Information injection-pump assembly
ZEXEL
101603-6280
1016036280
MITSUBISHI
ME056479
me056479
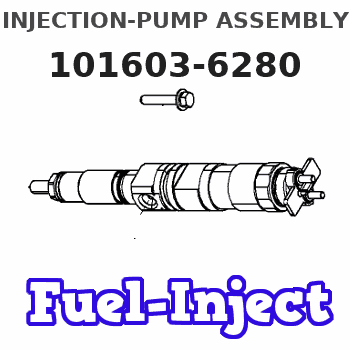
Rating:
Cross reference number
ZEXEL
101603-6280
1016036280
MITSUBISHI
ME056479
me056479
Zexel num
Bosch num
Firm num
Name
Calibration Data:
Adjustment conditions
Test oil
1404 Test oil ISO4113 or {SAEJ967d}
1404 Test oil ISO4113 or {SAEJ967d}
Test oil temperature
degC
40
40
45
Nozzle and nozzle holder
105780-8140
Bosch type code
EF8511/9A
Nozzle
105780-0000
Bosch type code
DN12SD12T
Nozzle holder
105780-2080
Bosch type code
EF8511/9
Opening pressure
MPa
17.2
Opening pressure
kgf/cm2
175
Injection pipe
Outer diameter - inner diameter - length (mm) mm 6-2-600
Outer diameter - inner diameter - length (mm) mm 6-2-600
Overflow valve
131424-5120
Overflow valve opening pressure
kPa
255
221
289
Overflow valve opening pressure
kgf/cm2
2.6
2.25
2.95
Tester oil delivery pressure
kPa
157
157
157
Tester oil delivery pressure
kgf/cm2
1.6
1.6
1.6
Direction of rotation (viewed from drive side)
Right R
Right R
Injection timing adjustment
Direction of rotation (viewed from drive side)
Right R
Right R
Injection order
1-5-3-6-
2-4
Pre-stroke
mm
4.5
4.45
4.55
Beginning of injection position
Governor side NO.1
Governor side NO.1
Difference between angles 1
Cal 1-5 deg. 60 59.5 60.5
Cal 1-5 deg. 60 59.5 60.5
Difference between angles 2
Cal 1-3 deg. 120 119.5 120.5
Cal 1-3 deg. 120 119.5 120.5
Difference between angles 3
Cal 1-6 deg. 180 179.5 180.5
Cal 1-6 deg. 180 179.5 180.5
Difference between angles 4
Cyl.1-2 deg. 240 239.5 240.5
Cyl.1-2 deg. 240 239.5 240.5
Difference between angles 5
Cal 1-4 deg. 300 299.5 300.5
Cal 1-4 deg. 300 299.5 300.5
Injection quantity adjustment
Adjusting point
-
Rack position
9.6
Pump speed
r/min
700
700
700
Each cylinder's injection qty
mm3/st.
112
108.6
115.4
Basic
*
Fixing the rack
*
Standard for adjustment of the maximum variation between cylinders
*
Injection quantity adjustment_02
Adjusting point
C
Rack position
8+-0.5
Pump speed
r/min
225
225
225
Each cylinder's injection qty
mm3/st.
18.5
15.7
21.3
Fixing the rack
*
Standard for adjustment of the maximum variation between cylinders
*
Injection quantity adjustment_03
Adjusting point
A
Rack position
R1(9.6)
Pump speed
r/min
700
700
700
Average injection quantity
mm3/st.
112
111
113
Basic
*
Fixing the lever
*
Injection quantity adjustment_04
Adjusting point
B
Rack position
R1(9.6)
Pump speed
r/min
1100
1100
1100
Average injection quantity
mm3/st.
113.5
111
116
Difference in delivery
mm3/st.
9
9
9
Fixing the lever
*
Injection quantity adjustment_05
Adjusting point
E
Rack position
-
Pump speed
r/min
100
100
100
Average injection quantity
mm3/st.
170
150
190
Fixing the lever
*
Remarks
After startup boost setting
After startup boost setting
Injection quantity adjustment_06
Adjusting point
F
Rack position
R2(9.3)
Pump speed
r/min
700
700
700
Average injection quantity
mm3/st.
