Information injection-pump assembly
ZEXEL
101603-7760
1016037760
ISUZU
1156027800
1156027800
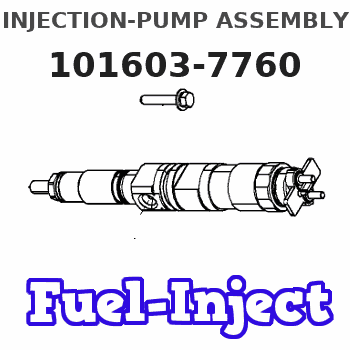
Rating:
Service parts 101603-7760 INJECTION-PUMP ASSEMBLY:
1.
_
7.
COUPLING PLATE
8.
_
9.
_
11.
Nozzle and Holder
1-15300-168-1
12.
Open Pre:MPa(Kqf/cm2)
22.1{225}
15.
NOZZLE SET
Cross reference number
ZEXEL
101603-7760
1016037760
ISUZU
1156027800
1156027800
Zexel num
Bosch num
Firm num
Name
Calibration Data:
Adjustment conditions
Test oil
1404 Test oil ISO4113 or {SAEJ967d}
1404 Test oil ISO4113 or {SAEJ967d}
Test oil temperature
degC
40
40
45
Nozzle and nozzle holder
105780-8140
Bosch type code
EF8511/9A
Nozzle
105780-0000
Bosch type code
DN12SD12T
Nozzle holder
105780-2080
Bosch type code
EF8511/9
Opening pressure
MPa
17.2
Opening pressure
kgf/cm2
175
Injection pipe
Outer diameter - inner diameter - length (mm) mm 6-2-600
Outer diameter - inner diameter - length (mm) mm 6-2-600
Overflow valve
132424-0620
Overflow valve opening pressure
kPa
157
123
191
Overflow valve opening pressure
kgf/cm2
1.6
1.25
1.95
Tester oil delivery pressure
kPa
157
157
157
Tester oil delivery pressure
kgf/cm2
1.6
1.6
1.6
Direction of rotation (viewed from drive side)
Left L
Left L
Injection timing adjustment
Direction of rotation (viewed from drive side)
Left L
Left L
Injection order
1-5-3-6-
2-4
Pre-stroke
mm
3.7
3.65
3.75
Beginning of injection position
Governor side NO.1
Governor side NO.1
Difference between angles 1
Cal 1-5 deg. 60 59.5 60.5
Cal 1-5 deg. 60 59.5 60.5
Difference between angles 2
Cal 1-3 deg. 120 119.5 120.5
Cal 1-3 deg. 120 119.5 120.5
Difference between angles 3
Cal 1-6 deg. 180 179.5 180.5
Cal 1-6 deg. 180 179.5 180.5
Difference between angles 4
Cyl.1-2 deg. 240 239.5 240.5
Cyl.1-2 deg. 240 239.5 240.5
Difference between angles 5
Cal 1-4 deg. 300 299.5 300.5
Cal 1-4 deg. 300 299.5 300.5
Injection quantity adjustment
Adjusting point
-
Rack position
11.3
Pump speed
r/min
700
700
700
Average injection quantity
mm3/st.
78.5
76.9
80.1
Max. variation between cylinders
%
0
-2.5
2.5
Basic
*
Fixing the rack
*
Standard for adjustment of the maximum variation between cylinders
*
Injection quantity adjustment_02
Adjusting point
H
Rack position
9.5+-0.5
Pump speed
r/min
260
260
260
Average injection quantity
mm3/st.
10.7
8.7
12.7
Max. variation between cylinders
%
0
-14
14
Fixing the rack
*
Standard for adjustment of the maximum variation between cylinders
*
Injection quantity adjustment_03
Adjusting point
A
Rack position
R1(11.3)
Pump speed
r/min
700
700
700
Average injection quantity
mm3/st.
78.5
77.5
79.5
Basic
*
Fixing the lever
*
Injection quantity adjustment_04
Adjusting point
B
Rack position
R1+0.05
Pump speed
r/min
550
550
550
Average injection quantity
mm3/st.
76
72.8
79.2
Fixing the lever
*
Injection quantity adjustment_05
Adjusting point
I
Rack position
-
Pump speed
r/min
100
100
100
Average injection quantity
mm3/st.
96.5
96.5
106.5
Fixing the lever
*
Rack limit
*
Timer adjustment
Pump speed
r/min
550--
Advance angle
deg.
0
0
0
Remarks
Start
Start
Timer adjustment_02
Pump speed
r/min
500
Advance angle
deg.
0.5
Timer adjustment_03
Pump speed
r/min
1350
Advance angle
deg.
