Information injection-pump assembly
ZEXEL
101603-8063
1016038063
ISUZU
8943937523
8943937523
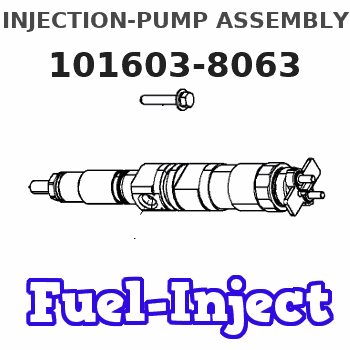
Rating:
Service parts 101603-8063 INJECTION-PUMP ASSEMBLY:
1.
_
7.
COUPLING PLATE
8.
_
9.
_
11.
Nozzle and Holder
8-94394-906-0
12.
Open Pre:MPa(Kqf/cm2)
18.1{185}/22.1{225}
14.
NOZZLE
Include in #1:
101603-8063
as INJECTION-PUMP ASSEMBLY
Include in #2:
104741-5070
as _
Cross reference number
ZEXEL
101603-8063
1016038063
ISUZU
8943937523
8943937523
Zexel num
Bosch num
Firm num
Name
Calibration Data:
Adjustment conditions
Test oil
1404 Test oil ISO4113 or {SAEJ967d}
1404 Test oil ISO4113 or {SAEJ967d}
Test oil temperature
degC
40
40
45
Nozzle and nozzle holder
105780-8140
Bosch type code
EF8511/9A
Nozzle
105780-0000
Bosch type code
DN12SD12T
Nozzle holder
105780-2080
Bosch type code
EF8511/9
Opening pressure
MPa
17.2
Opening pressure
kgf/cm2
175
Injection pipe
Outer diameter - inner diameter - length (mm) mm 6-2-600
Outer diameter - inner diameter - length (mm) mm 6-2-600
Overflow valve
132424-0620
Overflow valve opening pressure
kPa
157
123
191
Overflow valve opening pressure
kgf/cm2
1.6
1.25
1.95
Tester oil delivery pressure
kPa
157
157
157
Tester oil delivery pressure
kgf/cm2
1.6
1.6
1.6
Direction of rotation (viewed from drive side)
Left L
Left L
Injection timing adjustment
Direction of rotation (viewed from drive side)
Left L
Left L
Injection order
1-5-3-6-
2-4
Pre-stroke
mm
3.5
3.45
3.55
Rack position
Point A R=A
Point A R=A
Beginning of injection position
Governor side NO.1
Governor side NO.1
Difference between angles 1
Cal 1-5 deg. 60 59.5 60.5
Cal 1-5 deg. 60 59.5 60.5
Difference between angles 2
Cal 1-3 deg. 120 119.5 120.5
Cal 1-3 deg. 120 119.5 120.5
Difference between angles 3
Cal 1-6 deg. 180 179.5 180.5
Cal 1-6 deg. 180 179.5 180.5
Difference between angles 4
Cyl.1-2 deg. 240 239.5 240.5
Cyl.1-2 deg. 240 239.5 240.5
Difference between angles 5
Cal 1-4 deg. 300 299.5 300.5
Cal 1-4 deg. 300 299.5 300.5
Injection quantity adjustment
Adjusting point
-
Rack position
12.6
Pump speed
r/min
900
900
900
Average injection quantity
mm3/st.
99.4
97.8
101
Max. variation between cylinders
%
0
-2.5
2.5
Basic
*
Fixing the rack
*
Standard for adjustment of the maximum variation between cylinders
*
Injection quantity adjustment_02
Adjusting point
H
Rack position
9.5+-0.5
Pump speed
r/min
260
260
260
Average injection quantity
mm3/st.
8
6.7
9.3
Max. variation between cylinders
%
0
-14
14
Fixing the rack
*
Standard for adjustment of the maximum variation between cylinders
*
Injection quantity adjustment_03
Adjusting point
A
Rack position
R1(12.6)
Pump speed
r/min
900
900
900
Average injection quantity
mm3/st.
99.4
98.4
100.4
Basic
*
Fixing the lever
*
Boost pressure
kPa
26
26
Boost pressure
mmHg
195
195
Injection quantity adjustment_04
Adjusting point
B
Rack position
R1(12.6)
Pump speed
r/min
1400
1400
1400
Average injection quantity
mm3/st.
105.5
102.3
108.7
Fixing the lever
*
Boost pressure
kPa
26
26
Boost pressure
mmHg
195
195
Injection quantity adjustment_05
Adjusting point
C
Rack position
R1-1.25
Pump speed
r/min
900
900
900
Average injection quantity
mm3/st.
