Information injection-pump assembly
ZEXEL
101603-6840
1016036840
MITSUBISHI
ME035344
me035344
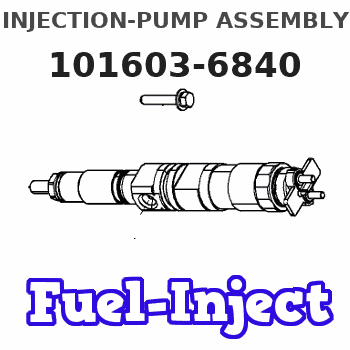
Rating:
Service parts 101603-6840 INJECTION-PUMP ASSEMBLY:
1.
_
6.
COUPLING PLATE
7.
COUPLING PLATE
8.
_
9.
_
11.
Nozzle and Holder
ME035655
12.
Open Pre:MPa(Kqf/cm2)
21.6{220}
15.
NOZZLE SET
Include in #1:
101603-6840
as INJECTION-PUMP ASSEMBLY
Include in #2:
104741-1743
as _
Cross reference number
ZEXEL
101603-6840
1016036840
MITSUBISHI
ME035344
me035344
Zexel num
Bosch num
Firm num
Name
Calibration Data:
Adjustment conditions
Test oil
1404 Test oil ISO4113 or {SAEJ967d}
1404 Test oil ISO4113 or {SAEJ967d}
Test oil temperature
degC
40
40
45
Nozzle and nozzle holder
105780-8140
Bosch type code
EF8511/9A
Nozzle
105780-0000
Bosch type code
DN12SD12T
Nozzle holder
105780-2080
Bosch type code
EF8511/9
Opening pressure
MPa
17.2
Opening pressure
kgf/cm2
175
Injection pipe
Outer diameter - inner diameter - length (mm) mm 6-2-600
Outer diameter - inner diameter - length (mm) mm 6-2-600
Overflow valve
131424-5520
Overflow valve opening pressure
kPa
255
221
289
Overflow valve opening pressure
kgf/cm2
2.6
2.25
2.95
Tester oil delivery pressure
kPa
157
157
157
Tester oil delivery pressure
kgf/cm2
1.6
1.6
1.6
Direction of rotation (viewed from drive side)
Left L
Left L
Injection timing adjustment
Direction of rotation (viewed from drive side)
Left L
Left L
Injection order
1-5-3-6-
2-4
Pre-stroke
mm
3.3
3.25
3.35
Beginning of injection position
Governor side NO.1
Governor side NO.1
Difference between angles 1
Cal 1-5 deg. 60 59.5 60.5
Cal 1-5 deg. 60 59.5 60.5
Difference between angles 2
Cal 1-3 deg. 120 119.5 120.5
Cal 1-3 deg. 120 119.5 120.5
Difference between angles 3
Cal 1-6 deg. 180 179.5 180.5
Cal 1-6 deg. 180 179.5 180.5
Difference between angles 4
Cyl.1-2 deg. 240 239.5 240.5
Cyl.1-2 deg. 240 239.5 240.5
Difference between angles 5
Cal 1-4 deg. 300 299.5 300.5
Cal 1-4 deg. 300 299.5 300.5
Injection quantity adjustment
Adjusting point
-
Rack position
11
Pump speed
r/min
850
850
850
Each cylinder's injection qty
mm3/st.
65
63
67
Basic
*
Fixing the rack
*
Standard for adjustment of the maximum variation between cylinders
*
Injection quantity adjustment_02
Adjusting point
H
Rack position
9.5+-0.5
Pump speed
r/min
275
275
275
Each cylinder's injection qty
mm3/st.
10.5
9
12
Fixing the rack
*
Standard for adjustment of the maximum variation between cylinders
*
Injection quantity adjustment_03
Adjusting point
A
Rack position
R1(11)
Pump speed
r/min
850
850
850
Average injection quantity
mm3/st.
65
64
66
Basic
*
Fixing the lever
*
Injection quantity adjustment_04
Adjusting point
B
Rack position
R1(11)
Pump speed
r/min
1450
1450
1450
Average injection quantity
mm3/st.
77.5
75.5
79.5
Fixing the lever
*
Injection quantity adjustment_05
Adjusting point
C
Rack position
R1(11)
Pump speed
r/min
600
600
600
Average injection quantity
mm3/st.
