Information injection-pump assembly
ZEXEL
101603-7450
1016037450
ISUZU
1156026531
1156026531
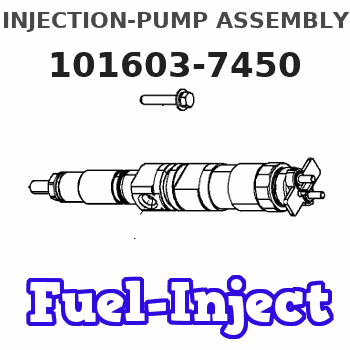
Rating:
Cross reference number
ZEXEL
101603-7450
1016037450
ISUZU
1156026531
1156026531
Zexel num
Bosch num
Firm num
Name
Calibration Data:
Adjustment conditions
Test oil
1404 Test oil ISO4113 or {SAEJ967d}
1404 Test oil ISO4113 or {SAEJ967d}
Test oil temperature
degC
40
40
45
Nozzle and nozzle holder
105780-8140
Bosch type code
EF8511/9A
Nozzle
105780-0000
Bosch type code
DN12SD12T
Nozzle holder
105780-2080
Bosch type code
EF8511/9
Opening pressure
MPa
17.2
Opening pressure
kgf/cm2
175
Injection pipe
Outer diameter - inner diameter - length (mm) mm 6-2-600
Outer diameter - inner diameter - length (mm) mm 6-2-600
Overflow valve
131424-4920
Overflow valve opening pressure
kPa
127
107
147
Overflow valve opening pressure
kgf/cm2
1.3
1.1
1.5
Tester oil delivery pressure
kPa
157
157
157
Tester oil delivery pressure
kgf/cm2
1.6
1.6
1.6
Direction of rotation (viewed from drive side)
Right R
Right R
Injection timing adjustment
Direction of rotation (viewed from drive side)
Right R
Right R
Injection order
1-5-3-6-
2-4
Pre-stroke
mm
3.6
3.55
3.65
Rack position
After adjusting injection quantity. R=A
After adjusting injection quantity. R=A
Beginning of injection position
Drive side NO.1
Drive side NO.1
Difference between angles 1
Cal 1-5 deg. 60 59.5 60.5
Cal 1-5 deg. 60 59.5 60.5
Difference between angles 2
Cal 1-3 deg. 120 119.5 120.5
Cal 1-3 deg. 120 119.5 120.5
Difference between angles 3
Cal 1-6 deg. 180 179.5 180.5
Cal 1-6 deg. 180 179.5 180.5
Difference between angles 4
Cyl.1-2 deg. 240 239.5 240.5
Cyl.1-2 deg. 240 239.5 240.5
Difference between angles 5
Cal 1-4 deg. 300 299.5 300.5
Cal 1-4 deg. 300 299.5 300.5
Injection quantity adjustment
Adjusting point
-
Rack position
13.3
Pump speed
r/min
850
850
850
Average injection quantity
mm3/st.
95.8
94.2
97.4
Max. variation between cylinders
%
0
-2.5
2.5
Basic
*
Fixing the rack
*
Standard for adjustment of the maximum variation between cylinders
*
Injection quantity adjustment_02
Adjusting point
H
Rack position
9.5+-0.5
Pump speed
r/min
275
275
275
Average injection quantity
mm3/st.
8
6.7
9.3
Max. variation between cylinders
%
0
-14
14
Fixing the rack
*
Standard for adjustment of the maximum variation between cylinders
*
Injection quantity adjustment_03
Adjusting point
A
Rack position
R1(13.3)
Pump speed
r/min
850
850
850
Average injection quantity
mm3/st.
95.8
94.8
96.8
Basic
*
Fixing the lever
*
Boost pressure
kPa
33.3
33.3
Boost pressure
mmHg
250
250
Injection quantity adjustment_04
Adjusting point
B
Rack position
R1-0.15
Pump speed
r/min
1400
1400
1400
Average injection quantity
mm3/st.
96.2
93
99.4
Fixing the lever
*
Boost pressure
kPa
33.3
33.3
Boost pressure
mmHg
250
250
Injection quantity adjustment_05
Adjusting point
C
Rack position
R2(R1-0.
55)
Pump speed
r/min
550
550
550
Average injection quantity
mm3/st.
