Information injection-pump assembly
ZEXEL
101603-6301
1016036301
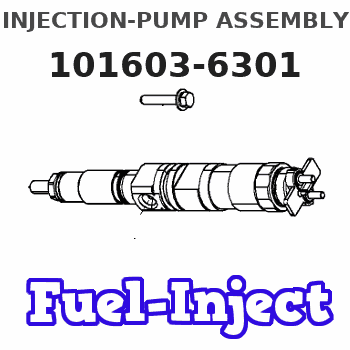
Rating:
Service parts 101603-6301 INJECTION-PUMP ASSEMBLY:
1.
_
6.
COUPLING PLATE
7.
COUPLING PLATE
8.
_
9.
_
11.
Nozzle and Holder
ME035749
12.
Open Pre:MPa(Kqf/cm2)
21.6{220}
15.
NOZZLE SET
Cross reference number
ZEXEL
101603-6301
1016036301
Zexel num
Bosch num
Firm num
Name
Calibration Data:
Adjustment conditions
Test oil
1404 Test oil ISO4113 or {SAEJ967d}
1404 Test oil ISO4113 or {SAEJ967d}
Test oil temperature
degC
40
40
45
Nozzle and nozzle holder
105780-8140
Bosch type code
EF8511/9A
Nozzle
105780-0000
Bosch type code
DN12SD12T
Nozzle holder
105780-2080
Bosch type code
EF8511/9
Opening pressure
MPa
17.2
Opening pressure
kgf/cm2
175
Injection pipe
Outer diameter - inner diameter - length (mm) mm 6-2-600
Outer diameter - inner diameter - length (mm) mm 6-2-600
Overflow valve
131424-5520
Overflow valve opening pressure
kPa
255
221
289
Overflow valve opening pressure
kgf/cm2
2.6
2.25
2.95
Tester oil delivery pressure
kPa
157
157
157
Tester oil delivery pressure
kgf/cm2
1.6
1.6
1.6
Direction of rotation (viewed from drive side)
Left L
Left L
Injection timing adjustment
Direction of rotation (viewed from drive side)
Left L
Left L
Injection order
1-5-3-6-
2-4
Pre-stroke
mm
3
2.95
3.05
Beginning of injection position
Governor side NO.1
Governor side NO.1
Difference between angles 1
Cal 1-5 deg. 60 59.5 60.5
Cal 1-5 deg. 60 59.5 60.5
Difference between angles 2
Cal 1-3 deg. 120 119.5 120.5
Cal 1-3 deg. 120 119.5 120.5
Difference between angles 3
Cal 1-6 deg. 180 179.5 180.5
Cal 1-6 deg. 180 179.5 180.5
Difference between angles 4
Cyl.1-2 deg. 240 239.5 240.5
Cyl.1-2 deg. 240 239.5 240.5
Difference between angles 5
Cal 1-4 deg. 300 299.5 300.5
Cal 1-4 deg. 300 299.5 300.5
Injection quantity adjustment
Adjusting point
-
Rack position
12.1
Pump speed
r/min
800
800
800
Each cylinder's injection qty
mm3/st.
88
85.4
90.6
Basic
*
Fixing the rack
*
Standard for adjustment of the maximum variation between cylinders
*
Injection quantity adjustment_02
Adjusting point
H
Rack position
9.5+-0.5
Pump speed
r/min
275
275
275
Each cylinder's injection qty
mm3/st.
10.5
9
12
Fixing the rack
*
Standard for adjustment of the maximum variation between cylinders
*
Injection quantity adjustment_03
Adjusting point
A
Rack position
R1(12.1)
Pump speed
r/min
800
800
800
Average injection quantity
mm3/st.
88
87
89
Basic
*
Fixing the lever
*
Boost pressure
kPa
49.3
49.3
Boost pressure
mmHg
370
370
Injection quantity adjustment_04
Adjusting point
C
Rack position
(R1-0.8)
Pump speed
r/min
600
600
600
Average injection quantity
mm3/st.
67
65
69
Fixing the lever
*
Boost pressure
kPa
18.7
18.7
18.7
Boost pressure
mmHg
140
140
140
Injection quantity adjustment_05
Adjusting point
I
Rack position
-
Pump speed
r/min
100
100
100
Average injection quantity
mm3/st.
110
90
130
Fixing the lever
*
Rack limit
*
Boost compensator adjustment
Pump speed
r/min
700
700
700
Rack position
R1-1.1
Boost pressure
kPa
13.3
13.3
13.3
Boost pressure
mmHg
100
100
100
Boost compensator adjustment_02
Pump speed
r/min
700
700
700
Rack position
(R1-0.8)
Boost pressure
kPa
18.7
17.4
20
Boost pressure
mmHg
140
130
150
Boost compensator adjustment_03
Pump speed
r/min
700
700
700
Rack position
R1(12.1)
Boost pressure
kPa
36
29.3
42.7
Boost pressure
mmHg
270
220
320
Timer adjustment
Pump speed
r/min
1250--
Advance angle
deg.
0
0
0
Remarks
Start
Start
Timer adjustment_02
Pump speed
r/min
1200
Advance angle
deg.
