Information injection-pump assembly
ZEXEL
101603-6521
1016036521
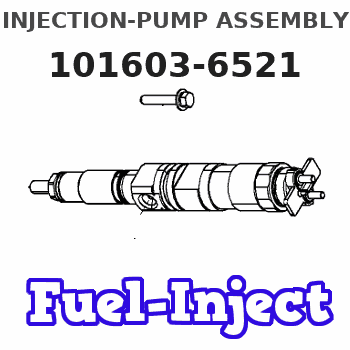
Rating:
Service parts 101603-6521 INJECTION-PUMP ASSEMBLY:
1.
_
6.
COUPLING PLATE
7.
COUPLING PLATE
8.
_
9.
_
11.
Nozzle and Holder
ME035749
12.
Open Pre:MPa(Kqf/cm2)
21.6{220}
15.
NOZZLE SET
Include in #1:
101603-6521
as INJECTION-PUMP ASSEMBLY
Include in #2:
104749-6760
as _
Cross reference number
ZEXEL
101603-6521
1016036521
Zexel num
Bosch num
Firm num
Name
Calibration Data:
Adjustment conditions
Test oil
1404 Test oil ISO4113 or {SAEJ967d}
1404 Test oil ISO4113 or {SAEJ967d}
Test oil temperature
degC
40
40
45
Nozzle and nozzle holder
105780-8140
Bosch type code
EF8511/9A
Nozzle
105780-0000
Bosch type code
DN12SD12T
Nozzle holder
105780-2080
Bosch type code
EF8511/9
Opening pressure
MPa
17.2
Opening pressure
kgf/cm2
175
Injection pipe
Outer diameter - inner diameter - length (mm) mm 6-2-600
Outer diameter - inner diameter - length (mm) mm 6-2-600
Overflow valve
131424-5520
Overflow valve opening pressure
kPa
255
221
289
Overflow valve opening pressure
kgf/cm2
2.6
2.25
2.95
Tester oil delivery pressure
kPa
157
157
157
Tester oil delivery pressure
kgf/cm2
1.6
1.6
1.6
Direction of rotation (viewed from drive side)
Left L
Left L
Injection timing adjustment
Direction of rotation (viewed from drive side)
Left L
Left L
Injection order
1-5-3-6-
2-4
Pre-stroke
mm
3
2.95
3.05
Beginning of injection position
Governor side NO.1
Governor side NO.1
Difference between angles 1
Cal 1-5 deg. 60 59.5 60.5
Cal 1-5 deg. 60 59.5 60.5
Difference between angles 2
Cal 1-3 deg. 120 119.5 120.5
Cal 1-3 deg. 120 119.5 120.5
Difference between angles 3
Cal 1-6 deg. 180 179.5 180.5
Cal 1-6 deg. 180 179.5 180.5
Difference between angles 4
Cyl.1-2 deg. 240 239.5 240.5
Cyl.1-2 deg. 240 239.5 240.5
Difference between angles 5
Cal 1-4 deg. 300 299.5 300.5
Cal 1-4 deg. 300 299.5 300.5
Injection quantity adjustment
Adjusting point
-
Rack position
12.1
Pump speed
r/min
800
800
800
Each cylinder's injection qty
mm3/st.
88
85.4
90.6
Basic
*
Fixing the rack
*
Standard for adjustment of the maximum variation between cylinders
*
Injection quantity adjustment_02
Adjusting point
H
Rack position
9.5+-0.5
Pump speed
r/min
275
275
275
Each cylinder's injection qty
mm3/st.
10.5
9
12
Fixing the rack
*
Standard for adjustment of the maximum variation between cylinders
*
Injection quantity adjustment_03
Adjusting point
A
Rack position
R1(12.1)
Pump speed
r/min
800
800
800
Average injection quantity
mm3/st.
88
87
89
Basic
*
Fixing the lever
*
Boost pressure
kPa
49.3
49.3
Boost pressure
mmHg
370
370
Injection quantity adjustment_04
Adjusting point
C
Rack position
(R1-0.8)
Pump speed
r/min
600
600
600
Average injection quantity
mm3/st.
67
65
69
Fixing the lever
*
Boost pressure
kPa
18.7
18.7
18.7
Boost pressure
mmHg
140
140
140
Injection quantity adjustment_05
Adjusting point
I
Rack position
-
Pump speed
r/min
100
100
100
Average injection quantity
mm3/st.
