Information injection-pump assembly
BOSCH
9 400 611 994
9400611994
ZEXEL
101603-2710
1016032710
HINO
220205690A
220205690a
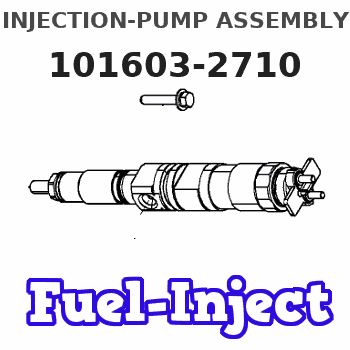
Rating:
Service parts 101603-2710 INJECTION-PUMP ASSEMBLY:
1.
_
7.
COUPLING PLATE
8.
_
9.
_
11.
Nozzle and Holder
23600-2710A
12.
Open Pre:MPa(Kqf/cm2)
17.7{180}
15.
NOZZLE SET
Cross reference number
BOSCH
9 400 611 994
9400611994
ZEXEL
101603-2710
1016032710
HINO
220205690A
220205690a
Zexel num
Bosch num
Firm num
Name
101603-2710
9 400 611 994
220205690A HINO
INJECTION-PUMP ASSEMBLY
H07C-T K 14BF INJECTION PUMP ASSY PE6AD PE
H07C-T K 14BF INJECTION PUMP ASSY PE6AD PE
Calibration Data:
Adjustment conditions
Test oil
1404 Test oil ISO4113 or {SAEJ967d}
1404 Test oil ISO4113 or {SAEJ967d}
Test oil temperature
degC
40
40
45
Nozzle and nozzle holder
105780-8140
Bosch type code
EF8511/9A
Nozzle
105780-0000
Bosch type code
DN12SD12T
Nozzle holder
105780-2080
Bosch type code
EF8511/9
Opening pressure
MPa
17.2
Opening pressure
kgf/cm2
175
Injection pipe
Outer diameter - inner diameter - length (mm) mm 6-2-600
Outer diameter - inner diameter - length (mm) mm 6-2-600
Overflow valve
134424-0920
Overflow valve opening pressure
kPa
162
147
177
Overflow valve opening pressure
kgf/cm2
1.65
1.5
1.8
Tester oil delivery pressure
kPa
157
157
157
Tester oil delivery pressure
kgf/cm2
1.6
1.6
1.6
Direction of rotation (viewed from drive side)
Right R
Right R
Injection timing adjustment
Direction of rotation (viewed from drive side)
Right R
Right R
Injection order
1-4-2-6-
3-5
Pre-stroke
mm
4.8
4.77
4.83
Beginning of injection position
Drive side NO.1
Drive side NO.1
Difference between angles 1
Cal 1-4 deg. 60 59.75 60.25
Cal 1-4 deg. 60 59.75 60.25
Difference between angles 2
Cyl.1-2 deg. 120 119.75 120.25
Cyl.1-2 deg. 120 119.75 120.25
Difference between angles 3
Cal 1-6 deg. 180 179.75 180.25
Cal 1-6 deg. 180 179.75 180.25
Difference between angles 4
Cal 1-3 deg. 240 239.75 240.25
Cal 1-3 deg. 240 239.75 240.25
Difference between angles 5
Cal 1-5 deg. 300 299.75 300.25
Cal 1-5 deg. 300 299.75 300.25
Injection quantity adjustment
Adjusting point
A
Rack position
11.5
Pump speed
r/min
800
800
800
Average injection quantity
mm3/st.
115.5
114
117
Max. variation between cylinders
%
0
-3.5
3.5
Basic
*
Fixing the lever
*
Boost pressure
kPa
24.7
24.7
Boost pressure
mmHg
185
185
Injection quantity adjustment_02
Adjusting point
-
Rack position
6+-0.5
Pump speed
r/min
400
400
400
Average injection quantity
mm3/st.
10
9
11
Max. variation between cylinders
%
0
-10
10
Fixing the rack
*
Boost pressure
kPa
0
0
0
Boost pressure
mmHg
0
0
0
Remarks
Adjust only variation between cylinders; adjust governor according to governor specifications.
