Information injection-pump assembly
BOSCH
9 400 610 652
9400610652
ZEXEL
101603-6860
1016036860
MITSUBISHI
ME035346
me035346
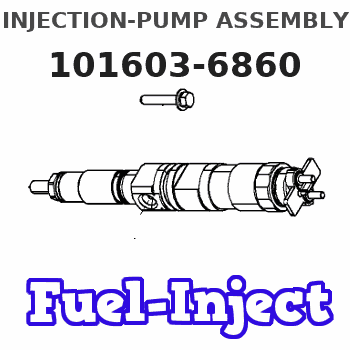
Rating:
Service parts 101603-6860 INJECTION-PUMP ASSEMBLY:
1.
_
6.
COUPLING PLATE
7.
COUPLING PLATE
8.
_
9.
_
11.
Nozzle and Holder
ME035655
12.
Open Pre:MPa(Kqf/cm2)
21.6{220}
15.
NOZZLE SET
Include in #1:
101603-6860
as INJECTION-PUMP ASSEMBLY
Include in #2:
104741-1754
as _
Cross reference number
BOSCH
9 400 610 652
9400610652
ZEXEL
101603-6860
1016036860
MITSUBISHI
ME035346
me035346
Zexel num
Bosch num
Firm num
Name
Calibration Data:
Adjustment conditions
Test oil
1404 Test oil ISO4113 or {SAEJ967d}
1404 Test oil ISO4113 or {SAEJ967d}
Test oil temperature
degC
40
40
45
Nozzle and nozzle holder
105780-8140
Bosch type code
EF8511/9A
Nozzle
105780-0000
Bosch type code
DN12SD12T
Nozzle holder
105780-2080
Bosch type code
EF8511/9
Opening pressure
MPa
17.2
Opening pressure
kgf/cm2
175
Injection pipe
Outer diameter - inner diameter - length (mm) mm 6-2-600
Outer diameter - inner diameter - length (mm) mm 6-2-600
Overflow valve
131424-5520
Overflow valve opening pressure
kPa
255
221
289
Overflow valve opening pressure
kgf/cm2
2.6
2.25
2.95
Tester oil delivery pressure
kPa
157
157
157
Tester oil delivery pressure
kgf/cm2
1.6
1.6
1.6
Direction of rotation (viewed from drive side)
Left L
Left L
Injection timing adjustment
Direction of rotation (viewed from drive side)
Left L
Left L
Injection order
1-5-3-6-
2-4
Pre-stroke
mm
3.3
3.25
3.35
Beginning of injection position
Governor side NO.1
Governor side NO.1
Difference between angles 1
Cal 1-5 deg. 60 59.5 60.5
Cal 1-5 deg. 60 59.5 60.5
Difference between angles 2
Cal 1-3 deg. 120 119.5 120.5
Cal 1-3 deg. 120 119.5 120.5
Difference between angles 3
Cal 1-6 deg. 180 179.5 180.5
Cal 1-6 deg. 180 179.5 180.5
Difference between angles 4
Cyl.1-2 deg. 240 239.5 240.5
Cyl.1-2 deg. 240 239.5 240.5
Difference between angles 5
Cal 1-4 deg. 300 299.5 300.5
Cal 1-4 deg. 300 299.5 300.5
Injection quantity adjustment
Adjusting point
-
Rack position
11
Pump speed
r/min
850
850
850
Each cylinder's injection qty
mm3/st.
65
63
67
Basic
*
Fixing the rack
*
Standard for adjustment of the maximum variation between cylinders
*
Injection quantity adjustment_02
Adjusting point
H
Rack position
9.5+-0.5
Pump speed
r/min
275
275
275
Each cylinder's injection qty
mm3/st.
10.5
9
12
Fixing the rack
*
Standard for adjustment of the maximum variation between cylinders
*
Injection quantity adjustment_03
Adjusting point
A
Rack position
R1(11)
Pump speed
r/min
850
850
850
Average injection quantity
mm3/st.
65
64
66
Basic
*
Fixing the lever
*
Injection quantity adjustment_04
Adjusting point
B
Rack position
R1(11)
Pump speed
r/min
1450
1450
1450
Average injection quantity
mm3/st.
77.5
75.5
79.5
Fixing the lever
*
Injection quantity adjustment_05
Adjusting point
C
Rack position
R1(11)
Pump speed
r/min
600
600
600
Average injection quantity
mm3/st.
51.5
49.5
53.5
Fixing the lever
*
Injection quantity adjustment_06
Adjusting point
I
Rack position
14.1+-0.