110
90
130
Fixing the lever
*
Rack limit
*
Boost compensator adjustment
Pump speed
r/min
700
700
700
Rack position
R1-1.1
Boost pressure
kPa
13.3
13.3
13.3
Boost pressure
mmHg
100
100
100
Boost compensator adjustment_02
Pump speed
r/min
700
700
700
Rack position
(R1-0.8)
Boost pressure
kPa
18.7
17.4
20
Boost pressure
mmHg
140
130
150
Boost compensator adjustment_03
Pump speed
r/min
700
700
700
Rack position
R1(12.1)
Boost pressure
kPa
36
29.3
42.7
Boost pressure
mmHg
270
220
320
Timer adjustment
Pump speed
r/min
1250--
Advance angle
deg.
0
0
0
Remarks
Start
Start
Timer adjustment_02
Pump speed
r/min
1200
Advance angle
deg.
0.5
Timer adjustment_03
Pump speed
r/min
1300
Advance angle
deg.
1.6
1.1
2.1
Timer adjustment_04
Pump speed
r/min
1400
Advance angle
deg.
3.5
3
4
Remarks
Finish
Finish
Test data Ex:
Governor adjustment
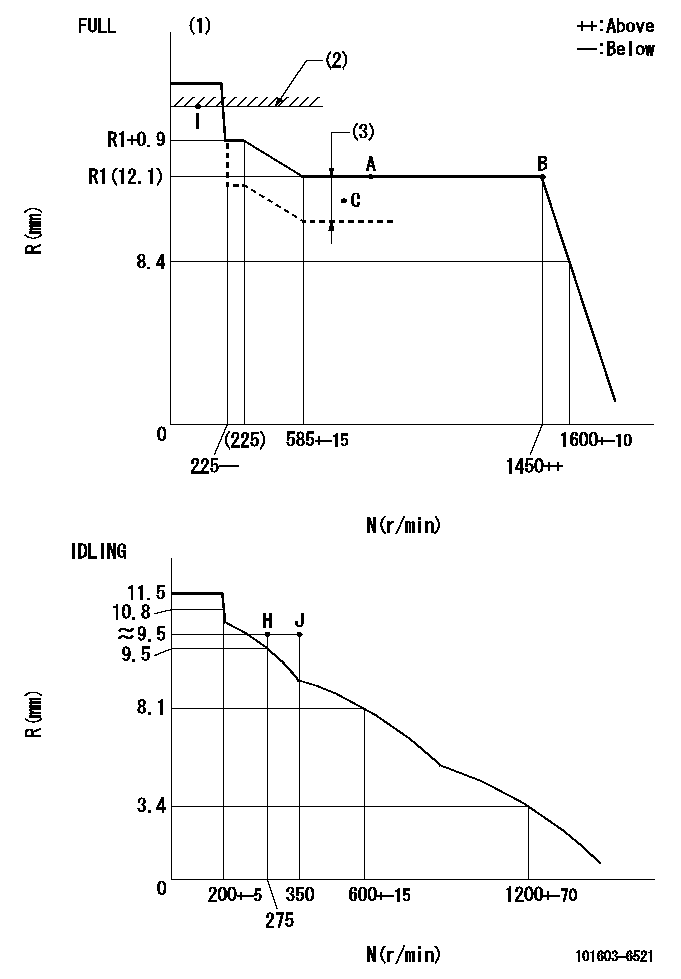
N:Pump speed
R:Rack position (mm)
(1)Torque cam stamping: T1
(2)RACK LIMIT
(3)Boost compensator stroke: BCL
----------
T1=B44 BCL=1.1+-0.1mm
----------
----------
T1=B44 BCL=1.1+-0.1mm
----------
Speed control lever angle
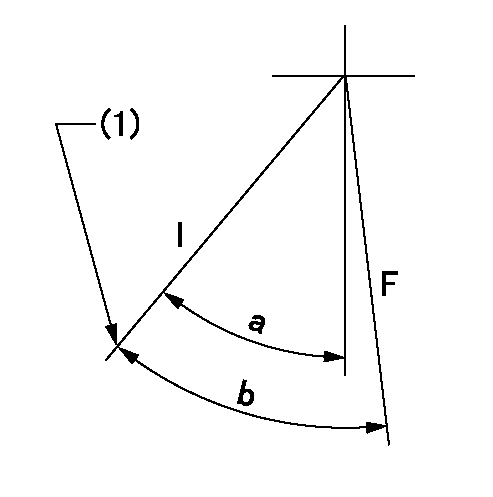
F:Full speed
I:Idle
(1)Stopper bolt set position 'H'
----------
----------
a=33deg+-5deg b=(41deg)+-3deg
----------
----------
a=33deg+-5deg b=(41deg)+-3deg
Stop lever angle
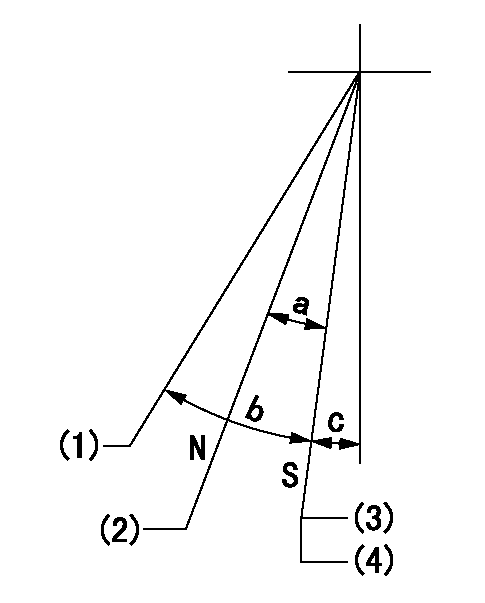
N:Pump normal
S:Stop the pump.