77.6
74.4
80.8
Fixing the lever
*
Boost pressure
kPa
33.3
33.3
Boost pressure
mmHg
250
250
Injection quantity adjustment_06
Adjusting point
D
Rack position
R2-1.3
Pump speed
r/min
550
550
550
Average injection quantity
mm3/st.
54
50.8
57.2
Fixing the lever
*
Boost pressure
kPa
0
0
0
Boost pressure
mmHg
0
0
0
Injection quantity adjustment_07
Adjusting point
I
Rack position
-
Pump speed
r/min
150
150
150
Average injection quantity
mm3/st.
93
93
125
Fixing the lever
*
Boost compensator adjustment
Pump speed
r/min
550
550
550
Rack position
R2-1.3
Boost pressure
kPa
2
2
4.7
Boost pressure
mmHg
15
15
35
Boost compensator adjustment_02
Pump speed
r/min
550
550
550
Rack position
R2(R1-0.
55)
Boost pressure
kPa
20
20
20
Boost pressure
mmHg
150
150
150
Timer adjustment
Pump speed
r/min
(1170)
Advance angle
deg.
0
0
0
Remarks
Start
Start
Timer adjustment_02
Pump speed
r/min
1325
Advance angle
deg.
1.5
1
2
Timer adjustment_03
Pump speed
r/min
1400
Advance angle
deg.
2
1.5
2.5
Remarks
Finish
Finish
Test data Ex:
Governor adjustment
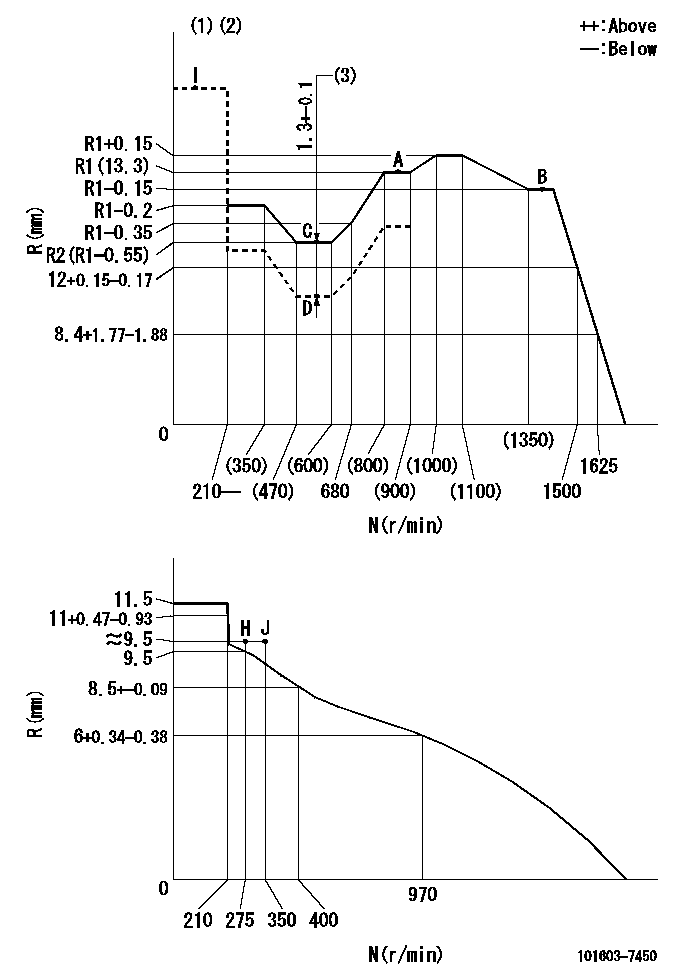
N:Pump speed
R:Rack position (mm)
(1)Torque cam stamping: T1
(2)Tolerance for racks not indicated: +-0.05mm.
(3)Boost compensator stroke
----------
T1=E95
----------
----------
T1=E95
----------
Speed control lever angle

F:Full speed
I:Idle
(1)Use the hole at R = aa
(2)Stopper bolt set position 'H'
----------
aa=48mm
----------
a=43deg+-5deg b=37deg+-3deg
----------
aa=48mm
----------
a=43deg+-5deg b=37deg+-3deg
Stop lever angle

N:Pump normal
S:Stop the pump.
