Information injection-pump assembly
BOSCH
9 400 615 143
9400615143
ZEXEL
101603-6740
1016036740
MITSUBISHI
ME056582
me056582
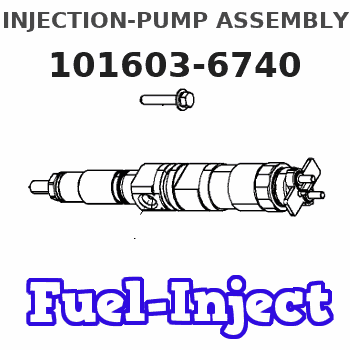
Rating:
Service parts 101603-6740 INJECTION-PUMP ASSEMBLY:
1.
_
7.
COUPLING PLATE
8.
_
9.
_
11.
Nozzle and Holder
12.
Open Pre:MPa(Kqf/cm2)
21.6(220)
15.
NOZZLE SET
Include in #1:
101603-6740
as INJECTION-PUMP ASSEMBLY
Include in #2:
104740-1620
as _
Cross reference number
BOSCH
9 400 615 143
9400615143
ZEXEL
101603-6740
1016036740
MITSUBISHI
ME056582
me056582
Zexel num
Bosch num
Firm num
Name
9 400 615 143
ME056582 MITSUBISHI
INJECTION-PUMP ASSEMBLY
6D22 * K 14BF INJECTION PUMP ASSY PE6AD PE
6D22 * K 14BF INJECTION PUMP ASSY PE6AD PE
Calibration Data:
Adjustment conditions
Test oil
1404 Test oil ISO4113 or {SAEJ967d}
1404 Test oil ISO4113 or {SAEJ967d}
Test oil temperature
degC
40
40
45
Nozzle and nozzle holder
105780-8140
Bosch type code
EF8511/9A
Nozzle
105780-0000
Bosch type code
DN12SD12T
Nozzle holder
105780-2080
Bosch type code
EF8511/9
Opening pressure
MPa
17.2
Opening pressure
kgf/cm2
175
Injection pipe
Outer diameter - inner diameter - length (mm) mm 6-2-600
Outer diameter - inner diameter - length (mm) mm 6-2-600
Overflow valve
131424-5120
Overflow valve opening pressure
kPa
255
221
289
Overflow valve opening pressure
kgf/cm2
2.6
2.25
2.95
Tester oil delivery pressure
kPa
157
157
157
Tester oil delivery pressure
kgf/cm2
1.6
1.6
1.6
Direction of rotation (viewed from drive side)
Right R
Right R
Injection timing adjustment
Direction of rotation (viewed from drive side)
Right R
Right R
Injection order
1-5-3-6-
2-4
Pre-stroke
mm
4.5
4.45
4.55
Beginning of injection position
Governor side NO.1
Governor side NO.1
Difference between angles 1
Cal 1-5 deg. 60 59.5 60.5
Cal 1-5 deg. 60 59.5 60.5
Difference between angles 2
Cal 1-3 deg. 120 119.5 120.5
Cal 1-3 deg. 120 119.5 120.5
Difference between angles 3
Cal 1-6 deg. 180 179.5 180.5
Cal 1-6 deg. 180 179.5 180.5
Difference between angles 4
Cyl.1-2 deg. 240 239.5 240.5
Cyl.1-2 deg. 240 239.5 240.5
Difference between angles 5
Cal 1-4 deg. 300 299.5 300.5
Cal 1-4 deg. 300 299.5 300.5
Injection quantity adjustment
Adjusting point
-
Rack position
9.6
Pump speed
r/min
700
700
700
Each cylinder's injection qty
mm3/st.
112
108.6
115.4
Basic
*
Fixing the rack
*
Standard for adjustment of the maximum variation between cylinders
*
Injection quantity adjustment_02
Adjusting point
C
Rack position
8+-0.5
Pump speed
r/min
225
225
225
Each cylinder's injection qty
mm3/st.
18.5
15.7
21.3
Fixing the rack
*
Standard for adjustment of the maximum variation between cylinders
*
Injection quantity adjustment_03
Adjusting point
A
Rack position
R1(9.6)
Pump speed
r/min
700
700
700
Average injection quantity
mm3/st.
112
111
113
Basic
*
Fixing the lever
*
Injection quantity adjustment_04
Adjusting point
B
Rack position
R1(9.6)
Pump speed
r/min
1100
1100
1100
Average injection quantity
mm3/st.
