Information injection-pump assembly
ZEXEL
101603-6880
1016036880
MITSUBISHI
ME035348
me035348
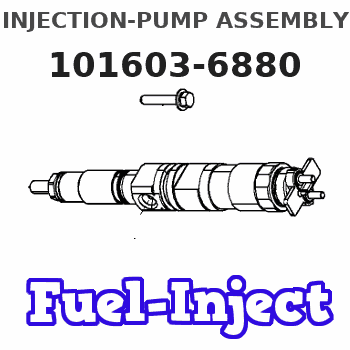
Rating:
Service parts 101603-6880 INJECTION-PUMP ASSEMBLY:
1.
_
6.
COUPLING PLATE
7.
COUPLING PLATE
8.
_
9.
_
11.
Nozzle and Holder
ME035748
12.
Open Pre:MPa(Kqf/cm2)
21.6(220)
15.
NOZZLE SET
Include in #1:
101603-6880
as INJECTION-PUMP ASSEMBLY
Include in #2:
104749-6981
as _
Cross reference number
ZEXEL
101603-6880
1016036880
MITSUBISHI
ME035348
me035348
Zexel num
Bosch num
Firm num
Name
Calibration Data:
Adjustment conditions
Test oil
1404 Test oil ISO4113 or {SAEJ967d}
1404 Test oil ISO4113 or {SAEJ967d}
Test oil temperature
degC
40
40
45
Nozzle and nozzle holder
105780-8140
Bosch type code
EF8511/9A
Nozzle
105780-0000
Bosch type code
DN12SD12T
Nozzle holder
105780-2080
Bosch type code
EF8511/9
Opening pressure
MPa
17.2
Opening pressure
kgf/cm2
175
Injection pipe
Outer diameter - inner diameter - length (mm) mm 6-2-600
Outer diameter - inner diameter - length (mm) mm 6-2-600
Overflow valve
131424-5520
Overflow valve opening pressure
kPa
255
221
289
Overflow valve opening pressure
kgf/cm2
2.6
2.25
2.95
Tester oil delivery pressure
kPa
157
157
157
Tester oil delivery pressure
kgf/cm2
1.6
1.6
1.6
Direction of rotation (viewed from drive side)
Left L
Left L
Injection timing adjustment
Direction of rotation (viewed from drive side)
Left L
Left L
Injection order
1-5-3-6-
2-4
Pre-stroke
mm
3.6
3.55
3.65
Beginning of injection position
Governor side NO.1
Governor side NO.1
Difference between angles 1
Cal 1-5 deg. 60 59.5 60.5
Cal 1-5 deg. 60 59.5 60.5
Difference between angles 2
Cal 1-3 deg. 120 119.5 120.5
Cal 1-3 deg. 120 119.5 120.5
Difference between angles 3
Cal 1-6 deg. 180 179.5 180.5
Cal 1-6 deg. 180 179.5 180.5
Difference between angles 4
Cyl.1-2 deg. 240 239.5 240.5
Cyl.1-2 deg. 240 239.5 240.5
Difference between angles 5
Cal 1-4 deg. 300 299.5 300.5
Cal 1-4 deg. 300 299.5 300.5
Injection quantity adjustment
Adjusting point
-
Rack position
10.8
Pump speed
r/min
850
850
850
Each cylinder's injection qty
mm3/st.
60
58.1
61.9
Basic
*
Fixing the rack
*
Standard for adjustment of the maximum variation between cylinders
*
Injection quantity adjustment_02
Adjusting point
H
Rack position
9.5+-0.5
Pump speed
r/min
275
275
275
Each cylinder's injection qty
mm3/st.
9.3
8.2
10.4
Fixing the rack
*
Standard for adjustment of the maximum variation between cylinders
*
Injection quantity adjustment_03
Adjusting point
A
Rack position
R1(10.8)
Pump speed
r/min
850
850
850
Average injection quantity
mm3/st.
60
59
61
Basic
*
Fixing the lever
*
Injection quantity adjustment_04
Adjusting point
B
Rack position
R1+0.6
Pump speed
r/min
1450
1450
1450
Average injection quantity
mm3/st.
80.5
78.5
82.5
Fixing the lever
*
Injection quantity adjustment_05
Adjusting point
C
Rack position
R1-0.4
Pump speed
r/min
600
600
600
Average injection quantity
mm3/st.
42.5
40.5
44.5
Fixing the lever
*
Injection quantity adjustment_06
Adjusting point
I
Rack position
-
Pump speed
r/min
100
100
100
Average injection quantity
mm3/st.
80
75
85
Fixing the lever
*
Rack limit
*
Timer adjustment
Pump speed
r/min
1250--
Advance angle
deg.
0
0
0
Remarks
Start
Start
Timer adjustment_02
Pump speed
r/min
1200
Advance angle
deg.