51.5
49.5
53.5
Fixing the lever
*
Injection quantity adjustment_06
Adjusting point
I
Rack position
14.1+-0.
5
Pump speed
r/min
100
100
100
Average injection quantity
mm3/st.
90
70
110
Fixing the lever
*
Rack limit
*
Timer adjustment
Pump speed
r/min
1250--
Advance angle
deg.
0
0
0
Remarks
Start
Start
Timer adjustment_02
Pump speed
r/min
1200
Advance angle
deg.
0.5
Timer adjustment_03
Pump speed
r/min
1350
Advance angle
deg.
2.4
1.9
2.9
Timer adjustment_04
Pump speed
r/min
1500
Advance angle
deg.
5
4.5
5.5
Remarks
Finish
Finish
Test data Ex:
Governor adjustment
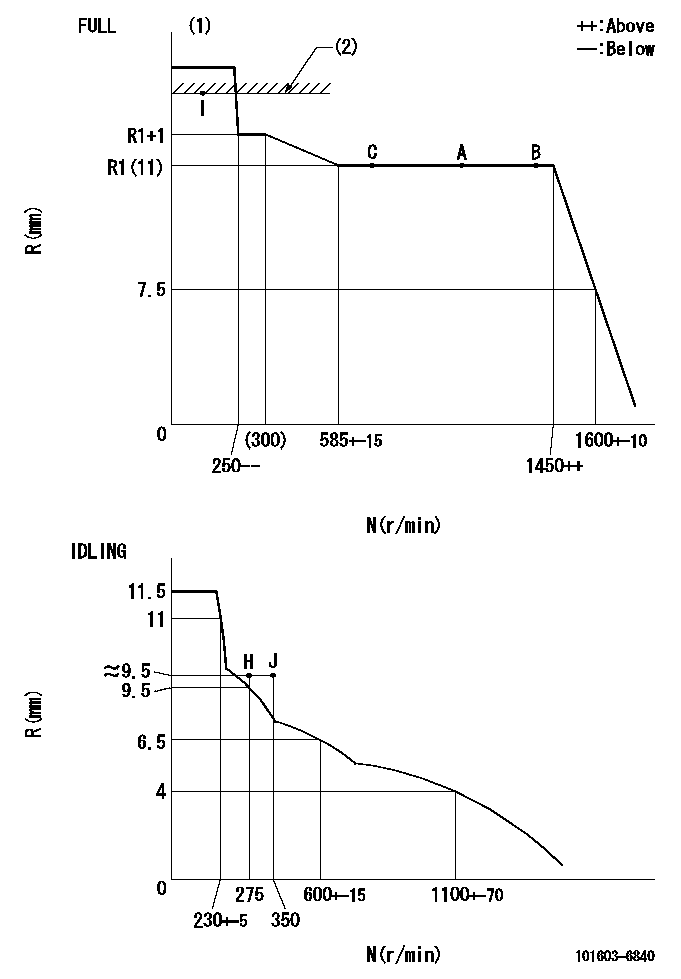
N:Pump speed
R:Rack position (mm)
(1)Torque cam stamping: T1
(2)RACK LIMIT
----------
T1=A10
----------
----------
T1=A10
----------
Speed control lever angle

F:Full speed
I:Idle
(1)Stopper bolt set position 'H'
----------
----------
a=18.5deg+-5deg b=40.5deg+-3deg
----------
----------
a=18.5deg+-5deg b=40.5deg+-3deg
Stop lever angle
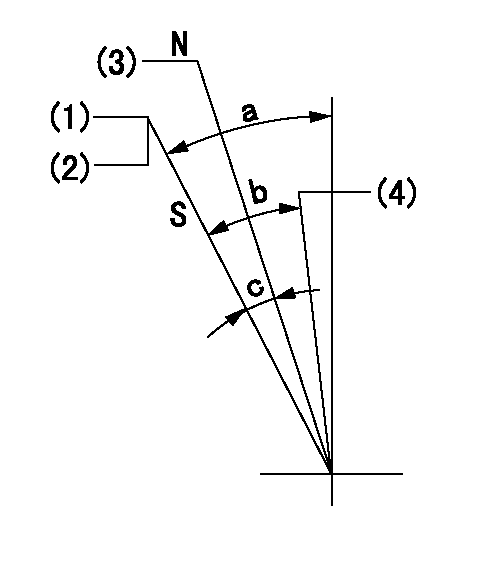
N:Engine manufacturer's normal use
S:Stop the pump.