73.6
70.4
76.8
Fixing the lever
*
Boost pressure
kPa
0
0
0
Boost pressure
mmHg
0
0
0
Injection quantity adjustment_06
Adjusting point
I
Rack position
-
Pump speed
r/min
150
150
150
Average injection quantity
mm3/st.
102
102
134
Fixing the lever
*
Boost pressure
kPa
0
0
0
Boost pressure
mmHg
0
0
0
Boost compensator adjustment
Pump speed
r/min
900
900
900
Rack position
R1-1.25
Boost pressure
kPa
5.3
4
6.6
Boost pressure
mmHg
40
30
50
Boost compensator adjustment_02
Pump speed
r/min
900
900
900
Rack position
R1(12.6)
Boost pressure
kPa
12.7
6
19.4
Boost pressure
mmHg
95
45
145
Timer adjustment
Pump speed
r/min
1175--
Advance angle
deg.
0
0
0
Load
3/4
Remarks
Start
Start
Timer adjustment_02
Pump speed
r/min
1125
Advance angle
deg.
0.3
Load
3/4
Timer adjustment_03
Pump speed
r/min
1400
Advance angle
deg.
3.5
3
4
Load
4/4
Remarks
Finish
Finish
Test data Ex:
Governor adjustment
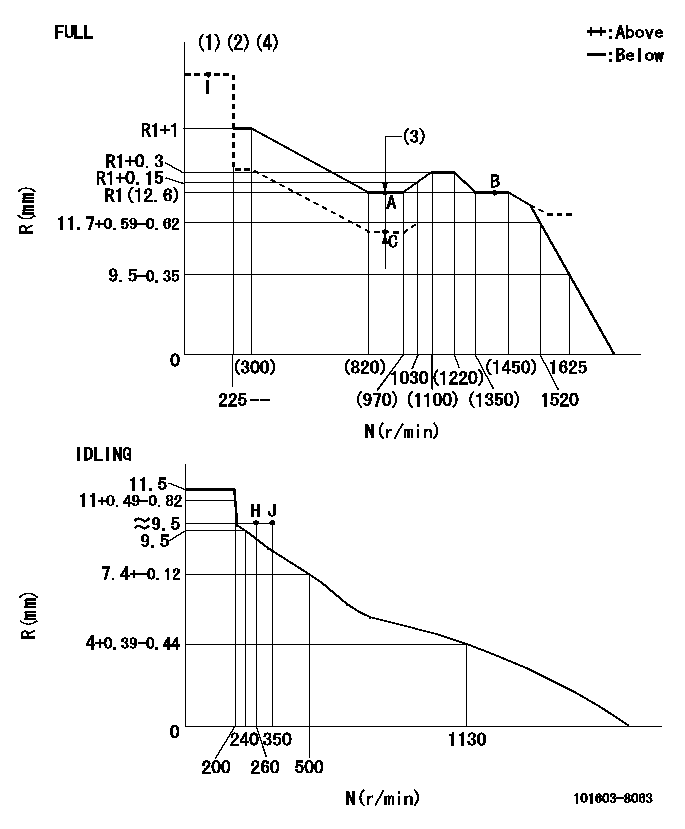
N:Pump speed
R:Rack position (mm)
(1)Torque cam stamping: T1
(2)Tolerance for racks not indicated: +-0.05mm.
(3)Boost compensator stroke: BCL
(4)Adjust so that the boost compensator pushrod protrusion R = Ra at 0 boost.
