Information injection-pump assembly
BOSCH
9 400 610 649
9400610649
ZEXEL
101603-4402
1016034402
ISUZU
1156022364
1156022364
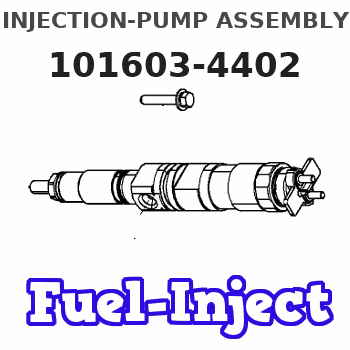
Rating:
Service parts 101603-4402 INJECTION-PUMP ASSEMBLY:
1.
_
7.
COUPLING PLATE
8.
_
9.
_
11.
Nozzle and Holder
1-15300-105-2
12.
Open Pre:MPa(Kqf/cm2)
18.1{185}
15.
NOZZLE SET
Cross reference number
BOSCH
9 400 610 649
9400610649
ZEXEL
101603-4402
1016034402
ISUZU
1156022364
1156022364
Zexel num
Bosch num
Firm num
Name
101603-4402
9 400 610 649
1156022364 ISUZU
INJECTION-PUMP ASSEMBLY
6BD1-T K 14BE INJECTION PUMP ASSY PE6A PE
6BD1-T K 14BE INJECTION PUMP ASSY PE6A PE
Calibration Data:
Adjustment conditions
Test oil
1404 Test oil ISO4113 or {SAEJ967d}
1404 Test oil ISO4113 or {SAEJ967d}
Test oil temperature
degC
40
40
45
Nozzle and nozzle holder
105780-8140
Bosch type code
EF8511/9A
Nozzle
105780-0000
Bosch type code
DN12SD12T
Nozzle holder
105780-2080
Bosch type code
EF8511/9
Opening pressure
MPa
17.2
Opening pressure
kgf/cm2
175
Injection pipe
Outer diameter - inner diameter - length (mm) mm 6-2-600
Outer diameter - inner diameter - length (mm) mm 6-2-600
Overflow valve
132424-0620
Overflow valve opening pressure
kPa
157
123
191
Overflow valve opening pressure
kgf/cm2
1.6
1.25
1.95
Tester oil delivery pressure
kPa
157
157
157
Tester oil delivery pressure
kgf/cm2
1.6
1.6
1.6
Direction of rotation (viewed from drive side)
Right R
Right R
Injection timing adjustment
Direction of rotation (viewed from drive side)
Right R
Right R
Injection order
1-5-3-6-
2-4
Pre-stroke
mm
3.4
3.35
3.45
Beginning of injection position
Drive side NO.1
Drive side NO.1
Difference between angles 1
Cal 1-5 deg. 60 59.5 60.5
Cal 1-5 deg. 60 59.5 60.5
Difference between angles 2
Cal 1-3 deg. 120 119.5 120.5
Cal 1-3 deg. 120 119.5 120.5
Difference between angles 3
Cal 1-6 deg. 180 179.5 180.5
Cal 1-6 deg. 180 179.5 180.5
Difference between angles 4
Cyl.1-2 deg. 240 239.5 240.5
Cyl.1-2 deg. 240 239.5 240.5
Difference between angles 5
Cal 1-4 deg. 300 299.5 300.5
Cal 1-4 deg. 300 299.5 300.5
Injection quantity adjustment
Adjusting point
-
Rack position
10.6
Pump speed
r/min
900
900
900
Average injection quantity
mm3/st.
67
65.4
68.6
Max. variation between cylinders
%
0
-2.5
2.5
Basic
*
Fixing the rack
*
Standard for adjustment of the maximum variation between cylinders
*
Injection quantity adjustment_02
Adjusting point
-
Rack position
9.6+-0.5
Pump speed
r/min
275
275
275
Average injection quantity
mm3/st.
9.4
8.1
10.7
Max. variation between cylinders
%
0
-14
14
Fixing the rack
*
Standard for adjustment of the maximum variation between cylinders
*
Remarks
Adjust only variation between cylinders; adjust governor according to governor specifications.
