Information injection-pump assembly
BOSCH
9 400 615 145
9400615145
ZEXEL
101603-6810
1016036810
MITSUBISHI
ME076006
me076006
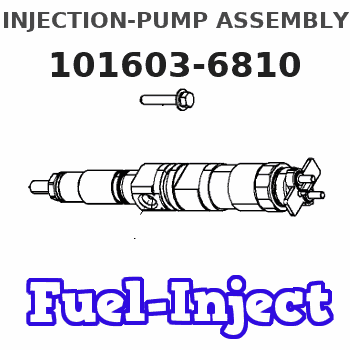
Rating:
Service parts 101603-6810 INJECTION-PUMP ASSEMBLY:
1.
_
6.
COUPLING PLATE
7.
COUPLING PLATE
8.
_
9.
_
11.
Nozzle and Holder
12.
Open Pre:MPa(Kqf/cm2)
21.6(220)
15.
NOZZLE SET
Include in #1:
101603-6810
as INJECTION-PUMP ASSEMBLY
Include in #2:
104740-1630
as _
Cross reference number
BOSCH
9 400 615 145
9400615145
ZEXEL
101603-6810
1016036810
MITSUBISHI
ME076006
me076006
Zexel num
Bosch num
Firm num
Name
9 400 615 145
ME076006 MITSUBISHI
INJECTION-PUMP ASSEMBLY
6D16 * K 14BE INJECTION PUMP ASSY PE6A PE
6D16 * K 14BE INJECTION PUMP ASSY PE6A PE
Calibration Data:
Adjustment conditions
Test oil
1404 Test oil ISO4113 or {SAEJ967d}
1404 Test oil ISO4113 or {SAEJ967d}
Test oil temperature
degC
40
40
45
Nozzle and nozzle holder
105780-8140
Bosch type code
EF8511/9A
Nozzle
105780-0000
Bosch type code
DN12SD12T
Nozzle holder
105780-2080
Bosch type code
EF8511/9
Opening pressure
MPa
17.2
Opening pressure
kgf/cm2
175
Injection pipe
Outer diameter - inner diameter - length (mm) mm 6-2-600
Outer diameter - inner diameter - length (mm) mm 6-2-600
Overflow valve
131424-5520
Overflow valve opening pressure
kPa
255
221
289
Overflow valve opening pressure
kgf/cm2
2.6
2.25
2.95
Tester oil delivery pressure
kPa
157
157
157
Tester oil delivery pressure
kgf/cm2
1.6
1.6
1.6
Direction of rotation (viewed from drive side)
Left L
Left L
Injection timing adjustment
Direction of rotation (viewed from drive side)
Left L
Left L
Injection order
1-5-3-6-
2-4
Pre-stroke
mm
3.3
3.25
3.35
Beginning of injection position
Governor side NO.1
Governor side NO.1
Difference between angles 1
Cal 1-5 deg. 60 59.5 60.5
Cal 1-5 deg. 60 59.5 60.5
Difference between angles 2
Cal 1-3 deg. 120 119.5 120.5
Cal 1-3 deg. 120 119.5 120.5
Difference between angles 3
Cal 1-6 deg. 180 179.5 180.5
Cal 1-6 deg. 180 179.5 180.5
Difference between angles 4
Cyl.1-2 deg. 240 239.5 240.5
Cyl.1-2 deg. 240 239.5 240.5
Difference between angles 5
Cal 1-4 deg. 300 299.5 300.5
Cal 1-4 deg. 300 299.5 300.5
Injection quantity adjustment
Adjusting point
-
Rack position
11.4
Pump speed
r/min
700
700
700
Each cylinder's injection qty
mm3/st.
54.5
52
57
Basic
*
Fixing the rack
*
Standard for adjustment of the maximum variation between cylinders
*
Injection quantity adjustment_02
Adjusting point
D
Rack position
8.7+-0.5
Pump speed
r/min
500
500
500
Each cylinder's injection qty
mm3/st.
7.6
5.9
9.3
Fixing the rack
*
Standard for adjustment of the maximum variation between cylinders
*
Injection quantity adjustment_03
Adjusting point
A
Rack position
R1(11.4)
Pump speed
r/min
700
700
700
Average injection quantity
mm3/st.
54.5
53.5
55.5
Basic
*
Fixing the lever
*
Injection quantity adjustment_04
Adjusting point
B
Rack position
R1+0.4
Pump speed
r/min
1450
1450
1450
Average injection quantity
mm3/st.