5
Pump speed
r/min
100
100
100
Average injection quantity
mm3/st.
90
70
110
Fixing the lever
*
Rack limit
*
Timer adjustment
Pump speed
r/min
1250--
Advance angle
deg.
0
0
0
Remarks
Start
Start
Timer adjustment_02
Pump speed
r/min
1200
Advance angle
deg.
0.5
Timer adjustment_03
Pump speed
r/min
1350
Advance angle
deg.
2.4
1.9
2.9
Timer adjustment_04
Pump speed
r/min
1500
Advance angle
deg.
5
4.5
5.5
Remarks
Finish
Finish
Test data Ex:
Governor adjustment
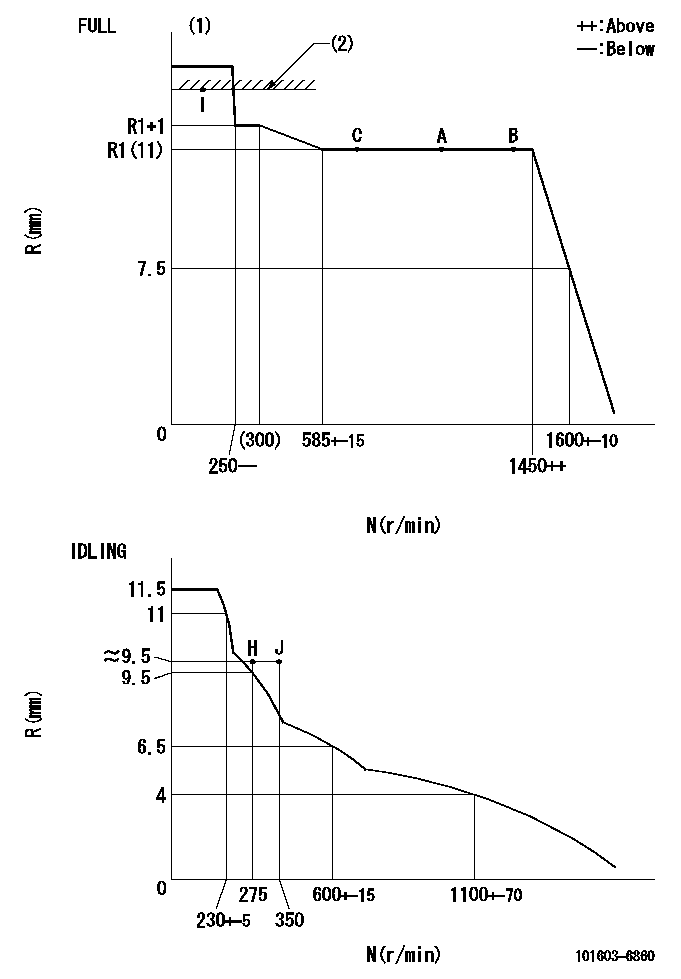
N:Pump speed
R:Rack position (mm)
(1)Torque cam stamping: T1
(2)RACK LIMIT
----------
T1=A10
----------
----------
T1=A10
----------
Speed control lever angle
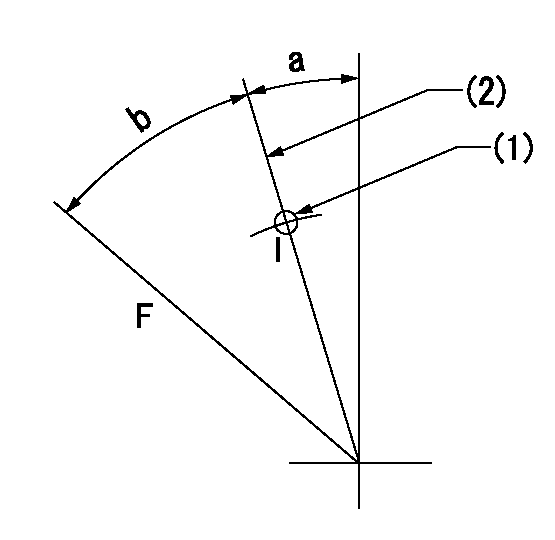
F:Full speed
I:Idle
(1)Use the hole at R = aa
(2)Stopper bolt set position 'H'
----------
aa=40mm
----------
a=18.5deg+-5deg b=40.5deg+-3deg
----------
aa=40mm
----------
a=18.5deg+-5deg b=40.5deg+-3deg
Stop lever angle
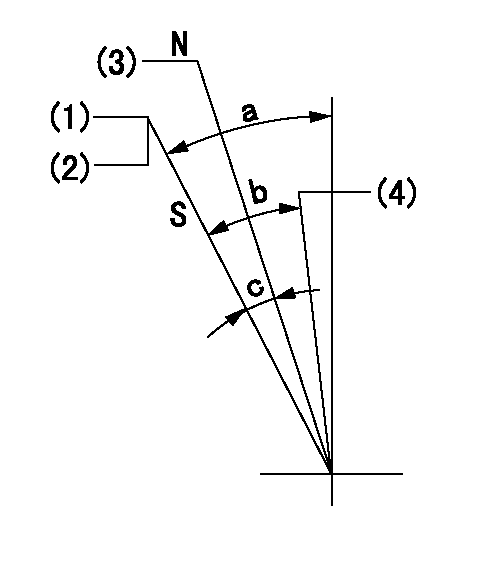
N:Engine manufacturer's normal use
S:Stop the pump.