113.5
111
116
Difference in delivery
mm3/st.
9
9
9
Fixing the lever
*
Injection quantity adjustment_05
Adjusting point
E
Rack position
-
Pump speed
r/min
100
100
100
Average injection quantity
mm3/st.
140
120
160
Fixing the lever
*
Remarks
After startup boost setting
After startup boost setting
Timer adjustment
Pump speed
r/min
850--
Advance angle
deg.
0
0
0
Remarks
Start
Start
Timer adjustment_02
Pump speed
r/min
800
Advance angle
deg.
0.5
Timer adjustment_03
Pump speed
r/min
1000
Advance angle
deg.
0.9
0.4
1.4
Timer adjustment_04
Pump speed
r/min
1150
Advance angle
deg.
3
2.5
3.5
Timer adjustment_05
Pump speed
r/min
-
Advance angle
deg.
4
3
5
Remarks
Measure the actual speed, stop
Measure the actual speed, stop
Test data Ex:
Governor adjustment
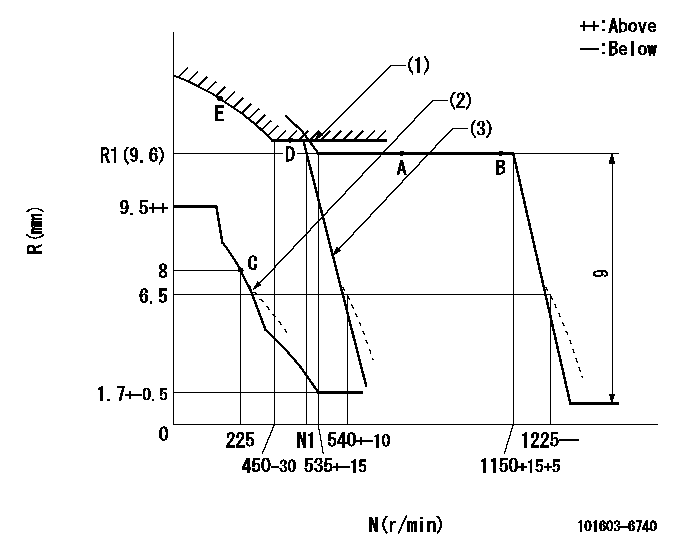
N:Pump speed
R:Rack position (mm)
(1)Excess fuel setting for starting: SXL
(2)Damper spring setting: DL
(3)When air cylinder is operating.
----------
SXL=R1+0.2mm DL=6.8-0.2mm
----------
----------
SXL=R1+0.2mm DL=6.8-0.2mm
----------
Speed control lever angle
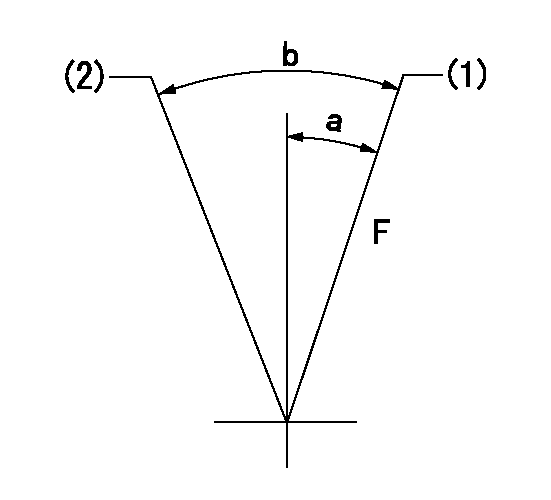
F:Full speed
I:Idle
(1)Set the pump speed at aa
(2)Set the pump speed at bb.
----------
aa=1150r/min bb=N1r/min
----------
a=10deg+-5deg b=(15deg)+-5deg
----------
aa=1150r/min bb=N1r/min
----------
a=10deg+-5deg b=(15deg)+-5deg
0000000901

F:Full load
I:Idle
(1)Stopper bolt setting
----------
----------
a=21.5deg+-5deg b=29deg+-3deg
----------
----------
a=21.5deg+-5deg b=29deg+-3deg
Stop lever angle
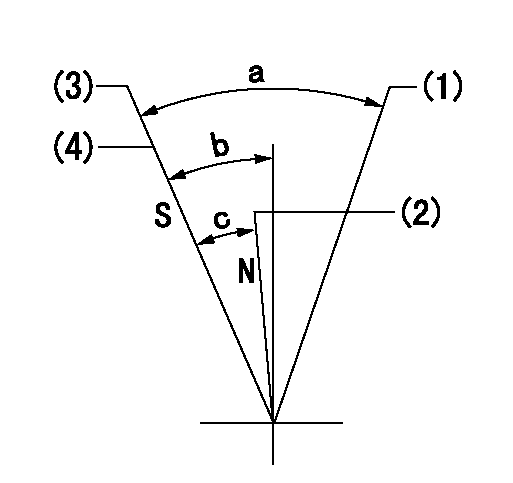
N:Pump normal
S:Stop the pump.