0.5
Timer adjustment_03
Pump speed
r/min
1350
Advance angle
deg.
2.4
1.9
2.9
Timer adjustment_04
Pump speed
r/min
1500
Advance angle
deg.
5
4.5
5.5
Remarks
Finish
Finish
Test data Ex:
Governor adjustment
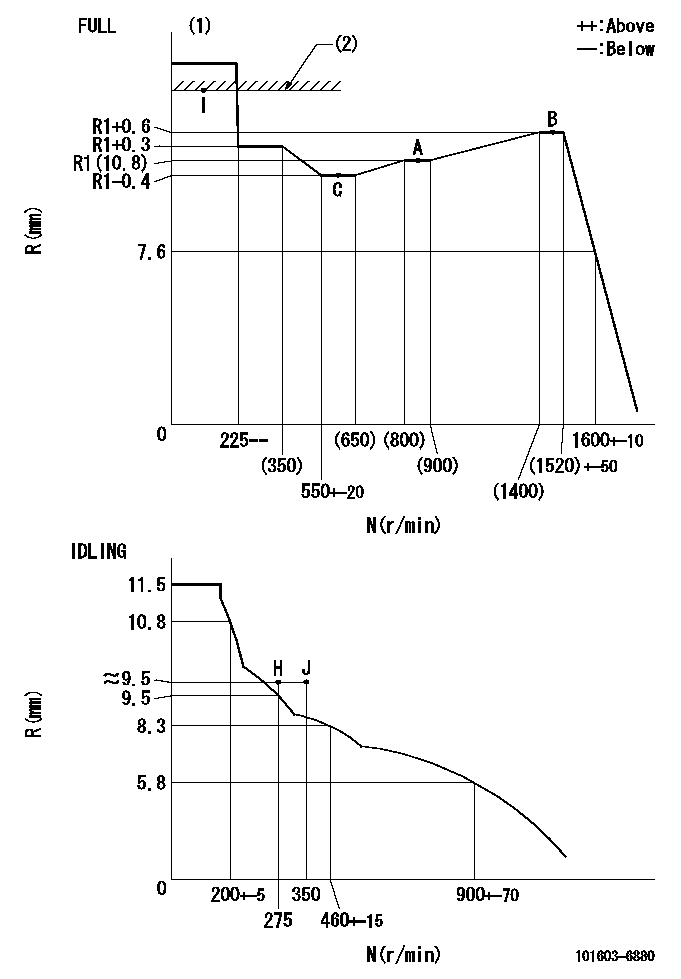
N:Pump speed
R:Rack position (mm)
(1)Torque cam stamping: T1
(2)RACK LIMIT
----------
T1=A77
----------
----------
T1=A77
----------
Speed control lever angle

F:Full speed
I:Idle
(1)Stopper bolt set position 'H'
----------
----------
a=10deg+-5deg b=(46deg)+-3deg
----------
----------
a=10deg+-5deg b=(46deg)+-3deg
Stop lever angle
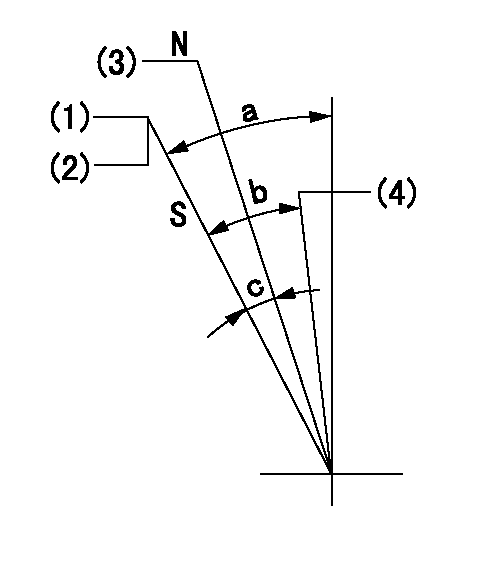
N:Engine manufacturer's normal use
S:Stop the pump.
(1)Set the stopper bolt at speed = rated point and rack position = aa (non-injection rack position). Confirm non-injection.
(2)After setting the stopper bolt , confirm non-injection at pump speed bb. Rack position = cc (non-injection rack position).
(3)Rack position = approximately dd
(4)Free (at shipping)
----------
aa=7.1mm bb=275r/min cc=8.8mm dd=15mm
----------
a=38deg+-5deg b=(26.5deg) c=12.5deg+-3deg
----------
aa=7.1mm bb=275r/min cc=8.8mm dd=15mm
----------
a=38deg+-5deg b=(26.5deg) c=12.5deg+-3deg
0000001501 MICRO SWITCH
Adjustment of the micro-switch
Adjust the bolt to obtain the following lever position when the micro-switch is ON.
