Information injection-pump assembly
ZEXEL
101603-7532
1016037532
ISUZU
8943969253
8943969253
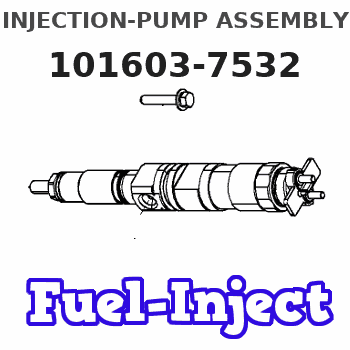
Rating:
Service parts 101603-7532 INJECTION-PUMP ASSEMBLY:
1.
_
7.
COUPLING PLATE
8.
_
9.
_
11.
Nozzle and Holder
8-94397-483-2
12.
Open Pre:MPa(Kqf/cm2)
18.1{185}
15.
NOZZLE SET
Cross reference number
ZEXEL
101603-7532
1016037532
ISUZU
8943969253
8943969253
Zexel num
Bosch num
Firm num
Name
Calibration Data:
Adjustment conditions
Test oil
1404 Test oil ISO4113 or {SAEJ967d}
1404 Test oil ISO4113 or {SAEJ967d}
Test oil temperature
degC
40
40
45
Nozzle and nozzle holder
105780-8210
Nozzle
105780-0070
Bosch type code
DN12SD12T-1
Nozzle holder
105780-2080
Bosch type code
EF8511/9
Opening pressure
MPa
17.2
Opening pressure
kgf/cm2
175
Injection pipe
Outer diameter - inner diameter - length (mm) mm 6-2-600
Outer diameter - inner diameter - length (mm) mm 6-2-600
Overflow valve
131424-4920
Overflow valve opening pressure
kPa
127
107
147
Overflow valve opening pressure
kgf/cm2
1.3
1.1
1.5
Tester oil delivery pressure
kPa
157
157
157
Tester oil delivery pressure
kgf/cm2
1.6
1.6
1.6
Direction of rotation (viewed from drive side)
Left L
Left L
Injection timing adjustment
Direction of rotation (viewed from drive side)
Left L
Left L
Injection order
1-5-3-6-
2-4
Pre-stroke
mm
4.2
4.15
4.25
Rack position
After adjusting injection quantity. R=A
After adjusting injection quantity. R=A
Beginning of injection position
Governor side NO.1
Governor side NO.1
Difference between angles 1
Cal 1-5 deg. 60 59.5 60.5
Cal 1-5 deg. 60 59.5 60.5
Difference between angles 2
Cal 1-3 deg. 120 119.5 120.5
Cal 1-3 deg. 120 119.5 120.5
Difference between angles 3
Cal 1-6 deg. 180 179.5 180.5
Cal 1-6 deg. 180 179.5 180.5
Difference between angles 4
Cyl.1-2 deg. 240 239.5 240.5
Cyl.1-2 deg. 240 239.5 240.5
Difference between angles 5
Cal 1-4 deg. 300 299.5 300.5
Cal 1-4 deg. 300 299.5 300.5
Injection quantity adjustment
Adjusting point
-
Rack position
11.2
Pump speed
r/min
900
900
900
Average injection quantity
mm3/st.
73.5
71.9
75.1
Max. variation between cylinders
%
0
-2.5
2.5
Basic
*
Fixing the rack
*
Standard for adjustment of the maximum variation between cylinders
*
Injection quantity adjustment_02
Adjusting point
H
Rack position
9.5+-0.5
Pump speed
r/min
260
260
260
Average injection quantity
mm3/st.
8.3
7
9.6
Max. variation between cylinders
%
0
-14
14
Fixing the rack
*
Standard for adjustment of the maximum variation between cylinders
*
Injection quantity adjustment_03
Adjusting point
A
Rack position
R1(11.2)
Pump speed
r/min
900
900
900
Average injection quantity
mm3/st.
73.5
72.5
74.5
Basic
*
Fixing the lever
*
Injection quantity adjustment_04
Adjusting point
B
Rack position
R1-0.1
Pump speed
r/min
1500
1500
1500
Average injection quantity
mm3/st.
84.6
80.6
88.6
Fixing the lever
*
Injection quantity adjustment_05
Adjusting point
C
Rack position
R1-0.3
Pump speed
r/min
600
600
600
Average injection quantity
mm3/st.
55.3
52.1
58.5
Fixing the lever
*
Injection quantity adjustment_06
Adjusting point
I
Rack position
-
Pump speed
r/min
150
150
150
Average injection quantity
mm3/st.
103
103
135
Fixing the lever
*
Timer adjustment
Pump speed
r/min
(1220)
Advance angle
deg.
0
0
0
Remarks
Start
Start
Timer adjustment_02
Pump speed
r/min
1300
Advance angle
deg.