Adjust only variation between cylinders; adjust governor according to governor specifications.
Injection quantity adjustment_03
Adjusting point
A
Rack position
R1(10.6)
Pump speed
r/min
900
900
900
Average injection quantity
mm3/st.
67
66
68
Basic
*
Fixing the lever
*
Injection quantity adjustment_04
Adjusting point
B
Rack position
R1-0.1
Pump speed
r/min
1500
1500
1500
Average injection quantity
mm3/st.
74.5
71.3
77.7
Fixing the lever
*
Injection quantity adjustment_05
Adjusting point
C
Rack position
(R1-0.4)
Pump speed
r/min
1600
1600
1600
Average injection quantity
mm3/st.
68.5
64.5
72.5
Fixing the lever
*
Injection quantity adjustment_06
Adjusting point
D
Rack position
R1-0.3
Pump speed
r/min
500
500
500
Average injection quantity
mm3/st.
42.7
39.5
45.9
Fixing the lever
*
Injection quantity adjustment_07
Adjusting point
E
Rack position
(R1-0.2)
Pump speed
r/min
400
400
400
Average injection quantity
mm3/st.
42.8
39.6
46
Fixing the lever
*
Injection quantity adjustment_08
Adjusting point
F
Rack position
(R1+0.15
)
Pump speed
r/min
300
300
300
Average injection quantity
mm3/st.
42.4
39.2
45.6
Fixing the lever
*
Injection quantity adjustment_09
Adjusting point
I
Rack position
-
Pump speed
r/min
150
150
150
Average injection quantity
mm3/st.
81
81
91
Fixing the lever
*
Rack limit
*
Timer adjustment
Pump speed
r/min
1050--
Advance angle
deg.
0
0
0
Remarks
Start
Start
Timer adjustment_02
Pump speed
r/min
1000
Advance angle
deg.
0.5
Timer adjustment_03
Pump speed
r/min
1300
Advance angle
deg.
0.9
0.4
1.4
Timer adjustment_04
Pump speed
r/min
1600
Advance angle
deg.
2
1.5
2.5
Remarks
Finish
Finish
Test data Ex:
Governor adjustment
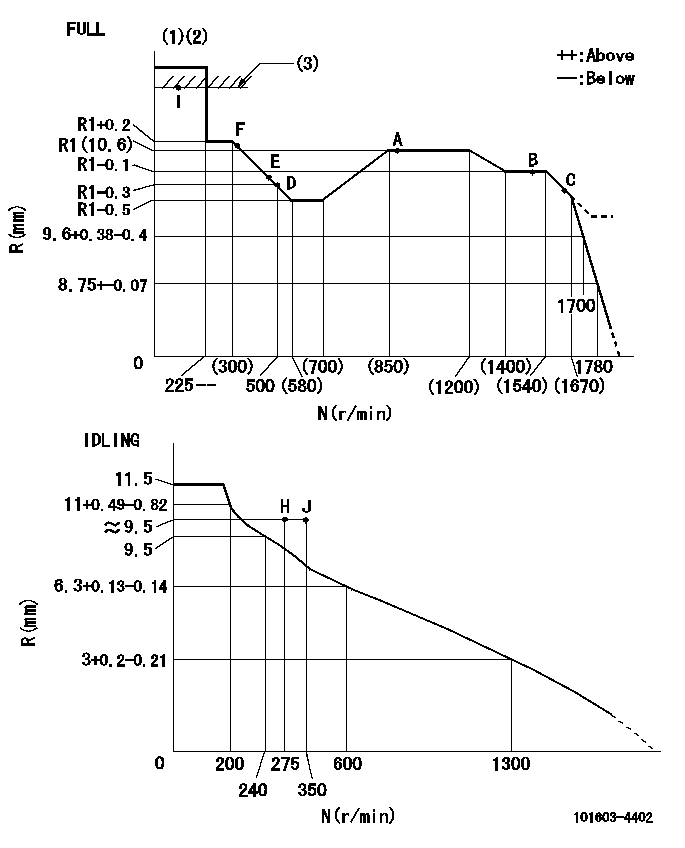
N:Pump speed
R:Rack position (mm)
(1)Torque cam stamping: T1
(2)Tolerance for racks not indicated: +-0.05mm.