104
103
105
Fixing the lever
*
Remarks
Adjust using 2-stage changeover device.
Adjust using 2-stage changeover device.
Timer adjustment
Pump speed
r/min
850--
Advance angle
deg.
0
0
0
Remarks
Start
Start
Timer adjustment_02
Pump speed
r/min
800
Advance angle
deg.
0.5
Timer adjustment_03
Pump speed
r/min
900
Advance angle
deg.
0.9
0.4
1.4
Timer adjustment_04
Pump speed
r/min
1150
Advance angle
deg.
3
2.5
3.5
Timer adjustment_05
Pump speed
r/min
-
Advance angle
deg.
4
3
5
Remarks
Measure the actual speed, stop
Measure the actual speed, stop
Test data Ex:
Governor adjustment
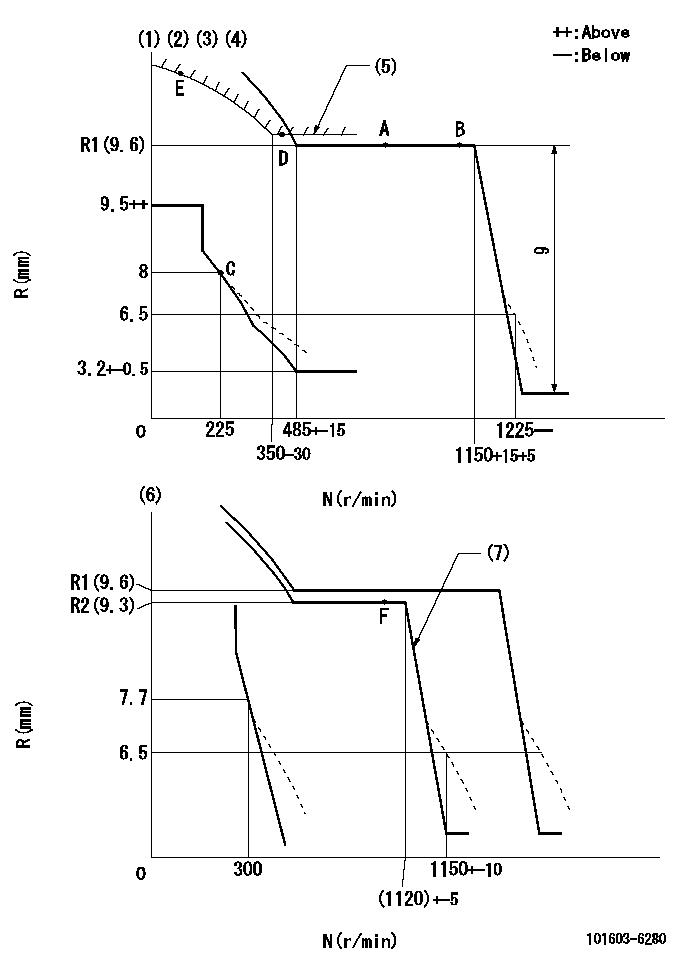
N:Pump speed
R:Rack position (mm)
(1)Adjust with speed control lever at full position (minimum-maximum speed specification)
(2)Lever ratio: RT
(3)Target shim dimension: TH
(4)Damper spring setting: DL
(5)Excess fuel setting for starting: SXL
(6)Adjust with the load control lever in the full position (variable speed specification).
(7)When air cylinder is operating.