1.3
0.8
1.8
Timer adjustment_03
Pump speed
r/min
1500
Advance angle
deg.
5.5
5
6
Remarks
Finish
Finish
Test data Ex:
Governor adjustment
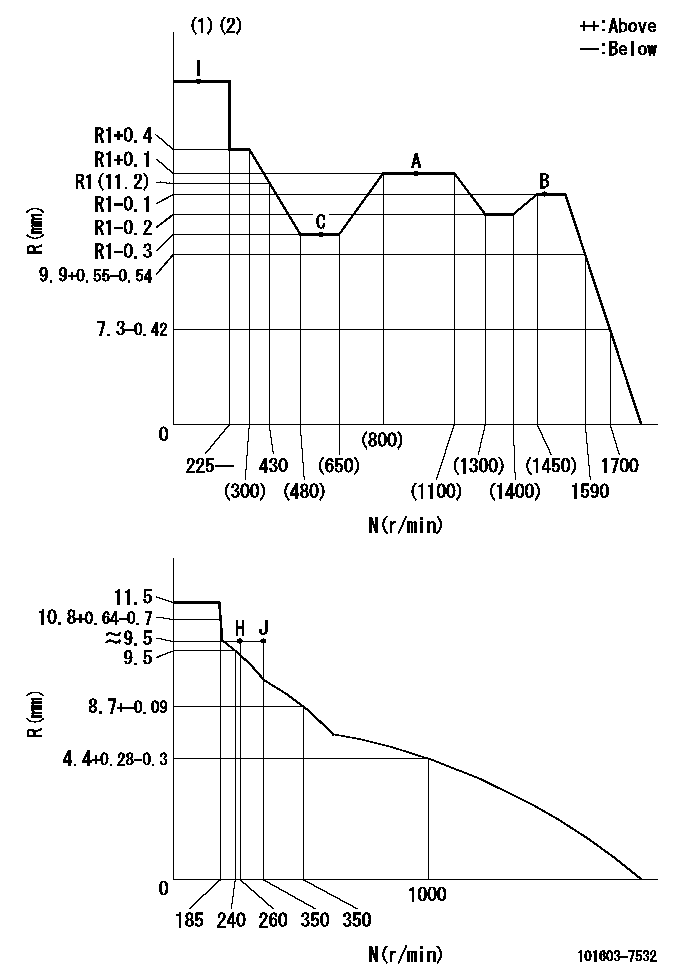
N:Pump speed
R:Rack position (mm)
(1)Torque cam stamping: T1
(2)Tolerance for racks not indicated: +-0.05mm.
----------
T1=G22
----------
----------
T1=G22
----------
Speed control lever angle

F:Full speed
I:Idle
(1)Use the pin at R = aa
(2)Stopper bolt set position 'H'
----------
aa=35mm
----------
a=11deg+-5deg b=(39deg)+-3deg
----------
aa=35mm
----------
a=11deg+-5deg b=(39deg)+-3deg
Stop lever angle
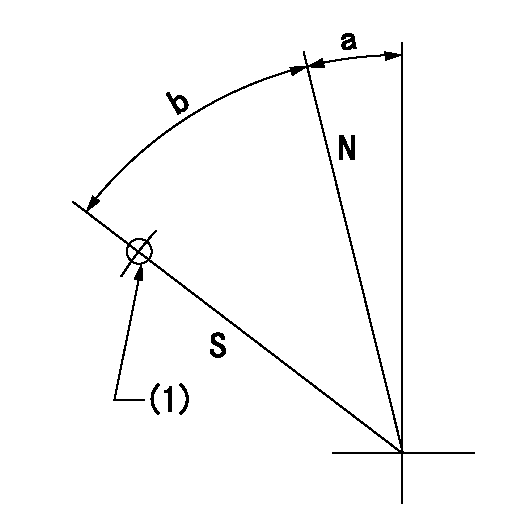
N:Pump normal
S:Stop the pump.
(1)Use the pin at R = aa
----------
aa=67mm
----------
a=16deg+-5deg b=29deg+-5deg
----------
aa=67mm
----------
a=16deg+-5deg b=29deg+-5deg
0000001501 I/P WITH LOAD PLUNGER ADJ
Plunger assembly number: PL (stamping: ST)
1. Adjustment procedures
(1)Insert the pre-stroke adjusting shims L1 for each cylinder.
(2)Adjust injection quantity.(max. var. bet. cyl. idling a1, full a2)
(3)At basic point A, adjust so that the pre-stroke is L2.
(4)Reconfirm the injection quantity.