(3)RACK LIMIT
----------
T1=E66
----------
----------
T1=E66
----------
Speed control lever angle
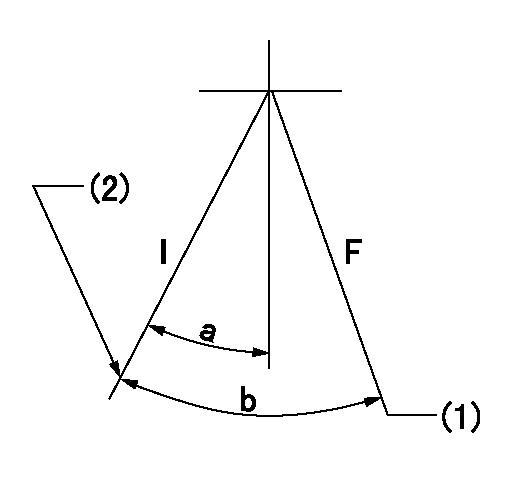
F:Full speed
I:Idle
(1)-
(2)Stopper bolt set position 'H'
----------
----------
a=33deg+-5deg b=36deg+-3deg
----------
----------
a=33deg+-5deg b=36deg+-3deg
Stop lever angle

N:Pump normal
S:Stop the pump.
----------
----------
a=25deg+-5deg b=40deg+-5deg
----------
----------
a=25deg+-5deg b=40deg+-5deg
0000001501 ACS
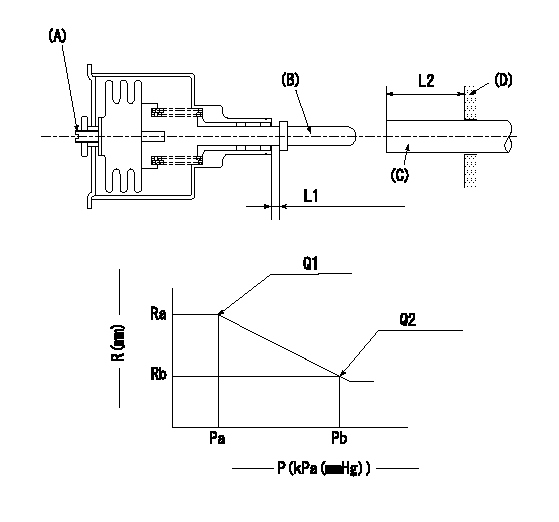
(A) Set screw
(B) Push rod 1
(C) Push rod 2
(D) Cover
1. Aneroid compensator unit adjustment
(1)Select the push rod 2 to obtain L2.
(2)Screw in (A) to obtain L1.
2. Adjustment when mounting the governor.
(1)Set the speed of the pump to N1 r/min and fix the control lever at the full set position.
(2)Screw in the aneroid compensator to obtain the performance shown in the graph above.
(3)As there is hysterisis, measure when the absolute pressure drops.
(4)Hysterisis must not exceed rack position = h1.