(1)Set the stopper bolt at speed = rated point and rack position = aa (non-injection rack position). Confirm non-injection.
(2)After setting the stopper bolt , confirm non-injection at pump speed bb. Rack position = cc (non-injection rack position).
(3)Rack position = approximately dd
(4)Free (at shipping)
----------
aa=5.4mm bb=275r/min cc=7.4mm dd=15mm
----------
a=41deg+-5deg b=(29.5deg) c=15.5deg+-3deg
----------
aa=5.4mm bb=275r/min cc=7.4mm dd=15mm
----------
a=41deg+-5deg b=(29.5deg) c=15.5deg+-3deg
0000001501 MICRO SWITCH
Adjustment of the micro-switch
Adjust the bolt to obtain the following lever position when the micro-switch is ON.
(1)Speed N1
(2)Rack position Ra
----------
N1=400+-5r/min Ra=9.2mm
----------
----------
N1=400+-5r/min Ra=9.2mm
----------
Timing setting

(1)Pump vertical direction
(2)Position of timer's tooth at No 1 cylinder's beginning of injection
(3)B.T.D.C.: aa
(4)-
----------
aa=13deg
----------
a=(0deg)
----------
aa=13deg
----------
a=(0deg)
Information:
CHECK CRANKCASE OIL LEVEL before starting and when refueling. The dipstick has 2 marks, and the distance between them represents 3 quarts. Always check oil with engine stopped and truck on level ground. Use oils meeting the following engine service classification:SC and SD (MS - Motor Severe Oils)CB (Supplement 1 Oils)CC (MIL-L-2104B or MIL-L-46152 Specification Oils)CD or MIL-L-2104CChange engine oil and filters as specified in the Lubrication and Maintenance Charts. CHECK ENGINE COOLANT LEVEL (with engine stopped). Always release cooling system pressure before checking. Fill to the proper level with water, free as possible from scale-forming minerals (not softened water), and rust inhibitor, or a solution of water and a permanent type anti-freeze containing rust inhibitor. It is recommended Caterpillar Coolant System Inhibitor be added to the coolant solution if protection is for temperatures above -20°F (-29°C). It is not necessary to add inhibitor to the coolant solution if protection is for temperatures -20°F (-29°C) and below.Models equipped with sight gauge; coolant should be warm (engine stopped) and coolant should be visible in the sight gauge.
Inhibitor contains alkali. Avoid contact with skin and eyes.
CHECK RADIATOR for dirt and foreign material, fan, water pump and accessory drive belts for cracks, breaks and frayed edges. While checking belts, also check for oil, water and fuel leaks and general appearance of engine and engine compartment. CHECK FUEL SUPPLY: Drain a cupful of fuel from the bottom of the tank to remove water or sediment.Fill fuel tanks after completing a run. Partially filled tanks will collect moisture if the truck is parked for any length of time. Use No. 2D diesel fuel in Caterpillar 1100 Series Diesel Truck Engines. Use No. 1-D diesel fuel in cold temperatures when white smoke must be minimized on start up. Keep fuel clean. Refer to Fuel Specifications for detailed information on fuel selection.
Inhibitor contains alkali. Avoid contact with skin and eyes.
CHECK RADIATOR for dirt and foreign material, fan, water pump and accessory drive belts for cracks, breaks and frayed edges. While checking belts, also check for oil, water and fuel leaks and general appearance of engine and engine compartment. CHECK FUEL SUPPLY: Drain a cupful of fuel from the bottom of the tank to remove water or sediment.Fill fuel tanks after completing a run. Partially filled tanks will collect moisture if the truck is parked for any length of time. Use No. 2D diesel fuel in Caterpillar 1100 Series Diesel Truck Engines. Use No. 1-D diesel fuel in cold temperatures when white smoke must be minimized on start up. Keep fuel clean. Refer to Fuel Specifications for detailed information on fuel selection.