(1)Free (at shipping)
(2)R = bb
(3)R = aa
(4)Stopper bolt setting
----------
aa=6-0.5mm bb=13.5mm
----------
a=(58deg) b=36deg+5deg-7deg c=24deg+-5deg
----------
aa=6-0.5mm bb=13.5mm
----------
a=(58deg) b=36deg+5deg-7deg c=24deg+-5deg
0000001501 2-STAGE CHANGEOVER DEVICE

RFD governor 2 stage changeover mechanism adjustment outline
(A) Bolt
(B) bolt
(c) Nut
(D) Return spring
(E) Bolt
(F) Bolt
(G) Screw
(H) Bolt
(I) Load lever
(J) Speed lever
(K) Air cylinder
(M Air inlet
Figure 1 is only for reference. Lever shape, etc, may vary.
1. Minimum-maximum speed specification adjustment (when running)
(a) Without applying air to the air cylinder, loosen bolts (A) and (B).
(1)High speed return L setting
(a) In the speed range Nf~Nf - 300r/min, adjust using the speed adjusting bolt to determine the temporary beginning of high speed control speed.
(b) Determine the rack position in the vicinity of Rf using the full load lever.
(c) Increase speed and confirm return distance L.
(d) Adjust using the tension lever bolt to obtain L.
(2)Setting full load rack position Rf
(a) Move the load control lever to the full side.
(b) Adjust the full load adjusting bolt so that Rf can be obtained, then fix.
(3)Setting the beginning of high speed operation Nf
(a) Adjust using bolt (E) so that Nf can be obtained, and then fix.
(4)Idle control setting (Re, Ni, Rc)
(a) Set the speed at Ns + 200r/min and move the load control lever to the idle side.
(b) Fix the lever in the position where Re can be obtained.
(c) Next, decrease speed to Ni and screw in the idle spring.
(d) Adjust to obtain rack position Ri.
(e) Increase the speed and after confirming that the rack position is Re at Ns, set the speed at 0.
(f) Confirm protrusion position Rc at idle.
(5)Damper spring adjustment
(a) Increase speed and set the speed at the rack position Rd - 0.1 mm
(b) Set using the damper spring so that the rack position Rd can be obtained.
(c) When Rd is not specified, Rd = Ri - 0.5 mm.
(6)High speed droop confirmation
(a) Return the load control lever to the full load lever position.
(b) Increase the speed and confirm that Rf can be obtained at Nf r/min.
(c) Confirm that speed is Nh at rack position Rh.
2. Variable speed specification adjustment (at operation)
(a) Remove return spring (D).
(b) Apply air pressure of 245~294 kPa {2.5~3 kg/cm2} to the air cylinder.
(c) Perform the following adjustment in this condition.
(1)Setting full load rack position Rf'
(a) Pull the load lever to the idle side.
(b) Obtain rack position Rf' using the nut (C). (Pump speed is Nf'-50 r/min.)
(2)Setting full speed Nf'
(a) Adjust using bolt (B) so that Nf can be obtained, and then fix.
(3)Low speed side setting
(a) At 350r/min, set bolt (F) at beginning of governor operation position, then fix.
3. Bolt (A) adjustment
(1)Install return spring (D) and perform the adjustments below at air pressure 0.
(a) Set at speed Nf using bolt (E).
(b) Screw in bolt (A).
(c) Screw in 1 more turn from the speed lever contact position
(d) Fix bolt (A).
(e) At this time confirm that the air cylinder's shaft moves approximately 1 mm towards the governor.
4. Lever operation confirmation using the air cylinder
(1)Apply 588 kPa {6 kg/cm2} air pressure to the air cylinder.
(2)Confirm that the cylinder piston is moved 50 mm by the spring (D).