Adjust only variation between cylinders; adjust governor according to governor specifications.
Injection quantity adjustment_03
Adjusting point
D
Rack position
-
Pump speed
r/min
100
100
100
Average injection quantity
mm3/st.
130
130
140
Fixing the lever
*
Boost pressure
kPa
0
0
0
Boost pressure
mmHg
0
0
0
Rack limit
*
Boost compensator adjustment
Pump speed
r/min
500
500
500
Rack position
R1-0.8
Boost pressure
kPa
4
2.7
5.3
Boost pressure
mmHg
30
20
40
Boost compensator adjustment_02
Pump speed
r/min
500
500
500
Rack position
R1(11.4)
Boost pressure
kPa
11.3
11.3
11.3
Boost pressure
mmHg
85
85
85
Timer adjustment
Pump speed
r/min
-
Advance angle
deg.
0
0
0
Remarks
Measure speed (beginning of operation).
Measure speed (beginning of operation).
Timer adjustment_02
Pump speed
r/min
-
Advance angle
deg.
1.5
1.2
1.8
Remarks
Measure the actual speed, stop
Measure the actual speed, stop
Test data Ex:
Governor adjustment
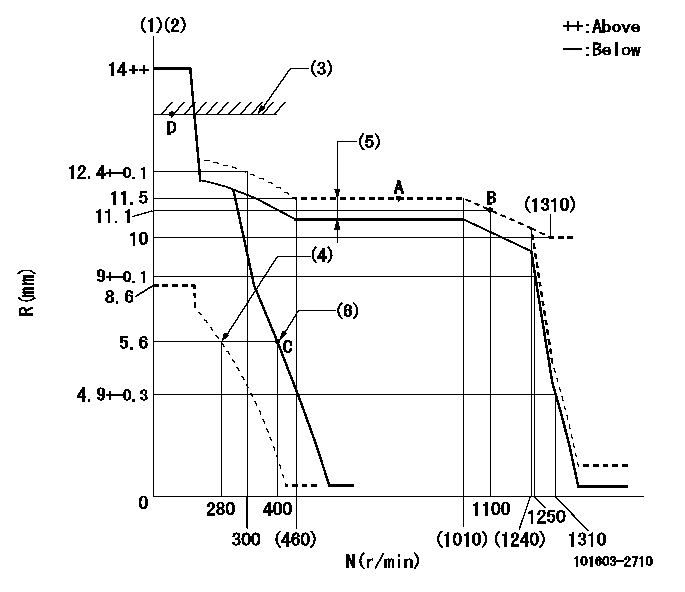
N:Pump speed
R:Rack position (mm)
(1)Target notch: K
(2)Tolerance for racks not indicated: +-0.05mm.
(3)RACK LIMIT
(4)Set idle sub-spring
(5)Boost compensator stroke: BCL
(6)Main spring setting
----------
K=17 BCL=0.8+-0.1mm
----------
----------
K=17 BCL=0.8+-0.1mm
----------
Speed control lever angle
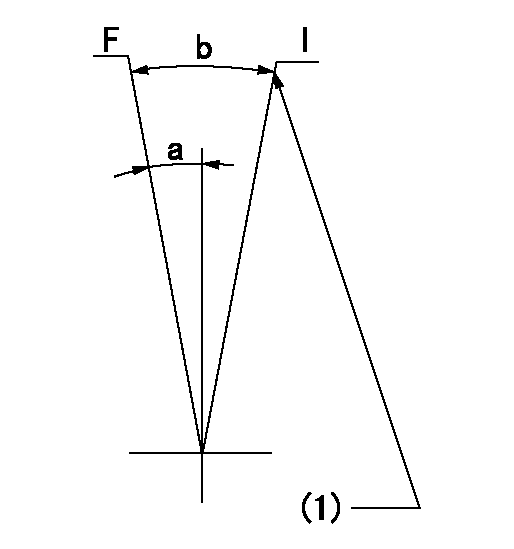
F:Full speed
I:Idle
(1)Stopper bolt setting
----------
----------
a=23deg+-5deg b=38deg+-5deg
----------
----------
a=23deg+-5deg b=38deg+-5deg
Stop lever angle

N:Pump normal
S:Stop the pump.
