Information injection-pump assembly
ZEXEL
101603-6061
1016036061
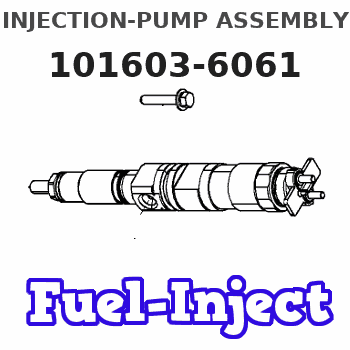
Rating:
Service parts 101603-6061 INJECTION-PUMP ASSEMBLY:
1.
_
3.
GOVERNOR
6.
COUPLING PLATE
7.
COUPLING PLATE
8.
_
9.
_
11.
Nozzle and Holder
ME035748
12.
Open Pre:MPa(Kqf/cm2)
21.6{220}
15.
NOZZLE SET
Include in #1:
101603-6061
as INJECTION-PUMP ASSEMBLY
Include in #2:
104740-1400
as _
Cross reference number
ZEXEL
101603-6061
1016036061
Zexel num
Bosch num
Firm num
Name
Calibration Data:
Adjustment conditions
Test oil
1404 Test oil ISO4113 or {SAEJ967d}
1404 Test oil ISO4113 or {SAEJ967d}
Test oil temperature
degC
40
40
45
Nozzle and nozzle holder
105780-8140
Bosch type code
EF8511/9A
Nozzle
105780-0000
Bosch type code
DN12SD12T
Nozzle holder
105780-2080
Bosch type code
EF8511/9
Opening pressure
MPa
17.2
Opening pressure
kgf/cm2
175
Injection pipe
Outer diameter - inner diameter - length (mm) mm 6-2-600
Outer diameter - inner diameter - length (mm) mm 6-2-600
Overflow valve
131424-5520
Overflow valve opening pressure
kPa
255
221
289
Overflow valve opening pressure
kgf/cm2
2.6
2.25
2.95
Tester oil delivery pressure
kPa
157
157
157
Tester oil delivery pressure
kgf/cm2
1.6
1.6
1.6
Direction of rotation (viewed from drive side)
Left L
Left L
Injection timing adjustment
Direction of rotation (viewed from drive side)
Left L
Left L
Injection order
1-5-3-6-
2-4
Pre-stroke
mm
3.6
3.55
3.65
Beginning of injection position
Governor side NO.1
Governor side NO.1
Difference between angles 1
Cal 1-5 deg. 60 59.5 60.5
Cal 1-5 deg. 60 59.5 60.5
Difference between angles 2
Cal 1-3 deg. 120 119.5 120.5
Cal 1-3 deg. 120 119.5 120.5
Difference between angles 3
Cal 1-6 deg. 180 179.5 180.5
Cal 1-6 deg. 180 179.5 180.5
Difference between angles 4
Cyl.1-2 deg. 240 239.5 240.5
Cyl.1-2 deg. 240 239.5 240.5
Difference between angles 5
Cal 1-4 deg. 300 299.5 300.5
Cal 1-4 deg. 300 299.5 300.5
Injection quantity adjustment
Adjusting point
-
Rack position
11
Pump speed
r/min
850
850
850
Each cylinder's injection qty
mm3/st.
60
58.1
61.9
Basic
*
Fixing the rack
*
Standard for adjustment of the maximum variation between cylinders
*
Injection quantity adjustment_02
Adjusting point
-
Rack position
10+-0.5
Pump speed
r/min
275
275
275
Each cylinder's injection qty
mm3/st.
10
8.9
11.1
Fixing the rack
*
Standard for adjustment of the maximum variation between cylinders
*
Remarks
Adjust only variation between cylinders; adjust governor according to governor specifications.
Adjust only variation between cylinders; adjust governor according to governor specifications.
Injection quantity adjustment_03
Adjusting point
A
Rack position
R1(11)
Pump speed
r/min
850
850
850
Average injection quantity
mm3/st.
