Information injection-pump assembly
ZEXEL
101603-6800
1016036800
MITSUBISHI
ME035799
me035799
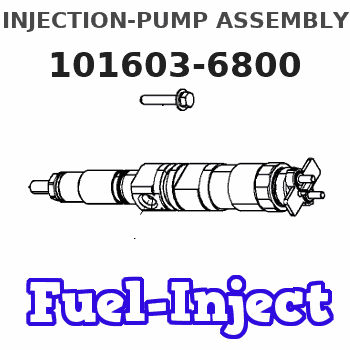
Rating:
Cross reference number
ZEXEL
101603-6800
1016036800
MITSUBISHI
ME035799
me035799
Zexel num
Bosch num
Firm num
Name
101603-6800
ME035799 MITSUBISHI
INJECTION-PUMP ASSEMBLY
6D14T * K
6D14T * K
Calibration Data:
Adjustment conditions
Test oil
1404 Test oil ISO4113 or {SAEJ967d}
1404 Test oil ISO4113 or {SAEJ967d}
Test oil temperature
degC
40
40
45
Nozzle and nozzle holder
105780-8140
Bosch type code
EF8511/9A
Nozzle
105780-0000
Bosch type code
DN12SD12T
Nozzle holder
105780-2080
Bosch type code
EF8511/9
Opening pressure
MPa
17.2
Opening pressure
kgf/cm2
175
Injection pipe
Outer diameter - inner diameter - length (mm) mm 6-2-600
Outer diameter - inner diameter - length (mm) mm 6-2-600
Overflow valve
131424-5520
Overflow valve opening pressure
kPa
255
221
289
Overflow valve opening pressure
kgf/cm2
2.6
2.25
2.95
Tester oil delivery pressure
kPa
157
157
157
Tester oil delivery pressure
kgf/cm2
1.6
1.6
1.6
Direction of rotation (viewed from drive side)
Left L
Left L
Injection timing adjustment
Direction of rotation (viewed from drive side)
Left L
Left L
Injection order
1-5-3-6-
2-4
Pre-stroke
mm
3
2.95
3.05
Beginning of injection position
Governor side NO.1
Governor side NO.1
Difference between angles 1
Cal 1-5 deg. 60 59.5 60.5
Cal 1-5 deg. 60 59.5 60.5
Difference between angles 2
Cal 1-3 deg. 120 119.5 120.5
Cal 1-3 deg. 120 119.5 120.5
Difference between angles 3
Cal 1-6 deg. 180 179.5 180.5
Cal 1-6 deg. 180 179.5 180.5
Difference between angles 4
Cyl.1-2 deg. 240 239.5 240.5
Cyl.1-2 deg. 240 239.5 240.5
Difference between angles 5
Cal 1-4 deg. 300 299.5 300.5
Cal 1-4 deg. 300 299.5 300.5
Injection quantity adjustment
Adjusting point
-
Rack position
12.1
Pump speed
r/min
800
800
800
Each cylinder's injection qty
mm3/st.
88
85.4
90.6
Basic
*
Fixing the rack
*
Standard for adjustment of the maximum variation between cylinders
*
Injection quantity adjustment_02
Adjusting point
H
Rack position
9.5+-0.5
Pump speed
r/min
275
275
275
Each cylinder's injection qty
mm3/st.
10.5
9
12
Fixing the rack
*
Standard for adjustment of the maximum variation between cylinders
*
Injection quantity adjustment_03
Adjusting point
A
Rack position
R1(12.1)
Pump speed
r/min
800
800
800
Average injection quantity
mm3/st.
88
87
89
Basic
*
Fixing the lever
*
Boost pressure
kPa
49.3
49.3
Boost pressure
mmHg
370
370
Injection quantity adjustment_04
Adjusting point
C
Rack position
(R1-0.8)
Pump speed
r/min
600
600
600
Average injection quantity
mm3/st.