----------
T1=H66 BCL=1.25+-0.1mm Ra=12+-0.5mm
----------
----------
T1=H66 BCL=1.25+-0.1mm Ra=12+-0.5mm
----------
Speed control lever angle
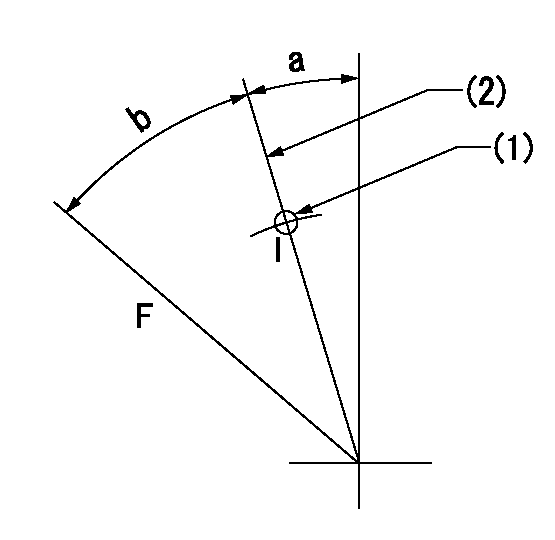
F:Full speed
I:Idle
(1)Use the pin at R = aa
(2)Stopper bolt set position 'H'
----------
aa=35mm
----------
a=10deg+-5deg b=(37deg)+-3deg
----------
aa=35mm
----------
a=10deg+-5deg b=(37deg)+-3deg
Stop lever angle
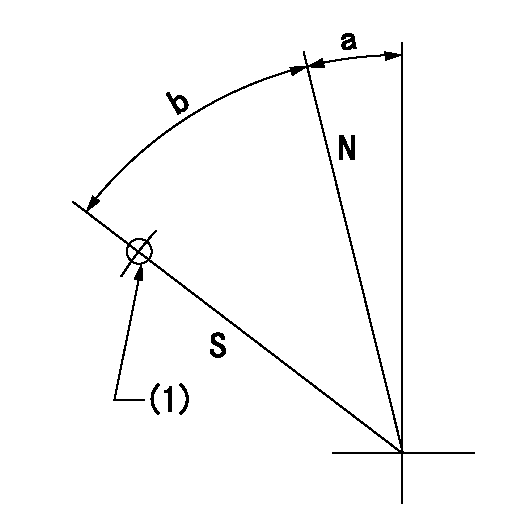
N:Pump normal
S:Stop the pump.
(1)Use the pin at R = aa
----------
aa=45mm
----------
a=12.5deg+-5deg b=40deg+-5deg
----------
aa=45mm
----------
a=12.5deg+-5deg b=40deg+-5deg
Timing setting
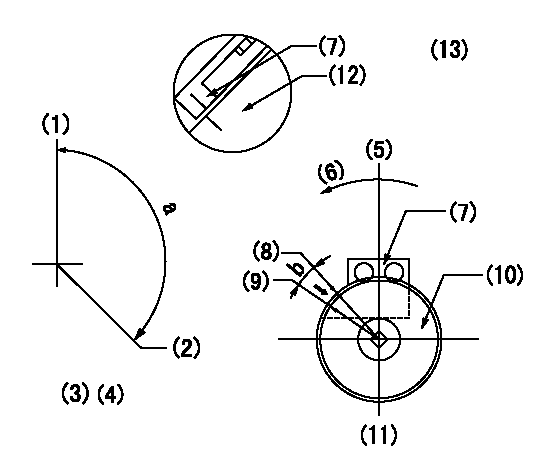
(1)Pump vertical direction
(2)Position of timer's threaded hole at the No. 1 cylinder's beginning of injection
(3)B.T.D.C.: aa
(4)-
(5)Pump vertical direction
(6)Direction of rotation
(7)Pointer
(8)Pointer stamping
(9)Timing device stamping
(10)Timing device
(11)Stamp both at the same time as shown above.
(12)Outside circumference of timing device
(13)Secondary timing stamping position for the No. 1 cylinder's beginning of injection
----------
aa=12deg bb=0deg30min
----------
a=(160deg)
----------
aa=12deg bb=0deg30min
----------
a=(160deg)
Information:
start by:a) remove valve covers
Do not let the tops of the fuel nozzles turn when the fuel lines are loosened. The nozzles will be damaged if the top of the nozzles turn in the body.
1. Use tooling (A) to loosen fuel injection line nut (1) at the fuel injection nozzles. 2. Disconnect fuel injection line nut (2) from head adapter nut (3).3. Remove adapter nut (3) and the O-ring seal.4. Move adapter (4) out of the valve cover base, and remove fuel injection line (1). 5. If necessary, remove seal (5) from fuel injection line (1). 6. Remove bolt (7) that holds clamp (6). Clamp (6) cannot be removed until fuel injection nozzle (8) is lifted 25.0 mm (1.00 in.).7. Remove fuel injection nozzle (8) with tooling (B) as follows: a. Install 6V6983 Adapter and 6V4152 Screw (9) [part of tooling (B)] into fuel injection nozzle (8). b. Install 6V6982 Tube Assembly (11) over the 6V4152 Screw. Use 2S5658 Washer and 1B2406 Nut (10) on the 6V4152 Screw to pull fuel injection nozzle (8) from the adapter. Items (10) and (11) are part of tooling (B).
