Information injection-pump assembly
ZEXEL
101603-6141
1016036141

Rating:
Service parts 101603-6141 INJECTION-PUMP ASSEMBLY:
1.
_
6.
COUPLING PLATE
7.
COUPLING PLATE
8.
_
9.
_
11.
Nozzle and Holder
ME035748
12.
Open Pre:MPa(Kqf/cm2)
21.6{220}
15.
NOZZLE SET
Include in #1:
101603-6141
as INJECTION-PUMP ASSEMBLY
Include in #2:
104740-1450
as _
Cross reference number
ZEXEL
101603-6141
1016036141
Zexel num
Bosch num
Firm num
Name
Calibration Data:
Adjustment conditions
Test oil
1404 Test oil ISO4113 or {SAEJ967d}
1404 Test oil ISO4113 or {SAEJ967d}
Test oil temperature
degC
40
40
45
Nozzle and nozzle holder
105780-8140
Bosch type code
EF8511/9A
Nozzle
105780-0000
Bosch type code
DN12SD12T
Nozzle holder
105780-2080
Bosch type code
EF8511/9
Opening pressure
MPa
17.2
Opening pressure
kgf/cm2
175
Injection pipe
Outer diameter - inner diameter - length (mm) mm 6-2-600
Outer diameter - inner diameter - length (mm) mm 6-2-600
Overflow valve
131424-5520
Overflow valve opening pressure
kPa
255
221
289
Overflow valve opening pressure
kgf/cm2
2.6
2.25
2.95
Tester oil delivery pressure
kPa
157
157
157
Tester oil delivery pressure
kgf/cm2
1.6
1.6
1.6
Direction of rotation (viewed from drive side)
Left L
Left L
Injection timing adjustment
Direction of rotation (viewed from drive side)
Left L
Left L
Injection order
1-5-3-6-
2-4
Pre-stroke
mm
3.6
3.55
3.65
Beginning of injection position
Governor side NO.1
Governor side NO.1
Difference between angles 1
Cal 1-5 deg. 60 59.5 60.5
Cal 1-5 deg. 60 59.5 60.5
Difference between angles 2
Cal 1-3 deg. 120 119.5 120.5
Cal 1-3 deg. 120 119.5 120.5
Difference between angles 3
Cal 1-6 deg. 180 179.5 180.5
Cal 1-6 deg. 180 179.5 180.5
Difference between angles 4
Cyl.1-2 deg. 240 239.5 240.5
Cyl.1-2 deg. 240 239.5 240.5
Difference between angles 5
Cal 1-4 deg. 300 299.5 300.5
Cal 1-4 deg. 300 299.5 300.5
Injection quantity adjustment
Adjusting point
-
Rack position
11
Pump speed
r/min
850
850
850
Each cylinder's injection qty
mm3/st.
60
58.1
61.9
Basic
*
Fixing the rack
*
Standard for adjustment of the maximum variation between cylinders
*
Injection quantity adjustment_02
Adjusting point
-
Rack position
10+-0.5
Pump speed
r/min
275
275
275
Each cylinder's injection qty
mm3/st.
10
8.9
11.1
Fixing the rack
*
Standard for adjustment of the maximum variation between cylinders
*
Remarks
Adjust only variation between cylinders; adjust governor according to governor specifications.
Adjust only variation between cylinders; adjust governor according to governor specifications.
Injection quantity adjustment_03
Adjusting point
A
Rack position
R1(11)
Pump speed
r/min
850
850
850
Average injection quantity
mm3/st.
60
59
61
Basic
*
Fixing the lever
*
Injection quantity adjustment_04
Adjusting point
B
Rack position
R1+0.6
Pump speed
r/min
1450
1450
1450
Average injection quantity
mm3/st.
80.5
78.5
82.5
Fixing the lever
*
Injection quantity adjustment_05
Adjusting point
C
Rack position
R1-0.4
Pump speed
r/min
600
600
600
Average injection quantity
mm3/st.
42.5
40.5
44.5
Fixing the lever
*
Injection quantity adjustment_06
Adjusting point
I
Rack position
-
Pump speed
r/min
100
100
100
Average injection quantity
mm3/st.
80
75
85
Fixing the lever
*
Rack limit
*
Timer adjustment
Pump speed
r/min
1250--
Advance angle
deg.
0
0
0
Remarks
Start
Start
Timer adjustment_02
Pump speed
r/min
1200
Advance angle
deg.
0.5
Timer adjustment_03
Pump speed
r/min
1350
Advance angle
deg.
2.4
1.9
2.9
Timer adjustment_04
Pump speed
r/min
1500
Advance angle
deg.