67
65
69
Fixing the lever
*
Boost pressure
kPa
18.7
18.7
18.7
Boost pressure
mmHg
140
140
140
Injection quantity adjustment_05
Adjusting point
I
Rack position
-
Pump speed
r/min
100
100
100
Average injection quantity
mm3/st.
110
90
130
Fixing the lever
*
Rack limit
*
Boost compensator adjustment
Pump speed
r/min
700
700
700
Rack position
R1-1.1
Boost pressure
kPa
13.3
13.3
13.3
Boost pressure
mmHg
100
100
100
Boost compensator adjustment_02
Pump speed
r/min
700
700
700
Rack position
(R1-0.8)
Boost pressure
kPa
18.7
17.4
20
Boost pressure
mmHg
140
130
150
Boost compensator adjustment_03
Pump speed
r/min
700
700
700
Rack position
R1(12.1)
Boost pressure
kPa
36
29.3
42.7
Boost pressure
mmHg
270
220
320
Test data Ex:
Governor adjustment
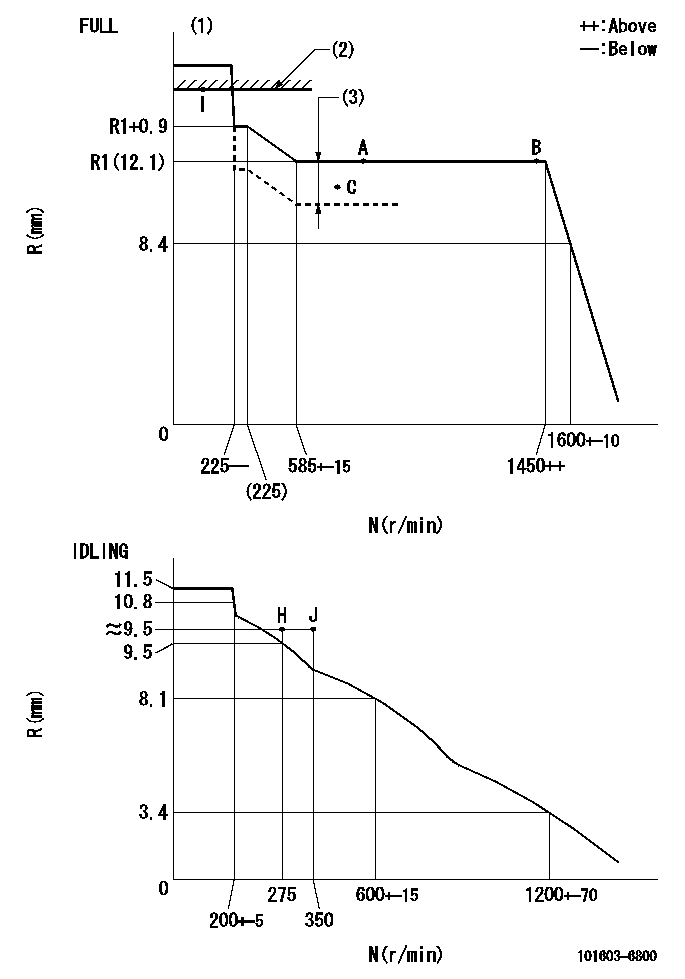
N:Pump speed
R:Rack position (mm)
(1)Torque cam stamping: T1
(2)RACK LIMIT
(3)Boost compensator stroke: BCL
----------
T1=B44 BCL=1.1+-0.1mm
----------
----------
T1=B44 BCL=1.1+-0.1mm
----------
Timer adjustment

(1)Adjusting range
(2)Step response time
(N): Speed of the pump
(L): Load
(theta) Advance angle
(Srd1) Step response time 1
(Srd2) Step response time 2
1. Adjusting conditions for the variable timer
(1)Adjust the clearance between the pickup and the protrusion to L.
----------
L=1.5+-0.2mm N2=800r/min C3=(8)deg t1=2--sec. t2=2--sec.