----------
N1=900 r/min L1=(1.5) mm L2=11+-0.5 mm h1=0.15
----------
Ra=R1(10.6) mm Rb=R2(10.1) mm Pa=89.8+-2.7 kPa(674+-20 mmHg) Pb=70.1+-0.7 kPa(526+-5 mmHg) Q1=67+-1 cm3/1000st Q2=56.5+-1.6 cm3/1000st
----------
N1=900 r/min L1=(1.5) mm L2=11+-0.5 mm h1=0.15
----------
Ra=R1(10.6) mm Rb=R2(10.1) mm Pa=89.8+-2.7 kPa(674+-20 mmHg) Pb=70.1+-0.7 kPa(526+-5 mmHg) Q1=67+-1 cm3/1000st Q2=56.5+-1.6 cm3/1000st
Timing setting
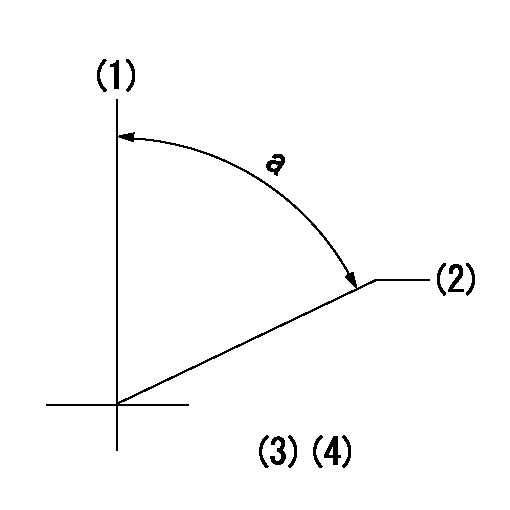
(1)Pump vertical direction
(2)Position of timer's threaded hole at No 1 cylinder's beginning of injection
(3)B.T.D.C.: aa
(4)-
----------
aa=14deg
----------
a=(60deg)
----------
aa=14deg
----------
a=(60deg)
Information:
ACTION REQUIRED
Replace cylinder head, reusing cylinder head bolts and washers after performing visual inspection. Reinstall injector, injector return line, and quill tube with new injector seals, injector return line seals, and quill tube bolts. Reference KENR6052 for removal and installation procedures and for troubleshooting guidance on diagnosing a leaking injector sleeve refer to the info below.
If the source of the sodium cannot be isolated via other normal testing of individual components (water pumps, oil coolers, etc.) then complete the following procedure:
1. Shut down the engine and allow system to cool.
2. Flip the ground level shutdown switch on the truck front bumper and leave the switch engaged. This action disables the fuel injection.
3. Verify that the engine will crank but the engine does NOT start.
4. Pull the last exhaust manifold from each bank of the engine.
5. Pressurize the truck cooling system, refer to Testing and Adjusting, KENR5397 for additional information.
6. Hold pressure on the cooling system for no more than 10 minutes for the first test. If the leak is bad, holding the pressure too long could risk hydraulic lock.
7. While cranking the engine, shine a light up into the exhaust manifolds and look for cylinders that are puffing steam and white smoke. Refer to Image 1.
8. Verify any leaks by pulling the exhaust thermocouple port from the exhaust runner on that cylinder. Check for signs of moisture/steaming in that exhaust runner.
9. Repair any leaking injector sleeve by replacing the head.
Image1
SERVICE CLAIM ALLOWANCES
Product smu/age whichever comes first Caterpillar Dealer Suggested Customer Suggested
Parts % Labor Hrs% Parts % Labor Hrs% Parts % Labor Hrs%
0-9000 hrs,
0-24 mo 100.0% 100.0% 0.0% 0.0% 0.0% 0.0%
9001-18000 hrs,
25-48 mo 33.0% 50.0% 0.0% 0.0% 50.0% 50.0%
This is a 8.0-hour job
If there has been a previous repair, part age/hours will apply. Retain a copy of the previous repair invoice in the dealer's records for audit purposes, and specify repair date and machine hours in the "Additional Comments" section of the warranty claim.
The 8 hour labor allowance consists of:
4 hours troubleshooting max per repair
4 hours repair time
If more than one cylinder has failed, an additional 4 hours repair time per additional cylinder is allowed. Repairing up to 4 cylinders (793F) and 6 cylinders (797B, 797F) in chassis is allowed. No additional troubleshooting time is allowed.
PARTS DISPOSITION
Handle the parts in accordance with your Warranty Bulletin on warranty parts handling.
Have questions with 101603-4402?
Group cross 101603-4402 ZEXEL
Isuzu
101603-4402
9 400 610 649
1156022364
INJECTION-PUMP ASSEMBLY
6BD1-T
6BD1-T