780-8140
Bosch type code
EF8511/9A
Nozzle
105780-0000
Bosch type code
DN12SD12T
Nozzle holder
105780-2080
Bosch type code
EF8511/9
Opening pressure
MPa
17.2
Opening pressure
kgf/cm2
175
Injection pipe
Outer diameter - inner diameter - length (mm) mm 6-2-600
Outer diameter - inner diameter - length (mm) mm 6-2-600
Overflow valve
132424-0620
Overflow valve opening pressure
kPa
157
123
191
Overflow valve opening pressure
kgf/cm2
1.6
1.25
1.95
Tester oil delivery pressure
kPa
157
157
157
Tester oil delivery pressure
kgf/cm2
1.6
1.6
1.6
Direction of rotation (viewed from drive side)
Left L
Left L
Injection timing adjustment
Direction of rotation (viewed from drive side)
Left L
Left L
Injection order
1-5-3-6-
2-4
Pre-stroke
mm
3.5
3.45
3.55
Rack position
Point A R=A
Point A R=A
Beginning of injection position
Governor side NO.1
Governor side NO.1
Difference between angles 1
Cal 1-5 deg. 60 59.5 60.5
Cal 1-5 deg. 60 59.5 60.5
Difference between angles 2
Cal 1-3 deg. 120 119.5 120.5
Cal 1-3 deg. 120 119.5 120.5
Difference between angles 3
Cal 1-6 deg. 180 179.5 180.5
Cal 1-6 deg. 180 179.5 180.5
Difference between angles 4
Cyl.1-2 deg. 240 239.5 240.5
Cyl.1-2 deg. 240 239.5 240.5
Difference between angles 5
Cal 1-4 deg. 300 299.5 300.5
Cal 1-4 deg. 300 299.5 300.5
Injection quantity adjustment
Adjusting point
-
Rack position
12.2
Pump speed
r/min
850
850
850
Average injection quantity
mm3/st.
89.5
87.9
91.1
Max. variation between cylinders
%
0
-2.5
2.5
Basic
*
Fixing the rack
*
Standard for adjustment of the maximum variation between cylinders
*
Injection quantity adjustment_02
Adjusting point
H
Rack position
9.5+-0.5
Pump speed
r/min
265
265
265
Average injection quantity
mm3/st.
8
6.7
9.3
Max. variation between cylinders
%
0
-14
14
Fixing the rack
*
Standard for adjustment of the maximum variation between cylinders
*
Injection quantity adjustment_03
Adjusting point
A
Rack position
R1(12.2)
Pump speed
r/min
850
850
850
Average injection quantity
mm3/st.
89.5
88.5
90.5
Basic
*
Fixing the lever
*
Boost pressure
kPa
24.7
24.7
Boost pressure
mmHg
185
185
Injection quantity adjustment_04
Adjusting point
B
Rack position
R1-0.15
Pump speed
r/min
1400
1400
1400
Average injection quantity
mm3/st.
97.5
94.3
100.7
Fixing the lever
*
Boost pressure
kPa
24.7
24.7
Boost pressure
mmHg
185
185
Injection quantity adjustment_05
Adjusting point
C
Rack position
R1-0.95
Pump speed
r/min
850
850
850
Average injection quantity
mm3/st.
73.5
70.3
76.7
Fixing the lever
*
Boost pressure
kPa
0
0
0
Boost pressure
mmHg
0
0
0
Injection quantity adjustment_06
Adjusting point
I
Rack position
-
Pump speed
r/min
150
150
150
Average injection quantity
mm3/st.
102
102
134
Fixing the lever
*
Boost pressure
kPa
0
0
0
Boost pressure
mmHg
0
0
0
Boost compensator adjustment
Pump speed
r/min
850
850
850
Rack position
R1-0.95
Boost pressure
kPa
5.3
4
6.6
Boost pressure
mmHg
40
30
50
Boost compensator adjustment_02
Pump speed
r/min
850
850
850
Rack position
R1(12.2)
Boost pressure
kPa
11.3
4.6
18
Boost pressure
mmHg
85
35
135
Timer adjustment
Pump speed
r/min
1175--
Advance angle
deg.
0
0
0
Load
3/4
Remarks
Start
Start
Timer adjustment_02
Pump speed
r/min
1125
Advance angle
deg.
0.3
Load
3/4
Timer adjustment_03
Pump speed
r/min
1400
Advance angle
deg.