----------
N1=1400r/min P1=0kPa(0kgf/cm2) P2=392kPa(4kgf/cm2) C1=0.5--deg C2=8+-0.3deg R01=0/4load R02=4/4load
----------
L=1.5+-0.2mm N2=800r/min C3=(8)deg t1=2--sec. t2=2--sec.
----------
N1=1400r/min P1=0kPa(0kgf/cm2) P2=392kPa(4kgf/cm2) C1=0.5--deg C2=8+-0.3deg R01=0/4load R02=4/4load
Speed control lever angle
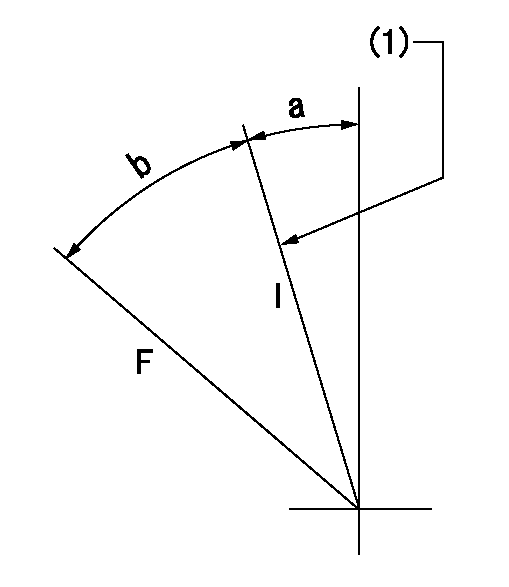
F:Full speed
I:Idle
(1)Stopper bolt set position 'H'
----------
----------
a=18.5deg+-5deg b=(41deg)+-3deg
----------
----------
a=18.5deg+-5deg b=(41deg)+-3deg
Stop lever angle
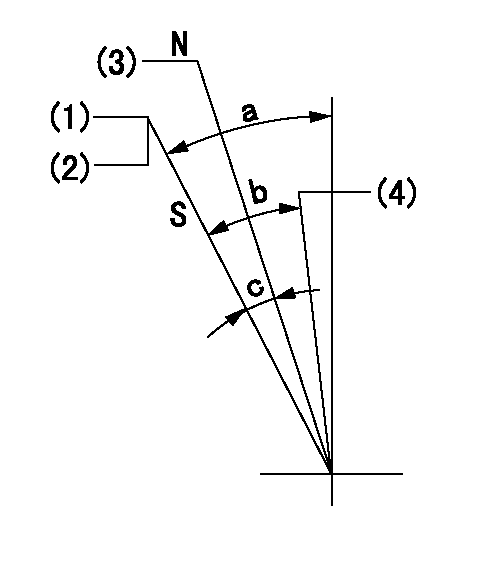
N:Engine manufacturer's normal use
S:Stop the pump.
(1)Set the stopper bolt at speed = rated point and rack position = bb. Confirm non-injection.
(2)After setting the stopper bolt, confirm non-injection at speed = cc.
(3)Rack position = approximately aa.
(4)Free (at shipping)
----------
aa=17.4mm bb=(7.5)mm cc=275r/min
----------
a=38.5deg+-5deg b=(27deg) c=17deg+-5deg
----------
aa=17.4mm bb=(7.5)mm cc=275r/min
----------
a=38.5deg+-5deg b=(27deg) c=17deg+-5deg
0000001501 MICRO SWITCH
Adjustment of the micro-switch
Adjust the bolt to obtain the following lever position when the micro-switch is ON.
(1)Speed N1
(2)Rack position Ra
----------
N1=400+-5r/min Ra=9.2mm
----------
----------
N1=400+-5r/min Ra=9.2mm
----------
0000001601 RACK SENSOR

R:Rack position (mm)
V:Voltage (V)
After installing the rack sensor, confirm the output value (VR).