(1)Speed N1
(2)Rack position Ra
----------
N1=400+-5r/min Ra=9.2mm
----------
----------
N1=400+-5r/min Ra=9.2mm
----------
Timing setting

(1)Pump vertical direction
(2)Position of timer's tooth at No 1 cylinder's beginning of injection
(3)B.T.D.C.: aa
(4)-
----------
aa=12deg
----------
a=(1deg)
----------
aa=12deg
----------
a=(1deg)
Information:
A pressurized cooling system serves two purposes. First, it permits safe operation at coolant temperatures higher than the normal boiling point; thereby, providing a margin of cooling for those intermittent peak loads. Secondly, it prevents cavitation in the water pump and reduces the possibility of air or steam pockets forming in the coolant passages.Many times engine overheating is caused by failure to make simple systematic inspections. Visual inspections should be made before testing. Coolant Level: Check the engine coolant level with engine stopped and cool. Always release cooling system pressure before checking. Fill to the proper level with water, as free as possible from scale forming minerals, not softened water. During freezing weather add sufficient permanent type antifreeze to the coolant to prevent freezing. Make up water added without the proper proportions of inhibitor can cause excessive mineral deposits. (Use inhibitor as recommended on container.)Most commercial antifreeze solutions contain rust inhibitors, however, it is recommended the adding of Caterpillar Coolant System Inhibitor to glycol base antifreeze if protection is for temperatures above -20°F (-29°C). If protection is for temperatures -20°F (-29°C) or below, do not add inhibitor.
Inhibitor contains alkali. Avoid contact with eyes. Avoid prolonged or repeated contact with skin.
Add coolant slowly to a hot engine (engine running) to prevent possible cracking or distorting the cylinder heads.
If a loss of coolant is noticeable, check for leaks in the system. After filling the system, start the engine and add coolant as necessary to maintain a full system during engine warm up. Running the engine at operating temperature will permit the temperature regulator to open and allow the coolant to circulate and purge air from the entire system. Some systems will normally loose some coolant during initial warm up cycle. Cleaning the Radiator (External): Clean dirt and trash from between the tubes of the radiator. Accumulation of debris may cause excessively high operating temperature. Wash, brush or blow the dirt out with whichever method is available and most effective. When cleaning with air do not exceed 30 PSI (2 kg/cm2). Cleaning the Cooling System (Internal): Clean the cooling system periodically. Mineral deposits can cause serious engine damage by retarding the transfer of heat to the coolant. A deposit of lime 1/32 inch thick insulates the same amount as 2 inches of steel, reducing the heat transfer substantially. Loose scale and sediment deposited in the cooling system will reduce circulation, resulting in possible engine damage. To clean, stop the engine when it is at normal operating temperature and drain as quickly as possible. Flush thoroughly, then fill with a solution of 3.2 ounces of Oxalic Acid or Sodium Bisulfate per one gallon of water. Run the engine at operating temperature one-half to one hour, then drain and flush until water is clear. Fill with a solution of .8 of an ounce of Sal Soda per one gallon of water and run the engine ten minutes. Drain, flush and fill with water, adding corrosion inhibitor or the desired amount of antifreeze.
ENGINE DRAIN
Inhibitor contains alkali. Avoid contact with eyes. Avoid prolonged or repeated contact with skin.
Add coolant slowly to a hot engine (engine running) to prevent possible cracking or distorting the cylinder heads.
If a loss of coolant is noticeable, check for leaks in the system. After filling the system, start the engine and add coolant as necessary to maintain a full system during engine warm up. Running the engine at operating temperature will permit the temperature regulator to open and allow the coolant to circulate and purge air from the entire system. Some systems will normally loose some coolant during initial warm up cycle. Cleaning the Radiator (External): Clean dirt and trash from between the tubes of the radiator. Accumulation of debris may cause excessively high operating temperature. Wash, brush or blow the dirt out with whichever method is available and most effective. When cleaning with air do not exceed 30 PSI (2 kg/cm2). Cleaning the Cooling System (Internal): Clean the cooling system periodically. Mineral deposits can cause serious engine damage by retarding the transfer of heat to the coolant. A deposit of lime 1/32 inch thick insulates the same amount as 2 inches of steel, reducing the heat transfer substantially. Loose scale and sediment deposited in the cooling system will reduce circulation, resulting in possible engine damage. To clean, stop the engine when it is at normal operating temperature and drain as quickly as possible. Flush thoroughly, then fill with a solution of 3.2 ounces of Oxalic Acid or Sodium Bisulfate per one gallon of water. Run the engine at operating temperature one-half to one hour, then drain and flush until water is clear. Fill with a solution of .8 of an ounce of Sal Soda per one gallon of water and run the engine ten minutes. Drain, flush and fill with water, adding corrosion inhibitor or the desired amount of antifreeze.
ENGINE DRAIN