Information injection-pump assembly
ZEXEL
101603-7591
1016037591
ISUZU
8943968881
8943968881
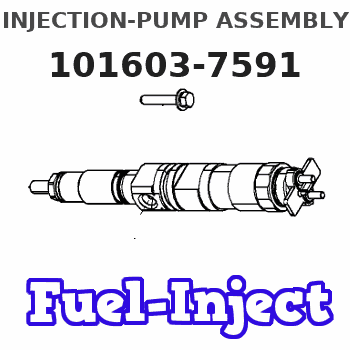
Rating:
Service parts 101603-7591 INJECTION-PUMP ASSEMBLY:
1.
_
7.
COUPLING PLATE
8.
_
9.
_
11.
Nozzle and Holder
8-94397-483-2
12.
Open Pre:MPa(Kqf/cm2)
18.1{185}
15.
NOZZLE SET
Cross reference number
ZEXEL
101603-7591
1016037591
ISUZU
8943968881
8943968881
Zexel num
Bosch num
Firm num
Name
Calibration Data:
Adjustment conditions
Test oil
1404 Test oil ISO4113 or {SAEJ967d}
1404 Test oil ISO4113 or {SAEJ967d}
Test oil temperature
degC
40
40
45
Nozzle and nozzle holder
105780-8140
Bosch type code
EF8511/9A
Nozzle
105780-0000
Bosch type code
DN12SD12T
Nozzle holder
105780-2080
Bosch type code
EF8511/9
Opening pressure
MPa
17.2
Opening pressure
kgf/cm2
175
Injection pipe
Outer diameter - inner diameter - length (mm) mm 6-2-600
Outer diameter - inner diameter - length (mm) mm 6-2-600
Overflow valve
131424-4920
Overflow valve opening pressure
kPa
127
107
147
Overflow valve opening pressure
kgf/cm2
1.3
1.1
1.5
Tester oil delivery pressure
kPa
157
157
157
Tester oil delivery pressure
kgf/cm2
1.6
1.6
1.6
Direction of rotation (viewed from drive side)
Left L
Left L
Injection timing adjustment
Direction of rotation (viewed from drive side)
Left L
Left L
Injection order
1-5-3-6-
2-4
Pre-stroke
mm
4.2
4.15
4.25
Rack position
After adjusting injection quantity. R=A
After adjusting injection quantity. R=A
Beginning of injection position
Governor side NO.1
Governor side NO.1
Difference between angles 1
Cal 1-5 deg. 60 59.5 60.5
Cal 1-5 deg. 60 59.5 60.5
Difference between angles 2
Cal 1-3 deg. 120 119.5 120.5
Cal 1-3 deg. 120 119.5 120.5
Difference between angles 3
Cal 1-6 deg. 180 179.5 180.5
Cal 1-6 deg. 180 179.5 180.5
Difference between angles 4
Cyl.1-2 deg. 240 239.5 240.5
Cyl.1-2 deg. 240 239.5 240.5
Difference between angles 5
Cal 1-4 deg. 300 299.5 300.5
Cal 1-4 deg. 300 299.5 300.5
Injection quantity adjustment
Adjusting point
-
Rack position
11.1
Pump speed
r/min
900
900
900
Average injection quantity
mm3/st.
69
67.4
70.6
Max. variation between cylinders
%
0
-2.5
2.5
Basic
*
Fixing the rack
*
Standard for adjustment of the maximum variation between cylinders
*
Injection quantity adjustment_02
Adjusting point
H
Rack position
9.8+-0.5
Pump speed
r/min
265
265
265
Average injection quantity
mm3/st.
18.2
16.9
19.5
Max. variation between cylinders
%
0
-14
14
Fixing the rack
*
Standard for adjustment of the maximum variation between cylinders
*
Injection quantity adjustment_03
Adjusting point
A
Rack position
R1(11.1)
Pump speed
r/min
900
900
900
Average injection quantity
mm3/st.
