Information injection-pump assembly
ZEXEL
101603-7283
1016037283
ISUZU
8943970564
8943970564
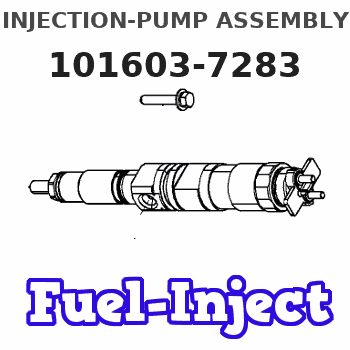
Rating:
Service parts 101603-7283 INJECTION-PUMP ASSEMBLY:
1.
_
7.
COUPLING PLATE
8.
_
9.
_
11.
Nozzle and Holder
8-94397-054-0
12.
Open Pre:MPa(Kqf/cm2)
18.1{185}
15.
NOZZLE SET
Cross reference number
ZEXEL
101603-7283
1016037283
ISUZU
8943970564
8943970564
Zexel num
Bosch num
Firm num
Name
Calibration Data:
Adjustment conditions
Test oil
1404 Test oil ISO4113 or {SAEJ967d}
1404 Test oil ISO4113 or {SAEJ967d}
Test oil temperature
degC
40
40
45
Nozzle and nozzle holder
105780-8140
Bosch type code
EF8511/9A
Nozzle
105780-0000
Bosch type code
DN12SD12T
Nozzle holder
105780-2080
Bosch type code
EF8511/9
Opening pressure
MPa
17.2
Opening pressure
kgf/cm2
175
Injection pipe
Outer diameter - inner diameter - length (mm) mm 6-2-600
Outer diameter - inner diameter - length (mm) mm 6-2-600
Overflow valve opening pressure
kPa
157
123
191
Overflow valve opening pressure
kgf/cm2
1.6
1.25
1.95
Tester oil delivery pressure
kPa
157
157
157
Tester oil delivery pressure
kgf/cm2
1.6
1.6
1.6
Direction of rotation (viewed from drive side)
Left L
Left L
Injection timing adjustment
Direction of rotation (viewed from drive side)
Left L
Left L
Injection order
1-5-3-6-
2-4
Pre-stroke
mm
3.7
3.65
3.75
Rack position
After adjusting injection quantity. R=A
After adjusting injection quantity. R=A
Beginning of injection position
Governor side NO.1
Governor side NO.1
Difference between angles 1
Cal 1-5 deg. 60 59.5 60.5
Cal 1-5 deg. 60 59.5 60.5
Difference between angles 2
Cal 1-3 deg. 120 119.5 120.5
Cal 1-3 deg. 120 119.5 120.5
Difference between angles 3
Cal 1-6 deg. 180 179.5 180.5
Cal 1-6 deg. 180 179.5 180.5
Difference between angles 4
Cyl.1-2 deg. 240 239.5 240.5
Cyl.1-2 deg. 240 239.5 240.5
Difference between angles 5
Cal 1-4 deg. 300 299.5 300.5
Cal 1-4 deg. 300 299.5 300.5
Injection quantity adjustment
Adjusting point
-
Rack position
12.2
Pump speed
r/min
900
900
900
Average injection quantity
mm3/st.
63
61.4
64.6
Max. variation between cylinders
%
0
-2.5
2.5
Basic
*
Fixing the rack
*
Standard for adjustment of the maximum variation between cylinders
*
Injection quantity adjustment_02
Adjusting point
H
Rack position
9.5+-0.5
Pump speed
r/min
260
260
260
Average injection quantity
mm3/st.
8
6.7
9.3
Max. variation between cylinders
%
0
-14
14
Fixing the rack
*
Standard for adjustment of the maximum variation between cylinders
*
Injection quantity adjustment_03
Adjusting point
A
Rack position
R1(12.2)
Pump speed
r/min
900
900
900
Average injection quantity
mm3/st.
63
62
64
Basic
*
Fixing the lever
*
Injection quantity adjustment_04
Adjusting point
B
Rack position
R1+0.1
Pump speed
r/min
1400
1400
1400
Average injection quantity
mm3/st.
71.1
67.9
74.3
Fixing the lever
*
Injection quantity adjustment_05
Adjusting point
I
Rack position
-
Pump speed
r/min
150
150
150
Average injection quantity
mm3/st.