0.5
Timer adjustment_03
Pump speed
r/min
1300
Advance angle
deg.
1.6
1.1
2.1
Timer adjustment_04
Pump speed
r/min
1400
Advance angle
deg.
3.5
3
4
Remarks
Finish
Finish
Test data Ex:
Governor adjustment
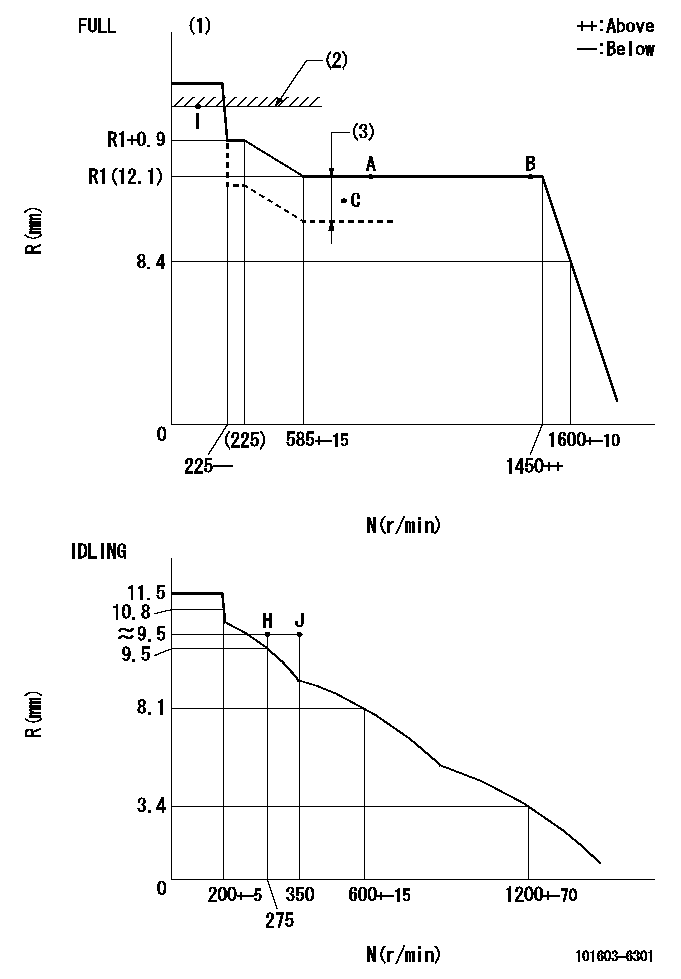
N:Pump speed
R:Rack position (mm)
(1)Torque cam stamping: T1
(2)RACK LIMIT
(3)Boost compensator stroke: BCL
----------
T1=B44 BCL=1.1+-0.1mm
----------
----------
T1=B44 BCL=1.1+-0.1mm
----------
Speed control lever angle
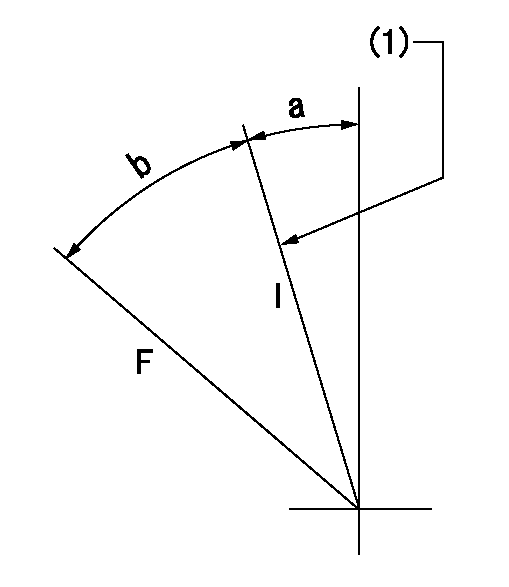
F:Full speed
I:Idle
(1)Stopper bolt set position 'H'
----------
----------
a=18.5deg+-5deg b=(41deg)+-3deg
----------
----------
a=18.5deg+-5deg b=(41deg)+-3deg
Stop lever angle
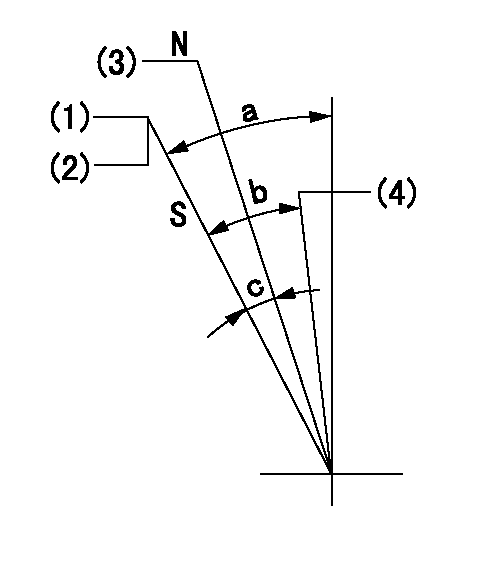
N:Engine manufacturer's normal use
S:Stop the pump.