5
4.5
5.5
Remarks
Finish
Finish
Test data Ex:
Governor adjustment
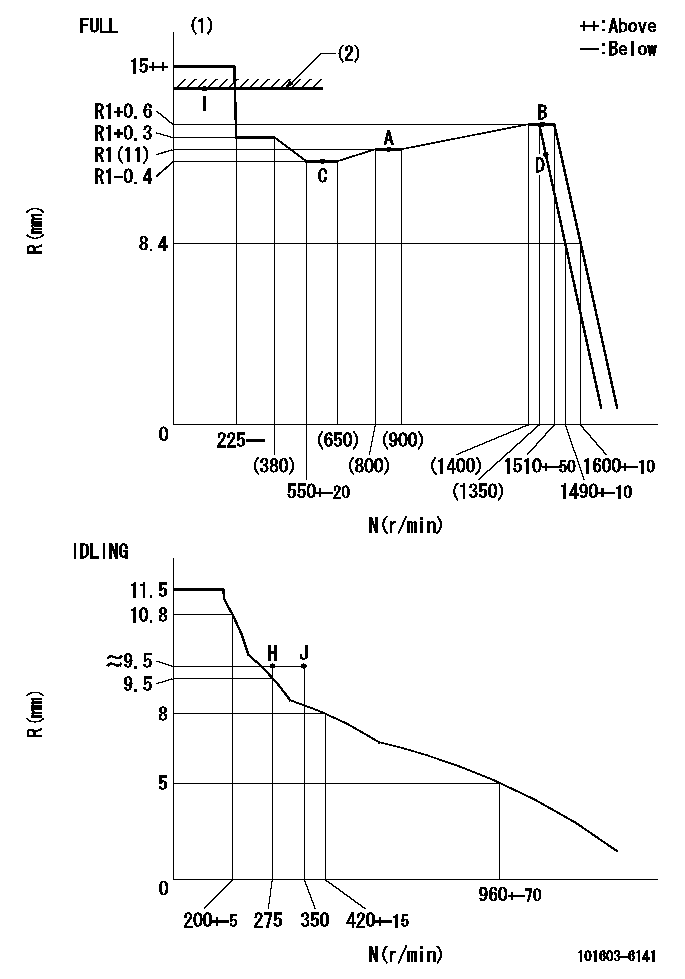
N:Pump speed
R:Rack position (mm)
(1)Torque cam stamping: T1
(2)RACK LIMIT
----------
T1=A63
----------
----------
T1=A63
----------
Speed control lever angle
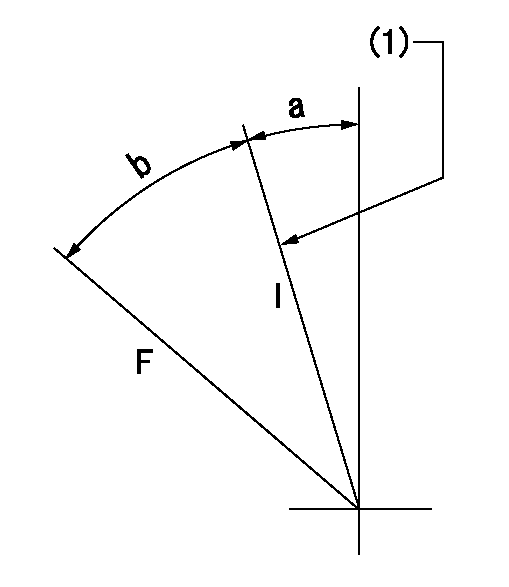
F:Full speed
I:Idle
(1)Stopper bolt set position 'H'
----------
----------
a=18.5deg+-5deg b=42deg+-3deeg
----------
----------
a=18.5deg+-5deg b=42deg+-3deeg
Stop lever angle
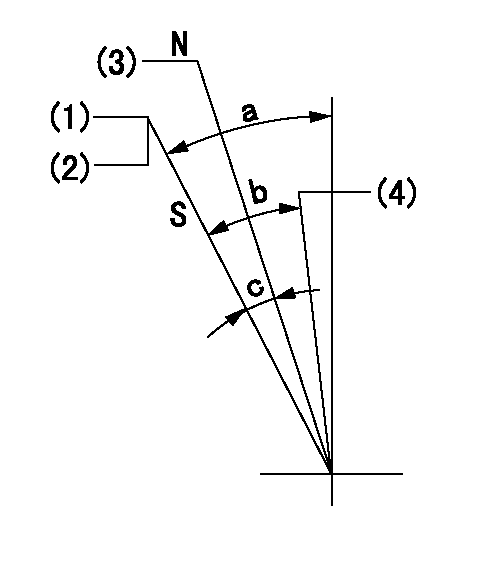
N:Engine manufacturer's normal use
S:Stop the pump.
(1)Set the stopper bolt at speed = rated point and rack position = aa (non-injection rack position). Confirm non-injection.
(2)After setting the stopper bolt , confirm non-injection at pump speed bb. Rack position = cc (non-injection rack position).