79.8
75.8
83.8
Fixing the lever
*
Injection quantity adjustment_05
Adjusting point
C
Rack position
R1(11.4)
Pump speed
r/min
600
600
600
Average injection quantity
mm3/st.
48.5
44.5
52.5
Fixing the lever
*
Injection quantity adjustment_06
Adjusting point
I
Rack position
14.3+-0.
5
Pump speed
r/min
100
100
100
Average injection quantity
mm3/st.
73
63
83
Fixing the lever
*
Rack limit
*
Injection quantity adjustment_07
Adjusting point
H
Rack position
9.5+-0.5
Pump speed
r/min
275
275
275
Each cylinder's injection qty
mm3/st.
8.7
7
10.4
Fixing the rack
*
Remarks
(check)
(check)
Timer adjustment
Pump speed
r/min
900--
Advance angle
deg.
0
0
0
Remarks
Start
Start
Timer adjustment_02
Pump speed
r/min
850
Advance angle
deg.
0.5
Timer adjustment_03
Pump speed
r/min
1200
Advance angle
deg.
2.7
2.2
3.2
Timer adjustment_04
Pump speed
r/min
1500
Advance angle
deg.
5
4.5
5.5
Remarks
Finish
Finish
Test data Ex:
Governor adjustment
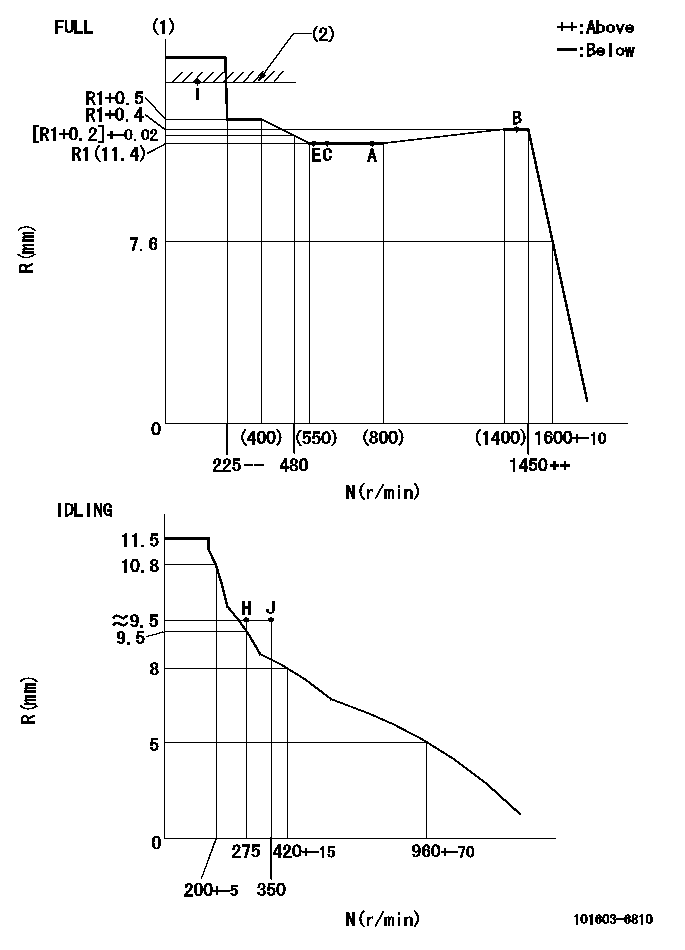
N:Pump speed
R:Rack position (mm)
(1)Torque cam stamping: T1
(2)RACK LIMIT
----------
T1=B07
----------
----------
T1=B07
----------
Speed control lever angle
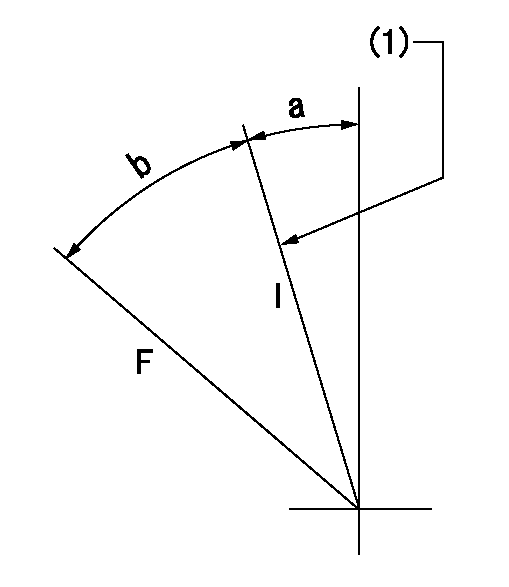
F:Full speed
I:Idle
(1)Stopper bolt set position 'H'
----------
----------
a=18.5deg+-5deg b=41deg+-3deg
----------
----------
a=18.5deg+-5deg b=41deg+-3deg
Stop lever angle
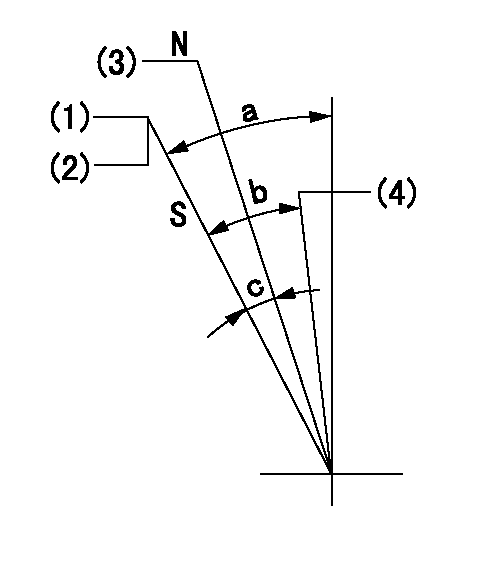
N:Pump normal
S:Stop the pump.
(1)At the rated pump speed and rack position aa, set the stopper bolt. (Confirm that there is no injection.)
(2)After setting the stopper bolt , confirm non-injection at pump speed bb. Rack position = cc (non-injection rack position).
(3)Rack position = approximately dd
(4)Free (at shipping)
----------
aa=6.7mm bb=275r/min cc=(8.3)mm dd=17.4mm
----------
a=38.5deg+-5deg b=(27deg) c=17deg+-5deg
----------
aa=6.7mm bb=275r/min cc=(8.3)mm dd=17.4mm
----------
a=38.5deg+-5deg b=(27deg) c=17deg+-5deg
0000001501 MICRO SWITCH
Adjustment of the micro-switch