69
68
70
Basic
*
Fixing the lever
*
Injection quantity adjustment_04
Adjusting point
I
Rack position
-
Pump speed
r/min
150
150
150
Average injection quantity
mm3/st.
103
103
135
Fixing the lever
*
Timer adjustment
Pump speed
r/min
1210--
Advance angle
deg.
0
0
0
Load
3/4
Remarks
Start
Start
Timer adjustment_02
Pump speed
r/min
1160
Advance angle
deg.
0.3
Load
3/4
Timer adjustment_03
Pump speed
r/min
1500
Advance angle
deg.
5.5
5
6
Load
4/4
Remarks
Finish
Finish
Test data Ex:
Governor adjustment
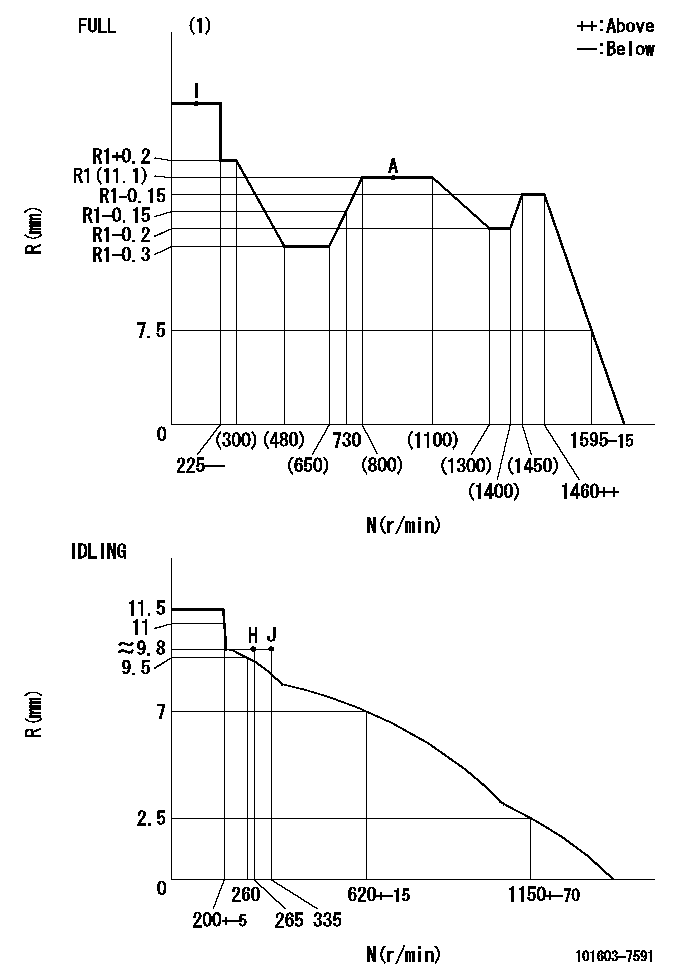
N:Pump speed
R:Rack position (mm)
(1)Torque cam stamping: T1
----------
T1=F71
----------
----------
T1=F71
----------
Speed control lever angle

F:Full speed
I:Idle
(1)Use the pin at R = aa
(2)Stopper bolt set position 'H'
----------
aa=28mm
----------
a=12.5deg+-5deg b=(45.5deg)+-3deg
----------
aa=28mm
----------
a=12.5deg+-5deg b=(45.5deg)+-3deg
Stop lever angle
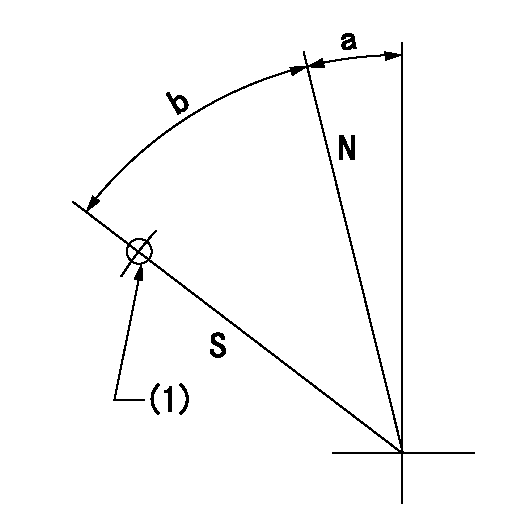
N:Pump normal
S:Stop the pump.