----------
RT=1 TH=2mm DL=7.5-0.2mm SXL=11.6+-0.1mm
----------
----------
RT=1 TH=2mm DL=7.5-0.2mm SXL=11.6+-0.1mm
----------
Speed control lever angle
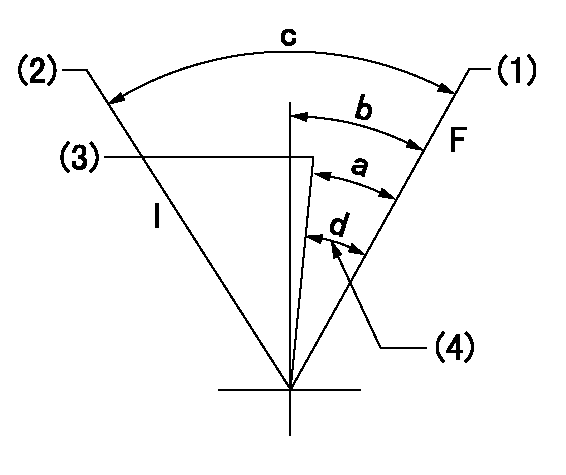
F:Full speed
I:Idle
(1)Pump speed = aa
(2)Pump speed = bb
(3)Pump speed cc
(4)Air cylinder's adjustable range
----------
aa=1150r/min bb=300r/min cc=(1120)r/min
----------
a=2deg+-5deg b=10deg+-5deg c=20deg+-5deg d=2deg
----------
aa=1150r/min bb=300r/min cc=(1120)r/min
----------
a=2deg+-5deg b=10deg+-5deg c=20deg+-5deg d=2deg
0000000901

F:Full load
I:Idle
(1)Stopper bolt setting
----------
----------
a=21deg+-5deg b=23.5deg+-3deg
----------
----------
a=21deg+-5deg b=23.5deg+-3deg
Stop lever angle
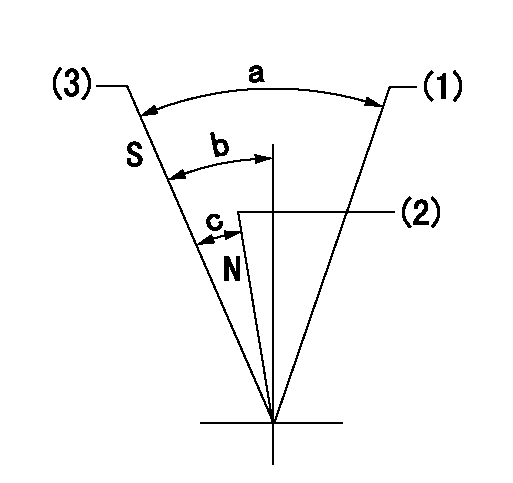
N:Engine manufacturer's normal use
S:Stop the pump.
(1)Free (at shipping)
(2)Rack position = aa
(3)Rack position = bb, set the stopper bolt.
----------
aa=13.5mm bb=6-0.5mm
----------
a=(58deg) b=36deg+5deg-7deg c=24deg+-5deg
----------
aa=13.5mm bb=6-0.5mm
----------
a=(58deg) b=36deg+5deg-7deg c=24deg+-5deg
0000001501 2-STAGE CHANGEOVER DEVICE

RFD governor 2 stage changeover mechanism adjustment outline
(A) Bolt
(B) bolt
(c) Nut
(D) Return spring
(E) Bolt
(F) Bolt
(G) Screw
(H) Bolt
(I) Load lever
(J) Speed lever
(K) Air cylinder
(M Air inlet
Figure 1 is only for reference. Lever shape, etc, may vary.
1. Minimum-maximum speed specification adjustment (when running)
(a) Without applying air to the air cylinder, loosen bolts (A) and (B).
(1)High speed return L setting
(a) In the speed range Nf~Nf - 300r/min, adjust using the speed adjusting bolt to determine the temporary beginning of high speed control speed.
(b) Determine the rack position in the vicinity of Rf using the full load lever.
(c) Increase speed and confirm return distance L.
(d) Adjust using the tension lever bolt to obtain L.
(2)Setting full load rack position Rf
(a) Move the load control lever to the full side.
(b) Adjust the full load adjusting bolt so that Rf can be obtained, then fix.
(3)Setting the beginning of high speed operation Nf
(a) Adjust using bolt (E) so that Nf can be obtained, and then fix.
(4)Idle control setting (Re, Ni, Rc)
(a) Set the speed at Ns + 200r/min and move the load control lever to the idle side.
(b) Fix the lever in the position where Re can be obtained.
(c) Next, decrease speed to Ni and screw in the idle spring.
(d) Adjust to obtain rack position Ri.
(e) Increase the speed and after confirming that the rack position is Re at Ns, set the speed at 0.
(f) Confirm protrusion position Rc at idle.
(5)Damper spring adjustment
(a) Increase speed and set the speed at the rack position Rd - 0.1 mm
(b) Set using the damper spring so that the rack position Rd can be obtained.
(c) When Rd is not specified, Rd = Ri - 0.5 mm.