(1)Free (at shipping)
(2)R = corresponding to aa
(3)Set the stopper bolt at speed = rated point and rack position = bb. Confirm non-injection.
(4)After setting the stopper bolt, confirm non-injection at speed = cc and rack position = dd.
----------
aa=17.4mm bb=(7.5)mm cc=275r/min dd=(9)mm
----------
a=17deg+-5deg b=(27deg) c=2deg+-5deg
----------
aa=17.4mm bb=(7.5)mm cc=275r/min dd=(9)mm
----------
a=17deg+-5deg b=(27deg) c=2deg+-5deg
0000001501 MICRO SWITCH
Adjustment of the micro-switch
Adjust the bolt to obtain the following lever position when the micro-switch is ON.
(1)Speed N1
(2)Rack position Ra
----------
N1=400+-5r/min Ra=9.2mm
----------
----------
N1=400+-5r/min Ra=9.2mm
----------
Timing setting

(1)Pump vertical direction
(2)Position of timer's tooth at No 1 cylinder's beginning of injection
(3)B.T.D.C.: aa
(4)-
----------
aa=15deg
----------
a=(0deg)
----------
aa=15deg
----------
a=(0deg)
Information:
Registering a New DEF Injector Injection Timing, Serial Number, and Part Number
Record the DEF injector trim code & part number.
Illustration 10 g06075057
(6) DEF Injector Injection Timing
(7) Part Number
Illustration 11 g06075059
(8) DEF Injector Serial Number
Record the DEF injector Serial Number.
Go to SIS.
Select "View More".
Select "Additional Service Information".
Select "C2.4, C3.3B" and "C3.8 Downloads".
Select ECU Trim Data Registration (Injector, Injection Timing, or DEF Injector).
Illustration 12 g06070579
Input the 6 or 7-digit code engine serial number. Refer to "General Information" to locate the serial number.
Click the button to select the engine.
Enter the new DEF injector part number, Serial number, and injection timing.
Illustration 13 g06075064
Once the new DEF injector Part number, Serial number and Injection timing values have been registered you may follow the DCU flashing procedure to obtain the new DPK flash file found in REHS9223, "Electronic Control Module (ECM) & Dosing Control Unit (DCU Flashing Procedure for the C2.4, C3.3B and C3.8 Engines".Note: Following the above procedure will ensure that any future DCU reflashing will flash the correct DEF injector information.New DEF Injector Install within Electronic Technician (ET)
The Caterpillar Electronic Technician (ET) is used to load injector trim files into the Engine Control Module (ECM).Replacing a DEF Injector
A new DEF Injection Timing Correction must be loaded into the DCU if an injector is replaced through Caterpillar Electronic Technician (ET).Replacing the DCU
Prior to replacing a DCU, It is recommended to download a Product Status Report for documentation of the DEF Injector. After replacing the DCU, ensure the DEF injector trim codes in the new DCU match the saved Product Status Report.
Establish communication between Cat ET and the engine ECM. Refer to Troubleshooting, "Electronic Service Tools", if necessary.
Select the following menu options on Cat ET:
Service
Calibrations
Diesel Exhaust Fluid Controller #1
Injector Code Calibration
Illustration 14 g06070577
Select Injector 1
Illustration 15 g06070578
Enter the new "DEF Injection Timing" Current Value.