60
59
61
Basic
*
Fixing the lever
*
Injection quantity adjustment_04
Adjusting point
B
Rack position
R1+0.6
Pump speed
r/min
1450
1450
1450
Average injection quantity
mm3/st.
80.5
78.5
82.5
Fixing the lever
*
Injection quantity adjustment_05
Adjusting point
C
Rack position
R1-0.4
Pump speed
r/min
600
600
600
Average injection quantity
mm3/st.
42.5
40.5
44.5
Fixing the lever
*
Injection quantity adjustment_06
Adjusting point
I
Rack position
-
Pump speed
r/min
100
100
100
Average injection quantity
mm3/st.
80
75
85
Fixing the lever
*
Rack limit
*
Timer adjustment
Pump speed
r/min
1250--
Advance angle
deg.
0
0
0
Remarks
Start
Start
Timer adjustment_02
Pump speed
r/min
1200
Advance angle
deg.
0.5
Timer adjustment_03
Pump speed
r/min
1350
Advance angle
deg.
2.4
1.9
2.9
Timer adjustment_04
Pump speed
r/min
1500
Advance angle
deg.
5
4.5
5.5
Remarks
Finish
Finish
Test data Ex:
Governor adjustment
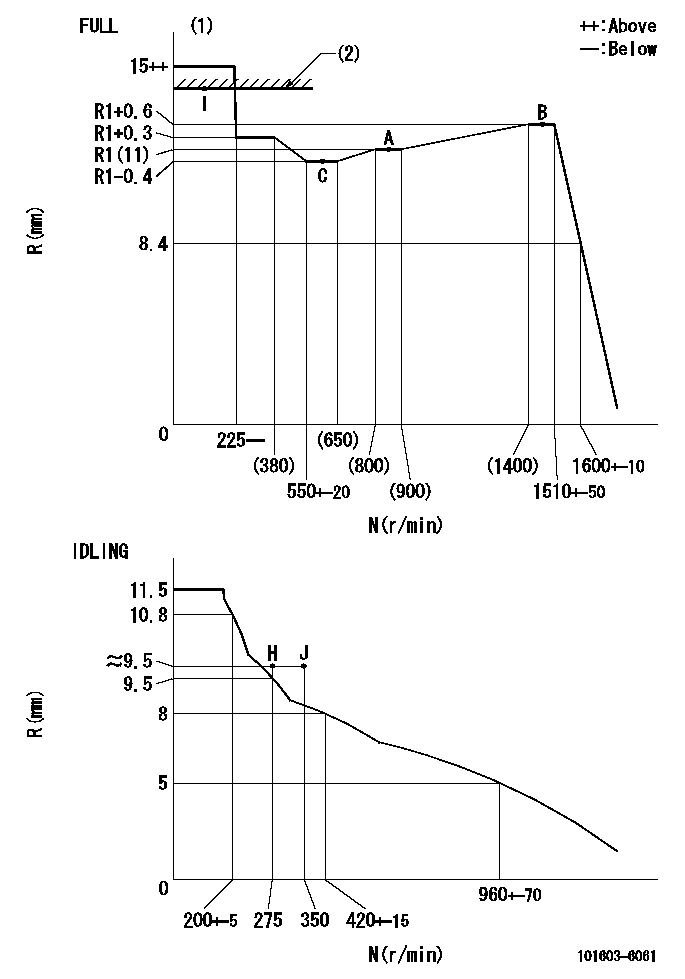
N:Pump speed
R:Rack position (mm)
(1)Torque cam stamping: T1
(2)RACK LIMIT
----------
T1=A63
----------
----------
T1=A63
----------
Speed control lever angle
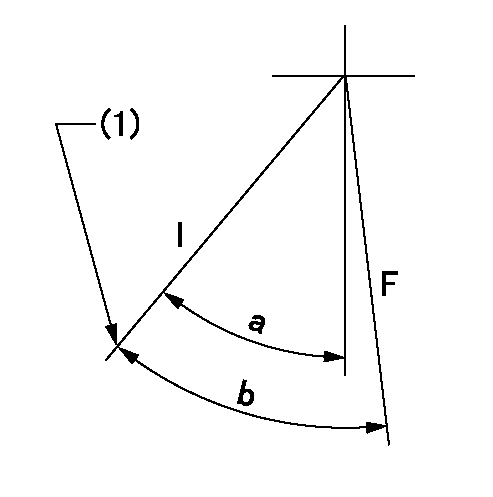
F:Full speed
I:Idle
(1)Stopper bolt set position 'H'
----------
----------
a=33deg+-5deg b=42deg+-3deeg
----------
----------
a=33deg+-5deg b=42deg+-3deeg
Stop lever angle
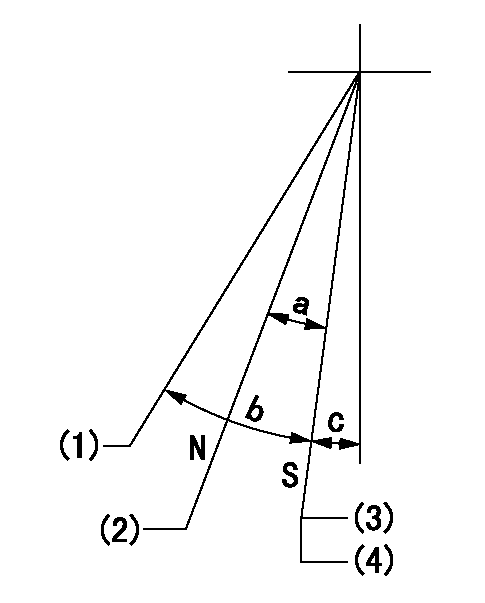
N:Engine manufacturer's normal use
S:Stop the pump.
(1)Free (at shipping)
(2)Rack position = approximately aa.
(3)Set the stopper bolt at speed = rated point and rack position = bb (non-injection rack position). Confirm non-injection.
(4)After setting the stopper bolt, confirm non-injection at speed cc. Rack position = dd (non-injection rack position).
----------
aa=17.4mm bb=(7)mm cc=275r/min dd=(8)mm
----------
a=17deg+-5deg b=(27deg) c=2deg+-5deg
----------
aa=17.4mm bb=(7)mm cc=275r/min dd=(8)mm
----------
a=17deg+-5deg b=(27deg) c=2deg+-5deg
0000001501 MICRO SWITCH
Adjustment of the micro-switch
Adjust the bolt to obtain the following lever position when the micro-switch is ON.
(1)Speed N1
(2)Rack position Ra
----------
N1=400+-5r/min Ra=9.2mm
----------
----------
N1=400+-5r/min Ra=9.2mm
----------
Timing setting

(1)Pump vertical direction
(2)Position of timer's tooth at No 1 cylinder's beginning of injection
(3)B.T.D.C.: aa
(4)-
----------
aa=12deg
----------
a=(1deg)
----------
aa=12deg
----------
a=(1deg)
Information:
Introduction
This document provides information about fuel degradation, which can cause a flow restriction of fuel through the fuel system and premature plugging of the filters. These guidelines should be used to guide service personnel in the use of fuels within diesel engines and covers recognized tests in identifying degredated fuels and best practices in storing fuels.This document can be used as a guide, but it does not provide all the information on all practices and procedures for degraded fuels. This document does not provide all the information for best practices for storing and handling fuels. Refer to Caterpillar Commercial Diesel Engine Fluids Recommendations, SEBU6251 for more information.The Thermal Stability and Oxidation Stability of Fuel
