Information injection-pump assembly
ZEXEL
101603-4470
1016034470
ISUZU
1156021962
1156021962
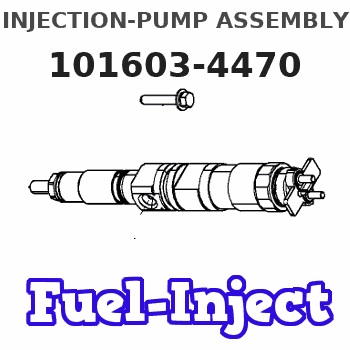
Rating:
Service parts 101603-4470 INJECTION-PUMP ASSEMBLY:
1.
_
7.
COUPLING PLATE
8.
_
9.
_
11.
Nozzle and Holder
1-15300-104-0
12.
Open Pre:MPa(Kqf/cm2)
18.1(185)
15.
NOZZLE SET
Cross reference number
ZEXEL
101603-4470
1016034470
ISUZU
1156021962
1156021962
Zexel num
Bosch num
Firm num
Name
Calibration Data:
Adjustment conditions
Test oil
1404 Test oil ISO4113 or {SAEJ967d}
1404 Test oil ISO4113 or {SAEJ967d}
Test oil temperature
degC
40
40
45
Nozzle and nozzle holder
105780-8140
Bosch type code
EF8511/9A
Nozzle
105780-0000
Bosch type code
DN12SD12T
Nozzle holder
105780-2080
Bosch type code
EF8511/9
Opening pressure
MPa
17.2
Opening pressure
kgf/cm2
175
Injection pipe
Outer diameter - inner diameter - length (mm) mm 6-2-600
Outer diameter - inner diameter - length (mm) mm 6-2-600
Overflow valve opening pressure
kPa
157
123
191
Overflow valve opening pressure
kgf/cm2
1.6
1.25
1.95
Tester oil delivery pressure
kPa
157
157
157
Tester oil delivery pressure
kgf/cm2
1.6
1.6
1.6
Direction of rotation (viewed from drive side)
Right R
Right R
Injection timing adjustment
Direction of rotation (viewed from drive side)
Right R
Right R
Injection order
1-5-3-6-
2-4
Pre-stroke
mm
3.6
3.55
3.65
Beginning of injection position
Drive side NO.1
Drive side NO.1
Difference between angles 1
Cal 1-5 deg. 60 59.5 60.5
Cal 1-5 deg. 60 59.5 60.5
Difference between angles 2
Cal 1-3 deg. 120 119.5 120.5
Cal 1-3 deg. 120 119.5 120.5
Difference between angles 3
Cal 1-6 deg. 180 179.5 180.5
Cal 1-6 deg. 180 179.5 180.5
Difference between angles 4
Cyl.1-2 deg. 240 239.5 240.5
Cyl.1-2 deg. 240 239.5 240.5
Difference between angles 5
Cal 1-4 deg. 300 299.5 300.5
Cal 1-4 deg. 300 299.5 300.5
Injection quantity adjustment
Adjusting point
A
Rack position
8.7
Pump speed
r/min
900
900
900
Average injection quantity
mm3/st.
49.9
48.4
51.4
Max. variation between cylinders
%
0
-2.5
2.5
Basic
*
Fixing the lever
*
Injection quantity adjustment_02
Adjusting point
B
Rack position
6.7+-0.5
Pump speed
r/min
290
290
290
Average injection quantity
mm3/st.
9.2
7.9
10.5
Max. variation between cylinders
%
0
-14
14
Fixing the rack
*
Injection quantity adjustment_03
Adjusting point
C
Rack position
-
Pump speed
r/min
150
150
150
Average injection quantity
mm3/st.
50
50
Fixing the lever
*
Remarks
After startup boost setting
After startup boost setting
Timer adjustment
Pump speed
r/min
350--
Advance angle
deg.
0
0
0
Remarks
Start
Start
Timer adjustment_02
Pump speed
r/min
300
Advance angle
deg.
0.5
Timer adjustment_03
Pump speed
r/min
900
Advance angle
deg.
2
1.5
2.5
Timer adjustment_04
Pump speed
r/min
1300
Advance angle
deg.
4
3.5
4.5
Remarks
Finish
Finish
Test data Ex:
Governor adjustment
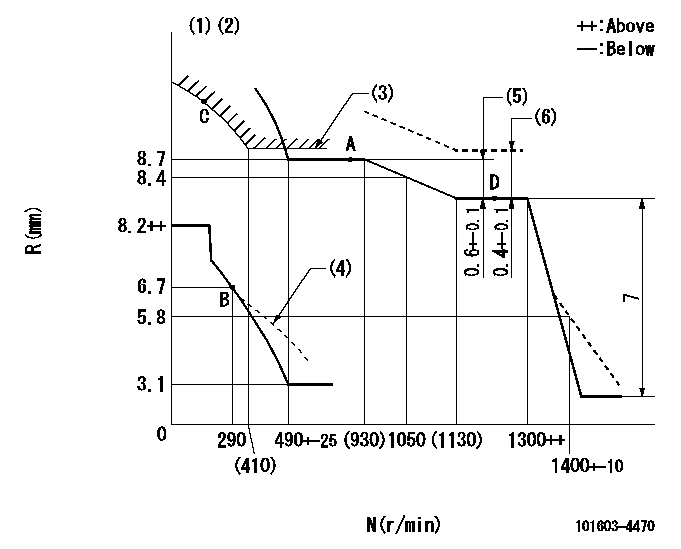
N:Pump speed
R:Rack position (mm)
(1)Lever ratio: RT
(2)Target shim dimension: TH
(3)Excess fuel setting for starting: SXL
(4)Damper spring setting: DL
(5)Rack difference between N = N1 and N = N2
(6)Tamper proof (shaft setting) (at N = N3).
----------
RT=1 TH=1.5mm SXL=9.1+0.2mm DL=6.2-0.2mm N1=1300r/min N2=900r/min N3=1300r/min
----------
----------
RT=1 TH=1.5mm SXL=9.1+0.2mm DL=6.2-0.2mm N1=1300r/min N2=900r/min N3=1300r/min
----------
0000000901