6
5.5
6.5
Remarks
Finish
Finish
Test data Ex:
Governor adjustment
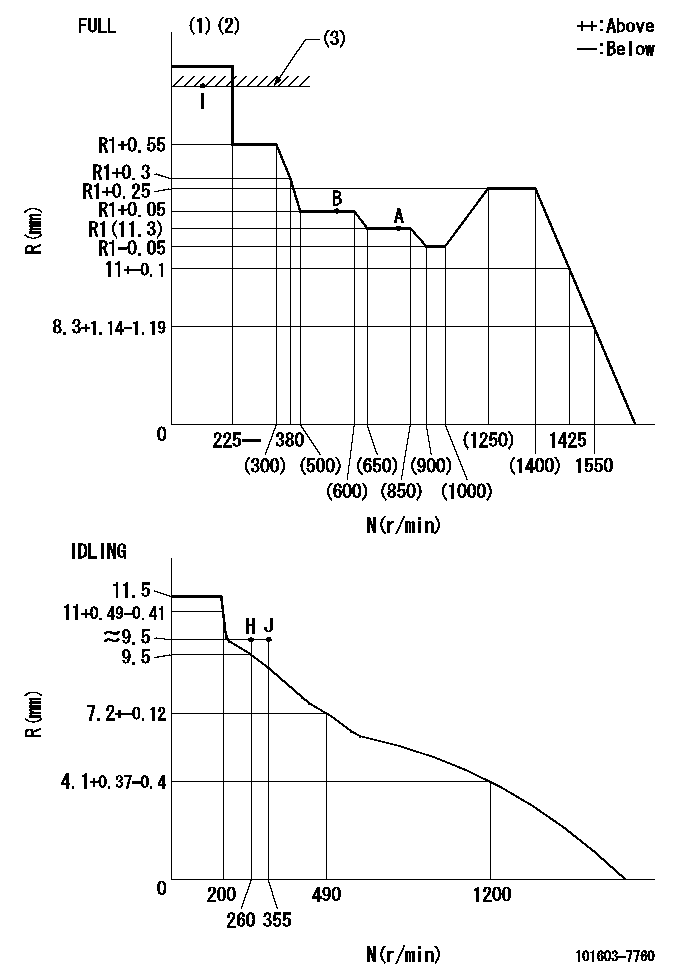
N:Pump speed
R:Rack position (mm)
(1)Torque cam stamping: T1
(2)Tolerance for racks not indicated: +-0.05mm.
(3)RACK LIMIT
----------
T1=B52
----------
----------
T1=B52
----------
Speed control lever angle

F:Full speed
I:Idle
(1)Stopper bolt set position 'H'
----------
----------
a=18deg+-5deg b=(34deg)+-3deg
----------
----------
a=18deg+-5deg b=(34deg)+-3deg
Stop lever angle
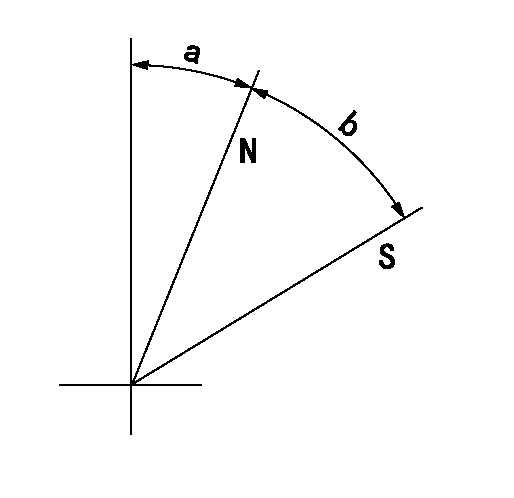
N:Pump normal
S:Stop the pump.
----------
----------
a=25deg+-5deg b=40deg+-5deg
----------
----------
a=25deg+-5deg b=40deg+-5deg
0000001501 TAMPER PROOF
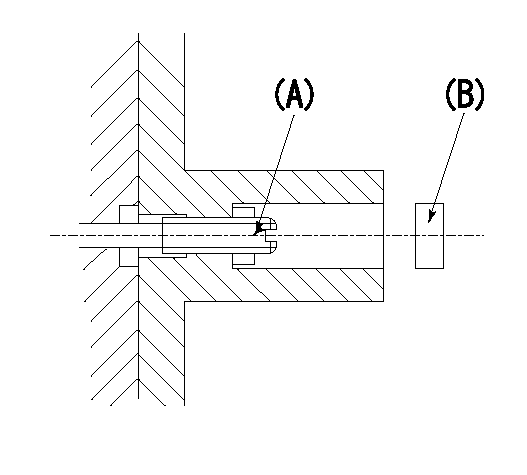
1. Set the full load.
(1)After governor adjustment (torque cam phase adjustment), move the load lever to increase the full rack position to R1.
(2)Set using the screw (A) so that the rack position is as shown above and tighten the locknut.
(3)Again set in the correct rack position using the load lever.