----------
----------
a=25deg+-5deg b=40deg+-5deg
----------
----------
a=25deg+-5deg b=40deg+-5deg
0000001501 RACK SENSOR

V1:Supply voltage
V2f:Full side output voltage
V2i:Idle side output voltage
(A) Black
(B) Yellow
(C) Red
(D) Trimmer
(E): Shaft
(F) Nut
(G) Load lever
1. Load sensor adjustment
(1)Connect as shown in the above diagram and apply supply voltage V1.
(2)Hold the load lever (G) against the full side.
(3)Turn the shaft so that the voltage between (A) and (B) is V2.
(4)Hold the load lever (G) against the idle side.
(5)Adjust (D) so that the voltage between (A) and (B) is V2i.
(6)Repeat the above adjustments.
(7)Tighten the nut (F) at the point satisfying the standards.
(8)Hold the load lever against the full side stopper and the idle side stopper.
(9)At this time, confirm that the full side output voltage is V2f and the idle side output voltage is V2i.
----------
V1=5+-0.02V V2f=0.15+0.03V V2i=2.35-0.03V
----------
----------
V1=5+-0.02V V2f=0.15+0.03V V2i=2.35-0.03V
----------
0000001601 I/P WITH LOAD PLUNGER ADJ
Plunger assembly number: PL (stamping: ST)
1. Adjustment procedures
(1)Insert the pre-stroke adjusting shims L1 for each cylinder.
(2)Adjust injection quantity.(max. var. bet. cyl. idling a1, full a2)
(3)At basic point A, adjust so that the pre-stroke is L2.
(4)Reconfirm the injection quantity.
----------
PL=131153-4720 ST=A726 L1=1mm L2=3.6+-0.05mm a1=+-14% a2=+-2.5%
----------
----------
PL=131153-4720 ST=A726 L1=1mm L2=3.6+-0.05mm a1=+-14% a2=+-2.5%
----------
Timing setting
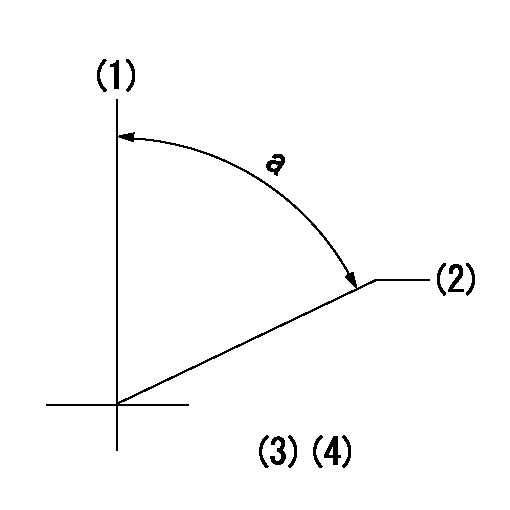
(1)Pump vertical direction
(2)Position of timer's threaded hole at No 1 cylinder's beginning of injection
(3)B.T.D.C.: aa
(4)-
----------
aa=10deg
----------
a=(60deg)
----------
aa=10deg
----------
a=(60deg)
Information:
Introduction
Do not perform any procedure in this Special Instruction until you have read the information and you understand the information.DEF injectors are being replaced in the field and returned to Caterpillar for testing. Results of the testing are finding a large portion of the returned DEF injectors are found to be fault not repeated.This form is to be used and filled out in any case that a DEF injector is being replaced.The DEF injector troubleshooting return form needs to be completed and included within failed part returns documenting what was found that led to DEF injector replacement. Attach the photos of DEF injector tip and mount area along with a Product Status Report to the SIMS claim.References
Table 1
Engine Publication Type Media Number
C7.1 Troubleshooting UENR0668
Testing and Adjusting UENR4467
Disassembly and Assembly UENR4468
C9.3 Troubleshooting UENR0978
Testing and Adjusting UENR3402
Disassembly and Assembly UENR0130
C13 Troubleshooting UENR0955
Testing and Adjusting UENR4302
Disassembly and Assembly UENR0131
C15/C18 Troubleshooting UENR0955
Testing and Adjusting UENR3351
Disassembly and Assembly UENR0132 Procedure
What code are you troubleshooting? __________
Follow the correct troubleshooting procedure. Reference Table 1 for correct media number to use.