----------
----------
----------
----------
0000001601 MICRO SWITCH
Adjustment of the micro-switch
Adjust the bolt to obtain the following lever position when the micro-switch is ON.
(1)Speed N1
(2)Rack position Ra
----------
N1=325+-5r/min Ra=7.3mm
----------
----------
N1=325+-5r/min Ra=7.3mm
----------
Timing setting

(1)Pump vertical direction
(2)Coupling's key groove position at No 1 cylinder's beginning of injection
(3)-
(4)-
----------
----------
a=(7deg)
----------
----------
a=(7deg)
Information:
The fuel system is a pressure type with a separate injection pump and injection valve for each cylinder. Fuel is injected into a precombustion chamber, not directly into the cylinder.A transfer pump supplies fuel filtered through primary (optional) and final filters to a manifold in the injection pump housing.The transfer pump supplies more fuel than is required for injection, so a bypass valve is built into the pressure side of the pump. The valve limits the maximum pressure within the supply system.An air vent valve located on the fuel filter base permits the removal of air in the injection pump supply system after servicing the filter or whenever air is allowed to enter the system. Air is removed by opening the valve and pressurizing the fuel system. The priming pump. The vent valve must be open and the pump operated until a stream of fuel, without air bubbles, flows from the vent line. Fuel Injection Pump Operation
Fuel enters the fuel injection pump housing from the fuel filter through the fuel manifold and enters the fuel injection pump through the inlet port. The injection pump plungers and lifters are lifted by the cam lobes on the fuel system's own camshaft and always make a full stroke. The lifters are held against the cam lobes by springs. Each pump measures the amount of fuel to be injected into its respective cylinder and delivers it to the fuel injection nozzle.The amount of fuel pumped per stroke is varied by turning the plunger in the barrel. The plunger is turned by the governor action through the gear segmented sliding rack which turns the gear segment on the bottom of the pump plunger. The position of the scroll on the plunger determines the amount of fuel injected into the cylinders. Fuel Pump
Figures A, B and C illustrate the functioning of an injection pump as the plunger makes a stroke.In Fig. A the plunger is down and the inlet port is uncovered. Fuel flows into the space above the plunger through the slot and into the recess around the plunger.In Fig. B the plunger has started up and the port is covered. The fuel is trapped and will be forced through a check valve, fuel line, and injection valve.In Fig. C the plunger has risen until the port is uncovered by the recess in the plunger. The fuel can now escape back through the port into the fuel manifold and injection will cease.Note that the recess in the pump plunger forms a helix around the upper end of the plunger. Figures D, E and F illustrate how rotating the pump plunger affects the quantity of fuel injected.In Fig. D the plunger has been rotated into the shut-off position. The slot connecting the top of the plunger with the recess is in line with the port; therefore, no fuel can be trapped and injected.In Fig. E the plunger has been rotated into the idling position. The narrow part of the plunger formed by the helix
Fuel enters the fuel injection pump housing from the fuel filter through the fuel manifold and enters the fuel injection pump through the inlet port. The injection pump plungers and lifters are lifted by the cam lobes on the fuel system's own camshaft and always make a full stroke. The lifters are held against the cam lobes by springs. Each pump measures the amount of fuel to be injected into its respective cylinder and delivers it to the fuel injection nozzle.The amount of fuel pumped per stroke is varied by turning the plunger in the barrel. The plunger is turned by the governor action through the gear segmented sliding rack which turns the gear segment on the bottom of the pump plunger. The position of the scroll on the plunger determines the amount of fuel injected into the cylinders. Fuel Pump
Figures A, B and C illustrate the functioning of an injection pump as the plunger makes a stroke.In Fig. A the plunger is down and the inlet port is uncovered. Fuel flows into the space above the plunger through the slot and into the recess around the plunger.In Fig. B the plunger has started up and the port is covered. The fuel is trapped and will be forced through a check valve, fuel line, and injection valve.In Fig. C the plunger has risen until the port is uncovered by the recess in the plunger. The fuel can now escape back through the port into the fuel manifold and injection will cease.Note that the recess in the pump plunger forms a helix around the upper end of the plunger. Figures D, E and F illustrate how rotating the pump plunger affects the quantity of fuel injected.In Fig. D the plunger has been rotated into the shut-off position. The slot connecting the top of the plunger with the recess is in line with the port; therefore, no fuel can be trapped and injected.In Fig. E the plunger has been rotated into the idling position. The narrow part of the plunger formed by the helix