3.5
3
4
Load
4/4
Remarks
Finish
Finish
Test data Ex:
Governor adjustment
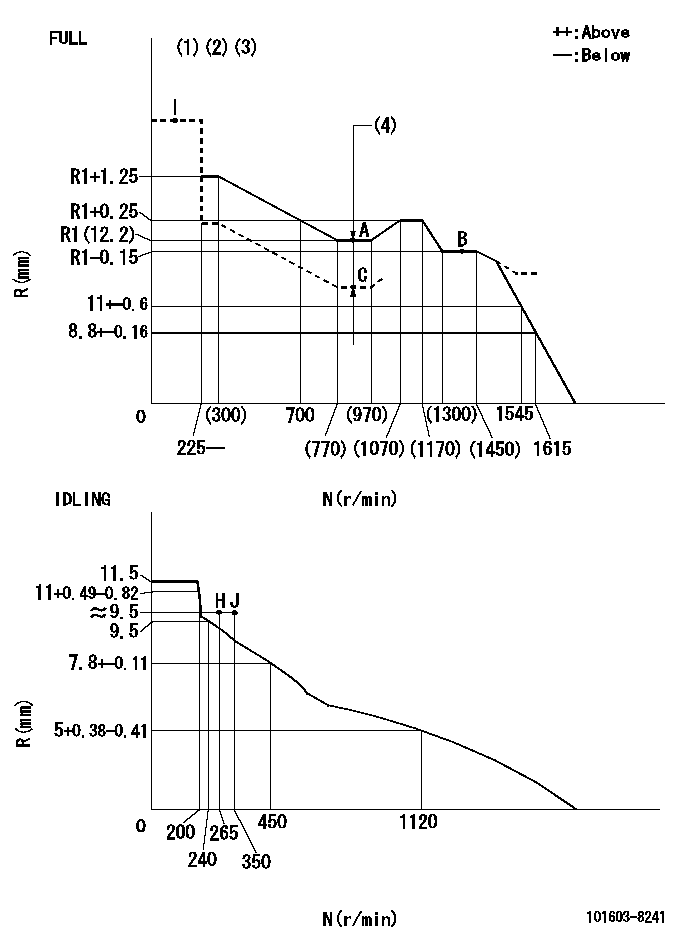
N:Pump speed
R:Rack position (mm)
(1)Torque cam stamping: T1
(2)Tolerance for racks not indicated: +-0.05mm.
(3)Adjust so that the boost compensator pushrod protrusion R = Ra at 0 boost.
(4)Boost compensator stroke: BCL
----------
T1=J09 Ra=12+-0.5mm BCL=0.95+-0.1mm
----------
----------
T1=J09 Ra=12+-0.5mm BCL=0.95+-0.1mm
----------
Speed control lever angle
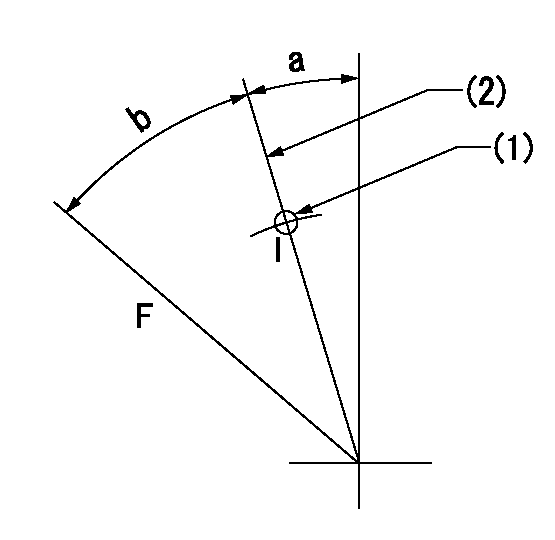
F:Full speed
I:Idle
(1)Use the pin at R = aa
(2)Stopper bolt set position 'H'
----------
aa=35mm
----------
a=11deg+-5deg b=36deg+-3deg
----------
aa=35mm
----------
a=11deg+-5deg b=36deg+-3deg
Stop lever angle
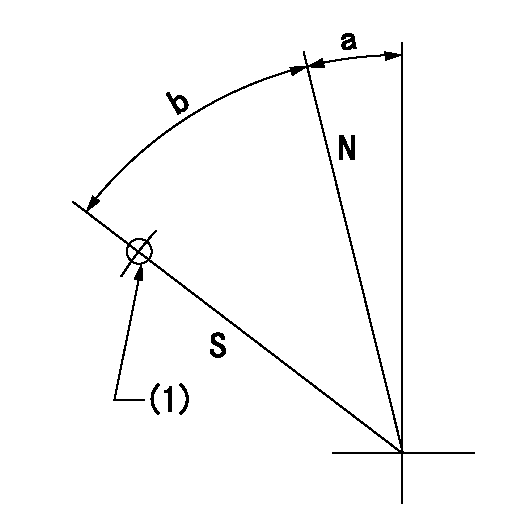
N:Pump normal
S:Stop the pump.