(3)Rack position = approximately dd
(4)Free (at shipping)
----------
aa=7mm bb=275r/min cc=(8)mm dd=17.4mm
----------
a=38.5deg+-5deg b=(27deg) c=17deg+-5deg
----------
aa=7mm bb=275r/min cc=(8)mm dd=17.4mm
----------
a=38.5deg+-5deg b=(27deg) c=17deg+-5deg
0000001201
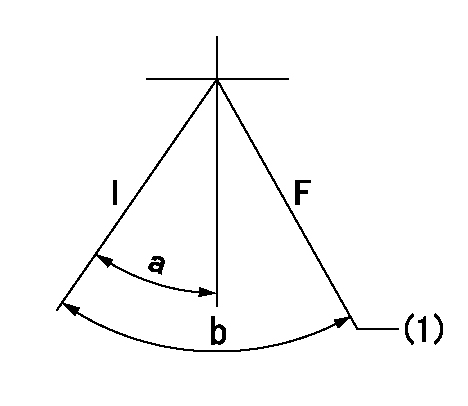
I:Idle
F:At operation, hold it in the full speed position.
(1)Rack position = aa, speed = bb.
----------
aa=8.4mm bb=1490r/min
----------
a=15deg+-5deg b=(36deg)+-3deg
----------
aa=8.4mm bb=1490r/min
----------
a=15deg+-5deg b=(36deg)+-3deg
0000001501 MICRO SWITCH
Adjustment of the micro-switch
Adjust the bolt to obtain the following lever position when the micro-switch is ON.
(1)Speed N1
(2)Rack position Ra
----------
N1=400+-5r/min Ra=9.2mm
----------
----------
N1=400+-5r/min Ra=9.2mm
----------
Timing setting

(1)Pump vertical direction
(2)Position of timer's tooth at No 1 cylinder's beginning of injection
(3)B.T.D.C.: aa
(4)-
----------
aa=12deg
----------
a=(1deg)
----------
aa=12deg
----------
a=(1deg)
Information:
Illustration 2 g03507406
Typical example of the 456-6048 DPF TOOL GP
Use the following procedure to measure the amount of ash in the DPF:
Use a wire with the maximum diameter of 1.04140 mm (0.041 inch) or the 456-6048 DPF TOOL GP. Hold the wire or tool so that the end of the wire is just inside the cell approximately 6.35000 mm (0.25 inch).
Drop the wire into the cell of the DPF.
Mark the wire at the top of the cell where the wire exits from the DPF.
Measure the depth that the wire dropped by measuring from the mark to the bottom tip of the wire.
Record the measurement.
Illustration 3 g03021156
Top view of DPF
View of locations for recording measurements
(1) Weld line
Perform Steps 7.b through 7.e for all locations. Refer to Illustration 3 for the proper location for recording measurements.
Average the measurements and refer to Table 3 for the acceptable measurements.
Table 3
Filter Assembly Part Number New Service Kit Part Number Reman Service Kit Part Number - Upgrade to New Reman Service Kit Part Number - Cat Factory Cleaned Measured Wire Depth Requires Cleaning Acceptable Cleaned Measured Wire Depth
358-3658 358-3659 20R-0696 20R-5620 Less than 178 mm (7 inch) Greater than 279 mm (11 inch)
358-3661 358-3662 20R-0697 20R-5621 Less than 203 mm (8 inch) Greater than 305 mm (12 inch)
358-3663 358-3664 20R-0698 20R-5622 Less than 203 mm (8 inch) Greater than 305 mm (12 inch)
358-3666 358-3667 20R-0699 20R-5623 Less than 254 mm (10 inch) Greater than 343 mm (13.5 inch)
358-3668 358-3669 20R-0700 20R-5624 Less than 279 mm (11 inch) Greater than 394 mm (15.5 inch)
The DPF is ready to be returned to service. DPF Ash Service
Purpose
The engine ash model must be reset whenever the filter is cleaned or replaced. Reseting the ash model places the DPF ash volume back to the "Clean State". The resetting will allow the regeneration of the DPF to function properly. Cat ET Location
Connect to Cat ET.
Illustration 4 g02477962
Select "Service" from the top menu and highlight "Service Procedures".
Illustration 5 g02477961
From the "Service Procedures" menu, highlight "DPF Ash Service". Select "Start".
Illustration 6 g02495621
Illustration 7 g02477958
Select "Ash Service Reset" to start the test procedure.
Illustration 8 g02477960
Choose the correct replacement type of diesel particulate filter in the menu that appears. The types of replacements for the diesel particulate filter are the following:
"Field cleaned" A filter that has been cleaned and reapplied
"New" - A new filter replacement
"Remanufactured" - A remanufactured filter replacement
Illustration 9 g02495643
Illustration 10 g02478024
Once the reset is completed, a log of the reset is captured and visible as a new row of information in the DPF ash service screen.
Perform a "Manual DPF Regeneration" with Cat ET to reset the soot level