(1)Pump speed aa and rack position bb (to be sealed at delivery)
(2)Normal
----------
aa=0r/min bb=1-0.5mm
----------
a=21deg+-5deg b=(55deg)
----------
aa=0r/min bb=1-0.5mm
----------
a=21deg+-5deg b=(55deg)
Timing setting
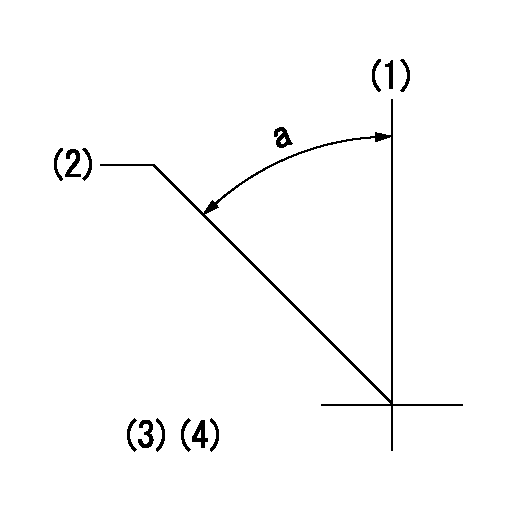
(1)Pump vertical direction
(2)Coupling's key groove position at No 1 cylinder's beginning of injection
(3)-
(4)-
----------
----------
a=(50deg)
----------
----------
a=(50deg)
Information:
Figure 1The next chart shows maximum acceptable voltage loss in the high current battery circuit feeding the starting motor. These values are maximums for machines of approximately 2000 SMH and up. Newer machines would be less than those shown.
Figure 2Voltages greater than those shown are most often caused by loose and/or corroded connections or defective switch contacts.Diagnosis Procedure
Do not operate the starting motor for more than 30 seconds at a time. After 30 seconds, the cranking must be stopped for two minutes to allow the starting motor to cool. This will prevent damage to the starting motor due to excessive heat buildup.
If the starting motor cranks real slow or does not crank at all, do the following procedure:1. Measure battery voltage at the battery posts with the multimeter while cranking or attempting to crank the engine. Make sure to measure the battery posts. Do not measure the cable post clamps.2. Is battery voltage equal to or greater than shown in Figure 1? a. If the battery voltage is OK, go to Step 3.b. If the battery voltage is too low, test the battery as shown in Special Instruction Form No. SEHS7633. A low battery can be caused by battery condition or a shorted starting motor.3. Measure current draw on the (+) battery cable between the battery and the starting motor solenoid with the clamp-on ammeter. The maximum current draw allowed is shown in Specifications under Load Test. The figures shown in Specifications are taken at temperature of 27°C (80°F). At temperatures below 27°C (80°F), the voltage will be less and the current draw will be higher. If current draw is too much, the starting motor has a problem and must be removed for repair or replacement. If voltage at the battery post is within approximately 2 volts of the lowest value in the applicable temperature range of Figure 1 and if the large starting motor cables get hot, then the starting motor has a problem and the 8T0900 Ammeter test is not needed.4. Measure starting motor voltage from test point (4) to (5) with the multimeter while cranking or attempting to crank the engine.5. Is voltage equal to or greater than shown in Figure 1? a. If the starting motor voltage is OK, the battery and starting motor cables down to the motor are within specifications. Go to Step 8.b. If the starting motor voltage is low, the voltage drop between the battery and the starting motor is too great. Go to Step 6.6. Measure the voltage drops in the cranking circuits with the multimeter. Compare the results with maximum voltage drops allowed in Figure 2.7. Are all the voltages within specifications? a. If the voltage drops are OK, go to Step 8, to check the engine.b. If the voltage drops are too high, repair and/or replace the faulty electrical component.8. Rotate the crankshaft by hand to make sure it is not locked up. Check oil viscosity and any external loads that would affect engine rotation.9. Is the
Have questions with 101603-2710?
Group cross 101603-2710 ZEXEL
Hino
101603-2710
9 400 611 994
220205690A
INJECTION-PUMP ASSEMBLY
H07C-T
H07C-T