(1)Use the pin at R = aa
----------
aa=45mm
----------
a=12.5deg+-5deg b=40deg+-5deg
----------
aa=45mm
----------
a=12.5deg+-5deg b=40deg+-5deg
Timing setting
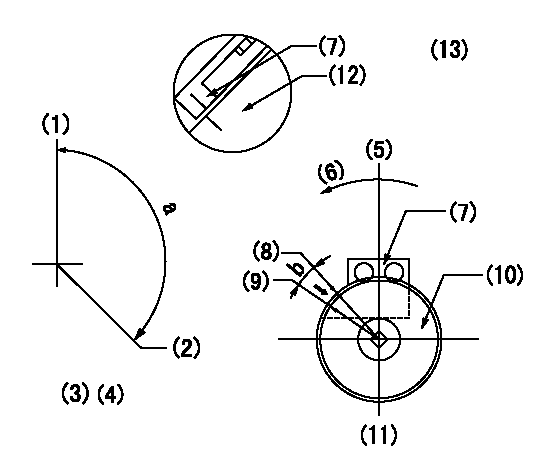
(1)Pump vertical direction
(2)Position of timer's threaded hole at No 1 cylinder's beginning of injection
(3)B.T.D.C.: aa
(4)-
(5)Pump vertical direction
(6)Direction of rotation
(7)Pointer
(8)Pointer stamping
(9)Timing device stamping
(10)Timing device
(11)Move b deg and stamp both at the same time as shown above.
(12)Outside circumference of timing device
(13)Secondary timing stamping position for the No. 1 cylinder's beginning of injection
----------
aa=12deg
----------
a=(160deg) b=0deg30min
----------
aa=12deg
----------
a=(160deg) b=0deg30min
Information:
Exhaust Smoke Can Be Seen While Starting Recommended Procedure1. Cold Outside Temperatures ... It can be necessary to use starting aids, or to heat engine oil or coolant at temperatures below 50°F (10°C).2. Air in Fuel System ... With air in the fuel system, the engine will normally be difficult to start, run rough, and release a large amount of white smoke. If the engine will not start, loosen a fuel injection line nut at the cylinder head. With the governor lever in the shutoff position, operate the fuel priming pump until the flow of fuel from the loosened fuel injection line is free of air. Tighten the fuel line nut. Fasten the priming pump and start the engine. If the engine still does not run smooth or releases a large amount of white smoke, loosen the fuel line nuts one at a time at the cylinder head until the fuel that comes out is free of air. Tighten the fuel line nuts. If the air can not be removed in this way, put 5 psi (35 kPa) of air pressure to the fuel tank.
Do not use more than 8 psi (55 kPa) of air pressure in the fuel tank or damage to the tank may result.
Check for leakage at the connections between the fuel tank and the fuel transfer pump. If leaks are found, tighten the connections or replace the lines. If there are no visual leaks, remove the fuel supply line from the tank and connect it to an outside fuel supply. If this corrects the problem, the suction line (standpipe) inside the fuel tank has a leak.3. Low Quality Fuel ... Remove a small amount of fuel from the tank and check for water in the fuel. If there is water in the fuel, remove fuel from the tank until it is free of water and fill with a good quality fuel. Change the fuel filter and "prime" (remove the air and/or low quality fuel from the fuel system) the fuel system with the fuel priming pump. If there is no water in the fuel, prime and start the engine by using an outside source of fuel. If engine starts correctly using different fuel, remove all fuel from the tank and fill with good quality fuel. Prime the fuel system if necessary.4. Low Fuel Pressure ... Change the fuel filter. If the pressure is still low, check the bypass valve in the fuel transfer pump. Debris in the system can make the valve become stationary in the open position.5. Fuel Injection Timing Not Correct ... Check and make necessary adjustments as per Testing and Adjusting section of this Service Manual.6. Valve Adjustment Not Correct ... Check and make necessary adjustments as per Testing and Adjusting section of this Service Manual. Intake valve clearance is .015 in. (0.38 mm) and exhaust valve clearance is .025 in. (0.64 mm).7. Bad Fuel Nozzle(s) ... Remove the fuel nozzles and test as per Testing and Adjusting section of
Do not use more than 8 psi (55 kPa) of air pressure in the fuel tank or damage to the tank may result.
Check for leakage at the connections between the fuel tank and the fuel transfer pump. If leaks are found, tighten the connections or replace the lines. If there are no visual leaks, remove the fuel supply line from the tank and connect it to an outside fuel supply. If this corrects the problem, the suction line (standpipe) inside the fuel tank has a leak.3. Low Quality Fuel ... Remove a small amount of fuel from the tank and check for water in the fuel. If there is water in the fuel, remove fuel from the tank until it is free of water and fill with a good quality fuel. Change the fuel filter and "prime" (remove the air and/or low quality fuel from the fuel system) the fuel system with the fuel priming pump. If there is no water in the fuel, prime and start the engine by using an outside source of fuel. If engine starts correctly using different fuel, remove all fuel from the tank and fill with good quality fuel. Prime the fuel system if necessary.4. Low Fuel Pressure ... Change the fuel filter. If the pressure is still low, check the bypass valve in the fuel transfer pump. Debris in the system can make the valve become stationary in the open position.5. Fuel Injection Timing Not Correct ... Check and make necessary adjustments as per Testing and Adjusting section of this Service Manual.6. Valve Adjustment Not Correct ... Check and make necessary adjustments as per Testing and Adjusting section of this Service Manual. Intake valve clearance is .015 in. (0.38 mm) and exhaust valve clearance is .025 in. (0.64 mm).7. Bad Fuel Nozzle(s) ... Remove the fuel nozzles and test as per Testing and Adjusting section of