(1)Use the pin at R = aa
----------
aa=45mm
----------
a=12.5deg+-5deg b=40deg+-5deg
----------
aa=45mm
----------
a=12.5deg+-5deg b=40deg+-5deg
0000001501 I/P WITH LOAD PLUNGER ADJ
Plunger assembly number: PL (stamping: ST)
1. Adjustment procedures
(1)Insert the pre-stroke adjusting shims L1 for each cylinder.
(2)Adjust injection quantity.(max. var. bet. cyl. idling a1, full a2)
(3)At basic point A, adjust so that the pre-stroke is L2.
(4)Reconfirm the injection quantity.
----------
PL=131153-4520 ST=A724 L1=1mm L2=4.2+-0.05mm a1=+-14% a2=+-2.5%
----------
----------
PL=131153-4520 ST=A724 L1=1mm L2=4.2+-0.05mm a1=+-14% a2=+-2.5%
----------
Timing setting
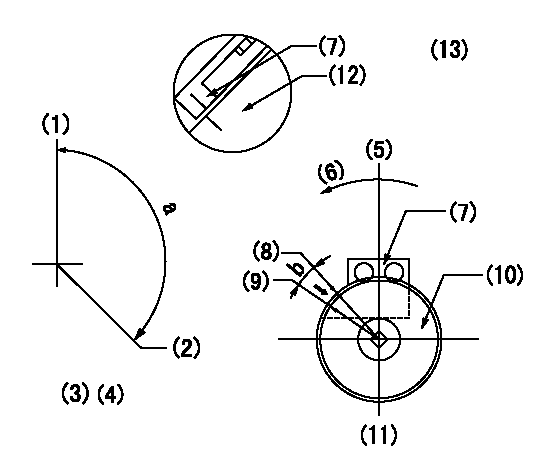
(1)Pump vertical direction
(2)Position of timer's threaded hole at No 1 cylinder's beginning of injection
(3)B.T.D.C.: aa
(4)-
(5)Pump vertical direction
(6)Direction of rotation
(7)Pointer
(8)Pointer stamping
(9)Timing device stamping
(10)Timing device
(11)Move b deg and stamp both at the same time as shown above.
(12)Outside circumference of timing device
(13)Secondary timing stamping position for the No. 1 cylinder's beginning of injection
----------
aa=11deg
----------
a=(150deg) b=1deg
----------
aa=11deg
----------
a=(150deg) b=1deg
Information:
Caterpillar: Confidential Yellow
PSP FOR THE USE OF TWO CLAMPS TO HOLD THE BODY AND FUEL NOZZLE IN POSITION ON 3406, 3408 AND 3412 ENGINES - MAILED WORLDWIDE EXC EPT CANADA, BRAZIL & CACO
  The information supplied in this service letter may not be valid after the termination date of this program.   Do not perform the work outlined in this Service Letter after the termination date without first contacting your Caterpillar product analyst.
PRODUCT SUPPORT PROGRAM FOR THE USE OF TWO CLAMPS TO HOLD THE BODY AND FUEL NOZZLE IN POSITION ON 3406, 3408 AND 3412 ENGINES, 1252, PS4019 U-74 AU-59 E-47 O-45 TT-12 TA-6 TM-6 This Program can be administered either before or after a failure. In either case the warranty allowances will be the same and contingent damage will not be allowed. The decision whether to apply the Program is made by the dealer. When reporting the repair use "PS4019" as Part Number and "7755" as Group Number. Although products in the field are to be administered as described above, dealers should rework parts stock immediately. Termination Date
September 30, 1986.