(1)Set the stopper bolt at speed = rated point and rack position = aa (non-injection rack position). Confirm non-injection.
(2)After setting the stopper bolt , confirm non-injection at pump speed bb. Rack position = cc (non-injection rack position).
(3)Rack position = approximately dd
(4)Free (at shipping)
----------
aa=5.4mm bb=275r/min cc=7.4mm dd=15mm
----------
a=41deg+-5deg b=(29.5deg) c=15.5deg+-3deg
----------
aa=5.4mm bb=275r/min cc=7.4mm dd=15mm
----------
a=41deg+-5deg b=(29.5deg) c=15.5deg+-3deg
0000001501 MICRO SWITCH
Adjustment of the micro-switch
Adjust the bolt to obtain the following lever position when the micro-switch is ON.
(1)Speed N1
(2)Rack position Ra
----------
N1=400+-5r/min Ra=9.2mm
----------
----------
N1=400+-5r/min Ra=9.2mm
----------
Timing setting

(1)Pump vertical direction
(2)Position of timer's tooth at No 1 cylinder's beginning of injection
(3)B.T.D.C.: aa
(4)-
----------
aa=13deg
----------
a=(0deg)
----------
aa=13deg
----------
a=(0deg)
Information:
No. 2D diesel fuel is recommended for use in the 1100 Series Caterpillar Diesel Truck Engines, although No. 1D may be used if desired.In selecting a fuel, note that distillate fuels are especially desirable because the fuel is heated to a vaporous state and condensed, thus eliminating all sediment and residue.There is considerable variation in the composition of fuels distributed under the No. 2D grade classifications. For desirable engine service it is most important to give special attention to cetane no., water and sediment, pour point, cloud point and sulphur content. USE FUELS WHICH MEET THE FOLLOWING REQUIREMENTS:Cetane No. ... 40 minimumWater and Sediment ... 0.1% maximumPour Point ... 10F° (-12C°) below ambient temperatureCloud Point ... No higher than ambient temperatureSulphur Content ... Above 0.4% adjust oil change periodGravity ... 32-40 A.P.I. at 60°F (16°C) Cetane No.: This is an indication of a fuel's ignition quality and should not be less than 40 for this engine. For high altitude operation or cold weather starting, a higher cetane number is required. Water and Sediment: A good clean fuel will contain no more than .1% sediment and water. Dirty fuels lead to early filter plugging and in addition can result in the formation or gums and resins reducing filter and engine life. Pour Point: The pour point of the fuel has no effect on engine performance, as long as the fuel is fluid enough to flow from the fuel tank to the engine. The pour point of the fuel should be at least 10F° (-12°C) below the lowest atmospheric temperature at which the engine must start and operate. In extremely cold temperatures it may be necessary to use No. 1D diesel fuel. Cloud Point: Cloud point is the temperature at which wax crystals become visible and is generally above the pour point of the fuel. The cloud point should be no higher than the lowest atmospheric temperature at which the engine must start to keep the fuel filter elements from plugging with wax crystals. Sulphur Content: As sulphur content increases, the crankcase oil change periods should be reduced. Fuel containing 0.4% or less sulphur content, use normal oil change periods. If the fuel contains 0.4% to 1.0% sulphur, oil change periods should be reduced to one-half normal interval. If the fuel contains more than 1.0% sulphur, oil change periods should be reduced to one-fourth normal interval. Gravity: Gravity is the measurement of heat units in a certain amount of fuel. The heavier the fuel (the lower the number) the more heat units per volume. If a fuel with a higher A.P.I. gravity is used the power produced will be lower. Select fuels with the lower A.P.I. gravity reading.Authorized dealers are familiar with fuels that have given good results in Caterpillar Diesel Engines and should be consulted regarding the fuel to use.