----------
R1=0.4mm
----------
----------
R1=0.4mm
----------
Timing setting
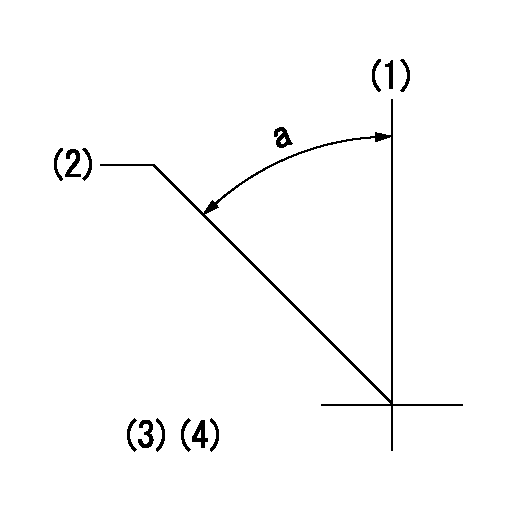
(1)Pump vertical direction
(2)Position of timer's threaded hole at No 1 cylinder's beginning of injection
(3)B.T.D.C.: aa
(4)-
----------
aa=14deg
----------
a=(40deg)
----------
aa=14deg
----------
a=(40deg)
Information:
The information supplied in this service letter may not be valid after the termination date of this program. Do not perform the work outlined in this Service Letter after the termination date without first contacting your Caterpillar product analyst.
Termination Date
March 31, 1997Problem
Improvements have been made to the remanufactured unit injectors that are used in various 3114 and 3116 Engines. All of the former 0R3002, 0R3003, 0R3190, 0R3389, 0R3580, 0R3742, 0R4368, 0R4369, 0R4370, 0R4374, and 0R4376 Remanufactured Unit Injectors need to be removed from Parts Stock.
Action Required
Remove all 0R3002, 0R3003, 0R3190, 0R3389, 0R3580, 0R3742, 0R4368, 0R4369, 0R4370, 0R4374, and 0R4376 Remanufactured Unit Injectors from Parts Stock.
When ordering parts, refer to the attached chart until the information is available in a permanent publication.
Service Claim Allowances
Submit one claim for all 0R3002, 0R3003, 0R3190, 0R3389, 0R3580, 0R3742, 0R4368, 0R4369, 0R4370, 0R4374, and 0R4376 Remanufactured Unit Injectors removed from Parts Stock.
TEPS Dealers should refer to their warranty bullitin for proper claiming and disposition.
Parts Disposition
All injectors removed from Parts Stock are to be returned as cores for remanufacturing.
U.S. and Canadian Dealers
Return all 0R3002, 0R3003, 0R3190, 0R3389, 0R3580, 0R3742, 0R4368, 0R4369, 0R4370, 0R4374, and 0R4376 Remanufactured Unit Injectors that are removed from Parts Stock and a copy of the claim to:
Caterpillar Inc.
Attn: Bill Harland - Warranty Review
501 Cardinal Drive
Corinth, MS 38834
All Other Dealers
Handle the parts in accordance with your Warranty Bulletin on Remanufactured Engines and Components, refer to the topic "Disposition of the Core Under Warranty".
Attach.(1-UNIT INJECTOR CHART)3114 & 3116 Unit Injector Chart
Termination Date
March 31, 1997Problem
Improvements have been made to the remanufactured unit injectors that are used in various 3114 and 3116 Engines. All of the former 0R3002, 0R3003, 0R3190, 0R3389, 0R3580, 0R3742, 0R4368, 0R4369, 0R4370, 0R4374, and 0R4376 Remanufactured Unit Injectors need to be removed from Parts Stock.
Action Required
Remove all 0R3002, 0R3003, 0R3190, 0R3389, 0R3580, 0R3742, 0R4368, 0R4369, 0R4370, 0R4374, and 0R4376 Remanufactured Unit Injectors from Parts Stock.
When ordering parts, refer to the attached chart until the information is available in a permanent publication.
Service Claim Allowances
Submit one claim for all 0R3002, 0R3003, 0R3190, 0R3389, 0R3580, 0R3742, 0R4368, 0R4369, 0R4370, 0R4374, and 0R4376 Remanufactured Unit Injectors removed from Parts Stock.
TEPS Dealers should refer to their warranty bullitin for proper claiming and disposition.
Parts Disposition
All injectors removed from Parts Stock are to be returned as cores for remanufacturing.
U.S. and Canadian Dealers
Return all 0R3002, 0R3003, 0R3190, 0R3389, 0R3580, 0R3742, 0R4368, 0R4369, 0R4370, 0R4374, and 0R4376 Remanufactured Unit Injectors that are removed from Parts Stock and a copy of the claim to:
Caterpillar Inc.
Attn: Bill Harland - Warranty Review
501 Cardinal Drive
Corinth, MS 38834
All Other Dealers
Handle the parts in accordance with your Warranty Bulletin on Remanufactured Engines and Components, refer to the topic "Disposition of the Core Under Warranty".
Attach.(1-UNIT INJECTOR CHART)3114 & 3116 Unit Injector Chart