Problem
Engines equipped with 4W5719 (3406) or 4W5733 (3408, 3412) Adapter Assemblies use one 4W5717 Clamp to hold the body and fuel nozzle in position. See the Illustration. These adapter assemblies are also used in 0R0977 (3406) 0R0980 (3408) and 0R2659 (3412) Remanufactured Head Assemblies. One clamp does not provide enough force to hold the body and fuel nozzle tight. This permits fuel to leak past the internal parts of the nozzle and cause the nozzle case to bulge or split. This program provides for an additional clamp and bolts to be used with these adapter assemblies. (SEE ILLUSTRATION)
Affected Product
1/850907/01/002
Parts Needed
1-4W5717 Clamp and 2-5P6900 Bolts for each adapter assembly.
Action Required
The new parts should be installed on cylinder heads in parts stock immediately. Only cylinder heads received before this Service Letter need to be checked. The new parts should be installed on products in the field only when the valve cover has been removed for some other repair or inspection. Install the new clamp and bolts 180 deg. from the existing clamp and bolts. Tighten the bolts for the new clamp to 31 +/- 7 N X m (23 +/- 5 lb ft). Check to make sure the bolts for the existing clamp are tightened to the same torque. Then check the torque on the bolts for the new clamp. (SEE ILLUSTRATION)
Parts Disposition
Not applicable.
PSP FOR THE USE OF TWO CLAMPS TO HOLD THE BODY AND FUEL NOZZLE IN POSITION ON 3406, 3408 AND 3412 ENGINES - MAILED WORLDWIDE EXC EPT CANADA, BRAZIL & CACO
  The information supplied in this service letter may not be valid after the termination date of this program.   Do not perform the work outlined in this Service Letter after the termination date without first contacting your Caterpillar product analyst.
PRODUCT SUPPORT PROGRAM FOR THE USE OF TWO CLAMPS TO HOLD THE BODY AND FUEL NOZZLE IN POSITION ON 3406, 3408 AND 3412 ENGINES, 1252, PS4019 U-74 AU-59 E-47 O-45 TT-12 TA-6 TM-6 This Program can be administered either before or after a failure. In either case the warranty allowances will be the same and contingent damage will not be allowed. The decision whether to apply the Program is made by the dealer. When reporting the repair use "PS4019" as Part Number and "7755" as Group Number. Although products in the field are to be administered as described above, dealers should rework parts stock immediately. Termination Date
September 30, 1986.
Problem
Engines equipped with 4W5719 (3406) or 4W5733 (3408, 3412) Adapter Assemblies use one 4W5717 Clamp to hold the body and fuel nozzle in position. See the Illustration. These adapter assemblies are also used in 0R0977 (3406) 0R0980 (3408) and 0R2659 (3412) Remanufactured Head Assemblies. One clamp does not provide enough force to hold the body and fuel nozzle tight. This permits fuel to leak past the internal parts of the nozzle and cause the nozzle case to bulge or split. This program provides for an additional clamp and bolts to be used with these adapter assemblies. (SEE ILLUSTRATION)
Affected Product
1/850907/01/002
Parts Needed
1-4W5717 Clamp and 2-5P6900 Bolts for each adapter assembly.
Action Required
The new parts should be installed on cylinder heads in parts stock immediately. Only cylinder heads received before this Service Letter need to be checked. The new parts should be installed on products in the field only when the valve cover has been removed for some other repair or inspection. Install the new clamp and bolts 180 deg. from the existing clamp and bolts. Tighten the bolts for the new clamp to 31 +/- 7 N X m (23 +/- 5 lb ft). Check to make sure the bolts for the existing clamp are tightened to the same torque. Then check the torque on the bolts for the new clamp. (SEE ILLUSTRATION)
Parts Disposition
Not applicable.