When troubleshooting procedure requests the DEF quality check, DEF injector resistance measurement, or Dosing Accuracy Test, document those results in Tables 2, 3, and 4.Tables
Table 2
DEF Quality Results
Step Instruction Completed (Yes/No) Result Comments Units
1 Follow the Testing and Adjusting procedure for "Diesel Exhaust Fluid Quality - Test"
2 DEF Contamination Test Pass / Fail
3 DEF Concentration Test % at 20° C (68° F)
Illustration 1 g06175415
Table 3
Injector Resistance Measurement
Step Instruction Completed (Yes/No) Result Comments Units
1 Turn the keyswitch to the OFF position. Allow 2 minutes to elapse before proceeding.
2 Disconnect the DEF injectors from the applicable harness.
3 Inspect the connector for damage and debris.
4 Measure the temperature of the injector (aluminum body). C
5 Connect two 398-4987 Probes to the DEF injector. The connectors must be used to prevent damage to the DEF injector connector. Reference Illustration 1 for example.
6 Measure the resistance of the DEF injector. Ohms
Table 4
Dosing Accuracy Test
Step Instruction Completed (Yes/No) Result Comments Units
1 Follow the Testing and Adjusting procedure for "Aftertreatment SCR System Dosing - Test"
2 Remove the injector from the DPF outlet.
3 Take a photograph of the DEF injector mount on the DPF outlet and the tip of the DEF injector.
4 Install the injector on the beaker.
5 Run the DEF System Dosing Accuracy test through Cat® Electronic Technician (ET).
6 Use the beaker to measure the amount of fluid from the dosing test. ml
7 Repeat the test to verify consistency. ml
8 Install the injector back onto the DPF outlet.
Do not perform any procedure in this Special Instruction until you have read the information and you understand the information.DEF injectors are being replaced in the field and returned to Caterpillar for testing. Results of the testing are finding a large portion of the returned DEF injectors are found to be fault not repeated.This form is to be used and filled out in any case that a DEF injector is being replaced.The DEF injector troubleshooting return form needs to be completed and included within failed part returns documenting what was found that led to DEF injector replacement. Attach the photos of DEF injector tip and mount area along with a Product Status Report to the SIMS claim.References
Table 1
Engine Publication Type Media Number
C7.1 Troubleshooting UENR0668
Testing and Adjusting UENR4467
Disassembly and Assembly UENR4468
C9.3 Troubleshooting UENR0978
Testing and Adjusting UENR3402
Disassembly and Assembly UENR0130
C13 Troubleshooting UENR0955
Testing and Adjusting UENR4302
Disassembly and Assembly UENR0131
C15/C18 Troubleshooting UENR0955
Testing and Adjusting UENR3351
Disassembly and Assembly UENR0132 Procedure
What code are you troubleshooting? __________
Follow the correct troubleshooting procedure. Reference Table 1 for correct media number to use.
When troubleshooting procedure requests the DEF quality check, DEF injector resistance measurement, or Dosing Accuracy Test, document those results in Tables 2, 3, and 4.Tables
Table 2
DEF Quality Results
Step Instruction Completed (Yes/No) Result Comments Units
1 Follow the Testing and Adjusting procedure for "Diesel Exhaust Fluid Quality - Test"
2 DEF Contamination Test Pass / Fail
3 DEF Concentration Test % at 20° C (68° F)
Illustration 1 g06175415
Table 3
Injector Resistance Measurement
Step Instruction Completed (Yes/No) Result Comments Units
1 Turn the keyswitch to the OFF position. Allow 2 minutes to elapse before proceeding.
2 Disconnect the DEF injectors from the applicable harness.
3 Inspect the connector for damage and debris.
4 Measure the temperature of the injector (aluminum body). C
5 Connect two 398-4987 Probes to the DEF injector. The connectors must be used to prevent damage to the DEF injector connector. Reference Illustration 1 for example.
6 Measure the resistance of the DEF injector. Ohms
Table 4
Dosing Accuracy Test
Step Instruction Completed (Yes/No) Result Comments Units
1 Follow the Testing and Adjusting procedure for "Aftertreatment SCR System Dosing - Test"
2 Remove the injector from the DPF outlet.
3 Take a photograph of the DEF injector mount on the DPF outlet and the tip of the DEF injector.
4 Install the injector on the beaker.
5 Run the DEF System Dosing Accuracy test through Cat® Electronic Technician (ET).
6 Use the beaker to measure the amount of fluid from the dosing test. ml
7 Repeat the test to verify consistency. ml
8 Install the injector back onto the DPF outlet.