----------
N1=800r/min Ra=R1(12.1)mm VR=1.99+-0.01V
----------
----------
N1=800r/min Ra=R1(12.1)mm VR=1.99+-0.01V
----------
Timing setting

(1)Pump vertical direction
(2)Position of timer's tooth at No 1 cylinder's beginning of injection
(3)B.T.D.C.: aa
(4)-
----------
aa=14deg
----------
a=(0deg)
----------
aa=14deg
----------
a=(0deg)
Information:
This engine has an exhaust driven turbocharger to provide compacted air to the cylinders.The exhaust gases enter the turbine housing and are directed through the blades of a turbine wheel, causing the turbine wheel and a compressor wheel to rotate.Filtered inlet air from the air cleaner is drawn through the air inlet of the compressor housing by the rotating compressor wheel. The air is forced through the aftercooler to the inlet manifold of the engine and is compressed by action of the compressor impeller.When the intake air passes through and is compressed by the turbocharger, it becomes heated and becomes less dense. By directing air through the aftercooler located between the turbocharger and the inlet manifold, some of that heat is removed from the air. The aftercooler is a simple device resembling a small radiator core. Coolant from the engine passes through the core tubes and the compressed air is directed around the tubes. Since the temperature of the coolant is lower than the air, the air is cooled as it leaves the aftercooler. This means more air (oxygen) is available for combustion, resulting in more fuel being burned and more power produced.When engine load increases, more fuel is injected into the engine cylinders. The increased volume of exhaust gas causes the turbocharger turbine wheel and compressor impeller to rotate faster. The higher RPM of the impeller increases the quantity of inlet air. As the turbocharger provides additional inlet air, more fuel can be burned; hence more horsepower derived from the engine.The turbocharger is mounted to the engine exhaust manifold. All the exhaust gases from the diesel engine pass through the turbocharger.The turbocharger bearings are pressure-lubricated by engine oil. The oil enters the top of the center section and is directed through passages to lubricate the thrust bearing, sleeves and the journal bearings of the turbocharger. Oil leaves the turbocharger through a port in the bottom of the center section and is returned to the engine sump.
CROSS SECTION OF THE TURBOCHARGERMaximum turbocharger speed is determined by the rack setting, the high idle speed setting and the altitude at which the engine is operated. The high idle speed and the rack setting are not the same for all altitudes.
If the high idle speed or the rack setting is greater than specified for the altitude at which the engine is operated, damage to engine or turbocharger parts can result.
The fuel pump rack has been set by qualified personnel for a particular engine application. The governor housing and turbocharger are sealed to prevent unqualified personnel from tampering with the adjustments.The engine can be operated at a lower altitude than specified without danger of engine damage. In this situation the engine will perform at slightly less than maximum efficiency. When operated at a higher altitude, the rack setting and high idle speed setting must be changed.The principal cause of fouled valves, damaged bearings, worn piston rings and cylinder liners is the entrance of airborne foreign matter into the engine cylinders; therefore,
CROSS SECTION OF THE TURBOCHARGERMaximum turbocharger speed is determined by the rack setting, the high idle speed setting and the altitude at which the engine is operated. The high idle speed and the rack setting are not the same for all altitudes.
If the high idle speed or the rack setting is greater than specified for the altitude at which the engine is operated, damage to engine or turbocharger parts can result.
The fuel pump rack has been set by qualified personnel for a particular engine application. The governor housing and turbocharger are sealed to prevent unqualified personnel from tampering with the adjustments.The engine can be operated at a lower altitude than specified without danger of engine damage. In this situation the engine will perform at slightly less than maximum efficiency. When operated at a higher altitude, the rack setting and high idle speed setting must be changed.The principal cause of fouled valves, damaged bearings, worn piston rings and cylinder liners is the entrance of airborne foreign matter into the engine cylinders; therefore,
Have questions with 101603-6800?
Group cross 101603-6800 ZEXEL
Mitsubishi
101603-6800
ME035799
INJECTION-PUMP ASSEMBLY
6D14T
6D14T