Adjust the bolt to obtain the following lever position when the micro-switch is ON.
(1)Speed N1
(2)Rack position Ra
----------
N1=400+-5r/min Ra=9.2mm
----------
----------
N1=400+-5r/min Ra=9.2mm
----------
0000001601 ACS

(A) Housing
(B) Snap ring
(C) adjusting screw
(D) Set screw
(E): Push rod
(F) Spacer
1. Adjustment of the aneroid compensator
(1)Adjust with the (D) set screw so that the clearance between the (A) housing and (B) snap ring is L1.
(2)Select the push rod (E) so that the distance from the end surface of the (F) spacer becomes L2.
(3)Turn adjusting screw (C) to adjust the start of aneroid compensator operation.
2. Adjustment when mounting the governor.
(1)Set the speed of the pump to N1 r/min and fix the control lever at the full set position.
(2)Turn adjusting screw (C) to obtain the performance shown in the graph above.
(3)After final adjustment, confirm that the gap between housing (A) and snapring (B) is L3.
----------
N1=1450r/min L1=1.4~1.7mm L2=0.5+-0.5mm L3=(0.1~0.5)mm
----------
Ra=R1+0.4mm Rb=R1-0.2+-0.2mm Rc=R1-0.8+-0.1mm Pa=94.6+4kPa(710+30mmHg) Pb=79.4kPa(596mmHg) Pc=61.6kPa(462mmHg) Q1=(79.8)+-2cm3/1000st Q2=- Q3=(52)+-2cm3/1000st
----------
N1=1450r/min L1=1.4~1.7mm L2=0.5+-0.5mm L3=(0.1~0.5)mm
----------
Ra=R1+0.4mm Rb=R1-0.2+-0.2mm Rc=R1-0.8+-0.1mm Pa=94.6+4kPa(710+30mmHg) Pb=79.4kPa(596mmHg) Pc=61.6kPa(462mmHg) Q1=(79.8)+-2cm3/1000st Q2=- Q3=(52)+-2cm3/1000st
Timing setting

(1)Pump vertical direction
(2)Position of timer's tooth at No 1 cylinder's beginning of injection
(3)B.T.D.C.: aa
(4)-
----------
aa=16deg
----------
a=(1deg)
----------
aa=16deg
----------
a=(1deg)
Information:
The electrical system is a combination of two separate electric circuits: the charging circuit and starting circuit. Each circuit is dependent on some of the same components. The battery (batteries), disconnect switch, circuit breaker, ammeter, cables and wires from the battery are common in each of the circuits.