102
102
134
Fixing the lever
*
Timer adjustment
Pump speed
r/min
1150
Advance angle
deg.
0.5
Timer adjustment_02
Pump speed
r/min
1300
Advance angle
deg.
2
1.5
2.5
Timer adjustment_03
Pump speed
r/min
1500
Advance angle
deg.
5.5
5
6
Remarks
Finish
Finish
Test data Ex:
Governor adjustment
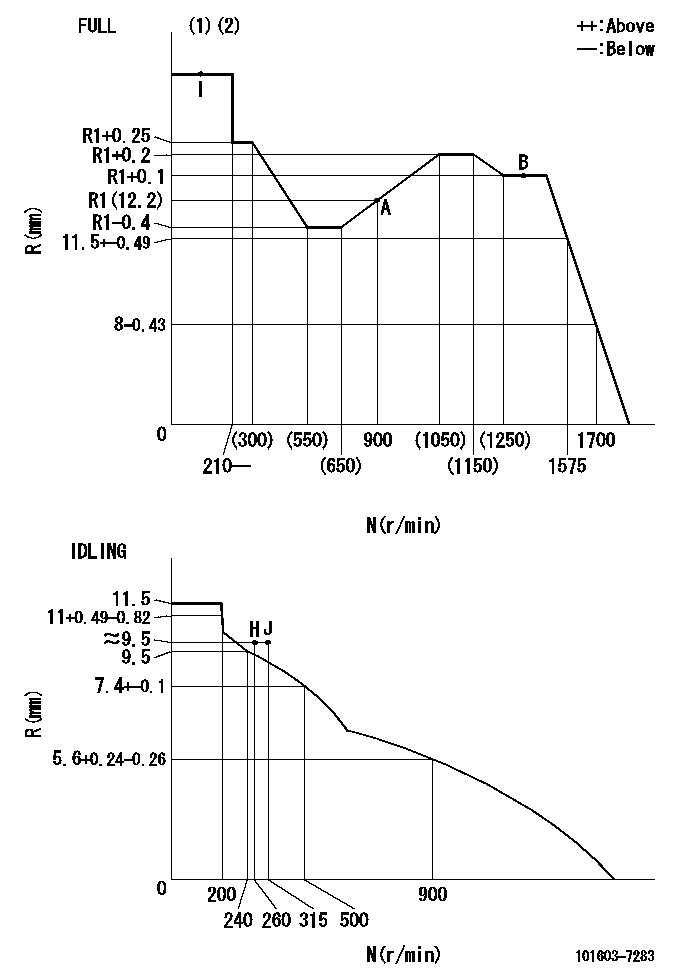
N:Pump speed
R:Rack position (mm)
(1)Torque cam stamping: T1
(2)Tolerance for racks not indicated: +-0.05mm.
----------
T1=E28
----------
----------
T1=E28
----------
Speed control lever angle
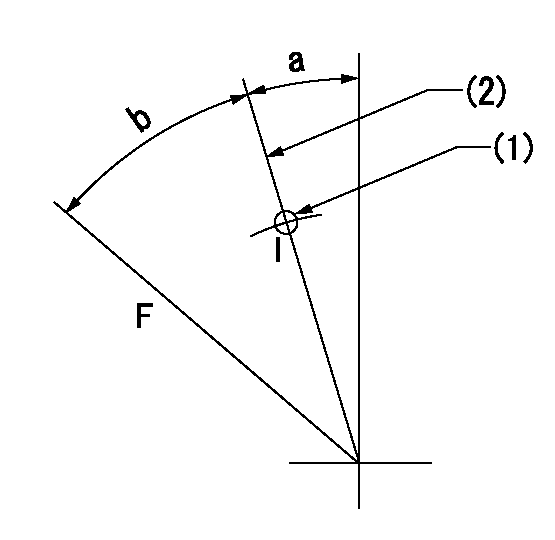
F:Full speed
I:Idle
(1)Use the pin at R = aa
(2)Stopper bolt set position 'H'
----------
aa=35mm
----------
a=10deg+-5deg b=(36.5deg)+-3deg
----------
aa=35mm
----------
a=10deg+-5deg b=(36.5deg)+-3deg
Stop lever angle

N:Pump normal
S:Stop the pump.