Click the "Change" button.Registering (Fuel) Injection Timing Correction
The following steps are to be followed when the fuel injection timing correction procedure has been performed and the engine ecm must be updates with the new value.Note: This procedure is only performed if the crankshaft, gear case, crank gear, or flywheel is replaced. Refer to the following engine specific Special Instructions for determining Injection Timing Correction.C2.4 , M0084937C3.3B , M0084939C3.8 , M0084935
Illustration 16 g06220029
Got to SIS web. Select C2.4, C3.3B, and C3.8 Downloads.
Illustration 17 g06220033
Select ECU and DCU Trim Data Registration.
Illustration 18 g06220036
Engine Serial Number and select search. Engine Serial Number is case-sensitive.
Illustration 19 g06220038
Click the circle (indicated by red arrow) and wait for the screen to change.
Illustration 20 g06220042
Scroll down until Injection Timing Correction is displayed. Enter new value, scroll to the bottom of page, and select Register.
Once the new Injection Timing Correction value has been registered a new DPK file will need to be downloaded and flashed to the Engine ECM. Refer to , REHS9223, "Electronic Control Module (ECM) & Dosing Control Unit (DCU) Flashing Procedure for the C2.4, C3.3B and C3.8 Engines".
Record the DEF injector trim code & part number.
Illustration 10 g06075057
(6) DEF Injector Injection Timing
(7) Part Number
Illustration 11 g06075059
(8) DEF Injector Serial Number
Record the DEF injector Serial Number.
Go to SIS.
Select "View More".
Select "Additional Service Information".
Select "C2.4, C3.3B" and "C3.8 Downloads".
Select ECU Trim Data Registration (Injector, Injection Timing, or DEF Injector).
Illustration 12 g06070579
Input the 6 or 7-digit code engine serial number. Refer to "General Information" to locate the serial number.
Click the button to select the engine.
Enter the new DEF injector part number, Serial number, and injection timing.
Illustration 13 g06075064
Once the new DEF injector Part number, Serial number and Injection timing values have been registered you may follow the DCU flashing procedure to obtain the new DPK flash file found in REHS9223, "Electronic Control Module (ECM) & Dosing Control Unit (DCU Flashing Procedure for the C2.4, C3.3B and C3.8 Engines".Note: Following the above procedure will ensure that any future DCU reflashing will flash the correct DEF injector information.New DEF Injector Install within Electronic Technician (ET)
The Caterpillar Electronic Technician (ET) is used to load injector trim files into the Engine Control Module (ECM).Replacing a DEF Injector
A new DEF Injection Timing Correction must be loaded into the DCU if an injector is replaced through Caterpillar Electronic Technician (ET).Replacing the DCU
Prior to replacing a DCU, It is recommended to download a Product Status Report for documentation of the DEF Injector. After replacing the DCU, ensure the DEF injector trim codes in the new DCU match the saved Product Status Report.
Establish communication between Cat ET and the engine ECM. Refer to Troubleshooting, "Electronic Service Tools", if necessary.
Select the following menu options on Cat ET:
Service
Calibrations
Diesel Exhaust Fluid Controller #1
Injector Code Calibration
Illustration 14 g06070577
Select Injector 1
Illustration 15 g06070578
Enter the new "DEF Injection Timing" Current Value.
Click the "Change" button.Registering (Fuel) Injection Timing Correction
The following steps are to be followed when the fuel injection timing correction procedure has been performed and the engine ecm must be updates with the new value.Note: This procedure is only performed if the crankshaft, gear case, crank gear, or flywheel is replaced. Refer to the following engine specific Special Instructions for determining Injection Timing Correction.C2.4 , M0084937C3.3B , M0084939C3.8 , M0084935
Illustration 16 g06220029
Got to SIS web. Select C2.4, C3.3B, and C3.8 Downloads.
Illustration 17 g06220033
Select ECU and DCU Trim Data Registration.
Illustration 18 g06220036
Engine Serial Number and select search. Engine Serial Number is case-sensitive.
Illustration 19 g06220038
Click the circle (indicated by red arrow) and wait for the screen to change.
Illustration 20 g06220042
Scroll down until Injection Timing Correction is displayed. Enter new value, scroll to the bottom of page, and select Register.
Once the new Injection Timing Correction value has been registered a new DPK file will need to be downloaded and flashed to the Engine ECM. Refer to , REHS9223, "Electronic Control Module (ECM) & Dosing Control Unit (DCU) Flashing Procedure for the C2.4, C3.3B and C3.8 Engines".