The disconnect switch must be ON to allow the electrical system to function. Some charging circuit components will be damaged if the engine is operated with the disconnect switch OFF.
The charging circuit is in operation when the diesel engine is operating. The electricity producing (charging) unit is an alternator. An alternator regulator in the circuit senses the state of charge in the battery and regulates the alternator output to keep the battery fully charged.The starting circuit operates only when the disconnect switch is ON and the start switch is actuated.The direct electric diesel engine starting circuit includes a glow plug for each diesel engine cylinder. Glow plugs are small heating elements in the precombustion chambers which promote fuel ignition when the engine is started in low temperatures.The lighting and charging circuits are both connected on the same side of the ammeter while the starting circuit connects to the other side of the ammeter. This alternator is a three phase self-rectifying charging unit.The alternator has four main components: end frame assembly (brush end), rotor assembly, stator and shell assembly, and end frame assembly (drive end).A separate regulator senses the charge condition of the battery as well as electrical system power demand and controls the alternator output accordingly by limiting the field current.
Never operate the alternator without the battery in the circuit. Making or breaking an alternator connection with a heavy load on the circuit will sometimes result in regulator damage.
The starting motor is a device used to rotate the flywheel of an engine fast enough to start the engine. Alternator Charging Circuit
(Negative Ground System Illustrated)
24 VOLT DIRECT ELECTRIC STARTING MOTORThe starting motor used with direct electric start incorporates a solenoid. The action of the solenoid engages the pinion with the ring gear on the engine flywheel, when the solenoid is energized. The pinion always engages before the electric contacts in the solenoid closes the circuit between the battery and the starting motor. An over-running clutch protects the starting motor from being overspeeded. Releasing the start-switch disengages the pinion from the ring gear on the flywheel.A solenoid is a magnetic switch that utilizes low current to close a high current circuit. The solenoid has an electromagnet with a movable core. There are contacts on the end of the core. The contacts are held open by a spring that pushes the core away from the magnetic center of the coil. Low current will energize the coil and form a magnetic field. The magnetic field draws the core to the center of the coil and the contacts close.
The disconnect switch must be ON to allow the electrical system to function. Some charging circuit components will be damaged if the engine is operated with the disconnect switch OFF.
The charging circuit is in operation when the diesel engine is operating. The electricity producing (charging) unit is an alternator. An alternator regulator in the circuit senses the state of charge in the battery and regulates the alternator output to keep the battery fully charged.The starting circuit operates only when the disconnect switch is ON and the start switch is actuated.The direct electric diesel engine starting circuit includes a glow plug for each diesel engine cylinder. Glow plugs are small heating elements in the precombustion chambers which promote fuel ignition when the engine is started in low temperatures.The lighting and charging circuits are both connected on the same side of the ammeter while the starting circuit connects to the other side of the ammeter. This alternator is a three phase self-rectifying charging unit.The alternator has four main components: end frame assembly (brush end), rotor assembly, stator and shell assembly, and end frame assembly (drive end).A separate regulator senses the charge condition of the battery as well as electrical system power demand and controls the alternator output accordingly by limiting the field current.
Never operate the alternator without the battery in the circuit. Making or breaking an alternator connection with a heavy load on the circuit will sometimes result in regulator damage.
The starting motor is a device used to rotate the flywheel of an engine fast enough to start the engine. Alternator Charging Circuit
(Negative Ground System Illustrated)
24 VOLT DIRECT ELECTRIC STARTING MOTORThe starting motor used with direct electric start incorporates a solenoid. The action of the solenoid engages the pinion with the ring gear on the engine flywheel, when the solenoid is energized. The pinion always engages before the electric contacts in the solenoid closes the circuit between the battery and the starting motor. An over-running clutch protects the starting motor from being overspeeded. Releasing the start-switch disengages the pinion from the ring gear on the flywheel.A solenoid is a magnetic switch that utilizes low current to close a high current circuit. The solenoid has an electromagnet with a movable core. There are contacts on the end of the core. The contacts are held open by a spring that pushes the core away from the magnetic center of the coil. Low current will energize the coil and form a magnetic field. The magnetic field draws the core to the center of the coil and the contacts close.