----------
----------
a=12.5deg+-5deg b=40deg+-5deg
----------
----------
a=12.5deg+-5deg b=40deg+-5deg
0000001501 I/P WITH LOAD PLUNGER ADJ
Plunger assembly number: PL (stamping: ST)
1. Adjustment procedures
(1)Insert the pre-stroke adjusting shims L1 for each cylinder.
(2)Adjust injection quantity.(max. var. bet. cyl. idling a1, full a2)
(3)At basic point A, adjust so that the pre-stroke is L2.
(4)Reconfirm the injection quantity.
----------
PL=131154-1320 ST=A255 L1=1mm L2=3.7+-0.05mm a1=+-14% a2=+-2.5%
----------
----------
PL=131154-1320 ST=A255 L1=1mm L2=3.7+-0.05mm a1=+-14% a2=+-2.5%
----------
Timing setting

(1)Pump vertical direction
(2)Position of timer's threaded hole at No 1 cylinder's beginning of injection
(3)B.T.D.C.: aa
(4)-
----------
aa=10deg
----------
a=(160deg)
----------
aa=10deg
----------
a=(160deg)
Information:
PARTS NEEDED
Qty
Part Number Description
2 1790133 FILM-AIR SHUTOFF
2 2898498 DAMPER AS
ACTION REQUIRED
Refer to the attached Rework Procedure.
OWNER NOTIFICATION
U.S. and Canadian owners will receive the attached Owner Notification.
SERVICE CLAIM ALLOWANCES
Caterpillar Dealer Suggested Customer Suggested
Parts % Labor Hrs% Parts % Labor Hrs% Parts % Labor Hrs%
100% 100% 0% 0% 0% 0%
This is a 1.0-hour job
PARTS DISPOSITION
Handle the parts in accordance with your Warranty Bulletin on warranty parts handling.
MAKE EVERY EFFORT TO COMPLETE THIS PROGRAM AS SOON AS POSSIBLE.
COPY OF OWNER NOTIFICATION FOR U.S. AND CANADIAN OWNERS
XYZ Corporation
3240 Arrow Drive
Anywhere, YZ 99999
PRIORITY - PRODUCT IMPROVEMENT PROGRAM FOR ADDING VIBRATION DAMPERS TO AIR SHUT OFFS
MODELS INVOLVED - CERTAIN 3500 DIESEL ENGINES
Dear Caterpillar Product Owner:
New vibration dampers need to be installed on the products listed. You will not be charged for the service performed. Contact your local Caterpillar dealer immediately to schedule this service. The dealer will advise you of the time required to complete this service.
It is VERY IMPORTANT that your Air Shut Offs be tested every 500 operating hours and the vibration dampers installed on the ASOs need to be inspected/serviced every 6000 operating hours. Please contact your Caterpillar Dealer for a copy of Caterpillar Special Instruction REHS3005, which details this procedure. A COPY OF THIS DOCUMENT SHOULD BE PLACED IN THE APPLICABLE Operating and Maintenance Manuals.
Please refer the dealer to their Service Letter dated 27Jul2006 when scheduling this service.
We regret the inconvenience this may cause you, but urge you to have this service performed as soon as possible to prevent unscheduled downtime.
Caterpillar Inc.
Identification #(s)
Attached to 27Jul2006 Service Letter
Rework Procedure
1. Remove existing plug from bottom of each Air Shut Off (ASO) housing, Image 1.1.1
Image1.1.1
2. Install new Vibration Damper P/N 289-8498 into the hole as shown in image 1.2.1, insuring that the threads are coated with Thread lock P/N 9S-3263 or 4C-4030 and torque the damper to 16 (+/- 2)Nm.
Image1.2.1
3. Install information labels over existing labels on the electrically actuated ASO solenoids as shown in image 1.3.1 or on hydraulically actuated ASO valve covers as shown in image 1.3.2.
Labels in languages other than English are available under the following Part Numbers:
-Arabic 297-2613
-French 297-2614
-German 297-2615
-Spanish 297-2616
-Portuguese 297-2617
-Russian 297-2618
Image1.3.1
Image1.3.2