(1)Set the stopper bolt at speed = rated point and rack position = aa. Confirm non-injection.
(2)After setting the stopper bolt, confirm non-injection at speed = bb. Rack position = cc.
(3)R = corresponding to dd
(4)Free (at shipping)
----------
aa=(7.5)mm bb=275r/min cc=(9)mm dd=17.4mm
----------
a=38.5deg+-5deg b=(27deg) c=17deg+-5deg
----------
aa=(7.5)mm bb=275r/min cc=(9)mm dd=17.4mm
----------
a=38.5deg+-5deg b=(27deg) c=17deg+-5deg
0000001501 MICRO SWITCH
Adjustment of the micro-switch
Adjust the bolt to obtain the following lever position when the micro-switch is ON.
(1)Speed N1
(2)Rack position Ra
----------
N1=400+-5r/min Ra=9.2mm
----------
----------
N1=400+-5r/min Ra=9.2mm
----------
Timing setting

(1)Pump vertical direction
(2)Position of timer's tooth at No 1 cylinder's beginning of injection
(3)B.T.D.C.: aa
(4)-
----------
aa=15deg
----------
a=(0deg)
----------
aa=15deg
----------
a=(0deg)
Information:
Table 4 is an example for using the equation that is in Table 3.
Table 4
Example of the Equation for the Addition of Cat SCA To Water For Maintenance
Total Volume of the Cooling System (V) Multiplication
Factor Amount of Cat SCA that is Required (X)
946 L
(250 US gal) × 0.023 22 L
(6 US gal) Note: Specific engine applications may require maintenance practices to be periodically evaluated to maintain the engine cooling system properly.Cleaning the System of Heavy-Duty Coolant/Antifreeze
Before Cat SCA can be effective, the cooling system must be free from rust, scale, and other deposits. Preventive cleaning helps avoid downtime caused by expensive out-of-service cleaning required for extremelydirty and neglected cooling systems.Cat Cooling System Cleaners
Dissolves or depresses mineral scales, corrosion products, light oil contaminations, and sludges
Cleans the cooling system after used coolant is drained or before the cooling system is filled with new coolant
Cleans the cooling system whenever the coolant is contaminated or whenever the coolant is foaming
The “Standard” version of the Cat Cooling System Cleaners clean the cooling system while still in service.
Reduces downtime and cleaning costs
Helps avoid costly repairs from pitting and other internal problems caused by improper cooling system maintenance
Can be used with glycol-based antifreeze
For the recommended service interval, refer to the Operation and Maintenance Manual, "Maintenance Interval Schedule" for your engine.Cat Standard Cooling System Cleaners are designed to clean the cooling system of harmful scale and corrosion without removing the engine from service. The cleaners, both “Standard” and “Quick Flush” can be used in all Cat engine cooling systems. Consult your Cat dealer for part numbers.Note: These cleaners must not be used in systems that have been neglected or that have heavy scale buildup. These systems require a stronger commercial solvent that is available from local distributors.Prior to performing a cleaning of the cooling system, take a 1-liter (1-quart) sample of coolant from the engine while in operation into a clear container. Take the sample shortly after start-up while the coolant is not yet hot. The coolant should be adequately mixed by the water pump. Allow the sample
Table 4
Example of the Equation for the Addition of Cat SCA To Water For Maintenance
Total Volume of the Cooling System (V) Multiplication
Factor Amount of Cat SCA that is Required (X)
946 L
(250 US gal) × 0.023 22 L
(6 US gal) Note: Specific engine applications may require maintenance practices to be periodically evaluated to maintain the engine cooling system properly.Cleaning the System of Heavy-Duty Coolant/Antifreeze
Before Cat SCA can be effective, the cooling system must be free from rust, scale, and other deposits. Preventive cleaning helps avoid downtime caused by expensive out-of-service cleaning required for extremelydirty and neglected cooling systems.Cat Cooling System Cleaners
Dissolves or depresses mineral scales, corrosion products, light oil contaminations, and sludges
Cleans the cooling system after used coolant is drained or before the cooling system is filled with new coolant
Cleans the cooling system whenever the coolant is contaminated or whenever the coolant is foaming
The “Standard” version of the Cat Cooling System Cleaners clean the cooling system while still in service.
Reduces downtime and cleaning costs
Helps avoid costly repairs from pitting and other internal problems caused by improper cooling system maintenance
Can be used with glycol-based antifreeze
For the recommended service interval, refer to the Operation and Maintenance Manual, "Maintenance Interval Schedule" for your engine.Cat Standard Cooling System Cleaners are designed to clean the cooling system of harmful scale and corrosion without removing the engine from service. The cleaners, both “Standard” and “Quick Flush” can be used in all Cat engine cooling systems. Consult your Cat dealer for part numbers.Note: These cleaners must not be used in systems that have been neglected or that have heavy scale buildup. These systems require a stronger commercial solvent that is available from local distributors.Prior to performing a cleaning of the cooling system, take a 1-liter (1-quart) sample of coolant from the engine while in operation into a clear container. Take the sample shortly after start-up while the coolant is not yet hot. The coolant should be adequately mixed by the water pump. Allow the sample