(6)High speed droop confirmation
(a) Return the load control lever to the full load lever position.
(b) Increase the speed and confirm that Rf can be obtained at Nf r/min.
(c) Confirm that speed is Nh at rack position Rh.
2. Variable speed specification adjustment (at operation)
(a) Remove return spring (D).
(b) Apply air pressure of 245~294 kPa {2.5~3 kg/cm2} to the air cylinder.
(c) Perform the following adjustment in this condition.
(1)Setting full load rack position Rf'
(a) Pull the load lever to the idle side.
(b) Obtain rack position Rf' using the nut (C). (Pump speed is Nf'-50 r/min.)
(2)Setting full speed Nf'
(a) Adjust using bolt (B) so that Nf can be obtained, and then fix.
(3)Low speed side setting
(a) At 350r/min, set bolt (F) at beginning of governor operation position, then fix.
3. Bolt (A) adjustment
(1)Install return spring (D) and perform the adjustments below at air pressure 0.
(a) Set at speed Nf using bolt (E).
(b) Screw in bolt (A).
(c) Screw in 1 more turn from the speed lever contact position
(d) Fix bolt (A).
(e) At this time confirm that the air cylinder's shaft moves approximately 1 mm towards the governor.
4. Lever operation confirmation using the air cylinder
(1)Apply 588 kPa {6 kg/cm2} air pressure to the air cylinder.
(2)Confirm that the cylinder piston is moved 50 mm by the spring (D).
----------
----------
----------
----------
0000001601 MICRO SWITCH
Adjustment of the micro-switch
Adjust the bolt to obtain the following lever position when the micro-switch is ON.
(1)Speed N1
(2)Rack position Ra
----------
N1=325+-5r/min Ra=7.3mm
----------
----------
N1=325+-5r/min Ra=7.3mm
----------
Timing setting

(1)Pump vertical direction
(2)Coupling's key groove position at No 1 cylinder's beginning of injection
(3)-
(4)-
----------
----------
a=(7deg)
----------
----------
a=(7deg)
Information:
Introduction
The problem that is identified now has a known permanent solution. Components to perform repairs are limited at this time. Review the solution below for further details. Problem
Caterpillar is aware of recent failures of the 8N-1721 Connecting Rod and the 8N-1984 Connecting Rod on certain diesel and gas applications of 3300 engines. Primary failure mode is a ventilated cylinder block due to the connecting rod crank end failure. All failures have occurred before 500 hours in service. Root cause has been identified and the team is working to resolve the issue. Solution
A "Quality Hold" is active for all new assemblies that utilize the 8N-1984 Connecting Rod and the 8N-1721 Connecting Rod manufactured between 01April 2011 and 31December 2012. The "Quality Hold" is applicable to all Morton service stock also.Cat ® Reman has identified a list of part numbers for Service kits, Piston Packs, and Rod Assembly boxes that may contain defective factory connecting rod assemblies. Dealers are advised not to use any factory new connecting rod assemblies that are found in the kits or assemblies prior to examination. Refer to Table 1.