Diesel fuels can deteriorate rapidly for a variety of reasons. When the fuel is stressed and stored for long intervals, degradation and oxidation can occur. Degradation and oxidation are complex chemical changes. These changes lead to deposits or sediment from certain hydrocarbons and traces of naturally occurring nitrogen and sulfur containing compounds in the fuel. Fuel composition and environmental factors influences the process.Diesel fuel is being used as a coolant for high pressure fuel injection systems with high temperature fuel wetted walls. This can stress the fuel in the fuel system. The thermal stress and an increase in recirculation fuel temperature is often responsible for fuel degradation and the formation of gums, resins and sediment, which can cause fuel flow restriction through fuel filters and fuel injection systems.Certain products are often left with the fuel in the fuel system for long periods. This exposes the fuel to oxygen. Complex reactions between the oxygen and the fuel components can generate fuel particulates. The particulates in the fuel system can turn into the sludge that is found in fuel tanks, fuel lines and the fuel filters. This will deteriorate the performance of the fuel system. Degradation also leads to a plugged fuel filter, a restriction to the fuel line and deposit formation in the fuel injection nozzle.Biodiesel and blends of biodiesel have poor thermal stability and oxidation stability compared to petroleum distillate diesel fuels. The use of these biodiesels and blends of biodiesel can accelerate the problems that are addressed in this Special Instruction. Using biodiesel blends above the maximum level approved for the engine is not recommended.Thermal and oxidative degradation of diesel fuel can result in a darkening of fuel color. Fuel color is not necessarily an indication of excessive degradation that will lead to the problems outlined in thisSpecial Instruction, but can be an indicator or degradation If concerns arise about the stability of darkened fuel, the thermal oxidation and oxidative stability tests should be run to confirm actual degradation.Thermal Oxidation Stability
Caterpillar recommends the use of the Accelerated Fuel Oil Stability Test (ASTM D6468). This is a test method that determines the instability of a fuel subjected to a thermal degradation process. This test exposes the fuel to actual operating conditions when the fuel cools the injectors during the engine operation.The test is performed by