F:Full load
I:Idle
(1)Stopper bolt setting
----------
----------
a=21deg+-3deg b=33deg+-5deg
----------
----------
a=21deg+-3deg b=33deg+-5deg
Stop lever angle

N:Pump normal
S:Stop the pump.
----------
----------
a=35.5deg+-5deg b=71deg+-5deg
----------
----------
a=35.5deg+-5deg b=71deg+-5deg
0000001501 TAMPER PROOF

N:Pump speed (r/min)
R:Rack position (mm)
1. After governor adjustment, adjust the shaft as described below and stamp the cap.
(1)Turn the load lever stopper bolt determining the full rack position (R = Rf) 1~2 turns counterclockwise.
(2)Then, increase the full rack position.
(3)Operate the pump at N = Nf and turn the shaft (B) clockwise.
(4)Adjust so that full rack is Rf+0.4.
(5)Tighten nut (A) to the specified torque.
(6)Turn the stopper bolt clockwise the same amount that it was turned counter clockwise in (1).
(7)Then, align with the full rack position (R = Rf) and fix.
(8)Apply thread lock adhesive to the entire circumference of the cap (C) and tap it down to pressfit and seal it..
(9)Check for air tightness.
----------
Rf=8.1mm Nf=1300r/min
----------
----------
Rf=8.1mm Nf=1300r/min
----------
Timing setting
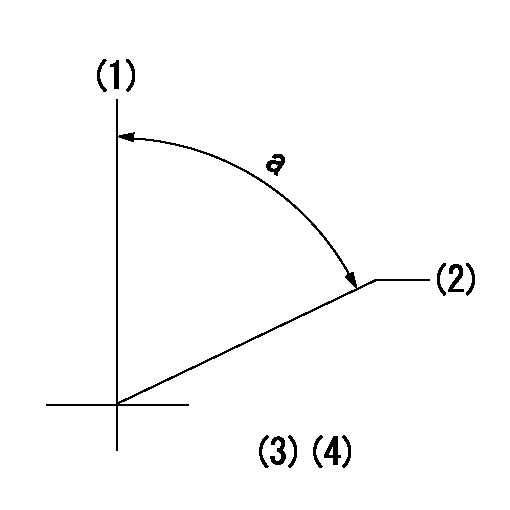
(1)Pump vertical direction
(2)Position of timer's threaded hole at No 1 cylinder's beginning of injection
(3)B.T.D.C.: aa
(4)-
----------
aa=14deg
----------
a=(60deg)
----------
aa=14deg
----------
a=(60deg)
Information:
1 Remove the plug from the dash and install 3T306 Starting Aid Switch. Connect two purple wires, from the wiring harness, to the switch. 2 Put 3T157 Support Assembly (1) in position. Install two 6H1717 Bolts (2) as shown. On D6D Tractors with 4N6016 Refrigerant Compressor Group, remove the existing spacer so support (1) will fit at location (A); use the existing bolt. Remove the bolt and washer from the cylinder head and put 3T1417 Brace (3) in position. Install 2A4256 Spacer (4), S1591 Bolt (5) and 5M2894 Washer. Do not use spacer (4) on D6D Tractors. Install S1594 Bolt (6) and 5M2894 Washer. 3 Put 6N7674 Valve Assembly (7) in position on support assembly (1) and install two S1618 Bolts (8), 5P4116 Washers and 1D4716 Nuts. Put 7N2059 Clamp Assembly (9) in position on the support assembly and install two S1618 Bolts (8), 5P4116 Washers and 1D4716 Nuts. 4 Remove the plug from the manifold and install 6N9995 Atomizer Assembly (9). The orifices of the atomizer must be toward each end of the manifold. Install 5P7907 Connector (10) in valve assembly (7). Install one end of 9P3121 Tube (11) in atomizer assembly (9) and connect the other end of tube (11) to connector (10) with 5P6314 Sleeve (12) and 5P6313 Nut (13). Remove the plug from the bypass elbow and install 6N5899 Switch (14). Connect 9G3005 Wire Assembly (15) to switch (14) and to one wire from valve assembly (7). 5 Install 3D5102 Grommet and 2B2404 Clip (16) to hold tube (11). Connect 9G3006 Wire Assembly (17) to valve assembly (7) and to the purple wire, from the starting aid switch, at the rear of the engine. Use former clips (18) to hold wire assembly (17) in position.6 Remove cap (19) from valve assembly (7) and install 7N296 Cylinder Assembly.