A replacement of compression seal washer (13) and of carbon dam seal (12) must be made each time the fuel injection nozzle is removed. Be sure that the replacement compression seal washer (13) is the same color code and part number as the original compression seal washer. If the wrong thickness washer is used, engine damage could occur. See the Specifications section of this book for more information.
8. Remove carbon dam seal (12) and compression seal washer (13) from fuel injection nozzle (8).Install Fuel Injection Nozzles
1. Use tool (D) to clean adapter bore (1) for the fuel injection nozzle. Use a tap driver to turn tool (D). 2. Install compression seal washer (3) on fuel injection nozzle (4).3. Use tool (A) to install carbon dam seal (2) on fuel injection nozzle (4). Refer to Special Instruction SEHS7292 for the use of tooling (C). 4. Install fuel injection nozzle (4) and clamp (5) as a unit. Install the bolt through the clamp into the adapter. 5. Install O-ring seal (6) on fuel injection line (7) and put clean diesel fuel on it. 6. Install fuel injection line (7). Move adapter (8) into position in the rocker arm cover base.
Do not let the tops of the fuel nozzles turn when the fuel lines are tightened. The nozzles will be damaged if the top of the nozzles turn in the body.
7. Use tooling (B) to tighten the inner fuel line nuts to a torque of 41 7 N m (30 5 lb.ft.). 8. Put clean diesel fuel oil on O-ring seal (11). Install O-ring seal (11) and nut (10). Tighten nut (10) to a torque of 30 5 N m (22 4 lb.ft.).9. Install nut (9) for the fuel injection line, and tighten the fuel injection line nut to a torque of 41 7 N m (30 5 lb.ft.).end by:a)
Do not let the tops of the fuel nozzles turn when the fuel lines are loosened. The nozzles will be damaged if the top of the nozzles turn in the body.
1. Use tooling (A) to loosen fuel injection line nut (1) at the fuel injection nozzles. 2. Disconnect fuel injection line nut (2) from head adapter nut (3).3. Remove adapter nut (3) and the O-ring seal.4. Move adapter (4) out of the valve cover base, and remove fuel injection line (1). 5. If necessary, remove seal (5) from fuel injection line (1). 6. Remove bolt (7) that holds clamp (6). Clamp (6) cannot be removed until fuel injection nozzle (8) is lifted 25.0 mm (1.00 in.).7. Remove fuel injection nozzle (8) with tooling (B) as follows: a. Install 6V6983 Adapter and 6V4152 Screw (9) [part of tooling (B)] into fuel injection nozzle (8). b. Install 6V6982 Tube Assembly (11) over the 6V4152 Screw. Use 2S5658 Washer and 1B2406 Nut (10) on the 6V4152 Screw to pull fuel injection nozzle (8) from the adapter. Items (10) and (11) are part of tooling (B).
A replacement of compression seal washer (13) and of carbon dam seal (12) must be made each time the fuel injection nozzle is removed. Be sure that the replacement compression seal washer (13) is the same color code and part number as the original compression seal washer. If the wrong thickness washer is used, engine damage could occur. See the Specifications section of this book for more information.
8. Remove carbon dam seal (12) and compression seal washer (13) from fuel injection nozzle (8).Install Fuel Injection Nozzles
1. Use tool (D) to clean adapter bore (1) for the fuel injection nozzle. Use a tap driver to turn tool (D). 2. Install compression seal washer (3) on fuel injection nozzle (4).3. Use tool (A) to install carbon dam seal (2) on fuel injection nozzle (4). Refer to Special Instruction SEHS7292 for the use of tooling (C). 4. Install fuel injection nozzle (4) and clamp (5) as a unit. Install the bolt through the clamp into the adapter. 5. Install O-ring seal (6) on fuel injection line (7) and put clean diesel fuel on it. 6. Install fuel injection line (7). Move adapter (8) into position in the rocker arm cover base.
Do not let the tops of the fuel nozzles turn when the fuel lines are tightened. The nozzles will be damaged if the top of the nozzles turn in the body.
7. Use tooling (B) to tighten the inner fuel line nuts to a torque of 41 7 N m (30 5 lb.ft.). 8. Put clean diesel fuel oil on O-ring seal (11). Install O-ring seal (11) and nut (10). Tighten nut (10) to a torque of 30 5 N m (22 4 lb.ft.).9. Install nut (9) for the fuel injection line, and tighten the fuel injection line nut to a torque of 41 7 N m (30 5 lb.ft.).end by:a)