This document provides information about fuel degradation, which can cause a flow restriction of fuel through the fuel system and premature plugging of the filters. These guidelines should be used to guide service personnel in the use of fuels within diesel engines and covers recognized tests in identifying degredated fuels and best practices in storing fuels.This document can be used as a guide, but it does not provide all the information on all practices and procedures for degraded fuels. This document does not provide all the information for best practices for storing and handling fuels. Refer to Caterpillar Commercial Diesel Engine Fluids Recommendations, SEBU6251 for more information.The Thermal Stability and Oxidation Stability of Fuel
Diesel fuels can deteriorate rapidly for a variety of reasons. When the fuel is stressed and stored for long intervals, degradation and oxidation can occur. Degradation and oxidation are complex chemical changes. These changes lead to deposits or sediment from certain hydrocarbons and traces of naturally occurring nitrogen and sulfur containing compounds in the fuel. Fuel composition and environmental factors influences the process.Diesel fuel is being used as a coolant for high pressure fuel injection systems with high temperature fuel wetted walls. This can stress the fuel in the fuel system. The thermal stress and an increase in recirculation fuel temperature is often responsible for fuel degradation and the formation of gums, resins and sediment, which can cause fuel flow restriction through fuel filters and fuel injection systems.Certain products are often left with the fuel in the fuel system for long periods. This exposes the fuel to oxygen. Complex reactions between the oxygen and the fuel components can generate fuel particulates. The particulates in the fuel system can turn into the sludge that is found in fuel tanks, fuel lines and the fuel filters. This will deteriorate the performance of the fuel system. Degradation also leads to a plugged fuel filter, a restriction to the fuel line and deposit formation in the fuel injection nozzle.Biodiesel and blends of biodiesel have poor thermal stability and oxidation stability compared to petroleum distillate diesel fuels. The use of these biodiesels and blends of biodiesel can accelerate the problems that are addressed in this Special Instruction. Using biodiesel blends above the maximum level approved for the engine is not recommended.Thermal and oxidative degradation of diesel fuel can result in a darkening of fuel color. Fuel color is not necessarily an indication of excessive degradation that will lead to the problems outlined in thisSpecial Instruction, but can be an indicator or degradation If concerns arise about the stability of darkened fuel, the thermal oxidation and oxidative stability tests should be run to confirm actual degradation.Thermal Oxidation Stability
Caterpillar recommends the use of the Accelerated Fuel Oil Stability Test (ASTM D6468). This is a test method that determines the instability of a fuel subjected to a thermal degradation process. This test exposes the fuel to actual operating conditions when the fuel cools the injectors during the engine operation.The test is performed by