----------
PL=131153-4520 ST=A724 L1=1mm L2=4.2+-0.05mm a1=+-14% a2=+-2.5%
----------
----------
PL=131153-4520 ST=A724 L1=1mm L2=4.2+-0.05mm a1=+-14% a2=+-2.5%
----------
Timing setting
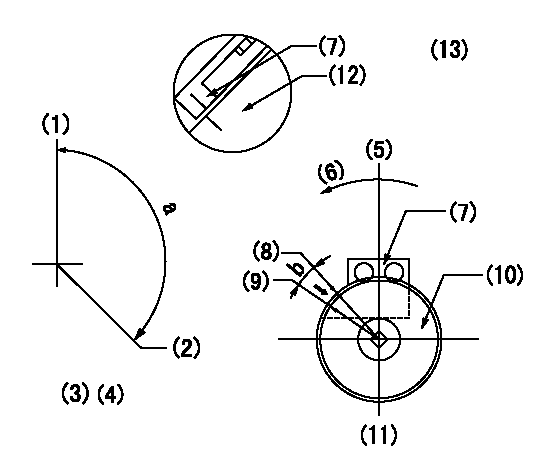
(1)Pump vertical direction
(2)Position of timer's threaded hole at No 1 cylinder's beginning of injection
(3)B.T.D.C.: aa
(4)-
(5)Pump vertical direction
(6)Direction of rotation
(7)Pointer
(8)Pointer stamping
(9)Timing device stamping
(10)Timing device
(11)Move b deg and stamp both at the same time as shown above.
(12)Outside circumference of timing device
(13)Secondary timing stamping position for the No. 1 cylinder's beginning of injection
----------
aa=11deg
----------
a=(150deg) b=1deg
----------
aa=11deg
----------
a=(150deg) b=1deg
Information:
Illustration 3 g01783679
Top view of machine
Illustration 4 g01783683
Right side view of machine (A) Hood and guard group (B) Lines group (Air) (C) Air cleaner
Illustration 5 g01783717
Front view of machineInstallation Procedure
The installation procedure that follows is specific for the listed machine.Diesel Particulate Filter Installation
Illustration 6 g01783522
(2) 331-8935 Bracket (12) 5P-8245 Hard Washer (13) 6V-8149 Nut (14) 8F-6437 Washer (15) 8T-4956 Bolt
Place two new 331-8935 Brackets (2) parallel to each other on top of the hood. Secure the brackets to the hood using four new 8F-6437 Washers (14), four new 5P-8245 Hard Washers (12), four new 6V-8149 Nuts (13), and four new 8T-4956 Bolts (15). Refer to Illustration 6.
Illustration 7 g01783527
(5) 295-3044 Exhaust Support Gp
Install the two lower halves of the new 295-3044 Exhaust Support Gp (5) onto two brackets (2) using four new washers (14) and four new bolts (15). Refer to Illustration 7.
Illustration 8 g01783553
(1) 331-8928 Diesel Particulate Filter Gp (5a) Bolt (5b) Hard washer (5c) Weld nut
Place the new 331-8928 Diesel Particulate Filter Gp (1) onto the two lower halves of exhaust support group (5). The weight of the diesel particulate filter group is approximately 44 kg (97 lb). Refer to Illustration 8.
Install the two upper halves of exhaust support group (5) onto the bottom halves of the exhaust support group using four 5P-8245 Hard Washers (5b), four 8T-3597 Weld Nuts (5c), and four 6V-3823 Bolt (5a). Refer to Illustration 8.
Illustration 9 g01783556
(a) Outlet module tube (9) 174-5414 Clamp (11) 255-2899 Tail Pipe As
Connect the new 255-2899 Tail Pipe As (11) to outlet module tube (a) of diesel particulate filter group (1) using a new 174-5414 Clamp (9). Refer to Illustration 9.
Illustration 10 g01783574
(b) Inlet module tube (3) 331-8931 Filter Tube As (7) 241-6170 Plug (8) 8T-6765 Pipe Plug (10) 209-4589 Clamp
Connect the new 331-8931 Filter Tube As (3) to inlet module tube (b) of diesel particulate filter group (1) using one new 209-4589 Clamp (10). Refer to Illustration 10.
Install the new 8T-6765 Pipe Plug (8) and 241-6170 Plug (7) onto the two respective bosses provided on filter tube assembly (3). Refer to Illustration 10.
Illustration 11 g01783595
(6) 270-0112 Bellows
Connect the new 270-0112 Bellows (6) to filter tube assembly (3) using one new clamp (10). Refer to Illustration 11.
Illustration 12 g01783578
(4) 331-8934 Filter Tube
Connect the new 331-8934 Filter Tube (4) to bellows (6) using one new clamp (10). Refer to Illustration 12.
Connect the other end of filter tube (4) to the air lines group using the clamp that is used to connect the muffler tube to the air lines group.Exhaust Monitor Installation
Refer to Special Instruction, REHS5606, "Installation and Operation of the Caterpillar Diesel Particulate Filter (DPF) and the Diagnostic Module for Non-Road Machine Applications (Non-California Applications)" for information regarding the installation and the operation of the exhaust monitor.The exhaust monitor is a device designed to monitor