Table 1
Service kit, Piston Pack, and Rod Assembly Part Numbers That May Contain the Defective New Connecting Rod Assemblies    
8N-1721     20R-1439     20R-1474    
0R-1696     20R-1428     20R-1660    
0R-1697     0R-9206     20R-1442    
0R-3043     20R-1462     20R-1482    
10R-3637     20R-1455     20R-1483    
10R-9259     20R-1477     20R-1451    
0R-1694     20R-1472     20R-1450    
0R-4284     20R-1448     20R-1445    
0R-1695     20R-1446     20R-1443    
0R-4635     20R-1468     20R-1426    
0R-4488     20R-1466     20R-1423    
0R-4506     20R-1441     0R-2078    
0R-3044     20R-1437     0R-3258    
0R-2080     20R-1435     20R-1665    
0R-3259     20R-1434     20R-1663    
0R-3612     20R-1429     20R-1675    
0R-3610     20R-1424     0R-3661    
10R-6152     0R-2557     0R-1692    
20R-1673     0R-2079     0R-1693    
20R-1664     20R-1341     0R-3660    
0R-4949     0R-2555     0R-3662    
0R-9205     0R-3613     20R-1127    
0R-2556     0R-4956     8N-1984    
0R-3706     0R-2554        
10R-1851     0R-4948    
10R-1636     10R-0889    
10R-1840     0R-3611    
0R-2077     10R-7253    
20R-1454     0R-7444    When an engine failure occurs due to the connecting rod assembly, dealers are asked to contact the Dealer Solution Network (DSN) Tier 2 core engine service engineer at Mossville Engine Center (MEC) to expedite support to the customer.To support field repairs and rebuilds, dealers are advised to inspect the manufacture date on any 3304, G3304, 3306, or G3306 engine with the 8N-1984 Connecting Rod , the 8N-1721 Connecting Rod , the 0R-0914 Connecting Rod , and the 0R-0915 Connecting Rod , used to perform repairs. If the manufacture date is within the suspect date range, do not use the part. Parts stocking service letters will be released soon to address suspect material in dealer inventories. Markings on the Suspect 8N-1984 Connecting Rod and the 8N-1721 Connecting Rod
Illustration 1 g03342875
(1
The problem that is identified now has a known permanent solution. Components to perform repairs are limited at this time. Review the solution below for further details. Problem
Caterpillar is aware of recent failures of the 8N-1721 Connecting Rod and the 8N-1984 Connecting Rod on certain diesel and gas applications of 3300 engines. Primary failure mode is a ventilated cylinder block due to the connecting rod crank end failure. All failures have occurred before 500 hours in service. Root cause has been identified and the team is working to resolve the issue. Solution
A "Quality Hold" is active for all new assemblies that utilize the 8N-1984 Connecting Rod and the 8N-1721 Connecting Rod manufactured between 01April 2011 and 31December 2012. The "Quality Hold" is applicable to all Morton service stock also.Cat ® Reman has identified a list of part numbers for Service kits, Piston Packs, and Rod Assembly boxes that may contain defective factory connecting rod assemblies. Dealers are advised not to use any factory new connecting rod assemblies that are found in the kits or assemblies prior to examination. Refer to Table 1.
Table 1
Service kit, Piston Pack, and Rod Assembly Part Numbers That May Contain the Defective New Connecting Rod Assemblies    
8N-1721     20R-1439     20R-1474    
0R-1696     20R-1428     20R-1660    
0R-1697     0R-9206     20R-1442    
0R-3043     20R-1462     20R-1482    
10R-3637     20R-1455     20R-1483    
10R-9259     20R-1477     20R-1451    
0R-1694     20R-1472     20R-1450    
0R-4284     20R-1448     20R-1445    
0R-1695     20R-1446     20R-1443    
0R-4635     20R-1468     20R-1426    
0R-4488     20R-1466     20R-1423    
0R-4506     20R-1441     0R-2078    
0R-3044     20R-1437     0R-3258    
0R-2080     20R-1435     20R-1665    
0R-3259     20R-1434     20R-1663    
0R-3612     20R-1429     20R-1675    
0R-3610     20R-1424     0R-3661    
10R-6152     0R-2557     0R-1692    
20R-1673     0R-2079     0R-1693    
20R-1664     20R-1341     0R-3660    
0R-4949     0R-2555     0R-3662    
0R-9205     0R-3613     20R-1127    
0R-2556     0R-4956     8N-1984    
0R-3706     0R-2554        
10R-1851     0R-4948    
10R-1636     10R-0889    
10R-1840     0R-3611    
0R-2077     10R-7253    
20R-1454     0R-7444    When an engine failure occurs due to the connecting rod assembly, dealers are asked to contact the Dealer Solution Network (DSN) Tier 2 core engine service engineer at Mossville Engine Center (MEC) to expedite support to the customer.To support field repairs and rebuilds, dealers are advised to inspect the manufacture date on any 3304, G3304, 3306, or G3306 engine with the 8N-1984 Connecting Rod , the 8N-1721 Connecting Rod , the 0R-0914 Connecting Rod , and the 0R-0915 Connecting Rod , used to perform repairs. If the manufacture date is within the suspect date range, do not use the part. Parts stocking service letters will be released soon to address suspect material in dealer inventories. Markings on the Suspect 8N-1984 Connecting Rod and the 8N-1721 Connecting Rod
Illustration 1 g03342875
(1